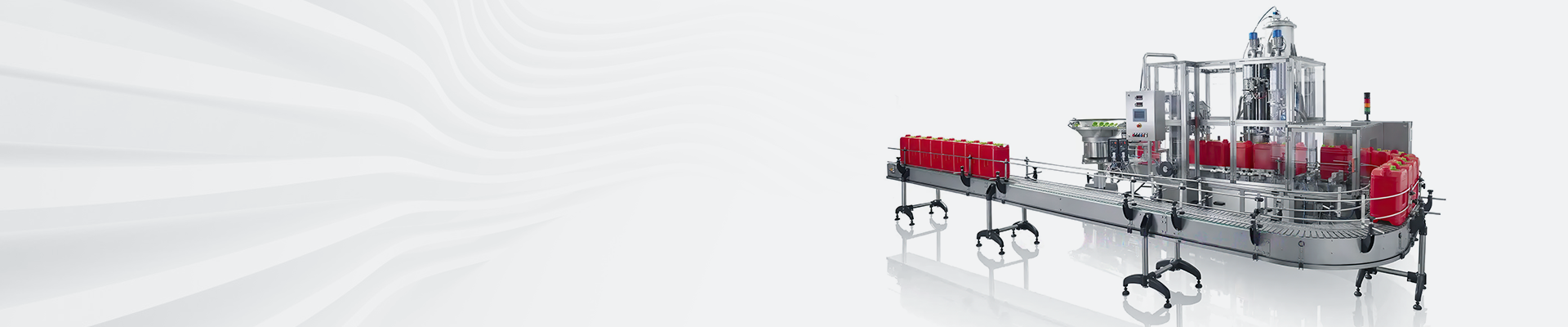
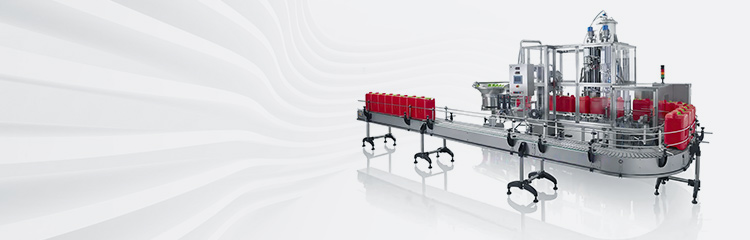


Summary:Application of variable frequency speed regulation technology in calcium carbide smelting feeding system.Using variable frequency speed regulation for batching, it has advantages that other adjustment methods cannot match in terms of frequency range, dynamic response, slip compensation, and work efficiency.
China's PVC production capacity has jumped to the world's first, China has become a real chlor-alkali country, the rapid development of the PVC industry has driven the development of the raw material calcium carbide industry. China's calcium carbide industry as a basic industry has a long history, in recent years China has become the world's largest producer of calcium carbide, according to the National Bureau of Statistics data show that in 1990 China's calcium carbide production of 2.28 million tons, to 2008 the domestic production of calcium carbide 13,612,100 tons, is 5.9 times the 1990. Mainly due to the international oil prices continue to rise, the petroleum method of PVC production sharp contraction of the formation. Calcium carbide PVC is the main downstream consumption industry of calcium carbide, accounting for more than 70% of the total consumption.
The main raw materials for calcium carbide production of coke (or blue carbon), lime, electricity, electrode paste. National Development and Reform Commission under the calcium carbide furnace energy consumption access standards, the project's comprehensive energy consumption standards per ton of calcium carbide power consumption of 3250 degrees (the previous standard for prospective enterprises is 3400kw.h/t). The accurate measurement of raw materials is the key means to improve the furnace condition and reduce the bottom energy consumption. The traditional calcium carbide raw material proportioning process mainly relies on the workers in the poor working environment by working experience to regulate, there are the following aspects of the problem:
① uneven mixing, can not be adjusted at the right time proportioning, low production efficiency.
② due to the lack of measuring equipment, human influence factors more material can not be well controlled, waste phenomenon is serious, production costs greatly increased, defective products.
③ Due to the material dust pollution is more serious, the labor environment is poor, seriously affecting the health of workers.
In 2010, the national implementation of sustainable development strategy and energy saving and emission reduction to promote the development of practical activities, the degree of automation of industrial processes is increasingly high, people's awareness of environmental protection and the national implementation of the low-carbon economy strategy, the application of mature technology is an important issue facing the high-energy-consuming industries. The annual output of 400,000t calcium carbide plant of Yili Chemical Company, in which Shendong Electric Power Company participates, plays an important role in the promotion and application of the nine process technologies optimized by design, and the frequency conversion technology plays an important role with its excellent performance and mature technical performance in the key processes. Frequency conversion speed control technology in large-scale closed calcium carbide furnace (30,000kVA) feeding system.
