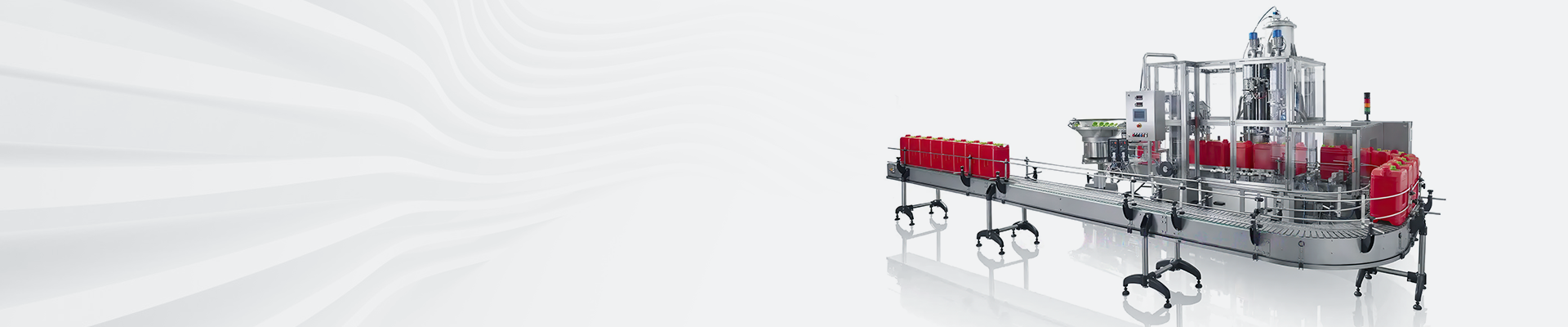
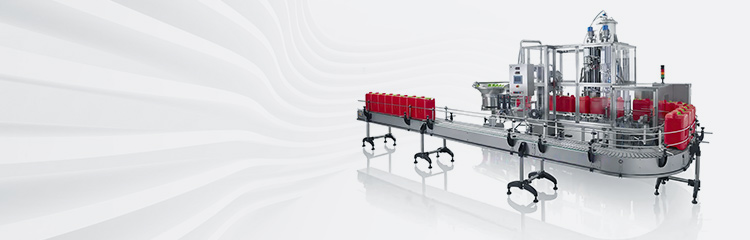

Summary:Equipping the advanced DCS control system in the ferromolybdenum smelting batching can ensure the accuracy of weighing the ferromolybdenum batching and improve the uniformity of the ferromolybdenum smelting mixture.Through the analysis and evaluation of system performance and further optimization and transformation, it provides a reliable basic guarantee for improving the quality of ferromolybdenum, and has achieved relatively satisfactory results in the production of ferromolybdenum ingredients.
0Preface
As we all know, in the furnace smelting iron molybdenum smelting process, the preliminary dosing operation is the key control process, molybdenum iron mixture components are hooked precision is to determine the effect of smelting one of the important basic parameters of process control.
Currently in China's iron molybdenum smelting dosage process, more commonly used cylinder mixer and V series mixer as dosage mixing device. Although it has the advantages of small investment, simple operation, etc., but there are different degrees of measurement accuracy is poor, the material homogeneous hook degree is not ideal and other problems, restricting the improvement of molybdenum iron quality. In the actual production of molybdenum iron batching in the use of AMEC, Enfi prior to the design of DCS weighing control system, in the actual production of molybdenum iron in practice, through the evaluation and analysis of the actual performance of the use of the system to determine the further optimization and transformation of the implementation of the program, and achieved a more satisfactory and practical results, and at the same time hope that this paper for the optimization of the design of such systems and operation and management to provide a reference.
17DCS molybdenum iron feeding system brief description and evaluation
The ferromolybdenum feeding system is mainly composed of DCS centralized control system (Dis-tributedControlSystem), high level storage silo, reduction scale, screw conveyor mixer and other parts.
