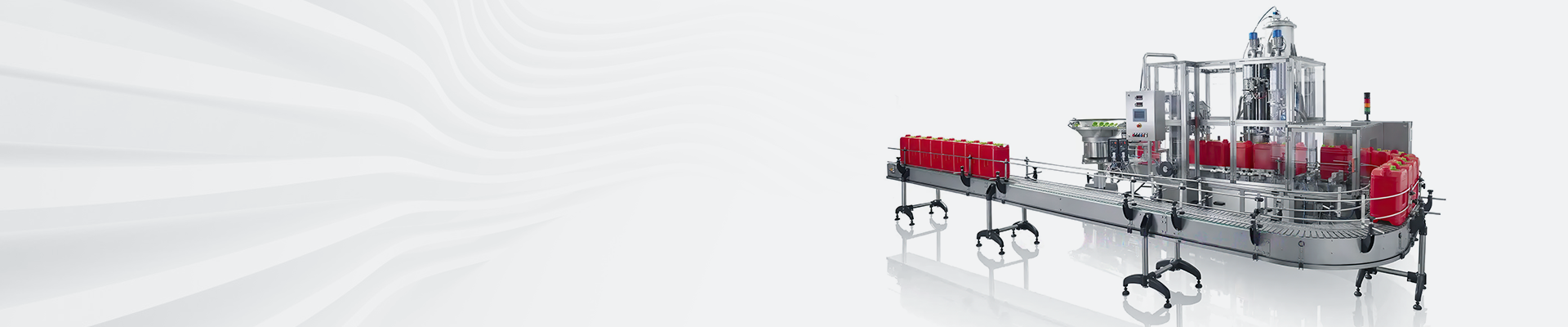
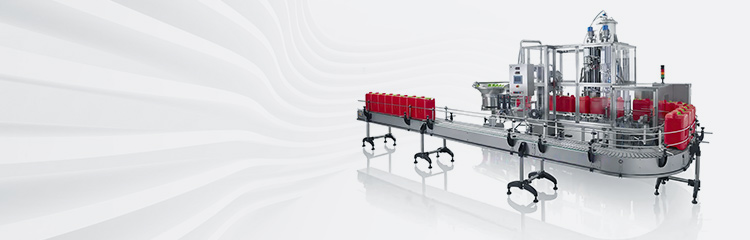

Summary:In the feed production process, the accuracy of feed ingredients directly affects product quality and has an impact on production costs and economic benefits.In the process of production and processing, it is necessary to control the accuracy of ingredients by improving the systematic understanding of formula design, raw material use, production sequencing, equipment maintenance, ingredient sequence, control accuracy and ingredient system application. Stable within standards to ensure product quality.
In the process of feed production, the accuracy of feed ingredients directly affects the quality of products, which has an impact on production costs and economic benefits. To control the dosage accuracy in the production and processing process, the dosage accuracy should be controlled and stabilized within the standard to ensure the product quality by improving the systematic grasp of the formula design, raw material use, production sequencing, equipment maintenance, dosage sequence, control accuracy and application of dosage system, and so on.
Batching system is the process of using specific batching equipment and production tools to accurately weigh and mix many different varieties of feed ingredients according to the requirements of the feed formula. The batching process generally includes the preparation of bulk raw materials and premix additives and other raw materials added in smaller quantities. In order to realize production automation, the pursuit of dosage accuracy, to avoid man-made dosage accidents, no longer use manual dosage of bulk raw materials, and small additives due to the variety of small additions, raw materials corrosive, mechanical dosage accuracy is low, the raw material is easy to caking, easy to stick warehouse, easy to chemical reaction, etc., generally use manual dosage or the use of carriers and other methods.
1 dosage accuracy
Dosing accuracy is to control the dosing error within a certain range. Dosing accuracy is divided into static accuracy and dynamic accuracy. Static accuracy refers to the error value between the actual dosage amount and the designed dosage amount in the static state (after the dosage is completed). Dynamic accuracy refers to the dynamic state (dosage process), the actual amount of dosage and the design of the error between the amount of dosage. The national standard is 0.1% FS for static and 0.3% FS for dynamic (FS=FullScale). Batch effect of batching error on cost, such as a pig concentrated feed formula consists of 18 raw materials, of which the content of soybean meal (CP43%) is 58.67%, in the production process, if its batching accuracy is 0.1%FS, then it will cause a certain amount of cost error, this hidden error will basically be due to the production habits with the increase in production in proportion to the expansion. In the actual production process, the dosage error is much greater than 0.1% FS, especially for artificial dosage, manual mechanical dosage or imperfect management of the processing unit, due to the dosage error can not be controlled within the standard range of implicit cost differences brought to the enterprise is incalculable. If the design content of crude protein of pig concentrated feed formula is 38.5%, and the dosing accuracy of all kinds of protein raw materials can reach 0.1%FS, then the difference of crude protein will be 38.5x0.001=0.0385, but this is an ideal state. In the actual production process, due to a variety of reasons for the dosage error, often resulting in irregular changes in the crude protein content of the product, causing hidden problems to product quality.
