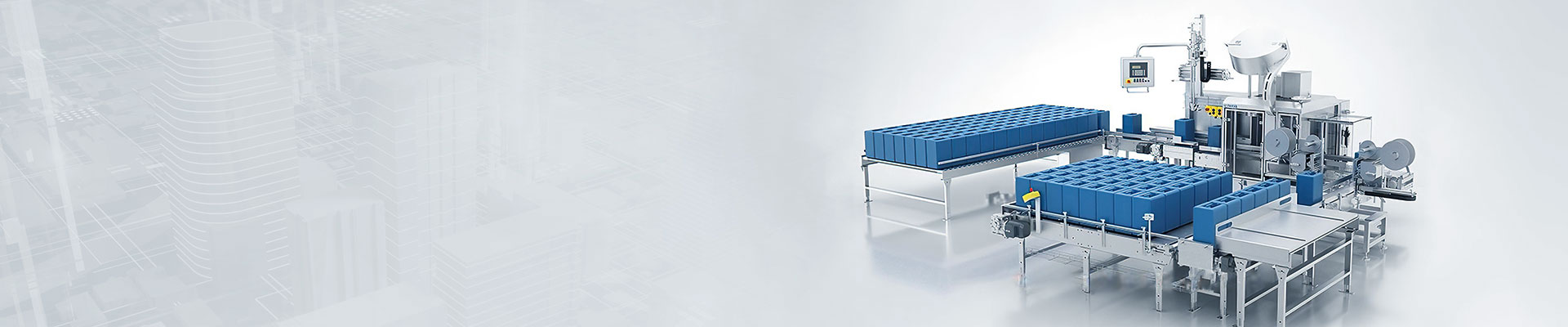
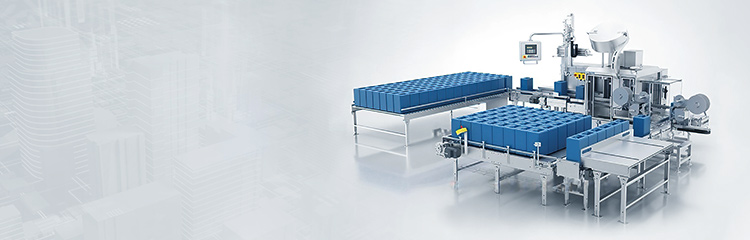
The weighing device of reaction kettle integrates advanced technologies in various fields such as mechanics, electronic technology and sensing technology. Metering quantitative feeding, reaction process control, discharging and other production process control and data management as one of the batching system. It consists of three parts: touch screen, operation cabinet and power distribution cabinet, and automatically and continuously controls the weighing, feeding, stirring and discharging of powder and liquid materials of the whole set of equipment according to the set formula.

Reaction kettle weighing is a device for real-time monitoring and recording the weight of materials in the reaction kettle. Its principle is based on the weighing sensor technology. By installing the weighing sensor in the support system of the reaction kettle, when the weight of the materials in the reaction kettle changes, the sensor will detect the stress and convert it into corresponding electrical signals. After amplification and processing, these electrical signals can accurately reflect the weight change of materials in the reaction kettle;
Reaction kettle weighing can monitor and record the weight change of materials in the reaction kettle in real time. By combining with the monitoring system, the weight change of materials in the reaction process can be monitored and recorded in real time, providing timely data support for the production process;
With the help of the weighing module, the operator can accurately control the feeding amount of materials and the collection amount of products in the reaction kettle, thus realizing the accurate control of the reaction process. This is helpful to improve the stability of the reaction and the purity of the product, and ensure the quality and efficiency of the production process.
The weighing module of the reaction kettle can also be used to monitor the weight change of materials in the reaction kettle, find abnormal situations in time and take corresponding measures to ensure the safety and stability of the production process;
The reactor has a complete production report system, including batch report, shift report, daily report and monthly report, and can also print each batch of production records in real time. Provide detailed data for factory analysis;
It can realize the setting of raw material transfer, and ensure the normal production when there is no material in the silo;
Convenient function of modifying batching parameters and control parameters;
The self-detection function of the system automatically confirms whether all components are normal, ensuring the normal operation of production;
Power failure self-protection function, which can restore the state before power failure after unexpected sudden power failure. UPS; needs to be configured;
The reaction kettle has alarm function, displaying alarm information and prompt information, and taking corresponding measures; l
Double-mixed system can realize independent control, and its production is not affected when one of them fails, so it has higher reliability;
Real-time display of various data in batching production, real-time display of batching process simulation diagram, intuitive image.