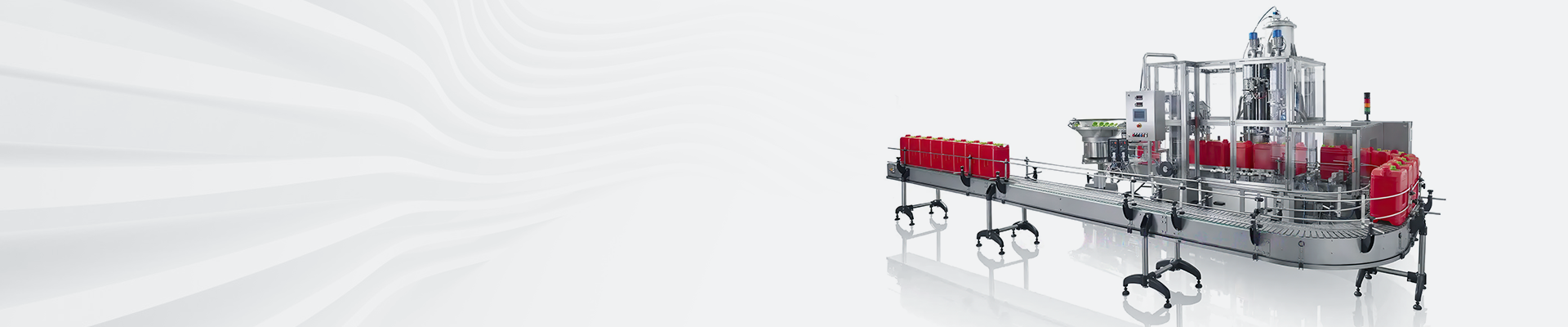
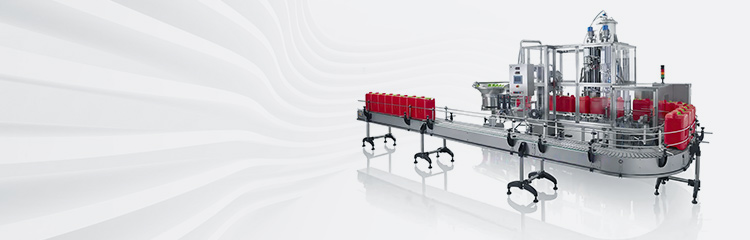

Summary:The liquid filling machine realizes speed regulation of the asynchronous motor by changing the stator power supply frequency to change the synchronous speed. It uses variable frequency control to drive the motor. The starting current is small, and it can realize soft start, multi-stage speed regulation and stepless speed regulation, which is convenient Perform acceleration and deceleration control.
Preface
Filling machine with the development of material dispensing, the emergence of a revolutionary filling system capable of filling means to achieve a variety of control functions. Filling equipment has the advantages of good versatility and flexibility as well as easy to operate, simple to understand, inexpensive, etc., so it can be fully adapted to the quantitative filling machine industrial environment of the universal control device. Increased arithmetic operations, data conversion, process control, data communications and other functions, can easily complete large and complex tasks.
Filling frequency control is the application of frequency conversion technology and microelectronics technology, by changing the motor operating power supply frequency mode to control the AC motor power control equipment. In the field of industrial production, frequency conversion speed control is a more reasonable and ideal speed control method of asynchronous motor control, by changing the stator power supply frequency to change the synchronous rotational speed to achieve the speed control of asynchronous motor, in the speed control process from high speed to low speed can be maintained at a limited rate of rotation, and thus has a high efficiency, wide-range and high-precision speed performance, can be a good way to improve the efficiency of industrial production. The use of frequency control drag motor, starting current is small, can realize the soft start, multi-step speed regulation and stepless speed regulation, convenient acceleration and deceleration control, is the motor to obtain high performance, a substantial saving of electric energy, and thus frequency control in industrial production and life has been more and more widely used.
Comprehensively described the use of frequency control of the respective functions of the design to achieve multi-step speed regulation. The actual rotational speed of the motor is checked by the photoelectric switch and the internal timer, and this rotational speed is used as a feedback signal to control the motor speed, thus realizing the automatic control of the speed of the filling conveyor. The purpose of automatic control is to make it consistent with the speed of the filling machine and save the time of filling.
Can filling conveyor design requirements
Liquid filling machine according to the bottle flow through the filling frequency control to adjust the speed of the conveyor belt, according to the bottle flow to choose a multi-stage speed control, so that the speed of the conveyor belt and weighing and filling machine speed is well matched.