2 factors affecting the accuracy of the ingredients
2.1 Formulation design and use of raw materials
In the feed formula design, the need to add raw material varieties on the dosage scale 8 to 10, in addition to soybean meal, cotton meal, lees, other raw materials will be added due to the amount of too little to achieve the dosage accuracy. More than 10 varieties of raw materials need to be manually dosed and added, greatly affecting the production speed. If the proportion of calcium bicarbonate is 0.101%, if the production of 1000kg mixer, then the batch of 1.01kg, it requires the use of dosage scales must be less than 10g accuracy, and must be pre-mixed before entering the mixer. Such formulation design not only increases the chances of the dosing accuracy exceeding the allowable value, but also reduces the production efficiency. Therefore, in the formulation design, must be based on the production process and equipment to consider whether the addition of various raw materials to facilitate the actual operation of production, whether in line with the production methods of the plant.
2.2 Process and equipment selection
In modern scale feed mills, generally used in the central control and management of intelligent computerized automatic dosage system, feeding system to computer as the dosage host, and the operating table, analog screen, out of the warehouse machine, weighing module scales and so on into a complete set of complete dosage control system. In the feeding system, the main factors affecting the dosage accuracy are the stepping motor of the dosage winch, the accuracy of the dosage weighing, the accuracy of the weighing instrument, the resolution of the load cell, the speed of the program running, the speed of the signal feedback, the model of the out-of-bin machine, and the parameters of the frequency converter regulation, and so on. The selection of these devices and parameters determined by the product structure, formula composition and use of raw materials. Such as in the selection of warehouse machine (equipment), to fully consider the characteristics of raw materials (density, volume, liquidity performance, etc.) and additive factors; in setting the parameters of the batching machine, we should also take into account the characteristics of the raw materials and additive, in the dynamic adjustment process, to maintain the accuracy of the batching. Such as quality of soybean meal, cotton meal, salt, stone powder and other raw materials of different weights, its inverter and
2.3 Distribution of bins and dosage sequence
Feed processing enterprises will use multi-scale dosage system, by the influence of the feeding line, suitable for each dosage silo of raw materials are fixed, which requires the selection of raw materials and formula design should fully consider the production process to meet the requirements of multi-species raw material formulations, to avoid the rise of the scale, the dosage is too small, the dosage of too long a time, and so on, the phenomenon of the dosage of the accuracy of the impact. In the actual dosage process, in addition to using the first big and then small, first light and then heavy dosage order, but also according to the fluidity of raw materials and viscosity to flexibly adjust the dosage order.
2.4 Batching method and control accuracy
2.4.1 Manual batching
In the production scale of smaller feed mills (less than 500kg mixer) or raw material fluidity performance is very poor in the specialty feed mills, often using manual way to complete the batching operation. At this time, the experience and responsibility of the dosage personnel become an important factor in determining the accuracy of dosage. In order to pursue the speed of dosage, some feed manufacturers often use dosage containers to carry out empirical dosage, due to the differences between each batch of raw materials and the differences in the operation of each person, so the dosage error is uncontrollable.
2.4.2 Manual batching
Manual batching refers to the mode of manual operation of the batching machine (batching winch) to complete the batching operation, the operator's experience, sense of responsibility and the accuracy of the batching scale and the batching machine determines the batching accuracy. In this way, the dosage error is uncontrollable and the product quality fluctuation is not regular.
2.4.2 Manual batching
Manual batching refers to the mode of manually operating the batching machine (batching winch) to complete the batching operation. The experience and responsibility of the operator and the accuracy of the batching scale and batching machine determine the batching accuracy. In this way, the dosage error is uncontrollable and the product quality fluctuation is not regular.
2.4.3 Automatic batching
It refers to the mode in which the batching computer commands the batching machine to complete the batching operation. In this mode, automatic dosage is fully realized, human error rate is minimized, which puts forward high requirements on the computer system as the core hardware equipment to keep normal operation, scientific design and reasonable structure layout.
3 Conclusion
Effective control of dosage accuracy is a systematic project, from the formula design to the use of raw materials, from the process to determine the selection of equipment, from the dosage order to the control accuracy, which one of the missing links will result in the system dosage accuracy is not enough, therefore, for the production process and dosage equipment has been fixed for the enterprise, continue to strengthen the dosage management at the production site, targeted design of formulas and the use of raw materials, it may be Maximize the dosage accuracy.