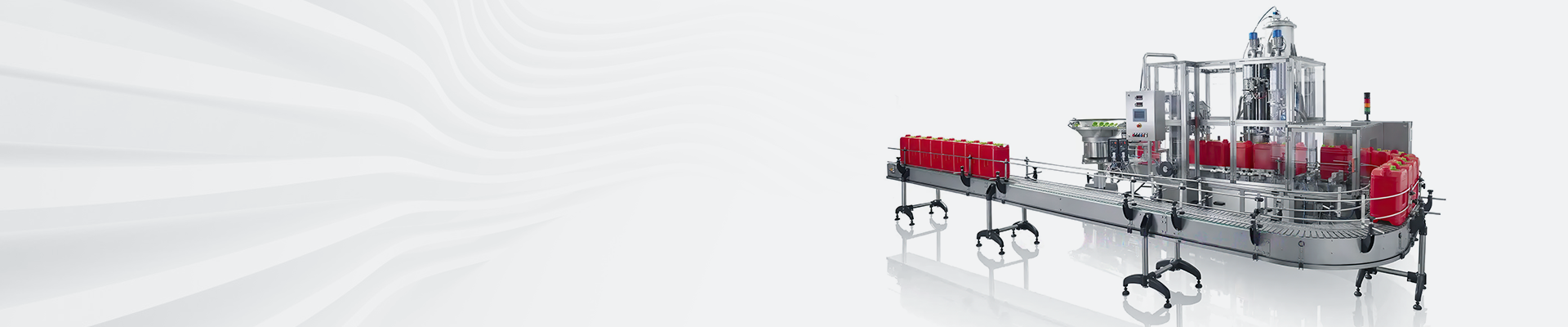
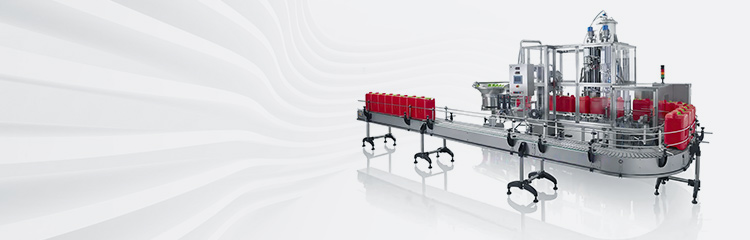

Summary:There is pollution in the paint filling process and it is not suitable for workers to operate for a long time.Based on the automatic filling machine production line and the on-site process flow of the paint filling production line, an automatic paint filling monitoring system is constructed.Through the communication mechanism between WINCC and PLC, the configuration plan of the host computer of the paint and dye filling system is designed.Ximenyu configuration software WINCCV7.3 and Step7V5.5 programming software are used to realize the display and process control of the host computer monitoring screen during the automatic paint filling process.The system operates reliably, reduces workers' labor intensity, and improves workers' working environment.Improve job safety.
0Introduction
Paint industry has developed more rapidly in recent years, paint as a chemical liquid industry, belongs to the flammable and explosive medium, it is difficult to realize the manual operation of the production process. Enterprises urgently need to increase the level of automation in the canning process to improve the competitiveness in the market.
PLC is a multi-type, miniaturized automatic control technology development of a new generation of industrial new control of the device, the use of digital computing, the implementation of control logic, arithmetic running operation will count the results of the digital or analog volume through the input / output channel, a variety of switches and buttons, sensors, the field of the signals such as the acquisition, and then through the function module to control a variety of industrialization of the actual production process. WINCC configuration software is on the computer in the use of the operating system under the monitoring and debugging of the operating screen and the actual production requirements for the creation of the human-machine interface, through the integration of the actual operating system, the use of interface communications will be WINCC configuration software and programming development software combined for use!
On the basis of the design of the paint automatic filling machine hardware composition scheme, the use of Siemens configuration software WINCCV7.3 and Step7V5.5 programming software, can be realized on the process control of the liquid filling machine mounted on the process control and the upper computer monitoring screen display and debugging of the process. In terms of automation control, it can greatly reduce the labor intensity of workers and improve the safety of real-time production.
1 paint weighing and filling machine structure
Structure of paint weighing and filling machine
(1) Conveying workstation. The initial station of the production line to complete the operation of moving empty bottles from the conveyor belt to the conveyor. Relying on the motor to drive the conveyor belt, move the empty bottles and bring them to the end of the conveyor belt; at the end, the sensor detects and controls the cylinder to push the bottles to the conveyor belt.
(2) Filling station. The core part of canning. Through the weighing module to sense whether the empty bottle is moved to the work station canning mouth below, the weighing module detects the signal, the PLC stops the conveyor, opens the canning head, completes the filling, and the conveyor line starts again. During the system operation, PLC monitors the level of the paint tank, and when it reaches the lower limit, the refill valve opens for refilling.
(3) Capping station. Before the bottle arrives, the cap should be taken beforehand. The use of sensors to determine the location of the bottle cap, to take the cap motor to move to the top of the bottle cap to take the cap; secondly, after taking the cap back to the top of the forthcoming set of cap station, and so on the bottle to reach this station, through the weighing sensor to detect the bottle, control the drive belt to stop; finally by the control of the set of cap motor lifting cylinder, with the rotation of the motor to complete the set of the cap action.
