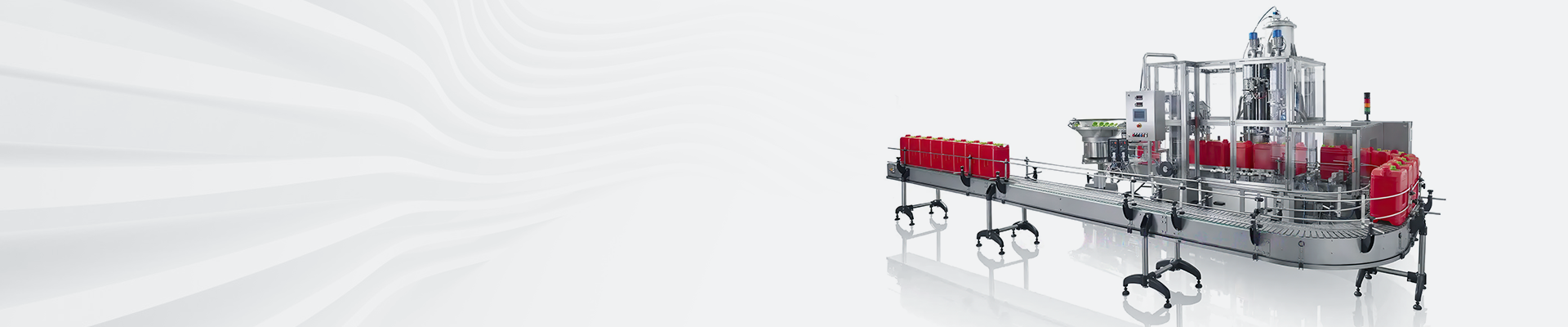
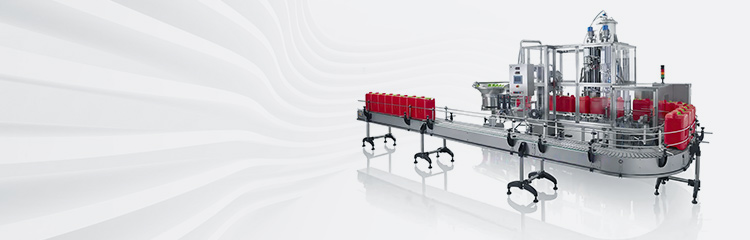
摘要:配料系统能够按照设定的配方自动控制相应的输送器向计量斗内输入物料,从而完成自动配料。根据配方、重量及控制参数,驱动各料仓喂料搅龙的启动、停止、快慢及点动操作,并驱动秤门在规定条件下的开启和关闭,以完成整个称量过程,若有秤下刮板机,则还将完成对此刮板机的启停控制。
配料是饲料生产中的关键工艺之一,每个饲料厂对配料工艺的要求都不一样,因此,设计一种喂料机结构的配料系统,使其能够灵活组合,以便能够轻松满足不同饲料厂的不同工艺要求。首先将整个自动配料系统分解为若千不同功能的模块(如称重模块、混合模块等),每个模块均由高性能微控制芯片及其外围线路组成,并将其封装在各自的控制盒内,且这种控制盒可以方便地安装在电气柜中的导轨上,每一个控制盒内的模块都能独立地完成其规定的控制功能。
控制模块之间的信息交换通过CAN总线来实现,CAN总线是一种高可靠性的工业控制总线,它可以将配料过程所需的不同功能的控制模块连接到CAN总线上,从而通过CAN总线实现功能模块之间控制信息和状态信息的传输,可以完成特定定量功能的各种控制模块外,投料系统还选择计算机作为人机界面,该界面也用于数据处理。
计算机作为人机界面的主要功能概括为:将模块通过CAN总线上传的定量状态信息通过动画以直观、动态的方式显示在计算机屏幕上,以达到使操作人员对定量过程一目了然的效果;定量过程的手动干预(例如启动、暂停、更换配料等)可以通过用鼠标点击图形界面上的按钮和菜单来实现,即相应的控制命令通过CAN总线传输到控制系统;控制命令通过CAN总线传输到控制系统。(控制命令通过CAN总线传输到相关控制模块)上传的定量数据汇总成各种报告,以便存储、显示和打印。通过网络从管理部门接收配方,同时将各种定量生产数据传输到管理部门。
1个主控制模块
这是所有控制模块中唯一的强制模块,其主要功能是:①协调所有其他控制模块的动作;②通过CAN总线接收来自所有其他控制模块的状态信息,并通过其232串口上传至计算机;③从计算机的串口接收手动控制命令,并通过CAN总线传输给连接到总线的相关模块;④混合机和手动加料的控制功能相互关联;④混料机和手动加料的控制功能与其他控制模块的控制功能相关。搅拌器和手动加料的控制功能相对简单,是常规喂料系统所必需的,因此也集成在该设备中。
2称重模块
这是系统中最重要的功能模块,负责电子秤的所有称重控制。如果系统中安装了多台秤,可以配备相同数量的称重模块。该模块的主要功能有:①从计算机接收配方内容和称重控制参数;②接收并执行计算机发出的开始、暂停、换仓等加料命令;③接收来自称重仪表的重量数据;④根据配方、重量和控制参数,驱动每个料仓的进料搅拌器进行启动、停止、快速、慢速和指向操作,并在规定的条件下驱动秤门打开和关闭,以完成称重过程,可以配备相同数量的称重模块。如果秤下面有刮板机,它还会完成刮板机的启停控制;⑤上传实际称重结果和报警信息。
3液体秤模块
该模块的功能与上述固体原料称重模块的功能基本相同,只是控制方法不同。
4加液模块
当配料过程使用流量计进行液体测量和液体添加过程控制时,使用该模块。其功能如下:①从CAN总线接收液体部分的配方和液体添加的控制参数,并上传液体添加状态数据;②当接收到加液命令时,开始加液过程,并对流量计的加液脉冲进行计数,当计数值与公式中设定的重量换算的脉冲数一致时,加液结束;③检测无液和泄漏故障,并在故障发生时上传报警信息。出现故障时会上传报警信息。
