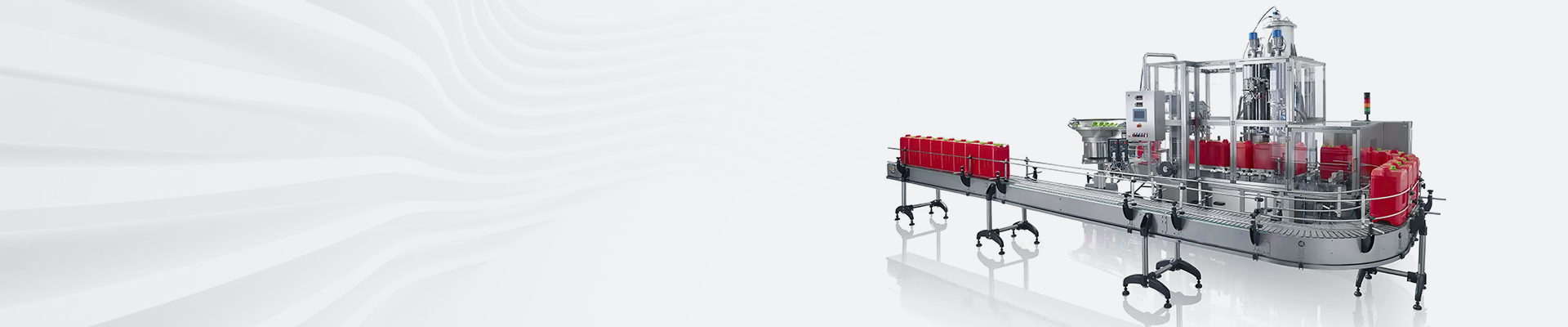
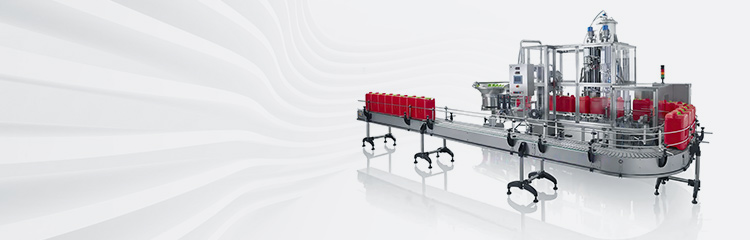
摘要:称重混合机实现的是在运输过程中完成配料过程,选择螺旋进行一定比例输送的原料进行混合。可对物料进行搅拌、混合、加热和冷却等工艺,以变频器控制电机调速实现自动控制。
在饲料加工生产中,工艺流程通常分为原料接收、清洗粉碎、配料、混合、造粒、成品包装等几个工段。其中,配料和混合是两个独立的部分,需要单独的配料秤和混合器。工艺复杂,设备投资大,占用空间大。许多国外公司已将配料和混合设备合二为一,这样可以充分发挥设备的效率并降低成本。我国在该领域的研究基本处于发展阶段,主要存在混配周期长、配料精度低、体内残留高等问题。针对这种情况,我院在国家“九五”科技攻关项目“饲料加工新型关键设备研制”中完成了快速称重式搅拌机的研制。
混合机机体选用单轴桨式混合机,具有双轴混合机混合时间短、混合均匀度高的特点,价格比双轴混合机便宜,占地面积小,便于工艺安排。由于系统采用了高速给料装置、变频控制、风量自动校正等控制技术,提高了配料的精度和速度。水平国内领先。
1快速称重混合机系统简介
该系统由单轴桨叶式混料机、高速给料机构、称量模块、配料称重仪表及相应的控制软件组成。
1.1主要技术性能指标
配料混合周期≤5min配料精度为0.2%(F.S);混合均匀度(CV)<5%;混合时间≤2min;配料种类不少于14种。
2混合机的结构形式
单轴桨叶式混合机是目前新型的混合设备,它对物料的适应性强,混合时间短,混合均匀度高。新颖、可靠的出料门结构,保证了混合机快速、高效,而且价格较双轴混合机便宜。
2.1试验条件试验物料:玉米粉
物料水分:15.2%
粉料粒度:粉碎筛片孔径中2.5mm
3高速给料装置与控制
对于快速称重混合机而言,其主要特点是高速给料,通过高速给料来缩短配料时间,以提高小时产量。对于配料精度而言,随着配料速度的提高,配料精度会随之下降。而配料精度又是决定产品质量的关键。所以速度与精度是一对矛盾体,如何使两者结合成最佳状态,变矛盾为统一体,这是关键技术。采用的设计方案如下。
3.1采用单、双绞龙喂料
对于大配比物料(例如玉米、麸皮等)快给料时采用双绞龙同时喂料,慢给料时采用单绞龙喂料,使大配比物料的给料(配料)时间缩短一半。
3.2采用变频控制技术
快给料时电机工作频率在50~60Hz之间,慢给料时电机工作频率在5~10Hz之间,该项技术的应用在保证高速给料的同时又兼顾到配料精度不受影响。
3.3采用空中量自动修正技术
对于各种小配比物料的添加,由于添加组分在加人混合机后无法减除,因此需要采用提前控制及时停止喂料的方法进行喂料控制,即称重控制仪表自动检测喂料机构停止喂料后的空中量作为下一次控制的提前量,避免添加量超差,以提高控制精度。
3.4对喂料绞龙进行特别设计新设计的喂料绞龙使物料在出口处能较为均匀地下料,以提高配料精度。
4投料系统
