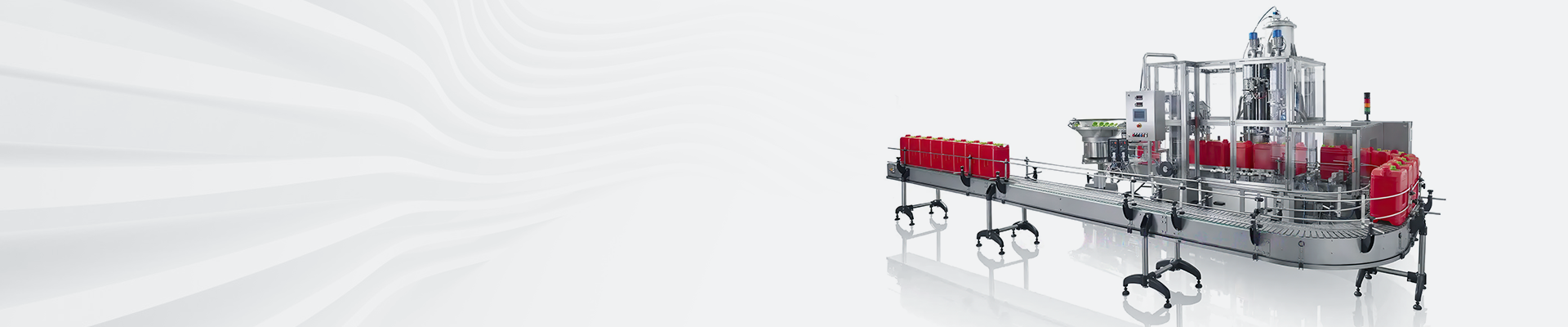
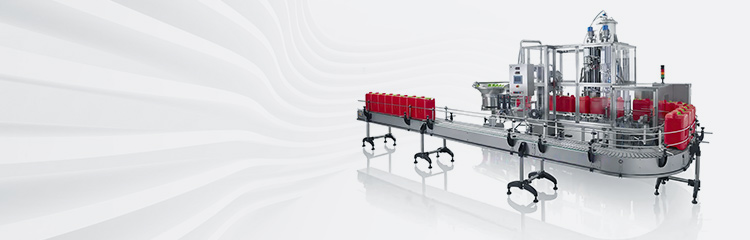

Summary:The dosing system can automatically control the corresponding conveyor to input materials into the measuring hopper according to the set formula, so as to complete the automatic dosing. According to the formula, weight and control parameters, it drives the start, stop, fast and slow and point operation of the feeding stirrer of each bin, and drives the opening and closing of the weighing door under the specified conditions, in order to complete the whole weighing process, and if there is a scraper under the weighing scale, it also completes the starting and stopping control of this scraper.
Batching is one of the key processes in feed production, and the requirements of each feed mill for the batching process are different, and some of them are very different. Therefore, the design of a modular structure of the dosage system, so that it can be flexibly combined to be able to easily meet the different process requirements of different feed mills is very necessary. To this end, first of all, the entire automatic dosage system is broken down into if thousands of different functions of the module (such as weighing although the module, mixing module, etc.), each module is composed of high-performance micro-controller chip and its peripheral circuitry, and will be encapsulated in their respective control box, and this control box can be conveniently mounted in the electrical cabinet in the rail, each of which can independently complete the control function of each control box module.
The information exchange between the control modules is realized through the CAN bus, which is a highly reliable industrial control bus, and it can connect the control modules with different functions required by the dosage process to the CAN bus, so as to realize the transmission of control information and status information between the functional modules through the CAN bus, so the CAN bus structure is a good choice. In addition to the various control modules that can accomplish specific dosage sub-functions, the feeding system also selects an ordinary office computer as the human-machine interface, which is also used for data processing.
The main functions of the computer as the human-machine interface can be summarized as follows: the dosage status information uploaded by the modules via CAN bus is displayed on the computer screen through animation in an intuitive and dynamic way, so as to achieve the effect of enabling the operator to have a clear understanding of the dosage process at a glance; @ manual intervention of the dosage process (e.g., startup, pause, change of bins, etc.) can be realized by clicking on buttons and menus on the graphical interface with the mouse, i.e., the corresponding control command is transmitted via the CAN bus to the control system; @ the control command is transmitted via the CAN bus to the control system. (Control commands are transmitted to relevant control modules via CAN bus.) Uploaded dosage data is summarized into various reports for storage, display and printing. “Receives formulas from the management department via the network, and transmits various dosage production data to the management department at the same time.
1 Main control module
This is the only mandatory module among all the control modules, and its main functions are: ① coordinating the actions of all other control modules; ② receiving the status information from all other control modules through CAN bus and uploading it to the computer through its 232 serial port; ③ receiving the manual control commands from the serial port of the computer and transmitting them to the relevant modules connected to the bus through CAN bus; ④ the control functions of mixer and hand-feeding are relative to each other; ④ the control functions of mixer and hand-feeding are relative to the control functions of the other control modules. The control function of mixer and hand feeding is relatively simple and necessary for the conventional feeding system, so it is also integrated in this module.
