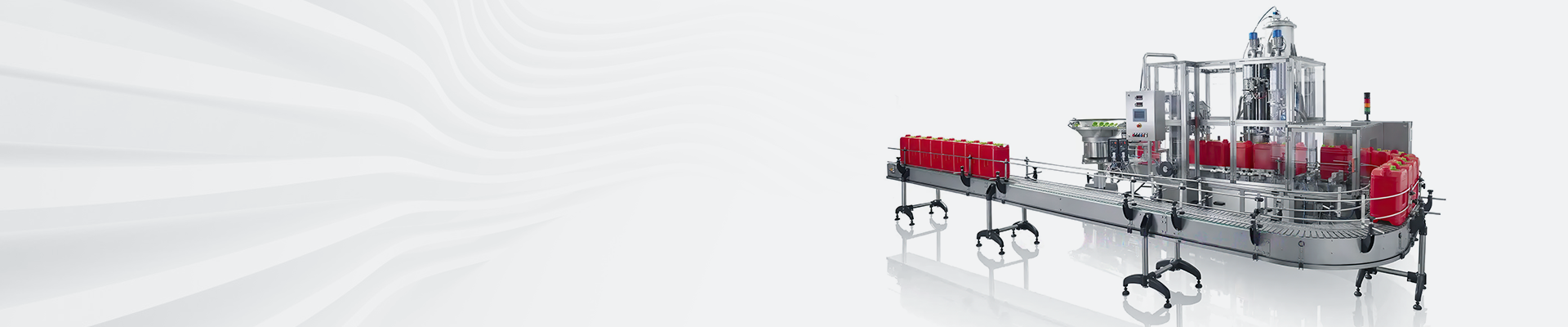
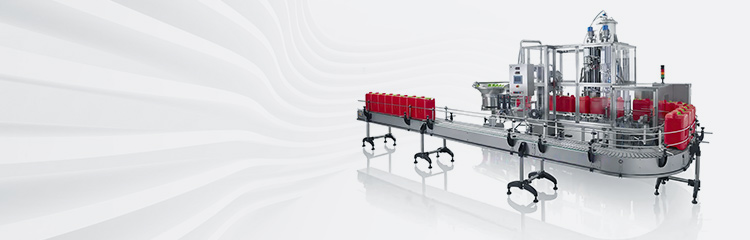

Summary:The batching system controls the on-site mixing and metering tank to set up a frequency converter, and realizes the interface with the Oracle batching database through ODBC access to complete data storage, data query, statistical reports, etc., thereby achieving effective cost control.
1 Introduction
In recent years, with the rapid development of PLC and automatic control technology, liquid materials one after another, many factories have been automated dosage transformation, in order to realize the bottom data acquisition and secondary system. One of the construction of a data acquisition monitoring dosage system, not only can faithfully reflect the situation of the liquid workshop paint production, but also to realize the automatic data acquisition by reactor, automatic recording of the reactor batch number, reaction tank number, dosage tank name, dosage time, dosage weight and other information. In this paper, the composition of the automatic dosing system, from the following aspects in detail.
2. Dosing hardware composition and functional requirements
2.1 Hardware composition
The PLC used in this dosage system is Siemens S7-300, equipped with a small DCS system, including digital output/digital input of two blocks, analog two blocks, Ethernet modules and power modules and CPU315 modules. The upper computer is an industrial control machine, which can realize the monitoring and management, and can transfer the collected data to the server automatically, and the lower level can finish the automatic batching calculation through PLC, and can realize the alarm control. S7-300 PLC is powerful and stable, which can meet the requirements of large-scale batching.
The automatic batching machine is composed of a set of S7-300 PLC, an industrial control machine (screen monitor) and a data acquisition server. The ICPC (monitor screen) is connected to the PLC using Ethernet and sends the data to the server in the workshop via the Ethernet bus.
The range of the electronic scale is 0~3000kg, and the output signal is 4~20MA. Due to the harsh environment at the site, a signal isolator is used to ensure the stability of the input signal to the PLC.
The inverter (Yaskawa) for controlling the motor on site, the speed is set to two levels, the first level adopts industrial frequency 50HZ-1400r/min, and the second level is set to 25HZ-700r/min. The PLC is used to control the speed of the second level.
