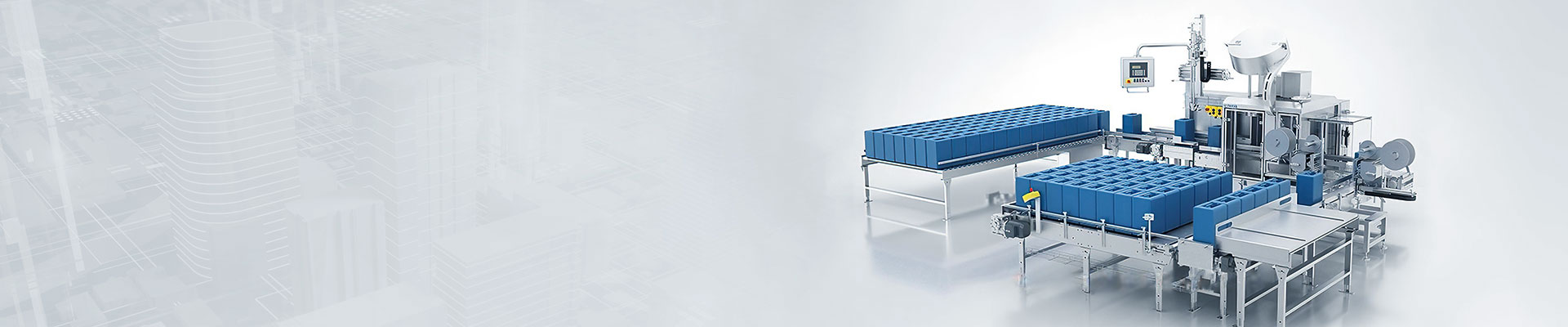
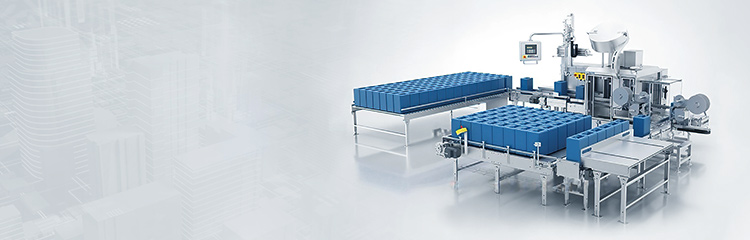
Batching scale adopts metering tank, equipped with pressure or tension weighing module for force-electricity conversion, the signal is amplified and processed by weighing instrument and then connected to PLC or DCS to complete the metering, and at the same time, it is used in conjunction with PLC. Based on the composition, working process, working principle, hardware and software design of metering and dosing automatic control to improve the quality of the process. The main ratio, temperature, time and material pre-treatment. PLC ladder programming is used to realize a variety of logic sequence control and flow rate detection control. The control system can realize automatic/manual switching and frequency conversion/industrial frequency switching (if it is necessary to quickly inject into the reaction tank, the industrial frequency operation mode can be used).

The dosing machine adopts metering tank, configured with pressure or tension weighing module for force-electricity conversion, and the signal is amplified and processed by the weighing instrument and accessed to PLC or DCS, etc. to complete the metering, and at the same time, it is used in conjunction with PLC. Based on the composition of metering and dosing automatic control, working process, working principle, hardware and software design to improve the quality of the process. The main ratio, temperature, time and material pre-treatment. PLC ladder programming is used to realize a variety of logic sequence control and flow rate detection control. The control system can realize automatic/manual switching and frequency conversion/industrial frequency switching (if it is necessary to inject the reaction tank quickly, the industrial frequency operation mode can be used).
According to the proportion of their respective formulas into a large tank, and even in some factories even the subsequent mixing part of the presence of manual mixing; the entire link in the environment will leak a lot of dust, on the workers, machines, products are all harmful but not beneficial. Dosing scale can do dust-free operation.
In the unpacking link, there are tons of bags unpacking station, tons of bags unpacking station (single machine can be optional dust removal system).
Conveying link, the use of vacuum Loading machine for material transportation, not only to meet the material from multiple points, but also to avoid dust leakage to the site conditions. Further back even if the pipeline leakage, negative pressure pneumatic conveying system will only draw air from the environment into the pipeline, and the site will not cause dust pollution.
Vacuum loader conveys materials to the storage bin, each bin is equipped with a screw conveyor at the bottom, and servo motor-driven screw, conveying materials to the measuring bin. The bottom of the measuring silo is equipped with a load cell, the whole process can be opened after the end of the valve at the bottom of the silo, the material with the help of gravity down to the mixer.
Valve closed, the mixer works, the whole process is over. The whole process is finished. Powder automatic dosing system features:
Avoid human error: production instructions and formulas need to be audited, otherwise it can not take effect, the correct material is recognized when feeding, otherwise it can not be put, the dosage process is fully automatic, no need for human operation.
No dust leakage during the working process, meanwhile avoiding the pollution of materials, adopting dustless Feeder to avoid dust escaping when feeding, adopting vacuum feeder to convey materials to the silo in airtight, and adopting airflow sealing when metering and feeding.
The structure and material of the equipment are in line with FDA regulations and health standards to ensure thorough cleaning and avoid cross contamination.
With on-line cleaning function, on-line drying function and quick installation structure, easy to clean and maintain.
Adopting high precision weighing module and many kinds of anti-interference technology, the weighing data is accurate and reliable.
Adopting advanced control algorithm and high performance actuator, high positioning accuracy, high metering accuracy and high output.
Adopting SIEMENSPLC and HMI touch screen technology, reliable performance, simple operation, with production data report, archiving, recording and tracking functions. It can communicate with the upper computer and exchange data.
System alarm and self-checking function to ensure the smooth running of production.