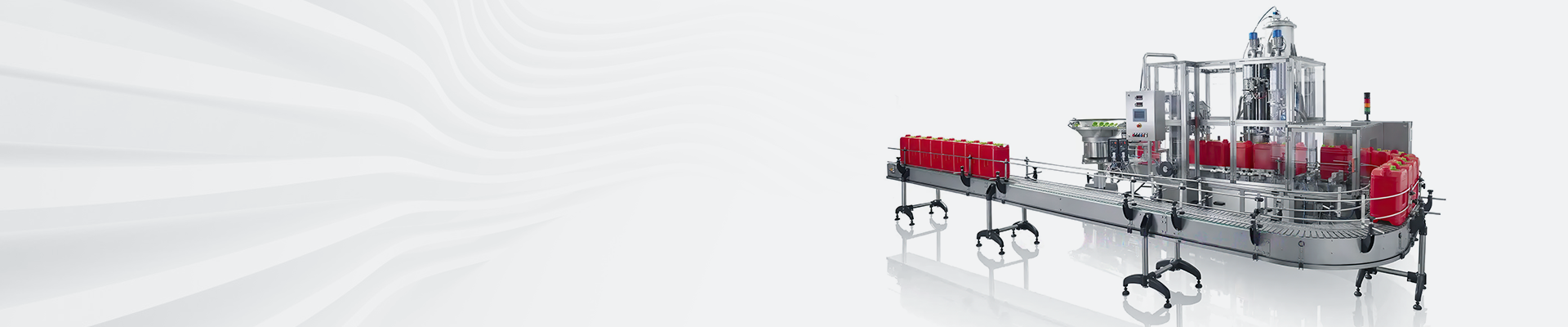
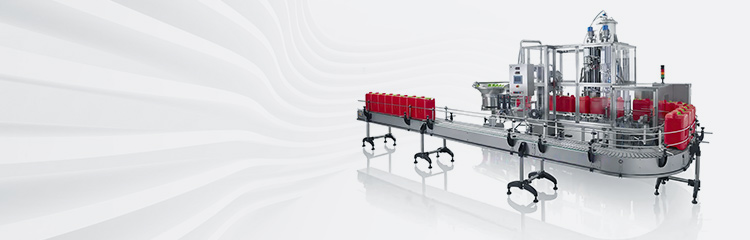

Summary:The automatic batching system starts under the control of the programmable controller and outputs other signals (loading, unloading, etc.).All feeding equipment motors are controlled by frequency converters, using a positive pressure high-density phase pneumatic conveying system consisting of an air compressor and a rotary valve.
The automatic dosing system is the basic liquid arriving at the most fundamental and primary process loop of the paint manufacturing process. Correct weighing and dosing work, as required by the process recipe, is the basis for ensuring that the required amount of liquid control is available for the production of paints. If the liquid control volume is not up to standard, or if there are unavoidable small deviations in each metering placement, the deviations must be controlled within acceptable limits or the performance of the final product will be affected. Using the existing industrial electronic scales or general weighbridge measurement, due to the presence of the human factor, the measurement of repeated accuracy is not high, open manual operation is difficult to ensure good process hygiene conditions, and therefore prone to deviation measurement. Therefore, the operation mode of automatic liquid supply and dosing is the best way. In recent years the production technology of the paint industry has been improved and updated. With the introduction of the Paint Safety Act, the requirements for paint safety have also increased. The working mode of automatic weighing and mixing automatic dosage system is gradually applied and popularized.
Process and Configuration
1) Design Concept
The automatic dosing system consists of storage reaction tank, supply system, weighing control system, mixing equipment, conveying equipment and control system.
Main functions: receiving and storing liquids (in bulk or in iron drums); distribution and mixing of different liquids and deposited liquids; distribution to intermittent or continuous dosing tanks. It is suitable for the batch production of coating companies that need liquids. This dosage production is measured and efficient, solves the heavy physical labor of customers carrying liquid manually, saves labor, solves the deviation of liquid in the process of carrying and the waste of residual liquid in the process of opening, saves the storage of liquid reaction tanks, reasonably uses the space, and flexibly sets up the point of preservation and the point of use. The automatic dosing system is automatically controlled by programmable controller, which can continuously store, use and dispense liquid without manual control.
2) Process Flow
Weighing and dosage system has two sets of receiving and weighing control system: set of batch receiving and dosage, batch vehicles are transported to the temporary liquid reactor by discharging positive pressure. Automatic dosage system: manually open the filling, pouring into the discharge port reaction tank, transported to the ground reaction tank through positive air pressure.
The liquid from the reaction tank is discharged from the reaction tank via diaphragm pump, screwed by the reaction tank, checked and delivered to the mixing reaction tank by positive air pressure. The liquid from the mixing reaction tank is discharged from the reaction tank via a diaphragm pump and the tube screw propeller is discharged from the reaction tank. In other words, the heavy liquid is stirred using a dosing screw propeller and the tube screw propeller is mixed into the reaction tank through a distributor. Setting up the magnetic separation process during transfer.
Due to the high-density phase pneumatic conveying, the de-dusting system requires only a small amount of inhalation of the de-dusting relatively mobile hopper, the air compressor hopper and the liquid reactor tank; the metering of the de-dusting is transported to the liquid reactor by pneumatic means. A separate plug-in pulse dust collector is installed for the batch reactor tank.
Dosing configuration
1)Storage of liquid: the liquid reactor is made of SUS304 steel plate with actual thickness of 3-5mm.
