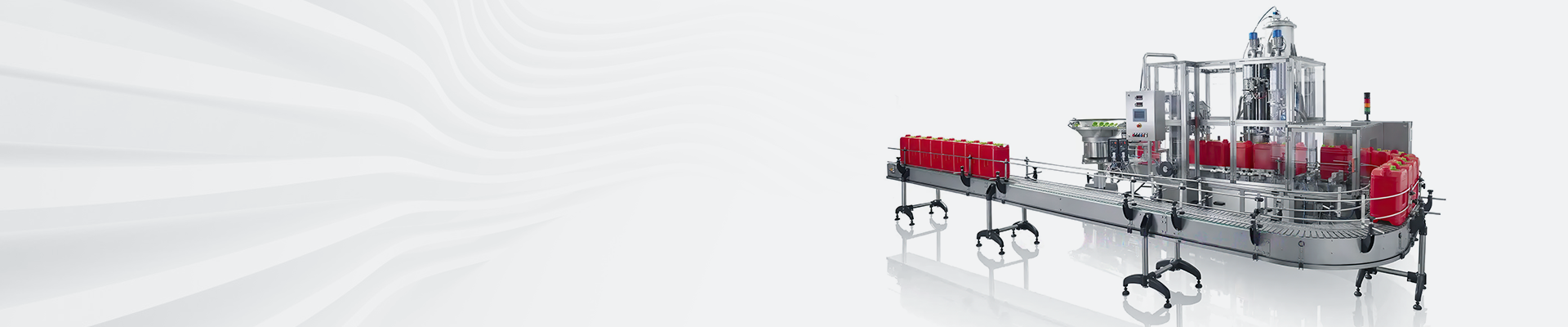
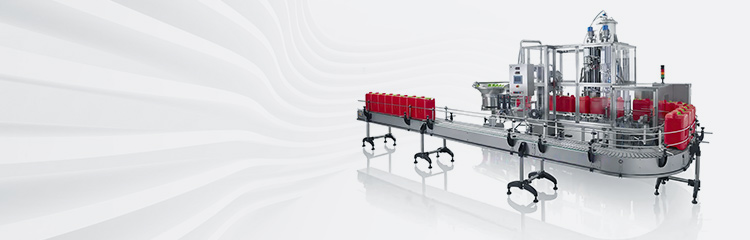

Summary:The automatic batching system mixes the main ingredients and auxiliary materials according to the proportion, passes through the belt scale, uses PLC to monitor the entire material conveying and batching process, and completes the function of displaying and alarming system faults. The belt conveyor is completed by transmitting signals to the frequency converter. Speed batching adjustment.
First, the basic composition and working principle of batching
Automatic batching system is widely used in various aspects of industrial production, mainly composed of silo, weighing silo, intermediate silo, mixing silo, silo wall vibrator, feeding vibrator, discharging vibrator, as well as conveyor belt, mixer and other parts. The motor completes the control of each vibrator and mixer; the solenoid valve completes the control of the intermediate bin door and the discharge door of the mixing bin. Once there is a failure in one aspect, a bell will be issued to warn and stop all output actions, until the fault is removed before continuing to run.
When the automatic dosage system is energized, the motor drives the belt to carry out the action, and the microprocessor carries out the control of the motor speed. The material is dropped from the hopper to the drop zone, transferred to the weighing zone by the belt, and the electronic belt weigher will weigh the material on the belt. The load cell outputs a voltage signal according to the material pressure, which is amplified and outputs a metering level signal, which is proportional to the weight of the material. Then the signal will be sent to the upper computer interface, and converted into a flow signal, the flow value in the current upper computer for display, and at the same time sent to the PLC, the PLC will be set with the upper computer for comparison with the dosage of the given value and arithmetic. The PLC will compare and calculate with the dosage given value set by the upper computer. The control quantity will be transmitted to the frequency converter, and the output value of the frequency converter will be changed, so as to complete the control of the rotational speed. Adjust the amount of feeding the same as the set value, complete the dosage process.
Second, PLC-based weighing system design
1、Hardware design of weighing system
The weighing and feeding system mainly uses SIMATICS7-/300 series PLC, the system by S7-/300 as well as the upper computer to realize the main and auxiliary batching machine two-level control. Now I take the belt scale PLC control of No. 1 to No. 4 as an example, each electronic belt scale is composed of a belt drive motor; two material level sensors; a speed sensor; a load cell and a frequency converter. The switching quantity controls the running status of the motor, and the input of the frequency converter control terminal is determined by the digital input of the PLC, which is tuned to high-frequency pulses by the frequency converter and delivered to the belt drive motor. The material level sensor starts detecting whether the hopper contains material or not, and the speed of the motor is monitored by the speed sensor. The system requires 8 digital output signals, 25 switching input signals as well as 24 switching output signals, and the total number of I/O points is 57. The number and type of I/O points are shown in Table 1.
SIMATICS7-/300 from Siemens is a small modular PLC, the advantage of which is that a wide range of individual modules can be combined to form systems with different requirements. Table 1: Number and type of PLCI/O ports
I chose SIEMENS S7-300 series PLC, is based on the company's automatic dosage system of controlled objects of the number of I / O points, as well as process requirements, scanning speed, and other aspects of the actual situation for consideration, the PLC for the CPU315-2DP. this model is a CPU with fieldbus SINECL2-DP interface template, with 48KB RAM and It has 48KB of RAM and 80KB of load memory, and its storage capacity can be expanded with a memory card to a maximum of 521KB, 1024 digital points, or 128 analog points. A 32-point SM322 relay output module and 32-point and 16-point DC SM321 digital input modules were selected for system I/O counting.