The function of the whole system is to use METTLER TOLEDO IND560 weighing terminal and PC operation station to form a centralized and decentralized control mode, smelting molybdenum and iron various pre-stored in the storage silo of raw materials, through the DCS system of the formula input function, accurate confirmation of the setup of the operating data, to be reduced to the scale to reach the target value of the set weight to stop continuing to feed, and then after the adoption of the PID closed-loop, variable frequency After adopting PID closed-loop, frequency conversion control, SmartControl self-learning adaptive adjustment technology working mechanism of the reduction scale for smooth control, according to the set ratio of the material will be unloaded, the material is mixed and stirred in turn, to be all brought together, through the subsequent screw conveyor mixer will be mixed material loaded hopper for molybdenum iron smelting process.
Reduction scale is the key equipment for precise control of the system, and its function is described as follows: the formula goes to the reduction scale controller from DCS, the controller confirms the formula and feeds it back to DCS, DCS sends out the batch start command and batch completion, and the signals of operation/failure/stop status, instantaneous and cumulative values, frequency converter speed signals, and DCS sends out the time synchronization commands, etc., all of which are all through the Profi-busDP field communication bus to complete a series of batching operation processes. Complete a series of dosage operation process. The electronic scale control terminal has the functions of flow output, instantaneous and totalized value output, calibration, drift correction, slow feeding weight error correction, system interlock, self-learning mode, TRAXDSP digital dynamic filtering technology, high-speed A/D processing technology, software anti-jamming, etc., and there is a communication port connecting to the DCS control system, which has the function of data redundancy fault-tolerant processing technology, recipe power failure memory and fault interlock. DCS has data redundancy and fault-tolerant processing technology, formula power failure memory and fault interlocking function, on-site control has emergency stop and fault instant alarm function.
The programmed PC interface of DCS operation station is rich in functions, and it can realize remote real-time supervision and control of dynamic data through industrial Ethernet, which can guarantee the reliability of the system and the precision of dynamic measurement, and provide historical trend graph of dosage data for query. The system is equipped with METTLER TOLEDO C750.CF controller, FWC weighing module, LIW-SS-xxx-000 feeder, Danish DanfossVLT2900 frequency converter German SEW feeding motor, French Schneider low-voltage electrical device, American DEIL industrial computer and other high-quality equipment, equipment with excellent performance and reliable operation.
Under the production condition of various material components uniformity, the feeding system can realize continuous and balanced dosing, it is easy to control the scale of single furnace molybdenum iron smelting, the normal operating condition is excellent, the material is up to the standard of the use of the ideal effect, the smelting reaction is excellent, it can save the use of furnace material heating agent to ensure the optimization of the quality of molybdenum iron, which is conducive to the optimization of the production cost, optimization of the environment at the site of the dosing, the accuracy of the weighing of materials is quasi-precision, the dosage control Safe and reliable, high degree of automation, low labor intensity. The important thing is that the amount of stirred material in the screw mixer is controlled reasonably and continuously in the unit time period, the mixing effect of ferromolybdenum mixture is better, and it realizes the optimal parameter control of smelting ferromolybdenum by the extra-furnace method.
2 Process problem analysis
(1) ferromolybdenum material mixing method is through the reduction scale will be the material unloaded in accordance with the control, after the screw mixer for mixing, that is, the use of time difference control mode to start each loss-in-weight scales in turn for the downstream material mixing. In essence, the sequence of materials in the 2 ~ 6 points cumulative pre-mixing and mixing, only when all the materials to reach the 7th point after the complete mixing and stirring, it is clear that the process can only ensure that the material to reach a specific accumulation of mixing point of the instantaneous homogeneity of the material, if the batch of material composition is not homogeneous, with the dosage time will lead to the whole system of materials to produce deviations. This shows that, if you want to achieve the desired effect of material mixing, to ensure that the dosage process is smooth and accurate, the stability of the output flow of the reduction scale material and the uniformity of the composition of the unit batch of material should be used as the focus of the process of pre-control, and at the same time, more stringent control of the material specifications, otherwise there may be a weight in line with the uniformity of the composition of the distortion of the false phenomenon occurs, the raw material specifications and characteristics of the requirements of the Table 1. Process to achieve good results is based on the stability of the material composition to ensure that in our country due to various constraints in the actual production of the impact of the actual results are often not quite satisfactory.
