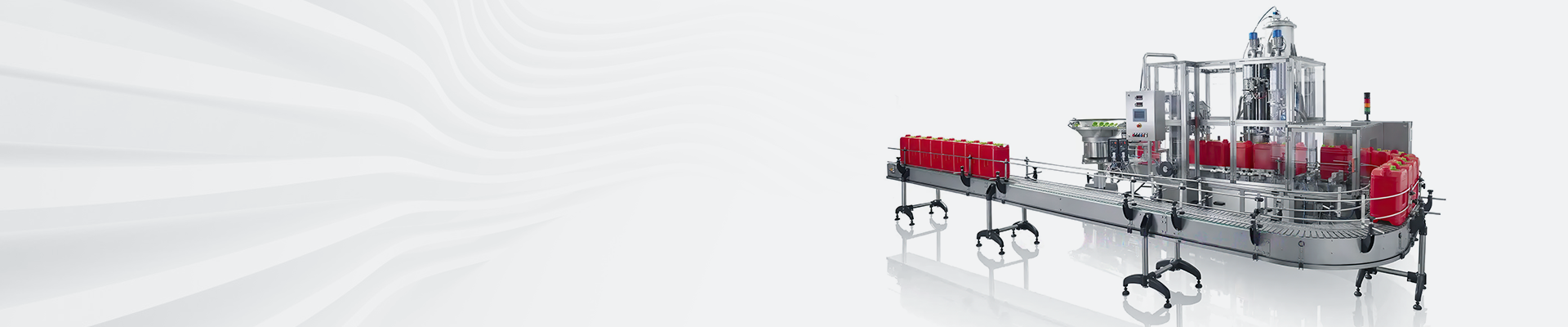
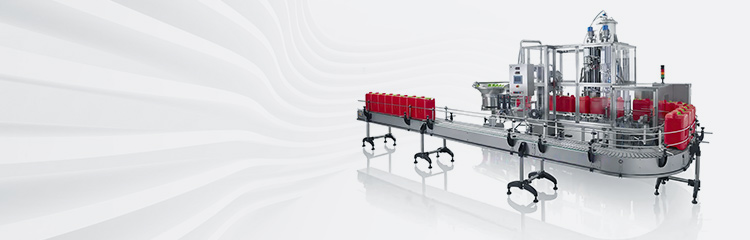

Summary:The flavor and spice dosage system proposes an automatic control system based on Profibus fieldbus, and on this basis, a process monitoring system based on IFIX configuration platform is developed. The monitoring system has comprehensive functions, friendly interface, easy operation and stable operation, which creates great economic and social benefits for the enterprise.
0Introduction
In order to improve the core competitiveness of Chinese cigarettes, the State Tobacco Monopoly Administration (STAA) has listed the cigarette flavoring project as a major strategic topic for focused research. Cigarette flavoring technology is the core technology to build Chinese-style cigarettes and the key technology to form the characteristics of cigarette products, so the sugar and spice mixing center is becoming more and more an indispensable and important equipment in the silk production line. In this paper, we will develop an IFIX-based flavor and spice modulation process monitoring system, in order to realize the fully automatic proportioning function of raw materials.
1 Flavor and fragrance modulation process flow
In the distiller at the same time into the water and water vapor, so that the raw materials and water full contact, the raw materials in the aroma components volatile. By controlling the weight and temperature of the water vapor, the aroma components in the raw materials are gradually volatilized and mixed and dissolved with the water vapor. Through the pre-set formula and procedure, the different natural flavors are dosed according to a certain proportion and order, and mixed and stirred to finally get the spice mixture that meets the requirements.
1.1 Raw material into tank
The automatic control system automatically searches the formula parameters of the corresponding grades in the raw material preformulation database according to the mixing work order issued by the production management or manually recorded, calculates the weight of the material to be formulated, then breaks down the names and weights of all the raw materials involved in the formulation according to the formula, and reminds the operators to replenish the missing raw materials, and at the same time, displays the amount of raw materials to be added on the monitoring screen. After manually sending the missing raw materials from the raw material storage area to the material liquid modulation area, and sending the raw materials to the corresponding raw material storage tanks through the hydraulic lifting platform or air pump, the automatic control system will automatically review the weight of the supplemented raw materials.
1.2 Raw material boiling
In order to increase the fluidity of raw materials in the pipeline, reduce losses in the delivery process, in the boiling tank of the higher viscosity of honey and moisturizing agents and other raw materials for pre-treatment. After the operator selects the name and weight of the raw materials to be boiled and the corresponding boiling tank, the automatic control system automatically calculates the required amount of raw materials and the amount of water by searching for the corresponding grades in the raw material pre-processing database, and prompts the operator to add the raw materials to be pre-processed into the selected simmering tank; and then automatically add the appropriate amount of water (the amount of water added by the simmering tank's own weighing module to measure), add water to finish After the water is added, the heating, stirring and heat preservation process is automatically executed according to the stirring time and temperature in the parameters of the recipe library (or input by the operator) to complete the boiling of raw materials. Boiled raw materials in the boiling tank temporary storage, as raw materials to be used.