2、Software design of dosage
SIMATICS7-300 series PLC is written in SIMATIC language, which is a language that can be run in a general-purpose microcomputer as well as WINDOWS environment. Through the programming software, not only can it be very convenient to write the program, and through the adapter cable will be written program directly into the PLC for execution, but also in the debugging, you can also be on-line monitoring and adjustment of signal input and output, and even on-line modification of the program value, which can be said to be very convenient.
To divide a working cycle of the system into several sequential cloths, each step is represented by a programming original, which is the basic idea of sequential function diagram design. The division of steps is based on the state of the outputs. In the case of any step, the ON/OFF state of the outputs is unchanged, but the total state of the two neighboring outputs is different. This is the direct logical relationship between the state of the programming element and the state of each output quantity. Between the various steps of the sequence function diagram, there is only one active step, and each step needs certain conditions to realize the conversion between the steps, only in the previous step for the active step, and to meet the conversion conditions of the state below, can be converted from the previous step to the subsequent step, at this time, the subsequent step is changed to the active step. When designing the sequence function diagram for the production line of the automatic dosage system, we divide a cycle into 10 steps according to the actual control requirements, and use the bit memory N to represent each step, N0.0 is set as the starting step, and N0.1-N1.1 represents each step.
The STEP7 language divides the user program into different types of blocks, and the program blocks can be divided into two major categories: system blocks and user blocks. User blocks mainly include: organization blocks (OB), function blocks (FB), functions (FC) and data blocks (DB). The main program of the system can be put into the organization block, while the subroutine can be put into the function block (FB or FC).
In the system, PLC is mainly responsible for receiving external switching signals and digital signals input from sensors, so as to judge the current operating status of the system and output various signals to control contactors, relays, solenoid valves and other components to perform the corresponding tasks. In addition to the above, there is an important task, is to receive the upper computer control commands to complete the automatic dosage control.
This automatic dosage system program has 7 blocks, respectively OB1 and FC1 to FC6. OB1 is a main program, through the other 6 "CALL" to call the current statement, and in this way call FC1-FC6 function module, in order to complete the whole program running purpose. 6 function module specific task allocation According to the following allocations: FC1 is mainly to complete the system operation and operation mode setting; FC2 is mainly to complete the system stopping control; FC3 is mainly to complete the ratio of metering pumps and metering pumps control; FC4 is mainly responsible for faults and accidents occurring in the processing control; FC5 is mainly to complete the control of the inverter; FC6 is responsible for displaying the relevant indicator.
3, the design of the ladder diagram in the system
In the program design ladder diagram design method for the start-stop circuit design method, this method only applies to the basic instructions related to the electric shock and coil, is a more general programming method, can be applied in any type of PLC. In the program, the initialization pulse SM0.1 is used to set the programming element M0.0, which corresponds to the initial step, in preparation for the completion of the conversion.
When the start button is pressed, the automatic conversion is completed in accordance with the sequence designed in the sequence function diagram. The normally open contact of the programming element of the previous step is used as a prerequisite for the conversion from the previous step to the subsequent step and is connected in series with the conversion condition, and the conversion from the previous step to the subsequent step can only be completed if the previous step is an active step and meets the corresponding conversion condition, and the normally closed contact of the programming element of the subsequent step is connected in series with the coil circuit of the programming element of the previous step. The normally closed contact of the subsequent step programming element is connected in series with the coil circuit of the preceding step programming element. When the preceding step is converted to the subsequent step, the subsequent step becomes active and the preceding step becomes inactive, and the self-protection function is realized by the normally open contact of the subsequent step, which completes the whole conversion control action requirements.
In order to realize that in the automatic mode of operation, the cycle of each mode can be completed continuously, while in the single-cycle mode, the cycle is stopped after only one cycle. In the program, the upper register M2.0 is used, in the automatic mode, after starting the power supply, M2.0 can be powered up and realize the self-protection function, while in the single-cycle mode, after starting the power supply, M2.0 can be powered up, but the self-protection function can not be realized, and in the manual mode, after starting the power supply, M2.0 can not be energized. When switching between the initial step M0.0 and the first step M0.1, the start button I0.4 is not connected in series with the coil circuit of M0.1, but the normally open contact of M2.0 is connected in series with the coil circuit of M0.1, so that the switching control between the automatic and the single-cycle mode of operation can be realized. In the manual state, I1.5 makes the steps of various programmed components in the reset state, and the corresponding outputs can be energized when the electric switch button is pressed respectively, so as to realize the point control of the mixer as well as conveyor belts No. 1 and No. 2.
Conclusion
The use of SIMATICS7-/300 series PLC system, with user-friendly programming, automatic completion of all the actions of the metering and dosing system, greatly reducing the customer's workload, the optimization of the closed-loop control system, not only reduces the cost, but also improves the accuracy of the control, to improve the efficient and stable operation of the entire system and reduce the maintenance of the latter. In the modern society of rising labor costs, the use of this solution can greatly improve production efficiency, and simple operation and easy maintenance. It is a highly feasible program.