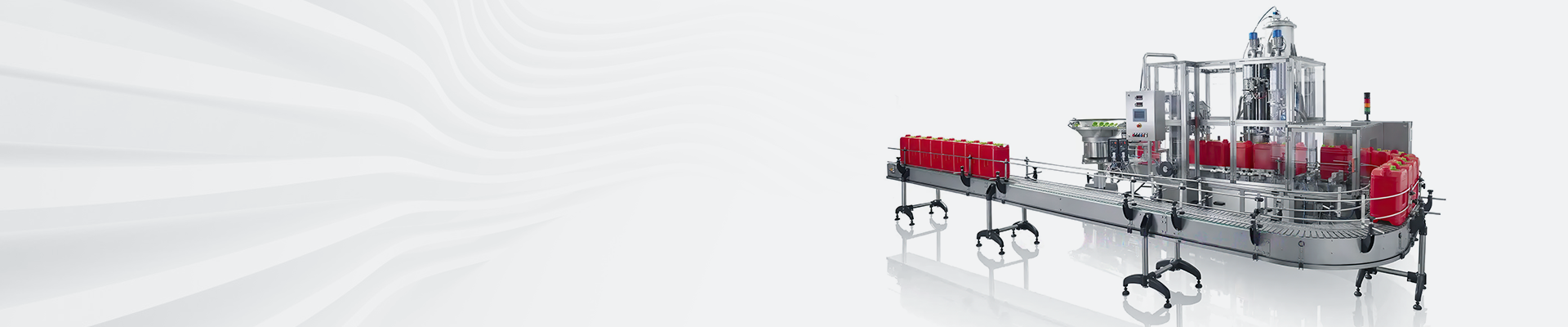
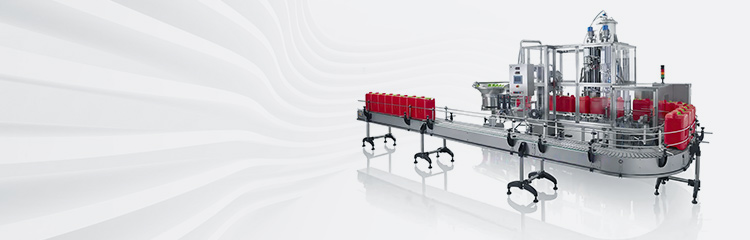

Summary:The hopper scale controls the cylinder to open the feeding door through the solenoid valve, and the materials in the storage hopper enter the weighing hopper through the outlet.When the amount of material in the weighing hopper reaches the requirement, the control system controls the cylinder to close the feeding door to complete the feeding process.
With the rapid development of industrial process automation, packaging, storage and transportation put forward higher requirements. Also for bulk material measurement of automatic hopper scale weighing speed and electronic weighing accuracy put forward higher requirements. Automatic hopper scale weighing speed and weighing accuracy depends on the feeding speed and feeding accuracy of its feeding device.
There are mainly two kinds of automatic hopper scales, electronic scales and non-continuous totalizing scales, which are designed to obtain the target value of a single weighing, and non-continuous totalizing scales, which are designed to obtain the target value of the accumulation of several weighings. Structurally speaking, and non-continuous totalizing scales have a feeding device, a weighing module and an unloading device, while there is also a bagging and packaging device. With the development of process automation in the logistics industry, automatic hopper scales are increasingly being used in other industries, thus placing higher demands on the weighing speed and accuracy of automatic hopper scales.
The weighing speed and accuracy of automatic hopper scales depend on the feeding speed and accuracy of the feeding device. The automatic hopper scales used in the chemical industry (material characteristics of corn as an example) are analyzed as follows.
1 Working principle of feeding device
Automatic hopper scale feeding device (including hopper), when the system requires feeding, the control system through the solenoid valve control cylinder 6 to open the feeding door 4, the material in the storage hopper 1 through the exit port 5 into the weighing hopper. When the amount of material in the weighing hopper to meet the requirements of the control system and control the cylinder to close the feeding door to complete the feeding process.
2 feeding device design
2.1 Storage hopper
The bottom of the storage hopper is generally large on the bottom of the small inverted cone, the material from the storage silo down discharge, due to the role of the material's self-weight, constantly overcome the internal and external frictional resistance to downward mobility, the material in the process of descending, the particles continue to move, extrusion and regrouping, to adapt to the cross-section of the author of the unit: contraction of the changes, and want to close to the mouth of the particles of the extrusion of friction intensified when the resistance is greater than the weight of the formation of the shed material Or bridging and other phenomena, thus affecting the normal feeding. Therefore, in the design of the hopper should be given full consideration to the characteristics of the material to prevent shed material.
When the material level in the storage hopper is reduced, the upper layer of material is reduced, the lower layer of material particles between the pressure is reduced, the internal and external friction between the material particles is also reduced, the flow rate of the material out of the mouth is gradually accelerated. When the material is about to be emptied, the flow rate increases sharply, which will lead to overweighing and even overflow from the weighing hopper. Therefore, in order to ensure 5E accurate weighing, should be installed in the storage hopper on the low level meter, the level of material below the meter should be greater than 2 times the maximum weighing capacity.
2.2 Emergency door
In the storage hopper should be configured below the emergency gate, especially when the storage hopper is quite large, such as some grain storage silos can reach more than 40, this time must be configured with emergency gate. When the hopper scale or its subsequent equipment failure, should immediately cut off the material with the emergency gate. So that when there are maintenance personnel in the hopper scale or other equipment for maintenance, there will be no uninformed personnel or other circumstances of the equipment to start, thus ensuring the safety of maintenance personnel.
