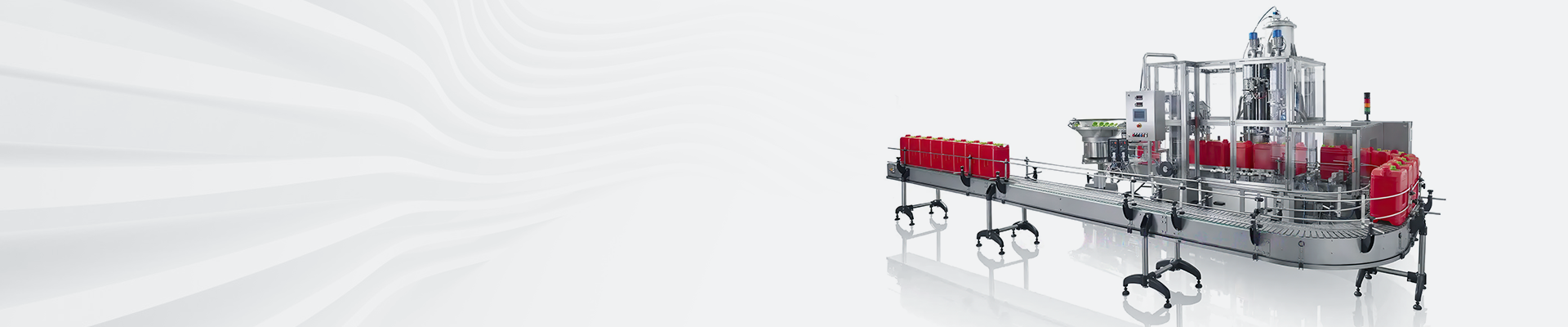
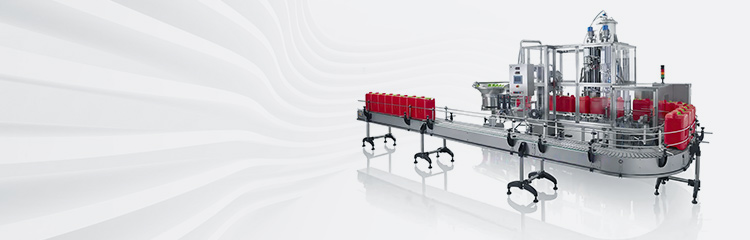
摘要:在钼铁冶炼配料中装备先进的DCS控制系统,可确保钼铁配料称重的精准度,提高钼铁冶炼混合物料的均匀度。通过对系统性能进行分析及评价,经过进一步的优化改造,为提高钼铁质量提供可靠基础保证,在钼铁配料生产中取得了较为满意的使用效果。
0前言
众所周知,在炉外法冶炼钼铁过程中,前期配料操作是工艺的关键控制环节,而钼铁混合料成分的准确性是决定冶炼效果的工艺控制重要基础参数之一。
目前,圆筒混合机和V系列混合机在我国钼铁冶炼中广泛用作配料和混合设备。虽然它具有投资小、操作简单等优点,但不同程度地存在测量精度差、物料均匀性不理想等问题,制约了钼铁质量的提高。AMEC和恩飞设计的DCS称重控制系统用于钼铁配料的实际生产中。在钼铁的实际生产实践中,经过对系统实际性能的评估分析,确定了进一步优化改造实施方案,取得了满意的实际效果。同时,希望本文能为此类系统的优化设计和运行管理提供参考。
17DCS钼铁投料系统简述及评价
钼铁给料系统主要由DCS集中和分散控制系统、高位料仓、还原秤、螺旋输送混合机等部分组成。
整个系统的功能是使用梅特勒-托利多IND560称重终端和PC操作站,形成集中和分散控制模式,将钼铁冶炼的各种原料预先存储在存储料仓中,通过DCS系统的公式输入功能,准确确认操作数据的设置,待秤缩小到达到设定重量的目标值时停止继续给料,然后采用PID闭环后,变频调速采用PID闭环后,变频控制,SmartControl自适应调节技术对工作机构的还原秤进行平稳控制,按照设定的比例将物料卸下,物料依次进行混合和搅拌,待物料全部汇集后,通过后续的螺旋输送混合机将混合后的物料装入料斗,用于钼铁冶炼过程。
配料秤是系统精确控制的关键设备,其功能如下所述还原秤是系统精确控制的关键设备,其功能如下所述:配方从DCS到达还原秤控制器,控制器确认配方并反馈给DCS,DCS发出批量启动命令和批量完成信号,以及运行/故障/停止状态、瞬时值和累积值信号。变频器速度信号,DCS发出时间同步命令等,所有这些都是通过Profi-busDP现场通信总线来完成一系列的配料操作过程完成一系列的配料操作过程,电子秤控制终端具有流量输出,瞬时和累计值输出,校准,漂移校正,慢速给料重量误差校正,系统联锁,TRAXDSP数字动态滤波技术,高速A/D处理技术,软件抗干扰等功能,并有一个通信端口连接到DCS控制系统,该系统具有数据冗余容错处理技术、配方断电记忆和故障联锁功能
DCS具有数据冗余和容错处理技术,公式停电记忆和故障联锁功能,就地控制具有紧急停机和故障即时报警功能
DCS操作站的程控PC界面功能丰富,可通过工业以太网实现动态数据的远程实时监控,保证系统的可靠性和动态测量的精度,并提供剂量数据的历史趋势图供查询。该系统配备了梅特勒-托利多C750。CF控制器、FWC称重模块、给料机、丹麦DanfossVLT2900变频器、德国SEW给料电机、法国施耐德低压电器、美国DEIL工业电脑等优质设备,设备性能优异,运行可靠。
在各种物料成分均匀的生产条件下,给料系统可实现连续、均衡配料,易于控制单炉钼铁冶炼规模,正常操作条件优良,物料达到理想的使用效果,冶炼反应良好,可节省炉料加热剂的使用,保证钼铁质量的最优化,这有利于优化生产成本,优化加药现场的环境,物料称重的准确度为准精密,加药控制安全可靠,自动化程度高,劳动强度低。重要的是合理、连续地控制单位时间内螺旋混合机内的搅拌物料量,钼铁混合物的混合效果更好,实现炉外冶炼钼铁的最佳参数控制。
