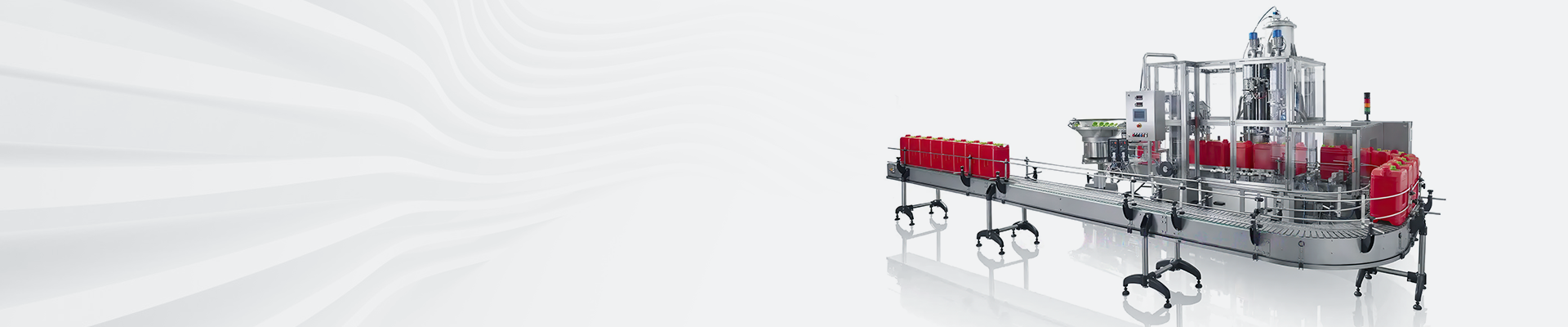
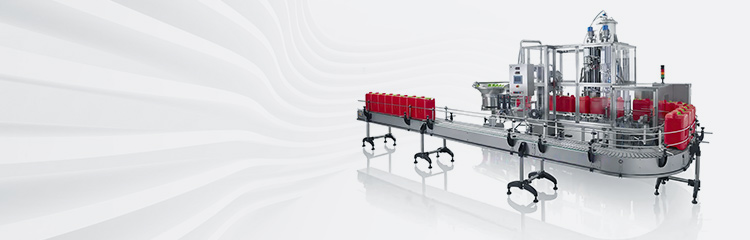

Summary:The automatic batching system uses configuration software, Mitsubishi PLC and weighing instruments. The host computer and PLC monitor and control various production data in real time. After the production is completed, the results are recorded and analyzed and compared in reports, curves, etc.
The application background and development trend of dosage are reviewed, and an automatic dosage optimization control system is designed for the shortcomings of the current dosage production enterprises, such as relatively backward technology level, low level of automation, low productivity, etc. The quantitative dosage is able to work in the three modes of full-automatic, remote manual and local manual. In terms of hardware design, the overall control structure combining industrial computer configuration software and PLC is adopted to realize the management and remote monitoring of mixing and dosage by the industrial computer, PLC completes the action control and related signal processing at the equipment level, and the connection and communication of mixing and dosage is realized through Ethernet and RS-485 bus; the positioning system of dosage truck is improved to realize the position coding scheme by using the designed positioning box to improve the positioning accuracy. The positioning system of the batching truck is improved, and the position coding scheme is realized by using the designed positioning box to improve the positioning accuracy. In software design, the design and development of the screen real-time monitoring and database management (SCADA) and other upper computer application software, can save the product formula, silo data, real-time data, etc., and can realize the historical data query, report printing, real-time data and status display, remote control and other functions, the two upper computer digital digging library can be effectively kept in synchronization. Designed the lower computer PLC main control program and communication, dosage accuracy control and dosage truck walking subroutine. Aiming at the dosage drop control problem prevailing in servo, a composite predictive control algorithm based on fuzzy adaptive combined with PID is adopted. The algorithm organically combines the characteristics of fuzzy adaptive control, wide-range fast adjustment and PID precise adjustment, and the fuzzy adaptive rule control combined with human experience is adopted when the deviation of the system is larger than a certain set value, and the PID control is adopted when the deviation of the system is smaller than the set value. PID control, the two inputs of the fuzzy controller are the expectation value and deviation of the speed-regulated batching system, and different air fall is predicted through different expectation values, and the effectiveness of the method is proved through simulation experiments; for the problem of working efficiency in mass production, the mathematical model of the system is established through the careful analysis of the working time sequence of the two batching trucks and the genetic algorithm is used for the search of the optimization, and the carefully designed Genetic operator, solved the optimal travel path of the two batching trucks required for the maximum working efficiency, and solved the optimization problem of the travel path of the batching trucks. The design research and development results, has been put into the actual production of indeterminate silica gel material, the operation results show that the system is stable and reliable, control accuracy and high production efficiency.
Second, the dosage architecture:
The speed-regulated batching consists of a computer as the human-machine interface of the whole weighing system. It is set as the master station to complete all the automated dosage parameter setting, process monitoring and data recording; another weighing touch control instrument is set as the slave station to take the master station as the backing, and it is in charge of the data setting and process monitoring of the quantitative dosage after the master station. The master station communicates directly with Siemens S7300 PLC system and mixing automatic touch control weighing instrument. Sealed junction box is used on site to prevent dust and moisture, which ensures reliable signal transmission. The weighing instrument adopts special industrial process touch control instrument, and the weighing control system communicates with the central control room through RS-485 bus, which can be controlled independently and also realize PLC on-line control. The signal detection of each valve position and unloader position adopts load cell, and the weighing module has the characteristics of non-contact, anti-interference, anti-dust and humidity resistance. The bin level adopts heavy hammer type material level meter, which can realize continuous bin level detection.