2.3 Shell
In the hopper scale outside the increase in shell to prevent the chemical dust flying, and attached to a dust-absorbing device for dust absorption, dust-absorbing device generates a negative pressure is generally in the 500Pa or so, when the negative pressure is too low, it can not play a good effect of dust absorption, and when the negative pressure is too large, it will have an impact on the weighing, and even the material will be sucked away.
2.4 Feed gate
For the chemical industry for the more appropriate feeding door should be fan-shaped feeding door. In the switch feed door, the implementation of the cylinder only need to overcome the friction of the material in the fan feed door can be, run quickly and reliably, can be better to complete the feeding process, and the fan feed door does not squeeze the material, there is no shutting off the situation of not tight and crushed materials.
2.5 Feeding mouth
The size of the feed opening should be able to ensure that the hopper scale in the rated flow rate required for the work of the feeding rate, in this calculation and non-continuous cumulative scale of the size of the discharge opening.
1) Calculation of the discharge opening for non-continuous totalizing scales
Since non-continuous totalizing scales are generally used for weighing large quantities of bulk materials, in order to meet their accuracy and flow requirements, the hoppers are generally designed to be relatively large, so that the flow rate Q is always the maximum weighing capacity of the hopper, for example, and the time required to complete a weighing cycle is Ding = 3600/(UW0Q/Max), the cycle time of a weighing cycle is T. Considering that the feeding and discharging times of the hopper are the same, a discontinuous totalizer can be used in 1/3 of the time, i.e. 7/3, to complete the feeding. Available 1/3 of the time i.e. 7/3 to complete the feeding, then the flow rate at the discharge port.
Calculation of the discharge port of the fixed packaging scales, generally installed in the material storage bin below or at the end of the industrial production line, used to quantitative measurement of bulk materials and packaging, distribution, with the continuous development of the degree of automation in the logistics industry, the requirements of the packaging speed is also increasing, for the 25-100kg bag requirements have reached 600 bags / h, or even higher. Now to 50kg packaging speed of 600 bags / h to calculate the size of the outlet. The time required to complete the measurement of 1 bag action time is very short, every detail of the time spent can affect the whole process. In addition to the amount of thy, stabilization, unloading and other time required, the feeding time can only account for the entire weighing time of 1 / 3, that is, about 2s, which also removes the small feeding time, about 0, 5% of the large feeding time of about L5s, from the solenoid valve action to the piston to reach the end of the cylinder stroke time required (Calculation conditions: cylinder specifications & 50x100, receiver caliber 1/4, gas pressure 0, 5MPa, piping length I.). 5MPa, piping length Im, the installation direction of the cylinder is horizontal, the cylinder loading rate of 30% according to the cylinder operating characteristics.
2) Adjustment of feeding port size
In the user site sometimes need to a variety of materials for thy amount, due to the flow of various materials is different, should be in the feed hopper to design a device to regulate the size of the feed port (Figure 3 through the adjusting bolts to promote the inner baffle plate rotation, can be made to feed the mouth of the adjustment between 60% -100%.
2.6 Design of feeding cylinder
When selecting the feeding cylinder, attention should be paid to the load factor of 30% to 40%, generally not more than 50%, the load factor is too large, which will seriously affect the operating speed, especially for electronic scales should be fully considered.
The quantitative feeding of the feeding device (i.e. large and small feeding) can be accomplished in the following ways.
1) Double Cylinder Linkage
When opening the door, both cylinders act at the same time to increase the force when opening the door, and the small feeding cylinder position can be adjusted to adjust the size of the small feeding volume to adapt to different materials. When small feeding is required, the big feeding cylinder retracts and forms a lever with the small feeding cylinder, and the feeding door stops in the small feeding state. After completing the small feeding, double cylinders retract at the same time to complete the feeding process.
2) Double-stroke cylinder
Double-stroke cylinder feeding when the control position of the feed gate is accurate and reliable, high repeatability, especially for single materials, if the replacement of materials, due to the characteristics of the material can not be adjusted to the flow, can not achieve the appropriate feeding speed and feeding accuracy.
3) Single cylinder equipped with control elements
Installed in the middle of the cylinder running a switch control element to detect its position, when the cylinder running to the middle of the need [i.e., small feeding position], touch the switch element, send a signal to control the solenoid valve so that the cylinder to stop running, small feeding process. The structure is characterized by simple structure, easy to adjust. However, due to the instability of the air pressure, the control accuracy is not very high, suitable for large weighing bucket feeding control.
3 Debugging of feeding device
Hopper scales in the formal use of the actual material before the need to feed the device debugging.
1) First of all, adjust the large feeding
debugging, set by the program does not run a small feeding action, but only a large feeding operation. By changing the size of the advance amount of debugging for many times, so that the feeding amount of error does not exceed the earth 0.5kg (50kg electronic scale, for example).
2) Small feeding adjustment
Enter the normal weighing state, by changing the size of the small feeding advance for many debugging, so that its final feeding error to meet the requirements.
4 Conclusion
In this paper, the design of automatic hopper scale feeding device of various influencing factors to ensure that the feeding device feeding speed and feeding accuracy, some of the data is based on the results of the test quoted directly, without giving the formula. According to this design idea designed automatic hopper scale has been widely used in logistics process control, and achieved certain social benefits.