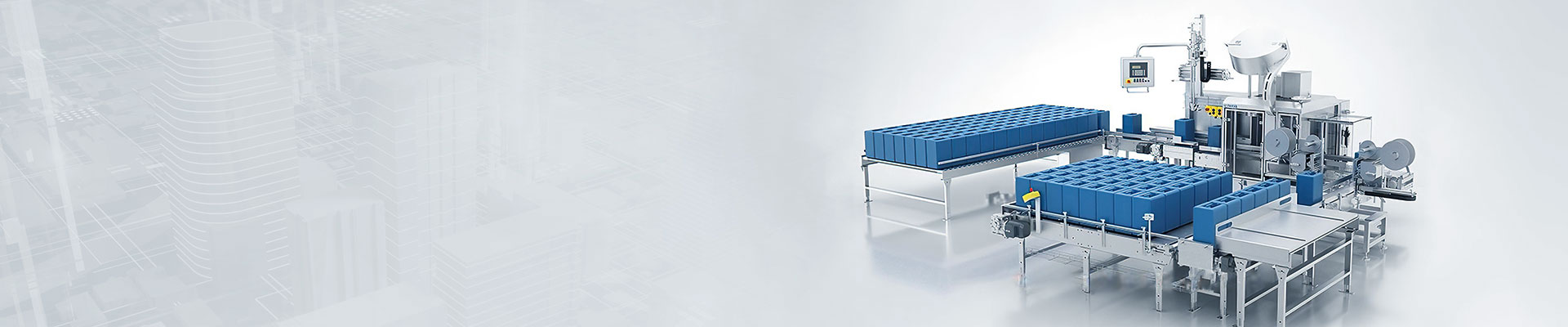
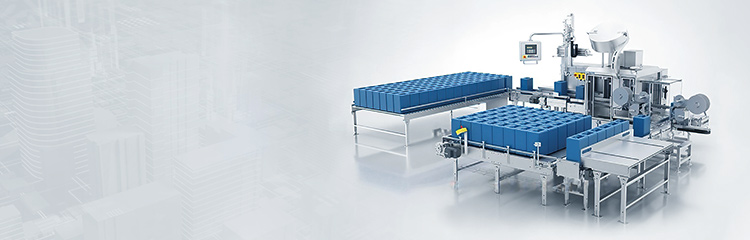
The automatic dosage system has a mechanism of mutual monitoring between the computer and the weighing instrument and various alarm mechanisms, with animation and PID control functions. The dosage can be operated by clicking on the mouse. The dosage ratio can be changed at any time. When changing the ratio of one material, the other ratios will be automatically adjusted according to their original ratios, which ensures that the total dosage ratio is 100%, thus guaranteeing the quality and yield of the products.

The automatic Batching system program takes the reactor as the control unit, and sets up the formula setting sector accordingly for different formula feeding and conveying in each reactor, which can flexibly cope with the demand of different formulas for different production batches of tasks.
The formula, feeding and discharging of the weighing and batching machine are all controlled by computer. In addition to the hopper, there are dynamic Weighing modules, precision amplifiers, analog/digital converters, micro-computers, monitors, printers and execution systems. The touch screen control system can control several reaction tanks and agitators, and can control the time of dry mixing and wet mixing, and can formulate several to dozens of materials, and can simultaneously display the batching process and print the name of each material, quality, total mass, cycle time, formula, daily report, monthly report and so on. Computerized automatic batching production line has large storage capacity of formula, many varieties of batching, high speed, high accuracy, abundant software available, convenient program modification, and is a product with high degree of automation. Through weighing instrument or touch screen, the required weight of various materials is set, which is automatically conveyed to the batching system by the winch in order for automatic weighing and flow control, so as to realize accurate measurement and batching.
The reaction kettle process step decomposition control flow is as follows:
1. Conveying of dosage
Before conveying the raw material flavor, internal logic judgment is carried out to determine whether the conveying of raw materials can be carried out, and the desire to convey should meet all the following requirements: the liquid level of raw material reaction kettle A/B/C must be greater than the value of the low liquid level, and the temperature must be higher than 120 ℃; the pumps of conveying the weighing and dosing system, P103A and P103B, are in operation or not (the two units must be kept in a state of stop at the same time); metering kettle A/B has at least one The weight of weighing unit is 0kg.
2. Selection of raw material reactor
Reactor selection, in the reactor to meet the conditions of raw material delivery, select the highest liquid level of a raw material reactor. After the raw material reactor selection is completed, the dosage selects the pneumatic valve of the corresponding pipeline, and the raw material pump delivers the weight of the quantitative range to the specified reactor.
3.Metering reactor selection
Metering reactor selection, under the condition of meeting the production requirements, select the weighing unit weight 0kg metering reactor, if both metering reactors are 0kg, the default selection of metering A reactor.
4. Trigger pneumatic valve start
In the PLC program internal selection of all the control kettle, pneumatic valve in the normally open state, pneumatic pump to the kettle delivery of liquid, through the measurement of kettle after the measurement kettle automatically read the weight of the quantitative range, reach the set specified weight of the pneumatic ball valve is automatically closed.
5. Raw material transfer pump start
After the dosage pneumatic valves are triggered to open one by one, the last pneumatic valve is opened in place of the rising edge signal, triggering the timer to start, timing 3S (can be set), start the raw material delivery system pump.
6. Raw material conveying dosage pump stop
In the process of conveying, metering reactor weighing module for weight measurement, when the weight measurement value reaches the weight of raw materials in the formula, stop the pump of raw material conveying system.
7. Close the dosage pneumatic valve
After the raw material conveying dosage pump stops, take the falling edge signal of the stop signal, trigger the timer to start, after timing 3S (can be set), according to the dosage pneumatic valve open in reverse order to close in turn.
8. Transportation of raw material reactor
Before conveying raw materials, internal logic judgment, whether the raw materials can be conveyed, want to convey should meet all the following requirements: raw material reactor level must be greater than the low level value, the temperature must be higher than 100 ℃; conveying the dosage of the pump P104 is running (must be kept in a state of stop).
9. Raw material reactor and reactor weighing selection
Formula into the system, that is, the selected formula number, metering kettle selection according to the raw material delivery when the selection of material number to start.
10. Individually add the formula interface
In the target mixing kettle selected formula, the dosing tank next to display the formula number; the other side of the display of all the formula name, in the process of Dosage system feeding, the corresponding powder flashing, each kind of material dosage system is put into the end of the system, it turns green, all put into the end of the process, it shows that feeding is complete. When this kettle selects the formula again, the dosage system resets and the data is overwritten. During the process of dosage system, this interface allows the operator to see at any time which step is being carried out by each reactor, in order to make the right emergency measures in case of emergency.
11. Rearrangement of Mixing Plant Conveyor to Target Mixing Tank Lines
May be in the busy time, the dosage control system will be a certain time to receive several commands, at this time should be considered in the master station to do an interrupt, as well as the priority of the insertion of the command, which needs to be communicated with the weighing and dosage system to negotiate the integration.
12. Metering kettle to the production line, without any metering and level monitoring in the metering tank, keep the manual feeding.