2 Weighing module
This is the most important function module in the system, responsible for all the weighing control of a scale. If more than one scale is installed in the system, the same number of weighing modules can be equipped. The main functions of this module are: ① Receive the formula content and weighing control parameters from computer; ② Receive and execute the start, pause, bin change and other dosing commands from computer; ③ Receive the weight data from weighing instrument; ④ According to the formula, weight and control parameters, drive the feeding stirrer of each bin to start, stop, fast, slow, and pointing operation, and drive the scale door to open and close in the stipulated conditions, in order to complete the weighing process, if there is a scale, the weighing module can be equipped with the same number of weighing modules. If there is a scraper under the scale, it will also complete the start-stop control of the scraper; ⑤ Upload the actual weighing results and alarm information.
3 Liquid weighing module
The function of this module is basically the same as that of the weighing module for solid raw materials mentioned above, only the control method is different.
4Liquid addition module
This module is used when the batching process uses flow meters for liquid measurement and control of the liquid addition process. Its function is as follows: ① Receive the formula of the liquid part and the control parameter of liquid addition from CAN bus, and upload the liquid addition status data; ② Start the liquid addition process when receiving the liquid addition command, and count the liquid addition pulses of the flowmeter, and end the liquid addition when the count value is in line with the number of pulses converted from the weight set in the formula; ③ Detect the no-liquid and leakage faults, and upload the alarm information when the faults occur. Alarm information is uploaded when a fault occurs.
5-hand dosing terminal module
The main component of this dosing module is a 5-inch LCD that can receive and display Chinese information. Its function is to receive hand dosing information from the CAN bus and display it on the LCD screen for the hand dosing operator to view. The contents of the display are as follows: ① the current recipe name and the total number of batches; ② the current feeding for the first few batches; ③ the subsequent recipe name and the total number of batches of the recipe.
6 Packing Scale Terminal Module
This module is used in the batching system of premix production, and its main component is also a 5-inch LCD display that can receive and display Chinese information. Its function is to receive the information required by the packing scale from the CAN bus and display it on the LCD screen for the packing operator to see, the display contents are as follows: ① the current recipe name and the total number of batches; ② the material being mixed is the first batch and its batch number; ③ the material to be packed in the buffer bin is the first batch and its batch number (each batch of material can have a specially specified batch number, which is used to identify the batch of material, for future inspection. The lot number can be composed of 11 digits or letters).
7 hand-added material verification module
Confirmation and verification of hand-fed ingredients in the dosing process is an important means of ensuring feed quality. When weighing the medicine (i.e. when weighing the raw materials of hand-added ingredients), the code name of the medicine, the weighed weight, the formula to which it belongs, the date of weighing and the code name of its operator, etc. can be written into the non-contact IC card attached to its packaging bag for verification when feeding. Therefore, the function of this module is: ① Receive the formula from the CAN bus from the hand-feeding part, and displayed on the LED screen; ② each bag of medicine in the input before reading the medicine bag on the IC card in the drug information (as long as the bag loaded with the IC card to the part of the card reader close to the card can be); ③ IC card reader information and the current hand-feeding formula for verification and validation, i.e., whether the drug is the formula for The IC card reader information and the current hand-feeding formula for verification and validation, that is, whether the drug is the ingredients in the formula, whether the weight is within the specified error, etc., if the formula does not match, the alarm, the alarm information is transmitted to the computer in the central control room, by the central controller to deal with; ④ will have been cast in the material in the feeding place on the screen and the computer screen in the central control room to play on the material has been cast on the mark (usually the material in the line of the line color change); ⑤ if necessary, but also attached to the electronic scale for the weight calibration.
8 Drug weighing module
Weighing module with an electronic scale, a touch screen and a card writer, its function is: ① CAN bus to receive from the central control room weighing tasks; ② weighing of drugs in accordance with the recipe passed to the task, step by step weighing of drugs, when the weight of the drug weighed in line with the formula in the specified weight, it will be written to the relevant information set aside in the card writer in advance in the IC card, and beeping to signal the weighing of the drug to notify him of the IC card that has been written to the information, notify him of the drug, and the drug, and the drug, and the drug, and the drug, and the drug, and the drug. He will have been written to the information of the IC card removed, into the bag of the prescribed part. If there are more than one medicine weigher weighing medicine at the same time, it is necessary to equip the same number of medicine weighing modules and their attached equipment.
9 Other Function Modules
Other functional modules can be designed and produced according to the needs. As seen above, the modular structure of the dosage system, for a specific dosage process, as long as the choice of the required control module box assembly, and the computer monitoring software for the corresponding combination, you can easily complete a dosage system in line with the process requirements of the formation of the dosage system. Due to the flexibility of the combination, it is not difficult to combine the control of the former and latter processes of dosage. The dosage system of this structure also has the following features. ① The modular control box can be installed close to the corresponding equipment, and the connection to the system is made with only a pair of twisted pairs of wires (i.e. CAN bus). The connection to the system is made by a pair of twisted pairs of wires (i.e. CAN bus). ② Because the dosage process is completed independently in each control module, the computer only serves as a human-machine interface, so once the computer fails, the entire dosage process is still in progress, only the lack of effective human monitoring. However, the experienced center controller can still understand the current dosage status according to the indicator lights on each control box and the readings of the weighing instrument. If the computer failure is eliminated in time, restart the computer monitoring program, you can continue to monitor the ongoing dosage process. Normally, in order to keep the dosage process under effective human monitoring and safety, the main module will be shut down once the.