(4) Finished product off-line station. By the measurement module sensor with PLC counter to complete the counting operation, and then by the clamping cylinder to complete the clamping action. Lifting motor positive rotation, drive the unloading platform to rise, in place, the paint bottle is pushed out by the cylinder, lifting motor reversal, unloading platform down to complete the unloading.
2 filling system control hardware configuration program
2.1 Controller configuration
Automatic filling line filling system is monitored by the WINCC upper computer, the upper computer and the master station through the MPI network communication". The slave station consists of five sub-station controllers for the transportation of the lower can machine, conveyor belt detection, filling and capping station detection, finished product full bottle counting detection, and analog replenishment and feeding function. Among them, the master station of the filling production line adopts CP5611 communication card to establish communication with the host computer and slave station, and adopts Siemens 300 series new standard type CPU314PLC to realize the function of this station by adding signal module. The feeding detection station adds analog input and output expansion module SM334.
2.2 Filling system working principle
Weighing and filling machine through a certain function relationship will be converted to the weight of the weight transfer to the measurement system host, and this data with the host of rapid collection, real-time processing and filling of the corresponding components of the settings for comparison. If the two are the same, the host will send a control signal to start to stop filling, this component to stop filling. The original start automatic filling equipment control process, filling time is from the previous closed air pressure valve, from the start of the filling time, open the filling valve, put into the start, the view of the batch start into the paint bottle, if the start batch does not reach the number of times the preset start batch, the batch system will be the next batch, when the preset start batch to reach the start of the start, automatically stop the start, to complete the final start of the filling, each batch of filling The weight signal is transferred to the host computer for saving.
3.1 Filling system flow
Paint dyes automatic filling line through the lower cans of paint bottles conveyed to the assembly line, paint bottles transported to the transport belt, the photoelectric sensor on the transport belt to detect the signal of the bottle, which drives the motor of the transport belt forward transport; paint bottles along with the transport belt forward transport when the paint bottles transported to the paint filling station, the filling station of paint bottles so that the photoelectric sensor to detect the signal of the input, the conveyor belt motor When the paint bottles are transported to the paint filling station, the photoelectric sensor at the filling station detects the input signal, the motor of the conveyor belt stops running, and the filling head limit sensor 1 turns on to start filling the paint bottles; when the filling of paint bottles is completed and the filling head limit sensor 2 turns on, the motor of the conveyor belt runs again to drive the conveyor belt forward to transport the filled paint bottles; when the photoelectric sensor at the capping station detects the filled paint bottles, the motor of the conveyor belt stops running, and the capping hand limit sensor 1 turns on to start capping the paint When the capping of the bottles is completed and the capping hand limit sensor 2 is turned on, the finished product will be counted as full bottles + 1, and the finished product will be transported with the conveyor belt to the next production link, and when the can discharging machine discharges the bottles again, the filling production line will complete the production link again and again. The paint tank for filling is 50L, when the paint in the tank is less than 5L, the refill valve solenoid valve will automatically open for paint replenishment; when the paint in the tank is greater than 45L, the refill valve solenoid valve will automatically close the valve to stop paint replenishment.
3.2 Paint tank level detection program design
Liquid level is analog, through the A/D conversion, 0 ~ 10V analog input is converted to 0 ~ 27684 digital quantity", collected to the PLC storage area. In the control program, the first analog input signal is read from the PIW256, and after the data type conversion of the integer of 16, the digital quantity collected by the PIW256 is converted to scale 0.0~50.0L actual engineering value.
4 Upper computer monitoring system design
Combined with the S7-PLCSIM debugging part, using WINCCV7.3 configuration software on the host computer interface configuration! to realize the function of automatic monitoring of the paint dye filling production line. The main functions of the monitoring interface include: filling system with two operation modes of manual and automatic control; counting statistics of finished products; analog detection of replenishment level; debugging of the return side of the configuration canning process; debugging of the configuration loading process screen; debugging of the configuration capping process screen; monitoring of the general screen of the configuration filling production line; and the operation status of the corresponding process on the host computer.
4.1 Establishing External Variables
In the Variable Manager, expand the newly created "s7", and create the following variables in the Name column and Address column, with the data type selected as a binary variable, the length as 1, and the address as a bit memory. In the analog monitor screen, the upper control button must be selected as the M intermediate bit memory.
4.2 Configuration screen
It is possible to realize the actions of paint bottle lowering, transportation, liquid level detection, canning and capping, etc., and has the function of working status indication. If you need to monitor the working process of each station in detail, you can switch to each sub-screen through the screen switch button.
5 Conclusion
The whole automatic filling machine adopts a distributed structure, field layer, PLC control layer and upper computer layer? The upper computer is developed under the WINCC environment, realizing the real-time control of the whole process engineering. S7-300PLC is used as the main controller, communicating with the upper computer through MPI, and the field layer completes the signal detection and control of the conveying line, canning and capping process! The application of this filling system can greatly reduce the labor intensity of workers, improve the working environment of workers and improve safety.