1.3 Liquid preparation
When preparing liquid material, the batching machine first controls the valve positioner to make the pneumatic ball valve open completely, so that the raw material flows into the measuring tank quickly, when the amount of raw material is close to the set value, then control the valve positioner to adjust the opening degree of the pneumatic ball valve, so that the raw material flows slowly into the measuring tank until the amount of raw material reaches the set value (>2kg) before closing the pneumatic ball valve completely, so that it can satisfy the requirements of the liquid material preparation speed and accuracy at the same time. Raw material preparation order for the first wetting agent, then other raw materials, and finally dosing water (water is also measured by the metering tank), so as to reduce raw material losses; to be involved in the automatic proportioning of all raw materials after the end of the preparation, the automatic control system automatically on the dosage of the pipeline for blowing and cleaning (hot water cleaning); and then according to the monitoring machine or set up in the vicinity of the modulation tank on the touch-screen pop-up to be manually added to the raw material name and weight (≤ 2kg) information, manual addition of raw materials and weight (≤ 2kg) information, manually. Then according to the name and weight (≤2kg) of the raw material to be added manually popped up on the monitor or the touch screen set near the modulating tank, the corresponding amount of raw material is weighed manually and poured into the selected modulating tank.
1.4 Finished material filling
After the finished material liquid modulation is completed, it can be temporarily stored in the modulation tank, or automatically measured and loaded into barrels and then sent to the finished spice storage room for temporary storage.2 Flavor and Fragrance Modulation Process Monitoring System Structure and Function Realization
According to the function, the monitoring system of flavor and spice making process can be divided into equipment control layer, centralized monitoring layer and production management layer.
2.1 Production management layer
The production management layer is responsible for receiving the production plan from the superior management system and further decomposing it into the production tasks of the sugar and spice modulation center system; during the production process, it handles the comprehensive information during the operation of the flavor and spice modulation process monitoring system and provides the superior management system with complete statistical data reports on the implementation of the production tasks and the quality data, etc. The production management layer is equipped with a small data server and a centralized monitoring layer. The production management system is equipped with a small data server, a factory-level management network switch, and a network printer. The small data server is equipped with two Ethernet cards: one is used to connect to the sugar spice modulation center switch to realize the communication between the production management layer and the centralized monitoring layer; the other is used to connect to the factory management network switch to realize the exchange of data and information with the relevant departments in the factory management network.
The server is installed with system software Windows2003Sever, database management software Oracle, office software Office2003, and after receiving the production plan provided by MES, the server will decompose it into the production tasks within the system of sugar and spice mixing center, and process and save all kinds of data in the process of production to form all kinds of reports required for sugar and spice mixing center monitoring computer to carry out monitoring and control. The monitoring computer of the sugar and spice making center carries out centralized monitoring and information query. Considering the importance of confidentiality of information in the sugar and spice center and the possibility of virus transmission through the management network, the server is equipped with firewalls and other network security devices to prevent illegal access and virus invasion.
2.2 Centralized monitoring layer
Centralized monitoring layer is the hub of production management and equipment control layer, with complete equipment monitoring functions, setting, displaying and modifying operation parameters and equipment parameters, fault diagnosis and analysis functions; it can receive production instructions and plans from production management system and decompose and execute them, and then give feedback on the completion of the lower level; it can realize the traceability control of the quality of the product batches.
Centralized monitoring layer is based on advanced computer network technology and computer graphics technology, PC and workstation as the standard human-computer interface system, providing “humanized” human-computer interaction interface and operation assistance system. Through the monitoring computer can realize the production of various operations, state monitoring, process parameters, control parameters of the display and setting, control system failure diagnosis and positioning, dosage control system, equipment failure alarm display and record.
During production, flavor and spice are separated, so two monitoring machines are set up. One of them is mainly used to operate and monitor the modulation and filling of spices; the other one is mainly used to operate and monitor the modulation and filling of flavors. The two monitors are hot standby for each other, so that if one of them fails, the other one can continue to work instead of the other. The monitoring machine communicates with PLC via Ethernet via Ethernet card and switch to realize convenient and fast data exchange.
2.3 Equipment control layer
The control layer of the batching equipment adopts Siemens Profi-Net bus control based on industrial Ethernet to realize the production operation control of the equipment and the collection of production site and equipment-related information.
The main PLC adopts CPU416-3PN/DP, which is a powerful CPU with high arithmetic degree and working memory to meet various requirements in high performance range.
