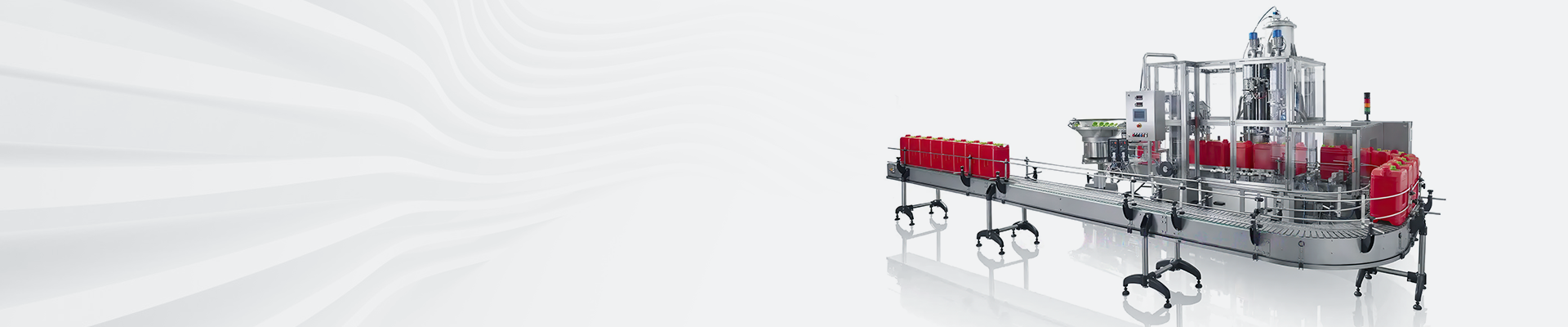
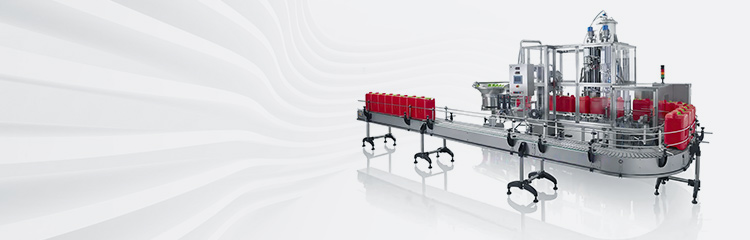

Summary:In ferroalloy production, various raw materials need to be uniformly mixed in a certain proportion.At present, factories usually use two methods of manual loading and automatic loading for material loading. Manual loading means manually placing the weighed materials on the conveyor trolley or belt for loading, and then enters the mine after passing through the furnace top transition silo. Hot furnace; while automatic feeding adopts automatic weighing and feeding method, and will not be subject to manual intervention.Since the raw materials contain a lot of dust, it is easy to inhale the dust during manual weighing and loading, leading to the occurrence of occupational diseases.This feeding method will increase the production risk and labor cost of the enterprise to a certain extent. Due to the large number of batches of ingredients, various errors are prone to occur during manual operation, which ultimately affects product quality and also significantly increases the cost of the enterprise. management costs
In the process of smelting ferroalloys, in order to ensure the high quality of the products and promote the normal production of ferroalloys, one of the key technologies is the batching and feeding system. With the development of China's computer technology and science and technology in recent years, the dosing and feeding system in the production process of the mineral heat furnace has gradually developed in the direction of informationization, automation, mechanization and refinement. Generally speaking, an excellent feeding system should take into account the reliability and energy saving and environmental protection characteristics in the actual operation process, and at the same time, improve the production efficiency of the enterprise on the basis of ensuring the quality of products. In addition, the application of dosing control system in ferroalloy smelting can provide technical and management personnel with specific key information in the production process, so as to optimize the scientific and reasonable production of the enterprise.
1 Dosing feeding automatic control system composition
Usually, the dosing and feeding control system of the mineral heat furnace includes three parts, namely, dosing, feeding and fabric. In the control system is mainly through the establishment of human-computer interface mode, in which the programmable controller PLC for the host: slave for the host computer touch screen.
1.1 Dosing
For the mineral heat system, the components of the dosing system mainly includes weighing scales, PLC, small belt, vibrator, touch screen and electromagnetic vibration feeder. According to various enterprises in the actual production process can make the dosage system in the touch screen on a variety of different materials at noon proportioning situation for calibration, in this process, the PLC system in the process of operation can read the weight of the material information, but also according to the program to start the electromagnetic vibration feeder on the material to discharge and weighing and a series of operations. And in the dosage system start, electromagnetic vibrating feeder will appear a large amount of vibration, vibration can facilitate its better and faster discharge operation. And when the material and the calibration value is getting closer and closer, it will be able to reduce the vibration amplitude of electromagnetic vibrating feeder in the actual operation to a certain extent, and then can effectively realize the fine discharging operation; and when the material in the programmers to reach the weight value set before, the discharging process will stop. In addition, in the process of operation of the automatic control system for feeding in mineral heat furnace, whether it is to implement fast or fine discharging can be infinitely adjustable amplitude of vibration, and at the same time, in the process of weighing the material, the touch screen can display the actual weight of the material in real time, and the accuracy of weighing the material can be controlled in the range of +0.5kg.