5配料终端模块
这个定量模块的主要组件是一个5英寸的LCD,可以接收和显示中文信息。其功能是从CAN总线接收手动配料信息,并将其显示在LCD屏幕上,供手动配料操作员查看。显示的内容如下:①当前配方名称和总批次数;②前几批的当前投料量;③后续配方名称和配方批次总数。
6打包秤终端模块
该模块用于预混料生产的配料系统,其主要部件也是一个5英寸的液晶显示屏,可以接收和显示中文信息。其功能是从CAN总线接收包装秤所需的信息,并显示在液晶屏上,供包装操作人员查看,显示内容如下:①当前配方名称和总批次数;②正在混合的物料是第一批及其批号;③缓冲仓中要包装的物料是第一批及其批号(每批物料可以有一个特别指定的批号,用来标识该批物料,以便将来检验。批号可以由11位数字或字母组成)。
7手加料验证模块
配料过程中手工投料成分的确认和验证是保证饲料质量的重要手段配料过程中手工投料成分的确认和验证是保证饲料质量的重要手段在称量料品时(即称量手工添加成分的原料时),料品的代号、称量的重量、所属配方、称量日期及其操作人员的代号、etc可以写入包装袋附带的非接触式IC卡,以便投料时进行验证,因此,该模块的功能是①从手投料部分接收来自can总线的配方,并显示在LED屏幕上;②在输入每袋料品之前,读取料袋上IC卡中的料品信息(只要将装有IC卡的料袋靠近读卡器的那部分卡即可);③IC卡读卡器信息和当前手动投料配方进行验证和确认,即料品是否为IC卡读卡器信息和当前手动投料配方进行验证和确认的配方,即料品是否为配方中的成分,重量是否在规定误差范围内等。如果超出范围,则报警,报警信息传送到中央控制室的计算机,由中央控制器处理;④将已投在进料处的物料在屏幕上和中央控制室的计算机屏幕上打在已投在物料上的标记上(通常是物料所在行的线条颜色发生变化);⑤如有必要,还可附在电子秤上进行重量校准。
8称料模块
称重模块带有一个电子秤、一个触摸屏和一个读卡器,其功能是:①CAN总线接收来自中央控制室的称重任务;②料物的称量按照传递给任务的配方,逐步称量物料,当称量的物料重量符合规定的重量时,它会将相关信息写入事先在IC卡中留出的写卡器中,并发出蜂鸣信号来表示物料的称量,以通知IC卡中已写入的信息,将已经写好信息的IC卡取下来,放进规格定量范围的包装里。如果有多台料品称重机同时称重料品,则必须配备相同数量的料品称重模块及其附属设备。
9其他功能模块
其它功能模块可根据需要进行设计制作。由上所见,模块化结构的配料系统,对于特定的配料工艺,只要选用所需的控制模块盒进行组装,并对电脑监控软件进行相应的组合,便可方便地完成一个符合工艺要求的配料系统的组建。由于其组合的灵活性,若想把配料的前道工序和后道工序的控制都组合到一起,也是一件不难的事情。该结构的配料系统还有如下特点。①模块控制盒可以在对应的设备处就近安装,与系统的连接仅用一对双绞线(即CAN总线)。从而使布线十分简洁。②由于配料过程在各控制模块中独立完成,电脑仅充当人机界面,所以一旦电脑发生故障,整个配料过程则仍在进行,只是缺少了人的有效监控而已。不过,有经验的中控员仍可根据各控制盒上的指示灯及称量仪表的读数,大致了解当前的配料状态。若电脑故障及时排除,重新启动电脑的监控程序,则可继续对正在进行的配料过程进行监控。通常,为了使配料过程在人的有效监控下安全运行,当主模块一旦检测到与电脑的通讯中断,则在各秤的当前称量完成后,自动终止后续的称量。按上述思路设计的配料系统,已在一些饲料厂运行成功.其组合的灵活性及其运行的可靠性均已得到验证,用户反应良好。