2)Transportation system: main parts, diaphragm pump unloader, screw holes, positive pressure blower, Roots blower, transportation pipe network, double pass valve, dust automatic dosing system, etc.
3)Mixing system: composed of storage reaction tank, diaphragm pump unloader, spiral, gate, inspection sieve, magnetic separator and so on.
4)High and low air pressure: high air pressure, liquid loading in the middle of the reaction tank at the specified height, high air pressure alarm, supply stop action. Protect the system to prevent clogging. In order to ensure the normal use of metering in the pneumatic, liquid reaction tank, when the metering layer reaches the specified position, a low pneumatic alarm will be issued, the dosage will be immediately supplemented by metering to ensure the continuity of production.
5) Dedusting air: including fan, pulse dust collector, butterfly valve and pipe network.
Equipment selection
(1)Bulk liquid
There is a bulk truck receiving unit (bulk trucks are transported in intensive stages). The bulk liquid enters the reaction tank through the discharge in the plant area generated by the air compressor, and the liquid particle metering is fluidized through the fluidization unit. Due to the pressure difference between the inside and outside of the tank, the liquid particle metering transports air along the discharge pipe to the above ground liquid segmented reaction tank.
(2) Liquid Discharge
The discharge of liquid from the iron drum is manually poured into a diaphragm pump screen in the supply area and transferred to the liquid reactor through positive pressure ventilation.
Utilizing the principle of probabilistic screening, the discharge diaphragm pump allows for a rational selection of screens to quickly screen difficult-to-filter urethanes and to obtain smaller separated particle sizes utilizing a large reaction tank and excitation frequency. Compared with the general control method, the body increases and the tendency to clogging is greatly reduced. The possibility of screening is increased. The control process is enhanced with a shorter control length than a typical screener, which does not affect the grade effect, and can be individually equipped with a small pulse dust collector to eliminate dust.
The equipment includes components such as frame, reaction tank frame, reaction tank tube, diaphragm pump motor, flexible connection, etc. The frame is fixed with square tubes and plates with u-shaped bolts, which are beautifully shaped, easy to wear and of high strength. The screen tube is as a steel welded structure and the screen frame is accommodated inside. Diaphragm pump motor is small in size, light in weight, easy to install, low noise, and the soft connection metering can be adjusted into the canvas bag. Screen and metering can be configured according to user requirements.
(3) Pneumatic conveying
The automatic feeding system uses a positive-pressure, high-density phase pneumatic conveying system consisting of an air compressor and a rotary valve, which is directly conveyed to the reactor, with power provided by the compressor. The dosing pressure is high and the flow rate is low, but the carrying capacity is large and has little effect on the material. High pressure is required during transportation, so the liquid substance will be clogged. Accordingly, the liquid transport pipes are fitted with auxiliary ducts, unblocking pipes and valves according to the metering layout of each transport unit. The blocking should be placed along the liquid delivery metering. The outer diameter of the blocking arm pipe is φ50~φ100mm, the diameter of the branch pipe is φ40~φ65mm, and the horizontal angle between the blocking branch pipe and the liquid delivery pipe is not more than 30. Check valves, plug valves, or ball valves must be installed in the sewer metering near the liquid delivery metering. Dust collector-treated metering is conveyed back to the liquid reactor through the existing positive gas pressure. A Roots blower provides the discharge source. To prevent pulse discharge, install an outlet injection port at the bottom of the pulse to fluidize the reactor tank.
(4) Reaction Tank Design
The reaction kettle is customized in a round shape, and the angle of the cone at the bottom of the liquid reaction tank is not less than 70 degrees, which helps the liquid to enter the diaphragm pump unloader smoothly. the tank of the REACTOR main body is made of SUS304 steel plate with an actual thickness of 3-5mm, and the flanges are connected with high-strength external hexagonal bolts. The bottom of the reactor is also made of SUS304 steel plate with actual thickness of 3-5mm by bending and welding, and the whole bottom of the reactor is welded with reinforced metering, which ensures the bearing capacity of the bottom of the reactor. In order to prevent the liquid cam, in the production process of the reaction kettle designed a reaction kettle external decompression device. According to the paint factory paint safety needs, the nuclear reactor needs to be cleaned regularly, special installation of discharge injection automatic dosing system.
(5) Measuring and mixing system
In order to reduce the height and total investment of the steel workshop, the automatic dosage system adopts a new type of quantitative spiral system.
Dosing auger metering is ideal for continuous recording and weight (i.e., gravimetric) measurement of polyurethane or liquid end metering streams. This includes continuous mixing or blending of the metering, recording of weight during unloading, and continuous addition of trace ingredients. There are two functions: the mass flow can be measured continuously in it. On the other hand, the Mass Flow 3360 Mass Flow Measurement function records the mass of the material flow at preset output levels. The Mass Flow Management function measures and manages the material flow. The low mounting height of the dosing auger provides accurate measurements and easy field integration and control. Suitable for arrangement and small liquid preparation processes. The specific structure and model are as follows:
(6) Pneumatic valve selection
Pneumatic instruments and automatic valves are indispensable automatic components of the metering and dosing system. Pneumatic instruments are used to continuously measure and indicate the position of the dosage in the dosing reactor tank to prevent interruption of the automatic process due to lack in the dosing reactor tank. Automated valves are actuators that control the amount of feed during the automated weighing process and are automated components that allow for remote, centralized control. The proper selection of these two main automation parts directly affects the stability of the automatic dosage system and the economy of the automatic dosage system from which it is composed.