(2) batching machine feeding mode is through the bucket elevator will be a variety of materials through a spiral channel delivery to the storage silo, segmented feeding process inevitably leads to a small amount of material between each other entrainment tampering mixing, affecting the authenticity of the material composition, and the result is likely to lead to the oxidation, reduction of diametrically opposed nature of the material in the storage silo at a certain point of the accumulation of materials, although in the state of the industrial scale of the composition of the material of the phenomenon of micro-deviations Although in the industrial scale state of the material composition of the micro-deviation phenomenon is allowed to exist, but the actual production of the accumulation of each under the mouth of the material and the control valve opening error will cause the material mixing, increasing the potential risk of accurate dosage.
(3) system dust collection using a centralized dust collection process, coupled with frequent feeding, a specific time period on the single nature of the material, and most of the material must be dry and fine particle size, very easy to cause material loss of flying, that is, the rate of material dust increased. After the collection of dust collection material is diverse and layered distribution, the composition of the material is difficult to determine, from a strict process point of view is not desired to produce such materials. In accordance with the usual practice, usually only a simple treatment after the use of manual addition of the way back to the dosage system, there may be a greater potential risk of further affecting the accuracy of the material composition, but also cause some of the dust collection branch pipeline empty phenomenon.
(4) reduce the size of the spiral output part of the scale specifications are based on the material output and material characteristics and tailored from the stability of the material flow and weighing accuracy and other considerations, the spiral blade and the shell cavity wall is bound to be tightly designed, the actual production of the material specifications and easy to cause the spiral cavity, especially in the scale spiral blade part of the wear speed up to meet the requirements of the normal flow rate of output, the maintenance is frequent and cumbersome. Maintenance is frequent and cumbersome. According to the working principle of the reduction scale, the reduction of material output per unit of time will inevitably result in the completion of the set weight of the daily standard value of the time lag, resulting in the dosage process of the material unloading set the synchronization of the deterioration of the impact of the uniformity of the mixture. Serious wear and tear of the spiral blade will make the subsequent conveying spiral cavity of the material accumulated too much, affecting the overall material balance of the dosage system.
3 Application optimization program
(1) in order to optimize the process, improve the raw material of the original uniformity, high storage silo "mother and child warehouse" hook chemical transformation, choose in the material mobility is good in some storage silo high inside, separated to make a uniform distribution of the same specifications of the 5 cone small silo, the lower end of the discharge is brought together, and the upper loading port to add a screen to prevent the first level. The upper loading port is equipped with a screen to prevent large materials and debris from falling into the bin, making a simple material homogenizer. Through the overhead crane alone on the way to the 10t batch of materials are spread in each sub-bin, the use of points, poly, points of the lower port control valve device, the use of storage bin materials have a high gravitational potential energy for the drop process of self-mixing, not only to ensure that each 10t unit of the batch of material grade homogeneity, but also to reduce the mixing equipment to reduce energy consumption, reduce the loss of flyer.
