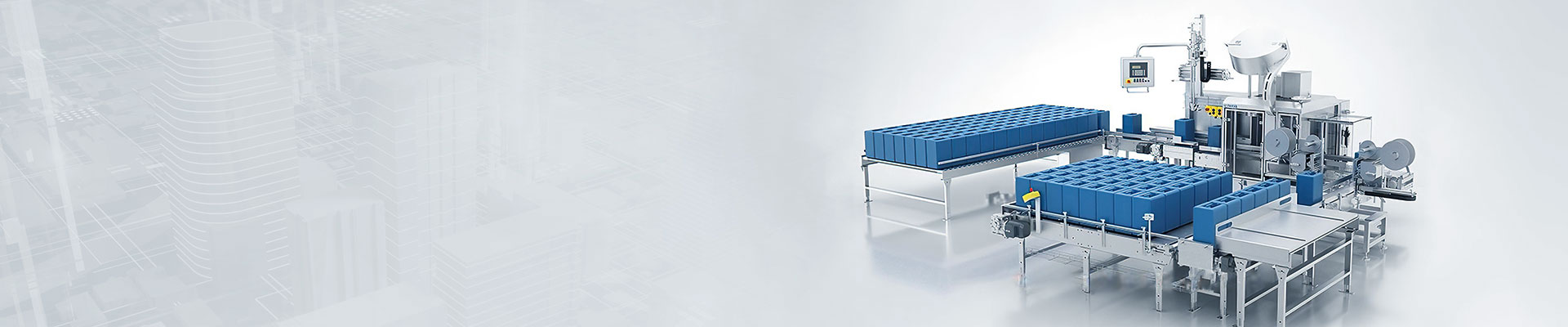
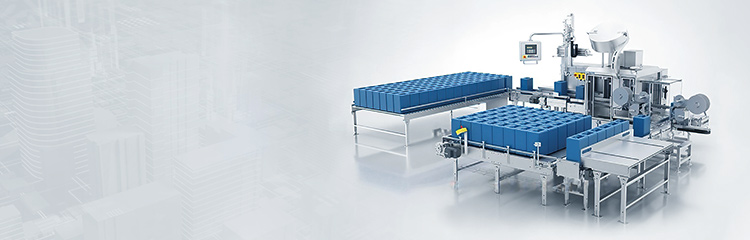
Bulk weigher can be divided into coarse and fine (big and small) feeding device, weighing part and discharging part. When the system works, the coarse and fine feeding device adds materials to the hopper (weighing part), and after stable weighing, the real weight of each scale is obtained and totalized. When the material leveler on the discharging part detects that the materials in the hopper have been discharged, the weighing controller discharges the materials in the hopper into the discharging hopper, and then completes a weighing cycle. Precise bulk material weigher adopts special weighing control software to feed the material according to the pre-set target weight, when the cumulative feeding weight reaches the pre-set weight value, the system automatically stops working and prompts the operator.

Bulk weigher can be divided into coarse and fine (big and small) feeding device, weighing part and discharging part. When the system works, the coarse and fine feeding devices add materials to the hopper (weighing part), and after stable weighing, the real weight of each scale is obtained and totalized. When the material leveler on the discharging part detects that the material in the hopper has been discharged, the weighing controller discharges the material in the hopper into the discharging hopper, and completes a weighing cycle. Precise bulk weigher adopts special weighing control software to feed materials according to the pre-set target weight. When the accumulated feeding weight reaches the pre-set weight value, the system automatically stops working and prompts the operator.
In the production process, batch feeding and continuous batch feeding metering equipment plays a crucial role. Among them, bulk weigher, as a common equipment, is widely used in various industries. Batch discharging refers to putting a certain amount of raw materials or products into the bulk scale for weighing according to the production needs to ensure the accuracy and stability of the production process. Continuous batch discharging, on the other hand, is the process of continuously discharging raw materials or products according to set parameters during uninterrupted production to ensure uninterrupted production.
Bulk weigher can accurately control the quantity of each discharging through precise weighing technology to ensure the quality and efficiency of production. It can not only improve production efficiency and reduce the uncertainty of manual feeding, but also save time and cost. Bulk weigher has a wide range of applications and is suitable for the production process in different industries such as chemical, food, pharmaceutical and so on.
Through continuous innovation and optimization, bulk scales are not only improved in metering accuracy, but also become more convenient and intelligent in operation and maintenance. In future production, batch discharging and continuous batch discharging metering equipment will continue to play a key role in helping various industries to achieve a more efficient and stable production process.
Process flow:
1. material loading: the material to be weighed is loaded into the hopper and the initial weight of the hopper is recorded.
2. Stabilization Waiting: Wait for the weighing signal to be issued after the material in the hopper is stabilized. 3. Weighing operation: after receiving the weighing signal, the weighing controller will release the material filled in the hopper and start weighing.
4. Weight Measurement: The weighing module measures the weight of the material in the hopper and transmits the data to the weighing controller.
5. Output result: the weighing instrument converts the measurement result into material weight and outputs it.
Technical parameters:
The technical parameters of bulk weigher usually include weighing range, weighing accuracy, weighing speed, etc. The specific parameters need to be selected according to the application scenario.
1. weighing range: according to different industries, applications and material characteristics, the weighing range is usually tens of grams to several tons.
2. weighing accuracy: different application scenarios require different accuracy, generally weighing accuracy between 0.2%-1%.
3. weighing speed: bulk weigher weighing speed is also an important indicator of user demand, generally within 3-6 times / minute.