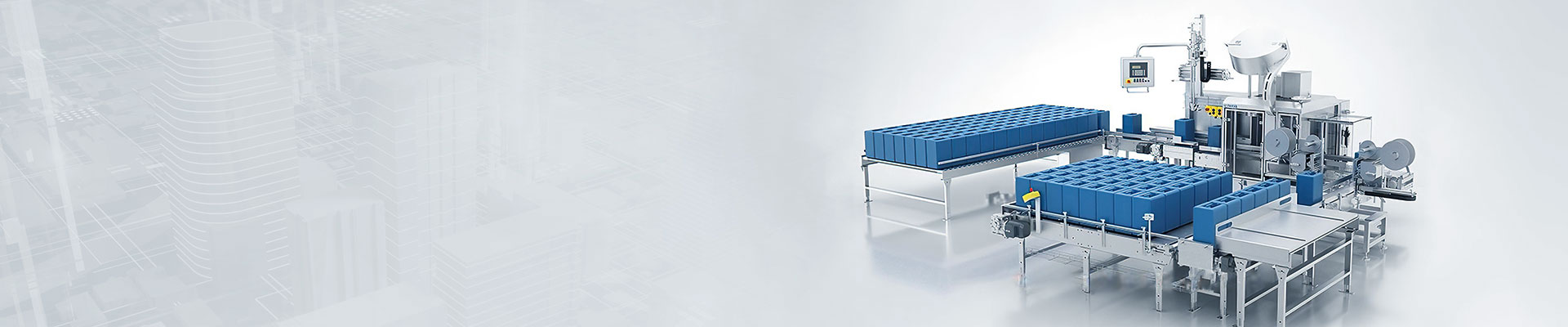
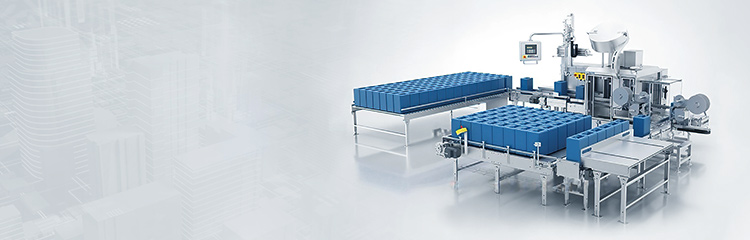
Weighing dosing system based on PC and precise quantitative dosing is a set of machine, electricity, signal processing and dosing in one of the technical equipment, electrical part is mainly composed of weighing sensor, weighing instrument, programmable controller (PLC), frequency converter, industrial computer and printer. In the process of dynamic weighing, the weight signal of the weight sensor on the quantitative weighing hopper is received. When the weight of the material in the hopper reaches each set value, the output I/O quantitative signal to the PLC. PLC collects the quantitative output signal of the weighing display instrument, and controls the output frequency of each frequency converter through PLC, so as to control the thickness and fine feeding amount of the corresponding vibration feeder and the switching door action of each weighing hopper.

Automatic Dosage system is a kind of automatic dosage equipment applied in industrial production, with the computer of uploading coordinated computing program as the control center, for the automation control of the mixing process at the front-end of production, realizing the program of machine for man. Not only has high measuring accuracy, automation control and other characteristics, but also for the enterprise to save a lot of production labor, for the enterprise to bring great benefits.
The reaction kettle weighing adopts the combination of floating type and semi-floating type, so that the weighing control system formed afterward can automatically measure the weighing data, which can be stored in the computer and manage the weighing data. It is realized by the change of heat transferred through the jacket, which is realized by controlling the electric heating power. To realize the temperature control, the temperature of the reactor and the jacket temperature must be detected, and the control program carries out automatic temperature control according to the temperature change in the jacket and the reactor. The feeding system will start from the feeding pump of the raw material until the qualified material is sent to the reactor. It will include the control and interlocking of all the feeding and discharging valves, the starting and stopping of the feeding pumps, the control state detection of fast and slow feeding and all the data processing functions.
The feeding system is mainly controlled by PLC, touch screen and weighing module, PLC and its corresponding electric main circuit are installed in the electric control cabinet to control the field signals. The control cabinet is installed with touch screen HMI for monitoring and adjusting, displaying the working status of dosage, time setting, dosage adjusting parameters, alarm information, etc., in order to improve the reliability of safe operation of dosage. According to different kinds of powdery objects mixed together in different weight proportions and the new material, the use of dynamic data exchange (DDE) technology to realize the InTouch on the production site data collection and transmission, while completing the data interaction between VB and InTouch, and gives a specific configuration process dosage program.
Equipment form: horizontal, vertical multi-layer / single / insulation
Equipment series: 50L-150M3
Working temperature: room temperature / can be sterilized in place
Working pressure: atmospheric pressure
Heating and cooling mode: vacuum, electric heater, jacket and inner snake tube, sterile air
Stirring mode: rotating shaft, rotating cylinder type.
Control form: automatic weighing and dosing control (hand control)
Material: high quality stainless steel
Temperature control range: 20 ~ 60 ℃, ± 0.5 ℃
Rotation speed control range: 0~30rmp, ±1%