(2) in order to simplify the batching dust collection powder processing procedures and effectively reduce the dust collection induced draft fan energy consumption, split dust collector transformation, according to the amount of dust generated by the material, selectively in the upper part of the corresponding silo design specifications of different simple bag filter dust collection work, and according to the size of the dust rate design of the different diameter to control the induced air flow, the induced air branch pipeline is installed into a 30 ° cut angle and people induced air duct, and the pipe elbow using a large obtuse angle design to reduce the resistance loss of pipe elbow to complete the filter bag blowback cleaning and control of the working state of the pipe with an off-line pulse control system. The pipe elbow adopts large obtuse angle design to reduce the elbow resistance loss of the pipe, and the offline pulse control system is used to complete the filter bag blowback cleaning and pipeline working condition control. Through the projection of the dust collector resistance proved that the effect is very good, the induced draft fan matching power can be effectively reduced. Dust collector materials are separately separated and stored in their respective storage silos to avoid confusion and cross between the materials, to ensure the homogeneity of the materials, so that the dust is accurately and automatically returned to be collected in the corresponding silo, and then reasonably into the batching process.
(3) for some reduction scale material output is not smooth problem of structural transformation, according to the material dynamic placement angle and density of accumulation parameters set different cone tilt angle of the silo, in the specific gravity of small, easy to absorb the phenomenon of moisture bonding shed material silo installed low-speed mechanical rake arm and micro-vibration device, in the material mobility is good reduction scale scale of the upper part of the spiral set up umbrella-shaped anti-impact anti-squeeze structure, dispersion of material on the helix of the direct Pressure, not only to ensure that the spiral blade of the full load operation and effective protection of the spiral blade, slow down the wear and tear speed, so that the reduction scale spiral processing capacity from the previous 800t to 2000t or more. At the same time, the spiral shell can be detached and fitted design, which is convenient for the maintenance of the spiral blade.
(4) the current process of the reduction scale to open the use of time difference control, this time setting parameter is in a certain period of time by the experimental verification, with the change of materials and equipment conditions and the timeliness of the deterioration of the material flow if the change in the mechanical application of this parameter, will inevitably affect the mixing accuracy of the material, changed to the sensor control, and symmetrical layout of certain silos, and strive to improve the degree of synchronization of the unloading of reduction scales, the material real-time Real-time mixing control accuracy can be improved.
Discussion of the effect
4.1 Material uniformity analysis
Smelting scale of 3.8t molybdenum oxide / furnace batching completion time totaling 18min, every 3min will be the material segmented sampling, sample preparation before the removal of steel chips to facilitate the preparation, and then use XGT-1000WR (HORIBA, Japan) X-ray fluorescence spectrometer to detect a representative of the content of the elements of Mo, Si, Fe, Ca, Al, used to check the homogeneity of the material. The measured compositions are shown in Figure 5, and the test results show that the homogeneity of the molybdenum-iron mixture material composition can be guaranteed.
Reaction condition, energy consumption, alloy segregation analysis 4.2 Smelting reaction continuous and smooth, 8~12min per furnace, which is a reflection of the material composition uniformity of the significant features, thus making the furnace heat loss is greatly reduced, as the furnace outside the method of smelting process, which is particularly important for the improvement of slag fluidity, metal recovery rate and molybdenum iron crystal structure improvement, alloy segregation from the original +5% down to +3%, the The compositional homogeneity of ferromolybdenum was improved. With the composition close to the molybdenum roasting sand smelting energy consumption analysis of energy consumption indicators after the transformation, the analysis results further verified the molybdenum iron smelting energy consumption indicators in the material uniformity improvement at the same time can be effectively reduced law.
5 Conclusion
(1) In the process of iron molybdenum batching, it is recommended to adopt DCS control system with the use of V-type mixer for iron molybdenum material mixing, the control system can be effectively simplified;
(2) The dosing process, although the preparation of ferromolybdenum smelting material specifications and quality control requirements are high, but the quality of ferromolybdenum and other production indicators have a positive and favorable effect on the improvement of the quality of ferromolybdenum, should be paid attention to;
(3) Through the further optimization and transformation of the feeder structure can improve the scientific nature of the equipment configuration, greatly enhancing the practical performance of the system;
(4) Improve the equipment level of ferromolybdenum smelting is the production of high-quality products, China's molybdenum smelting industry should be upgraded to the direction of the equipment to further enhance the competitiveness of China's ferromolybdenum products in the international market.