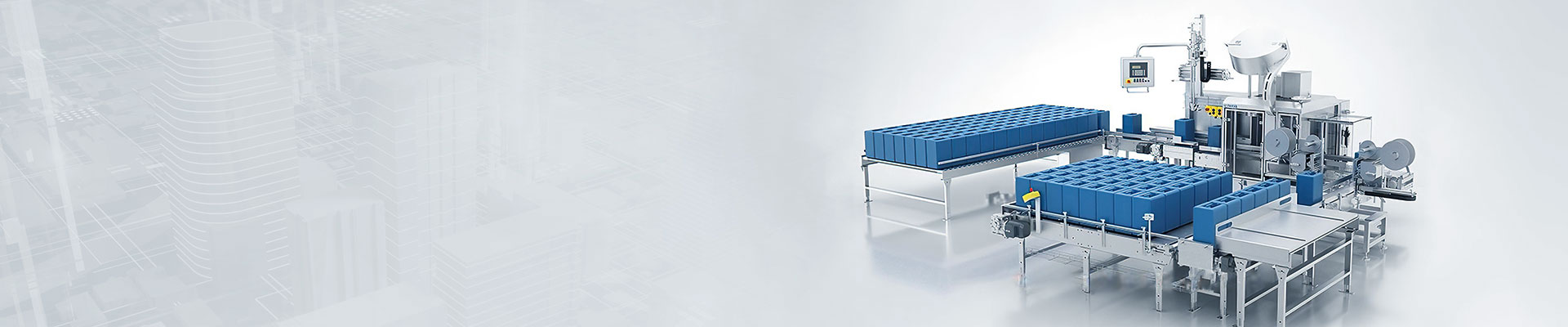
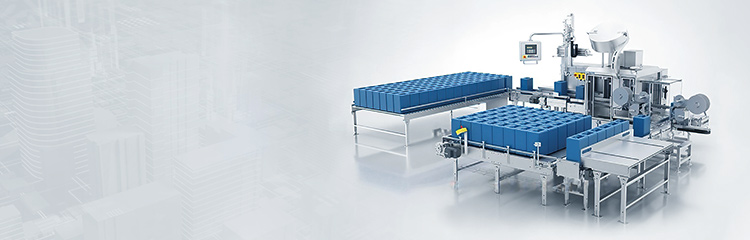
Liquid filling machine consists of stepping motor, gear pump filling head, conveyor belt and electrical control box, controlled by PLC programmable, the container is fed into the scale body at the same time when the motorized drum running, weighing module on the photoelectric switch detected by the container issued by the signal, the filling mechanism through the speed reducer to stay in the E stepping motor's output shaft is connected to the drive shaft of the ruler wheel pump, through the control of the stepping motor's running steps to achieve the Accurately control the number of revolutions of the gear pump to achieve the purpose of accurate measurement.

The Filling system can clean, transport and fill the empty bottles, and the filling quantity can be set according to the size of the empty bottles; transport and count the full bottles, and the counting value includes cumulative counting, unit package counting, and the unit package counting quantity can be set according to the size of the packages; and utilize the PLC's good automatic control performance. The good automatic control performance of PLC is utilized to realize the unmanned control of the canning production process.
According to the order of processing to create the required processing link, which has five parts: cleaning link, filling link, capping link, packaging link, testing link, and then design the manual control interface, due to the first container into the cleaning link. Filling, capping, packaging and testing all need to stop working, so the control interface should have a control switch for each link to ensure that no waste of raw materials and the smooth transfer of products.
The washing session utilizes flashing water droplets to show the washing process however, the real washing process is much more complex than what is shown. Filling is done by making sure that the last movement of the container is just at the filling port and that the filling process of the liquid inside the bottle is shown by the filling in the animation link. The capping process requires the capper to be lowered when the container stops at the capping port, thus simulating a process of capping. Packaging is relatively simple, and only requires an animated connection to make the implied logo appear in time at the last stopping position of the container. The inspection link is equipped with a robot that randomly grabs the container and is used to show the process of inspecting the product.
Technical characteristics
Applicable environment: ExdⅡBT4
Feeding pressure: 0.1~0.6Mpa
Weighing range:5~300kg/barrel
Weighing speed: 1~3 barrels/minute
Measuring accuracy: ±0.1%~0.2% (related to material and speed)
Air pressure: 0.5~0.6Mpa
Air volume: 0.2m3/min
Power supply: 220V/50Hz0.5kW
Countertop size: 800 x 800 (reference size);
Inlet: Diameter 40/50mm