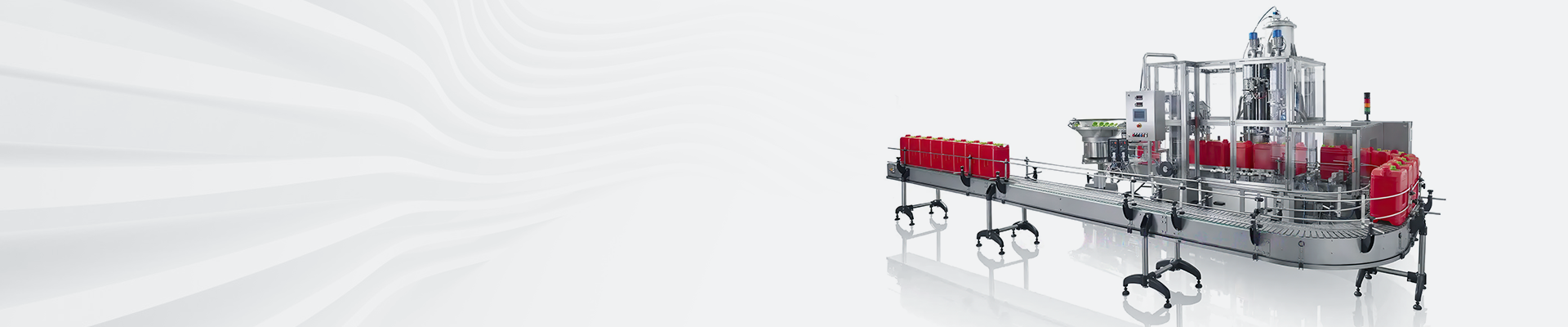
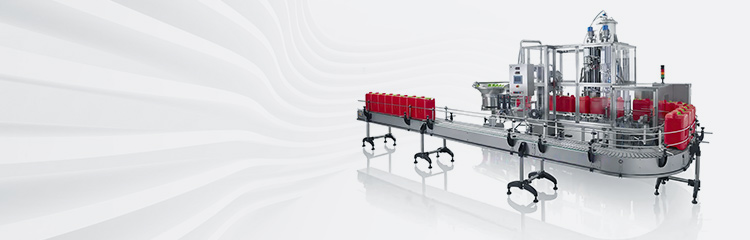

Summary:The automatic liquid filling machine is programmably controlled by PLC.It is mainly composed of liquid storage tank, filling mechanism, barrel pushing mechanism, incoming roller conveyor, weighing mechanism, outgoing roller conveyor and control box.
0Introduction
Barrel weighing and filling machine using high-precision electronic weighing technology, automatic filling machine to achieve the measurement of liquid filling, its measurement accuracy is not affected by pressure, temperature, bubbles and other factors, the filling range of 5 ~ 50kg, can be applied to edible oil, lubricants, chemical and other industries.
1 Working Principle
Liquid filling machine by PLC programmable control. It mainly consists of liquid storage tank, filling mechanism, barrel pushing mechanism, in roller conveyor, weighing mechanism, out roller conveyor and control box.
Automatic filling machine control empty barrel feeding, filling valve filling, filling and weighing, finished product output, to complete a filling process. Weighing and filling equipment storage tank on the design of the feeding mechanism, filling within the design of the float position set two values, the lowest value and the highest value, the float position in the lowest value of the feeding, the float position rises to the highest value to stop feeding. The filling valve is driven by a duplex cylinder to fill in two times. Automatic filling machine when the barrel is fed into the roller conveyor, photoelectric switch 1 detects that the barrel is in place, push the barrel cylinder action, liquid filling machine will push the empty barrel to the weighing mechanism on the unpowered roller, that is, position 2. photoelectric switch 2 detects that the barrel has reached the filling position, the filling valve is fully open to start filling, when the filling weight reaches the set initial weight, the filling valve is half-open to fill; when the filling weight reaches the set weight, that is, the required filling weight When the filling weight reaches the set initial weight, the filling valve is half open for filling; when the filling weight reaches the set weight, i.e. the required filling weight, the filling valve is fully closed. Push the barrel cylinder action, push the next empty barrel to position 2, this empty barrel will be quantitative liquid filling machine filling barrel from position 2 to position 3, that is, pushed to the conveyor conveyor out.
1 main components structural design
2.1 Liquid storage tank
Liquid storage tank, used to reserve enough liquid filling, filling structure mainly includes box, box cover, float components, pneumatic butterfly valves and mechanical valves, float components by the float, float pressure plate and connecting rod composed of a whole.
When the liquid level in the liquid storage tank is at the lower liquid level (lower limit value) and below, the float pressure plate is detached from the mechanical valve, the pneumatic butterfly valve opens, and the liquid material is conveyed to the liquid storage tank through the feeding port, and the float assembly rotates in the direction of the arrow as the liquid level rises, and the filling system stops conveying liquid material to the liquid storage tank when the liquid level in the liquid storage tank reaches the upper liquid level (upper limit value) and the float pressure plate presses down the contact of the mechanical valve, and the pneumatic butterfly valve closes, so the filling system stops conveying liquid material to the tank. The filling system stops conveying liquid material to the liquid storage tank, and so on.