1.2 Feeding
The lifting bucket is towed by the winch and loaded along the inclined bridge, and the winch motor mainly adopts the frequency conversion multi-stage speed control mode in the application of automatic control system of dosage loading. The feeding system in the actual operation of the process, in the highest end of the low-speed operation, while the lowest end of the operating speed is still low-speed, in the middle of the implementation of high-speed mode of operation, this mode of operation is not only able to reduce to a certain extent, the motor in the process of starting and stopping the strong impact, while for the delivery of materials to be able to realize the high-speed operation. Frequency converter optional braking resistor can to a certain extent to avoid due to the lifting bucket fast downward process of the motor generates power generation process and over-voltage protection and other undesirable conditions; and due to the winch drum installed pulse encoder in the actual operation of the main mode of operation is the use of photoelectric encoder on the feeding trolley's specific position and the actual speed of the real-time monitoring. In the actual application of the photoelectric encoder, each circle includes 1024 pulses, which indicates that in the process of monitoring the position and speed of the loading trolley can be realized with millimeter-level accuracy, and thus will be able to ensure the safety and reliability of the operation of the trolley to a large extent. In addition, in order to realize the accuracy of positioning in the process of operation, it is necessary to adopt the independent locking winch in the loading system, and the inclined bridge is equipped with two kinds of switch forms of limit and limit position, so as to ensure the accuracy and reliability of loading.
1.3 Fabrication
In the automatic control system of dosing and feeding, the fabric trolley mainly runs on the preset track, the specific way is to feed the material transported by the lifting bucket in the required hopper, and then the hopper will automatically add the material to the mineral heat furnace to implement the smelting operation. Usually, in the fabric trolley track will be simultaneously arranged three-phase power contact line, through the brush trolley motor connected to the power supply, in the actual operation of the relevant personnel through the power supply phase sequence control will be able to move forward and backward according to the requirements of the trolley operation. This method not only eliminates the need for trailing cables, but also significantly improves the reliability of the operation on the basis of reducing the operating costs of the system. More components of the fabric system, usually including the track, the formation of switches, automatic control systems and discharge mechanism, etc., which is installed in the hopper material sensors, the amount of material can be detected on the hopper, the control system will be able to detect the results of the operation of the automatic judgment of the feeding operation, and trolley tracks on the switches to control the specific location of the feeding, so as to achieve the automation of the operation of the fabric. Fabric trolley automation control system mainly includes bin level detection and control, related equipment to implement logical chain and protection control and fabric trolley position detection and control, etc., to a certain extent, to ensure that the whole dosage feeding automatic control system of safe and stable operation.
2 man-machine interface design and safe operation
Mineral furnace smelting in the actual operation of the process is taken in a continuous manner, because this requires the dosing and feeding system must be able to effectively adapt to the characteristics of the continuous operation of the mineral furnace, if in the actual operation of the process of the dosing and feeding system has any problems or failures, the relevant personnel must have the corresponding emergency response measures. In this study, the automatic control system has the following emergency measures in the design process.
2.1 Dosing section
Electromagnetic vibrating feeder and vibrator in the dosing system include two modes, respectively, automatic and manual, the relevant personnel in the automatic mode can be set according to the program to implement the automatic dosing work; if in the manual mode, the relevant personnel need to be manually operated to complete the dosing work.
2.2 Feeding part
The feeding system usually includes two modes, namely, automatic and manual mode, and the feeding control mode also includes two modes, namely, frequency conversion and industrial frequency. Generally speaking, in the actual operation process, when any failure occurs in the automatic mode, it can be switched to the industrial frequency mode, and then continue to complete the feeding operation under manual operation.
2.3 Fabrication
Fabric settings also include automatic and manual two kinds, usually the fabric in the automatic mode can realize completely automatic operation, and when any failure occurs in the automatic mode can be switched to the manual mode in a timely manner, and in the manual mode, the manual can be effective control of fabric trolley mode of operation.
3 Conclusion
In summary, the study for the mineral heat furnace dosing system is mainly the use of PLC, industrial control machine and weighing instrumentation to coordinate, and jointly complete the task of automatic dosing, through practice shows that such a system in the actual application of the process has the characteristics of stable and reliable operation, and at the same time, the human-computer interface has a beautiful and easy to operate advantages. And the application of automatic control system effectively improves the quality of ferroalloy products, improves the working environment of workers, significantly improves the economic and social benefits of enterprises, and thus promotes the progress and improvement of China's automatic control system.