ET200S modules are complete, economical in point count, flexible and complex in architecture, which is conducive to the modularization of the system design; they are distributed in the sub-station box next to the field equipment, which significantly saves the wiring cost; and the choice of active backplane bus can support hot-swapping of templates without causing CPU downtime. All detection signals and actuators are directly connected to the ET200S module. Feeders refer to devices that can be directly connected to the fieldbus. Electronic scales, valve islands, flow meters, RFID systems all use Profibus-DP interfaces, and Profibus-DP can be transparently connected to ProfiNet through IE/PBLink; pressure and temperature smart meters all use Profibus-PA interfaces, and are converted to Profibus-DP interfaces through DP/PALink before they are connected to ProfiNet through IE/PBLink. Each IE/PBLink can connect up to 64 Profibus-DP devices and each DP/PACopule can connect up to 32 PA instruments.
3IFIX and PLC communication
The configuration software of the centralized monitoring layer adopts the IFIX software of Intellution, which is a Windows-based HMI/SCADA component, specializing in providing a design environment for easy integration and cooperative work between factory-level and commercial systems [2].IFIX obtains and utilizes field data through the OPC method and communicates directly with existing I/O devices through the I/O drivers. /O devices through I/O drivers. The Sugar Spice Modulation Center system uses SI7 drives, which comply with the OPC standard, so any OPC client can access the hardware data through the SI7 drives. i.e., IFIX communicates with the PLC by using the OPC server to collect the data information from the PLC, and then transmits the data to IFIX through the SI7 drives. the whole communication process is as follows: firstly, establish the OPC server The whole communication process is as follows: firstly, the connection and data exchange between OPC server and PLC are established; then the IFIX configuration software as an OPC client communicates with the OPC server through the SI7 drive.
3.1 Communication between OPC server and PLC
The OPC server is established through SimaticNet, and the OPC server collects PLC data so as to provide a field data source for the OPC client.The OPC server and PLC communication settings are as follows:
(1) Hardware configuration of PCStation. Open the StationConfigurationEditor configuration window, add OPCServer in slot #1 of the rack, add IEGeneral in slot #3, and set the parameters of the network card in the pop-up property dialog box.
(2) Assign the name of PCStation. Click the “StationName” button to configure the PCStation name, which should be the same as the PCStation name inserted by Step7 hardware configuration.
(3)Configure PCStation via SimaticNet, create a new project in SimaticNet and insert a PCStation, the name of PCStation must be the same as the name of StationConfigurationEditor.
(4) Hardware configuration of PCStation. Double click Configuration to enter the hardware configuration interface, refer to the hardware configuration of PCStation and select the corresponding hardware from the hardware catalog window.
(5) Save compilation. After completing PCStation hardware configuration, click “Save Compilation” to store the current hardware configuration. (6) Establish the connection between PCStation and PLCS7. Click “ConfigureNetwork” button to enter NetPro configuration window, select IEGeneral and insert a new S7 connection in the connection table.
(7) Download to PCStation, after confirming all the configurations, click “Save Compile”, then a compilation result message will pop up, indicating whether the configuration is correct or not. If the configuration is correct, then the configuration is complete, click the “Download” button to download the configuration information to PCStation, otherwise the configuration information can not be downloaded to PCStation. after the download is complete, you can open the StationConfigurationEditor window to check whether the configuration is normal.
3.2 Data Communication Test
Through OPCScout, you can test whether the data communication is normal. If the “Quali-ty” status bar shows “good”, the data connection between OPCServer and PLCS7 has been successfully established.
3.3 Communication between IFIX and OPCServer
IFIX communicates with OPCServer via SI7. The data from OPCServer reaches IFIX DIT (drive image table) via SI7 driver, and then reaches IFIX PDB (process database) via IFIX SAC (process alarm and monitoring).The communication principle between IFIX and OPCServer is shown in Figure 6.The communication settings between IFIX and OPCServer are as follows:
(1) Open PowerTool to connect to the local server and establish a new channel, CommunicationsProcessor select TCP/IP, VirtualFielddevices select OPCServer.
(2) Add a new device, corresponding to the PLC connected at the bottom, Connec-tion select S7connection_1 previously established in OPCServer.
(3) Add a new data block. Each device can add more than one data block, fill in the start and end address of each data block should correspond to the address provided by the PLC.The setting of DataType should also be consistent with the data type given by the PLC. Each data block can read multiple bytes of data, up to a maximum of 238, which can be used separately by data type in IFIX.
(4) After the configuration is completed, you can check whether the data connection is normal or not through DataMonitor.
(5) After testing that the data connection is normal, add the I/O variables that the system needs to monitor in the IFIX real-time database, which can also be imported directly by PowerTool. The variables in these databases can be directly referenced in the IFIX screen.
4 Conclusion
IFIX can quickly construct and generate interfaces for database management, alarm processing, process control, animation display, report output, etc. It provides a safe, reliable and powerful guarantee for the integration and rapid development of industrial automation systems.