2.2 Filling mechanism
Weighing filling machine filling mechanism mainly consists of head, end head, end cap, shaft, container, cylinder, etc. The cylinder is a double-stroke cylinder. As the material flows into the container by its own weight, it requires better fluidity of the material. Cylinder initial position, the head and the end of the spacing H1, H1 size directly affects the filling accuracy, general barrel weighing liquid filling machine H1 value is not adjustable, and the equipment cylinder screw adjustable cylinder, according to the filling speed or material mobility requirements, adjust the screw on the cylinder before filling, H1 can be adjusted, the position of the filling for the high-flow filling; when close to filling the weight of the first action of the cylinder. When close to the filling weight, the first action of the cylinder, the spacing between the head and the end becomes H2, the first stroke of the filling machine cylinder h1 = H1 - H2; when the filling weight is reached, the second action of the cylinder, the spacing between the head and the end becomes H, at this time to stop filling, the head and the container with no gap between the head to prevent the material from falling when the impact is too large, the end of the head is open with a uniform small holes.
2.3 Weighing mechanism
Weighing mechanism of weighing filling machine mainly consists of independent non-powered roller conveyor, weighing filling device weighing sensor, measuring accuracy mainly depends on the accuracy of the sensor.
3 weighing and filling machine action control system
3.1 Action control
According to the process flow of the barrel weighing and filling machine, the PLC controller is used to coordinate and control the action of each part of the equipment. The controlled equipment (or instrument) are: pneumatic butterfly valve, motor, cylinder, load cell, motor.
3.2 Pneumatic control principle
According to the bucket weighing and filling machine action requirements, the design of the corresponding pneumatic system, the pneumatic system mainly consists of a pneumatic triplex, 4 electromagnetic directional valves, 5 out of the air throttle valve, a gas control valve, a mechanical valve and a pneumatic butterfly valve. The air output from the air source contains a large amount of moisture, oil and dust and other impurities, pneumatic triplex is the appropriate removal of these impurities, in order to avoid them from causing harm to the normal operation of the pneumatic system. The outgoing air throttle valve is to control the movement speed of the cylinder and make the piston run stably.
3.2.1 Filling air circuit design
Quantitative filling machine empty barrels from into the roller conveyor input, when the photoelectric switch 1 detects empty barrels, cylinder 1 action, piston rod 1 will push the empty barrels to the metering weighing mechanism roller, filling head down. Cylinder 2 is a compound action type cylinder, metering and filling device full stroke consists of two parts i.e. stroke 1+stroke 2, which is used when filling. When the photoelectric switch 2 detects the empty barrel under the filling head, the cylinder 2 action, the piston rod 2 retracts the full stroke, the filling head is all open, the liquid automatically flows into the barrel, when the barrel of liquid reaches the main metering value, the weighing module gives a signal, the piston rod 2 stretches out to reach the first stroke i.e. stroke 1, at this time, the filling mouth becomes smaller, metering and filling device when the barrel of liquid reaches the set value, the weighing module gives a signal, the piston rod 2 When the liquid in the barrel reaches the set value, the weighing module gives a signal, and the piston rod 2 extends to the second stroke, i.e. stroke 2, at this time, the filling port is closed, and liquid filling is completed. When the piston rod 1 pushes the next empty barrel to the weighing mechanism roller, this empty barrel also pushes the liquid barrel to the roller conveyor, and the liquid barrel is conveyed out.
3.2.2 Feeding air circuit design
Weighing and filling device feeding air circuit design selection of air-controlled valve, mechanical valve, pneumatic butterfly valve control, is a new design ideas, air-controlled valve is normally open, mechanical valve, pneumatic butterfly valve is normally closed. When the air source is opened, the air through the air control valve will directly open the pneumatic butterfly valve, and the liquid is transported to the liquid storage tank through the butterfly valve. Weighing and filling system when the liquid level in the storage tank reaches the set maximum value, the automatic filling system design of the float pressure plate presses down on the mechanical valve contacts, the mechanical valve shift, air through the mechanical valve will be pneumatic valve shift, weighing and filling equipment to the pneumatic butterfly valve of the air is closed, pneumatic valve and the pneumatic butterfly valve between the pipeline air through the pneumatic valve back to the atmosphere, the pneumatic butterfly valve is closed to stop to the storage tank delivery of liquid. With the filling process, the liquid level in the reservoir tank continues to fall, when the liquid level in the reservoir tank reaches the set minimum value, the design of the pressure plate to leave the mechanical valve contacts, mechanical valve, pneumatic valve reset under the action of the spring, the pneumatic butterfly valve is opened, the liquid through the pneumatic butterfly valve and re-conveyed to the reservoir tank. And so the cycle is repeated.
4 Conclusion
Weighing filling machine can be based on actual needs, such as liquid fluidity, filling volume of the size or the shape and size of the bucket containing the liquid, on the basis of the structural changes made to the liquid filling device to make it more widely used; can also be made according to the output needs to be made into a multi-head filling. If the equipment is equipped with automatic barrel feeding machine in front and capping machine and palletizer at the back, it can realize the fully automatic liquid barrel filling assembly line.