混料机运行过程中,物料不断翻滚,因为物料波动引起的振动会传递到称重模块,使称重仪表显示的重量跳动(即使搅拌机内没有物料)。跳跃值越大,配料精度越差。因此,混合材料的重量表明跳跃是不可避免的。因此,除了在设备设计和安装上采取必要的措施外,还必须在给料系统的软件和硬件上采取特殊的解决方案。通过反复试验,研究了混料机空载点、满载点和负载点的重量跳变范围,找出了具有规律性的数学模型,并据此进行软硬件的重量稳定性滤波。
4.1仪表软、硬件的处理
仪表硬件采用有源滤波处理,软件采用多重平衡找中间值运算、滚动式数字滤波技术,并且滤波常数可以设定。
4.2称重仪表的设计
称重仪表的设计开发综合应用了单片机、微电子技术、高分辨率快速模数转换(ADC)等多项技术。针对工业现场严重的电磁干扰,仪器采用了多种软硬件抗干扰技术。硬件上除了采用常规的隔离变压器、无源滤波器、有源低通滤波器、称重小信号屏蔽和接地技术外,还对模拟量输入/输出和开关量采用了一级或两级光电隔离等抗干扰措施。软件采用了多种数字滤波算法和滚动数字滤波算法,使称重显示值更加准确稳定,保证了系统的长期稳定安全运行。
4.3称重精度和精度的漂移的选定
为了使称重仪表的称重准确度和精度漂移达到或超过国家标准,仪表模拟电路选用超低温漂精密电阻、高精度放大器和ADC器件,连接称重模块采用先进的六线技术、差动平衡输入和软件零点自动跟踪技术,使仪表的称重准确度能够长期稳定,达到国家计量技术标准。
4.4系统软件
系统软件包括数据采集、数据处理、数据控制、模糊控制、报警监测及通讯等功能。
4.4.1数据采集和处理程序
数据采集程序是通过称重仪表采集传感器数据,然后通过V/F转换器得到相应的频率值。频率值与显示的重量值成正比,其比例因子是通过大量实验,再通过数据统计处理确定的。为了保证采样数据的准确性,提高控制精度,需要对采集的数据进行软件滤波,滤除瞬时干扰,然后通过非线性校正,得到正确的数据。
4.4.2控制程序
控制程序采用闭环控制,根据采样值与设定控制参数的比较,决定调整送料机构。控制程序采用闭环控制,根据采样值与设定控制参数的比较,决定调整送料机构。由于送料机构的惯性,简单的闭环控制无法精确控制送料时间,响应速度跟不上,因此,新软件采用模糊控制理论的控制方法。程序首先跟踪重量变化,预测重量变化趋势,产生超前控制量,并消除惯性造成的影响。然而,这个超前量是一个不确定量。经过大量试验后,根据预测量获得一套模糊控制技术,自动选择适合当前状态的模糊控制模式。用这种方法控制送料机构,再配合变频器控制,使送料机构不仅像以前一样匀速运行,而且模拟连续控制,从而解决了送料量难以控制的问题,保证了系统的控制精度,满足了最终的设计要求
5结论
应用快速称重混合机系统以后,动态配料精度由以往的0.3%(F.S)提高至0.2%(F.S)。混合机混合均匀度高,并且生产过程中的物料残留量低,这样提高了产品质量,增加了产品的竞争力。另外,该系统比以往同类设备节约空间高度约3m,建厂基建成本可相应下降,工艺设计更具灵活性。由于设备简单,制作成本及设备维护成本也随之下降提高企业的经济效益。再者该系统没有以往的秤体,从而避免了秤体开门喷料影响环境,改善了劳动环境。该项成果不仅应用于饲料行业,还可广泛应用在制粉等其他行业。