2工艺问题分析
(1)钼铁物料混合方式是通过减量秤将物料顺控卸出,后经螺旋搅拌机进行搅拌的方式,即利用时间差控制模式依次启动各个失重秤进行下料混合。其实质为各物料顺序在第2~6点累加进行预混合搅拌,只有当全部物料到达第7点处之后彻底完成混合搅拌,显而易见该工艺只可保证到达物料特定积聚混合点的瞬时均匀度,假若批次物料组份不均匀,随着配料时间的推移将导致整个物料体系产生偏差。由此表明,若要到达预期的物料混合效果,保证配料过程的顺畅、精准,减量秤物料输出流量的稳定性及单位批次物料组份的均匀性应作为工艺前期的控制重点,同时对物料规格的控制更为严格,否则可能出现重量相符而组份失真的均匀假象发生,原料规格要求及特性见表1。国外利用该搅拌工艺取得良好效果是基于物料组份的稳定性来保障的,在我国由于实际生产中的种种制约因素的影响,实际效果往往不甚尽如人意。
(1)钼铁物料混合采用减量秤依次出料,然后用螺旋搅拌机搅拌的方式,即利用时间差控制方式依次启动各失重秤下料和搅拌,钼铁物料混合采用减量秤依次出料,然后用螺旋搅拌机搅拌的方式,利用时间差控制方式依次启动各失重秤进行下料和混合,这一过程的实质是在第2-6点对所有物料进行预混合和累积搅拌,只有当全部物料到达第7点处之后彻底完成混合搅拌,显而易见该工艺只可保证到达物料特定积聚混合点的瞬时均匀度,假若批次物料组份不均匀,随着配料时间的推移将导致整个物料体系产生偏差。由此表明,若要到达预期的物料混合效果,保证配料过程的顺畅、精准,减量秤物料输出流量的稳定性及单位批次物料组份的均匀性应作为工艺前期的控制重点,同时对物料规格的控制更为严格,否则可能出现重量相符而组份失真的均匀假象发生。原材料规格的要求和特点。国外采用这种混合技术取得的良好效果是基于材料成分的稳定性。在中国,由于实际生产中各种限制因素的影响,实际效果往往不尽如人意。
(2)配料机的给料方式是通过斗式提升机将各种物料通过螺旋通道输送到各料仓。在分段投料过程中,不可避免地会夹带少量物料,并相互混合,影响物料成分的真实性。因此,具有截然相反的氧化和还原特性的材料可能会在储料仓的某一点堆积。虽然在工业规模上允许物料成分的轻微偏差,但实际生产中各出料口的累积和控制阀的开度误差都会导致物料混合。
(3)系统采用集中除尘技术,结合给料的频率,特定时间段给料的单一性,大部分物料必须干燥、粒度细,容易导致物料飞散损失,即物料粉尘率增加。收集的集尘材料是多样化的,呈层状分布,材料的成分难以确定,从严格的技术角度来看这是不可取的。按照惯例,通常经过简单处理后通过人工添加的方式返回配料系统,这可能存在较大的潜在风险,进一步影响物料成分的准确性,还会导致一些集尘支路被清空。
(4)根据物料产量和物料特性定制秤的螺旋输出部分的规格。考虑到稳定的物料流动和称重精度,螺旋叶片和壳体内腔壁必须紧密设计。在实际生产中,容易因材质规格造成螺旋腔卡死,尤其是秤中螺旋叶片部分磨损较快,达不到正常流量输出要求,维修频繁繁琐。根据减量秤的工作原理,单位时间出料量的减少必然导致设定重量的日标准值的完成延迟,从而导致配料过程中出料的设定同步性变差,影响混合料的均匀性。螺旋叶片的严重磨损会使螺旋输送机腔体内的物料堆积过多,影响配料系统的整体物料平衡。
3应用优化方案