Weighing and filling machine by photoelectric detection switch to detect the bottle flow speed, different bottle flow speed corresponds to the different speed of the frequency control, by the output terminal to control the frequency control of the multi-stage speed control terminal, to realize the speed adjustment, to achieve matching with the filling speed.
In the case of constant filling speed, the bottle speed must be consistent with the filling speed, in order to maintain consistency, it is necessary to use a photoelectric sensor to detect the bottle flow pulse input to the filling system, control frequency control multi-step speed regulation. And can be done on the weighing and filling machine on the upper monitoring. Frequency drive motor, so as to realize the speed regulation of the motor that is to control the speed of the bottle flow and canning speed consistent, to achieve the design purpose.
Weighing and filling machine process
Filling frequency control motor rotation drives the belt drive, and then the bottle to be filled is transmitted to the weighing and filling machine, to achieve the coordination of the bottle flow speed and filling speed, so as to improve work efficiency. Filling machine start after pressing the motor positive switch, the motor began to rotate, drive the belt drive, to be filled bottles in the belt drive through the photoelectric sensors, load cells for bottle counting sent to the filling machine for data processing, the processing of the bottle flow rate and memory inside the value set to compare, to determine whether the need for speed control, if not need to adjust the speed of the motor in accordance with the original speed of running If the need for speed regulation, the output control signal to the filling machine frequency control multi-stage speed control control terminal, frequency control to receive the control signal transmitted by the internal processing, the output of a specific frequency of the voltage to achieve the motor of the automatic filling machine frequency regulation. Frequency control abnormal output terminal feedback signal to the filling machine input, to realize the protection of liquid filling machine frequency control.
Input information analysis
This weighing and filling machine has five input signals, weighing and quantitative filling machine are start button, stop button, automatic, manual switching button, detection frequency input signal terminal. The start button is used to start the speed-regulated filling machine to start working, the stop button is used to end the speed-regulated filling machine, the automatic button is used to control the motor to run at an automatic speed, the manual button is used to manually control the motor speed, and the frequency signal input terminal is used to transfer the pulse signal from the photoelectric sensor into the liquid filling machine for logic processing.
Output information analysis
There are 6 output signals of the liquid filling machine, of which Y0, Y1 and Y2 are used to set the frequency control signals to control the low, medium, high and speed operation of the motor.Y3 is used to realize the over-fast alarm of the motor's speed, Y4 is used to realize the over-slow alarm of the motor's speed, and Y6 is used to start the motor's positive rotation operation.
Programming platform introduction
Programming software for Mitsubishi liquid filling equipment. Applicable to the whole series of programmable controllers such as Q, QnU, QS, QnA, AnS, AnA, FX, and so on. Support ladder diagram, instruction table, SFC, ST and FB, Label language programming, network parameter setting, can be programmed on-line changes, monitoring and debugging, with off-site read and write liquid filling machine program function. Automatic filling equipment adopts GXdeveloper software as the programming platform.
Introduction of configuration software
Filling NET platform on a new generation of configuration software, fully compatible with Windows7 operation of weighing and filling machines. It has a series of advantages such as leading technology, stable performance, powerful functions, beautiful graphics, easy to learn and use, flexible architecture, easy to expand.
The weighing and filling machine is connected to the control by means of communication, and can read and write the information inside the control and present this information in a visualized way, such as graphics and animation, in order to facilitate the monitoring of the control process. Can also be issued directly to the control of the instructions, set parameters to intervene in the control process, can be controlled by the control of the data arithmetic processing, the results will be returned to the control of the weighing and filling machine, to assist the control to complete complex functions. Can also be obtained from the control as well as their own data generated by the storage, reporting and other functions, thus extending the control of the filling device's ability and make up for the shortcomings of the filling machine. For example, the filling device can be used as an intermediate bridge to connect the weighing and filling machine and the enterprise management information of the factory, and to connect multiple control filling so that the weighing and filling machine can exchange data, share resources, coordinate and manage each other. Thus, the control structure is optimized in a wider scope to improve the efficiency of comprehensive automation.
Summarize
The main purpose of this design is to use frequency control motor rotation to drive the belt drive, and then the bottles to be filled are transmitted to the filling machine. Thus, the motor speed is controlled to achieve the coordination of bottle flow speed and filling speed, and improve the production efficiency. Frequency control multi-stage speed control terminal, accept the control signal transmitted by the internal processing, the output of a specific frequency voltage to achieve frequency control of the motor. Frequency control abnormal output feedback signal to the liquid filling machine input, to realize the protection of frequency control.