The automatic batching system has the functions of human-computer interaction, communication, display and storage, printing, etc. It also has data and graphic display, status monitoring, data input, information storage and other functional screens related to operation. The weighing system can realize real-time process data monitoring, simulation display of process flow, real-time data record access, system operator authority setting, process parameter setting, setting alarms for running process events and switching between manual and automatic control. The weighing and dosage system has on-site control instruments to display real-time flow, load, totalized value and temperature. Temperature indication is displayed by on-site temperature display instrument, pressure indication is displayed by on-site pressure display instrument and motor current is transmitted to centralized display in the control room by on-site display instrument. The frequency converter regulation is equipped with automatic switching switch, and communicates with the main control computer.
Third, the dosage software includes the following parts:
User management: including adding, deleting and modifying users.
Different users have different operation privileges, and the safety of the dosage system can be guaranteed by grading and partitioning management of users.
Scale management: in scale management, it mainly realizes adding, deleting and modifying scales. For a silica gel dosage system, the scale as a measuring tool, for product quality has a vital role. And the scale as a measuring tool, due to its own characteristics, there will be delay error. Users can set the parameters of the scale according to the difference of its physical characteristics, and its setting screen is as follows:
As you can see from the above, parameters including feeding delay, discharge time, discharge limit, closing delay, etc. can be set. This can be based on different scales with different physical characteristics, the implementation of different control programs to improve control accuracy.
Silo management: silo is a variety of raw materials in the batching before the temporary storage location, silo feeding control also has a great impact on the control accuracy. The management function of the silo is also very powerful, in the charging, the first fast charging, when the set range is reached, the discharge speed can be reduced, and also provides a drop control. If the above control has not reached the control accuracy, it can also be used to accurately dosage by pointing control.
Bin management also includes automatic calibration, which enables the dosage system to automatically adapt to changes in the dropout when the conditions change.
Parameter management: parameter management completes all other auxiliary management functions. Including site, customer information, construction parts, conveyor number, basic parameter setting, input switch monitoring, output switch monitoring, calibration scale and other functions.
Formula management: Silicone manufacturers can adjust the formula at any time according to production needs, including adding, deleting and modifying the formula. The software dosage provides a formula management tool without adding quantity limits.
Plan List: Plan List is to produce a set quantity of specific products according to the specified formula according to the production plan. You can specify the formula, customer, loading number, number of production cubes, number of mixing tanks, etc.
Real-time monitoring of the production process: real-time monitoring of the production screen through dynamic graphics, you can automatically or manually control the production process through the computer and keep abreast of the production dynamics.
Based on the software development of silicone frequency conversion can automatically manage the production process of the silicone mixing plant, and at the same time greatly improve the control accuracy, to ensure product quality.
Proportional regulation (feeding closed-loop control) principle of closed-loop control process is mainly through the disc feeder conveying materials for measurement, by the computer totalizer to receive weighing module signals and speed signals, processed and converted into the cumulative value and instantaneous flow rate, and the cumulative, instantaneous flow rate signals from the RS-485 port to the industrial control machine (host computer), and 4 ~ 20mA analog current signal to the AI regulator, the AI regulator will be the cumulative, instantaneous flow rate signal from the RS-485 port to industrial control machine (upper), and 4 ~ 20mA analog current signal to AI regulator. The AI regulator compares the signal with the internal set value and outputs a 420mA analog signal to the frequency converter, which then adjusts the rotational speed of the disk feeder, reducing the rotational speed of the disk feeder when the flow rate increases, and conversely increasing the rotational speed of the disk feeder to keep the flow rate of the material and the cumulative amount of the phase within the set range, thus obtaining a reliable quality of the product. Centralized monitoring, control and management of the industrial control machine.
Centralized monitoring, control and management of the industrial computer as the upper computer, through the RS485 bus interface with the computer totalizer and artificial intelligence regulator for two-way communication, and through the RS232 interface with the power control cabinet in the PLC for two-way communication, and the entire production process monitoring, according to the needs of the production process, the user can be in the industrial computer end of the set parameters, start and stop equipment, and the entire dosage system According to the needs of production process, users can set parameters, start and stop equipment, manage and control the whole batching system, and print reports. At the same time, there is a RS485 bidirectional communication interface in the industrial control machine for communication with other industrial control machines.
The decentralized control is detached from the industrial control machine, according to the requirements of the production process, directly input the parameters to the computer calculator and artificial intelligence regulator, start the buttons on the panel of the power control cabinet to carry out the automatic work of the system; it can also be taken directly to the manual way (on-site or remote operation) to make the system work.
High ReliabilityThe adoption of centralized control allows the system to work as follows: manual work; local work; automatic work with the support of intelligent weighing instruments after detaching from the industrial control machine; automatic work under the control of the upper computer and automatic work by the upper computer through the serial port to the lower computer to send in the parameters of the set formula to realize the automatic work, weighing terminals, thus greatly improving the reliability of the system.
Good product quality and production efficiency During the production process, according to the characteristics of the production process and process requirements, through the automatic batching system and automatic measuring equipment, it can ensure that each kind of material is operated under high precision (single machine precision up to 0.5%), which in turn ensures the precision of the mixture (system precision up to 1.0%), thus guaranteeing the quality of the product and increasing the production efficiency.
Strong processing capacity of the production process According to the needs of the production process, modify the corresponding parameters in the industrial control machine, you can meet the needs of different industries and mines, so that the system's ability to adapt to the production process has been greatly improved.