(1)为了优化工艺,提高原料原有的均匀性,对高位料仓的“子母仓”挂钩进行了改造。在一些物料流动性较好的高位储料仓中,分别制作了5个规格相同的小锥形料仓,均匀分布,下部出料端汇集在一起,上部装料口加装一级筛网,防止大块物料和杂质进入料仓,从而制作出简易的物料均化器。天车分料的方式将10t批次的物料均匀撒布在各子仓中,利用分料、集料、分料口的控制阀装置,利用储料仓中物料的高重力势能进行下落过程中的自混合,既保证了每10t单位批次物料的级配均匀性,又降低了混合设备的能耗和飞散损失。
(2)为简化炉料除尘处理工序,有效降低除尘引风机能耗,对分体式除尘器进行了改造,为简化炉料除尘处理工序,有效降低除尘引风机能耗,根据物料产尘量对分体式除尘器进行了改造,在相应的料仓上部有选择地设计不同规格的简易袋式除尘器进行集尘,并根据含尘率的大小设计不同的管径以控制进风量。每个进气支管以30度的切线角安装并与进气管连接,管道弯头设计成大钝角,以减少管道弯头的阻力损失。采用离线脉冲控制系统对除尘器阻力进行计算,证明效果很好,可有效降低引风机的匹配功率。集尘材料分开存放在各自的储料仓中,以避免材料之间的混淆和交叉,确保材料的均匀性,使灰尘准确地自动返回相应的料仓,然后合理地进入配料过程。
(3)针对部分减重秤出料不畅的问题,进行了结构改造。根据动态设定角度和堆积密度参数,设定不同的料斗锥倾角,在比重小、易吸潮的料仓内安装低速机械耙臂和微振动装置,在物料流动性好的秤内螺旋上部安装伞形抗冲击防挤压结构,分散物料对螺旋的直接压力,既保证螺旋叶片满负荷运行,又有效保护螺旋叶片,延缓磨损速度,减少物料。同时,蜗壳的可拆卸组合设计便于螺旋叶片的维护。
(4)现工艺对各减量秤开启采用时间差控制,此时间设置参数是在某一时间段由试验验证得出,随着物料及设备状况的改变而时效性变差,若物料流量变化而机械地套用此参数,势必影响物料混合精度,改为传感器控制,并对某些料仓进行对称布局,力求提高减料秤卸料的同步程度,物料实时搅拌控制精度得以提高。
效果讨论
4.1物料均匀度分析
冶炼规模为3.8t氧化钼/炉的配料完成时间共计18min,每隔3min将物料分段取样,试样制备前将钢屑剔除便于制备,后用XGT-1000WR(日本HORIBA)X射线荧光光谱仪检测具有代表性的Mo、Si、Fe、Ca、Al元素含量,用于检验物料的均匀度。实测组份见图5,检测结果显示,钼铁混合物料组份的均匀度可得到保证。
反应状况、能耗、合金偏析度分析4.2冶炼反应连续平稳,每炉8~12min,这是反映物料组份均匀的显著特征,从而使炉内热损失大为降低,作为炉外法冶炼工艺,这一点对熔渣的流动性改善、金属回收率提高及钼铁晶体结构改良显得尤为重要,合金偏析度由原来的+5%降为+3%,钼铁的组份均勾度得以提高。用成份接近的钼焙砂冶炼能耗分析改造后能耗指标状况,分析结果进一步验证了钼铁冶炼能耗指标在物料均匀度提高的同时可得到有效降低的规律。
5结语
(1)在钼铁配料过程中,建议采用DCS控制系统配合使用V型混料机进行钼铁物料的搅拌,控制系统可有效简化;
(2)配料工艺虽然对钼铁冶炼物料的制备规格及质量控制要求较高,但对钼铁质量等生产指标的提高有积极的利好作用,应予重视;
(3)通过对喂料机结构的进一步优化改造可提高设备配置的科学性,极大增强系统的实用性能;
(4)提升钼铁冶炼的装备水平是生产优质产品的前提保障,我国钼冶炼行业应向装备升级方向发展,进一步提升我国钼铁产品的国际市场竞争力。