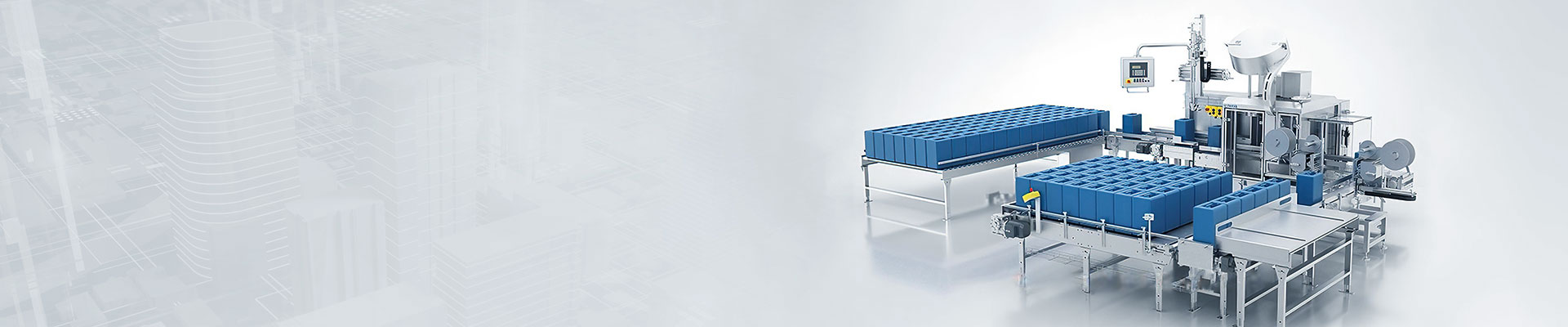
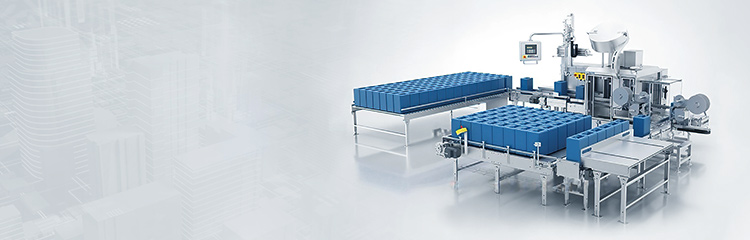
The weighing mixer achieves the requirement of batcher control precision and reduces the cost as much as possible through the dosage ratio of each raw material. According to the difference of each batch of materials and arbitrary change, optimize the calculation table input database using the development of visual man-machine interface, read the calculation data and display in the interface, visually create the database application program, make the application of the database more convenient and flexible, while supporting the application of network environment.

The feeding system adopts Siemens PLC to control the automatic operation of all the interlocking devices (start/stop, interlocking, position switching, etc.), and the upper computer is programmed by Siemens WINCC configuration software. The whole configuration screen is embedded in the overall Weighing system, which can be used for equipment start/stop operation, operation display, fault query record and maintenance, etc. The system is characterized by friendly interface, simple operation and reliable operation.
Weighing and mixing machine is suitable for conveying, measuring and batching of powdery and granular materials. Weighing and batching trolley, screw, belt as the material conveying tool, and at the same time for dynamic weighing and batching control of the complete set of automation equipment. According to the user's specific production process requirements, through the man-machine group configuration monitoring system and PLC program on the weight of the material loaded into the weighing and batching trolley, flow control, so as to achieve accurate measurement and batching. As a dynamic continuous measuring and batching automatic control device, it can also provide accurate measuring data and control means for production control and management of various industrial sites.
Components of a weighing mixer
Feeding part: the feeding part is the part that feeds the material from the silo to the weighing equipment, according to the different characteristics of the material, different feeding equipment is used, such as electromagnetic vibrating Feeder, screw feeder and so on.
Weighing section: The weighing section consists of the weighing module, standardized connectors, junction box and hopper weigher, which together with the weighing instrument carries out the weighing of the material and the detection of errors.
Discharge equipment: discharge equipment can be weighing equipment (reduction method) or discharge equipment (incremental method, zero method), usually consists of emptying valves, electromagnetic vibration feeder, screw feeder, electric (pneumatic) valves and so on.
Control system: the dosage control system consists of weighing instrument, upper industrial control machine, programmable controller and other control devices.
Calibration system: The weighing module should be regularly calibrated to ensure the accuracy of the system's dosage.
Main functions of the dosage control system
Monitoring function: detects and monitors parameters such as instantaneous flow rate, daily total, monthly total, and yearly total of the belt weighing process.
Screen display: the computer monitor can display the operating parameters of the control parameters in the dosage process, as well as display the real-time dosage curves and tables.
Printing management: dosage reports can be printed at any time for saving and querying.
Communication function: Bi-directional data and information can be exchanged between IPC and PLC, meters.
Data processing: The system can automatically process the collected signals and output them to the appropriate control volume.
Control function: automatically control the normal operation of the equipment according to the corresponding set value before operation, including PID adjustment.
Alarm function: the host in the screen mode and sound and light signal mode alarm various parameters abnormal or equipment status.
Automatic Dosage system is a set of complex automatic control system solutions, must be controlled according to the characteristics of the material and process requirements, as well as the specific reality of the enterprise, on-site production of comprehensive consideration, the design of the measurement and control of accurate, meet the requirements of the dosage system.