2.2 Introduction to Functional Requirements
1) Data acquisition by reactor, record reactor batch number, hopper number, name, charging time, charging weight and other information.
2) Automatic accumulation of reactor batch number by pouring liquid signal and timely manual confirmation.
3) The database is stored in the dosage database, and the data can be counted and summarized according to the reactor, according to the day, according to the shift, according to the month and other requirements.
4) In the collection of a reaction tank, record the liquid time, feeding time and other information and generate reports.
3. The realization of dosage software function
3.1 PLC programming dosage software
(1) The dosage software adopts Siemens own programming software (STEP7V5.2) for programming, in the whole PLC program through the organization of the block OB1, function block FB1, function FC10, data block DB10, etc. to achieve the purpose of feeding control and data recording.
(2) In order to smoothly realize data acquisition, the main methods used are:
By controlling the contactor of the motor of the on-site stirring metering tank to determine which metering tank is currently being fed;
Judging whether the reactor is being refueled by controlling the travel switch of the on-site reactor;
Calculating and recording the addition data by the change in data;
Accurately record the weight of each tank addition by adding, subtracting, multiplying and dividing with the S7-300 PLC internal function block FC10;
Through the S7-300PLC internal function block FC10 operation, and then save the results of the operation in the S7-300PLC, by the DB10 data block of data and manual interface connection, and data transmission to the VB screen;
In order to ensure that each reactor liquid PLC within the data refreshment, S7-300PLC program to take power reactor pouring liquid end fast return signal, in order to clear the DB10 data block within the previous reactor data, the data of this reactor is saved to the weighing and dosage system database;
Recording of dosing time: S7-300PLC takes a digital signal at the moment of motor stirring of the on-site reactor, and records the time of starting dosing through the use of standard function blocks.
(3) Automatic dosage part: Suppose the operator sends 500 kg data to PLC in the man-machine screen, of which 50 kg is fine dosage (for empirical data):
When the data on the electronic scale <0 ~ (500-50) > kg, fast dosage is carried out (industrial frequency 50HZ). Set the frequency converter by means of a digital quantity.
Fine dosage (IF 25HZ) when the data on the electronic scale < (500-50) ~ 500 > kg. Set the inverter by digital quantity.
3.2 OPC; DCOM
(1) The server system software adopts OPCSERVER which comes with Siemens software, and downloads it into PLC through a series of hardware configurations.
(2) The client (industrial control machine) accesses the points in OPCSERVER through DCOM.
(3) OPC is an abbreviation for OLE for process control. The weighing and batching system is an open trial system interface standard based on DCOM technology. OPC is a bridge connecting fieldbus signals and monitoring system software, with the system as a common interface, it can be the field signals and upper monitoring, human-machine interface software to facilitate the chain up, but also to the dosage system and the PC's certain general development platform and application of dosage software platform chain up, such as VisualBasic, and the dosage system can be used for the dosage system, and the dosage system can be used for the dosage system. It can also link the batching system with some common development platforms of PC and application batching software platforms, such as VisualBasic, Delphi, VisualC++ and so on.
3.3 Upper computer system software
The upper computer system software is programmed in MicrosoftVisuaLBasic, which is widely used in the development of various dosage system software and has the following advantages:
(1) COM (Distributed Component Object Management) provides the most complete and efficient Windows base class library, which can provide the full range of support needed on the Widows automatic dosage system platform;
(2) is based on component design and visualization of the development environment;
(3) Simple language, easy to develop;
(4) provides extremely convenient controls for data query, can be accessed through ODBC to realize the interface with Oracle weighing and dosage system database;
(5) Access to points in the PLC through the initialization of the OPC interface.
4 dosage database and reports
The dosage database is the core of the whole management information system. The analysis and calculation of data are all done in the database, including data storage, data query, statistical reports and so on. Therefore the security and stability of the database is very important. This database adopts Oracle's database ----Oracle. The records of data are based on the rising edge signal, and the signal is saved to the database as soon as it arrives. Record time, quantity and some other information. And the report uses Oracle's own report development tool Report6i to make.
5, conclusion
OPC technology due to the fast data interaction ability, has gradually replaced Ifix, Intouch and other expensive configuration dosage software, become the mainstream of industrial dosage system applications.