1 The birth of large-scale closed calcium carbide furnace is the achievement of China's chemical industry development of localization research, is the national industrial scientific development of the practice of research results. Through nearly 30 years of technology introduction, absorption, application of furnace type has been changed from open type to closed type, the capacity of the access requirements greater than 27000kVA. new closed furnace of a number of process technology indicators to become the project review and approval of the condition of the person indicators.
Large-scale closed calcium carbide furnace design due to the large amount of charging, furnace cover manually operated door closed. Furnace micro-negative pressure operation, remote centralized temperature regulation, feeding into the top of the feeding tube charging. Charging system design by the disc feeder, more than 9 down tube, belt conveyor, frequency conversion speed mixing and charging device and other components. The main function of frequency conversion speed control:
① Realize mixing according to the set ratio;
② according to the furnace temperature and production volume of timely charging, to keep the furnace and the downstream pipe full of material.
Large-scale closed calcium carbide furnace has high requirements for raw materials, the moisture of coke <1%, containing powder (less than 5mm) <3%, limestone calcined requires not oxidized; coke moisture drying to maintain coke does not inhale atmospheric moisture. All are required to be used in a short period of time, from coke moisture drying kiln, gas-fired lime kiln to the top of the calcium carbide furnace charging to achieve continuous operation, coke and lime charging at higher temperatures, it must be realized mechanical charging. Frequency control system requires interlocking with lime and coke charging system. Large-scale closed calcium carbide furnace design review, in accordance with industry access conditions require a comprehensive power consumption of 3250 per ton of finished calcium carbide, calcium carbide furnace electrode burning to realize the side of the production with the burning, in order to eliminate the dry burning of energy consumption, so the frequency feeding system is required to come out of the furnace and with the burning of electrodes with a strong reliability.
2 feeding, mixing system process and the main parameters of the Salazar power plant design and construction of eight 30,000kVA closed furnace, feeding system for a single control. 30,000kVA large-scale closed calcium carbide furnace feeding system is mainly composed of industrial control computers, dosage control system, the secondary instrumentation (containing measuring instruments and expert regulators), frequency converters, on-site operating panels, speed control belt scales and disc feeders, etc. . Production of calcium carbide material is mainly from the lime, coke 2 kinds of materials for the proportion and become, 2 kinds of materials have a silo, the silo materials were through the respective disc feeder, and by the electronic dosage of belt scales measured input into the total conveyor belt, and then by the total conveyor belt will be mixed materials were sent to the 11 downstream of the material pipe.
2.1 Main parameters
2.1.1 Disc feeder.
Motor type guide is YSP160Mz-4, power density 1lkW, speed 1140rpm, AC380V, 50Hz.
2.1.2 Electronic dosing belt scale.
Belt width: 1000mm; speed: 0.5m/s; production capacity: 60t/h (1 set).
2.2 Process control of the system
Frequency conversion speed batching control process is mainly through the electronic batching belt scale on the disc feeder conveying coke and lime measurement, by controlling the weighing instrument to receive weighing signals and speed signals, processed and converted into the cumulative value and instantaneous flow rate, and the cumulative value, instantaneous flow rate signal from the RS-485 day transmission to the industrial control machine (host computer) to the 4mA ~ 20mA analog current signal transmission to the PID Regulator, the regulator will be the signal and the internal set value comparison operation, 4mA ~ 20mA analog signal to the frequency converter, and then by the frequency converter to adjust the rotational speed of the disc feeder, when the flow rate increases, reduce the rotational speed of the disc feeder, and vice versa to increase the rotational speed of the disc feeder, so as to make the flow rate of the two kinds of materials and the stage of the cumulative amount of the flow rate is maintained in the set range, and thus obtain a reliable Product quality.
The parameters and operation process of the batching machine can be set and monitored by the industrial control machine, and the value of the PID regulator can be modified manually, which is convenient to operate and reliable to control, and the whole system realizes a high degree of automation, forming 8 closed-loop control systems which are both relatively independent and interconnected.
The change of 2 kinds of material quantity is mainly determined by the rotational speed of the disk feeder, that is, the final control object of the system is the disk feeder. The rotational speed of the disk feeder is controlled by the frequency converter, and the size of its capacity is directly related to the selection of specifications of the frequency converter.
2.3 Selection of frequency converter model
The motor model of the disk feeder selected for design is YSP160Mz-4, with a power of 11kW and a rated current of 25A. Since the system has been in continuous operation during work, the rated output current of the frequency converter should be greater than the rated current of the motor, which is 1.05~1.1 times. In normal operation, the uniformity of the materials on the site is better, the frequency of motor acceleration and deceleration is relatively low, and the time of acceleration and deceleration is relatively short, although the maximum output torque of the frequency converter is determined by the maximum output current of the frequency converter, according to the calculation results and the design recommendation of Dalian Heavy Industry, we choose the frequency converter of Chuangjie Company, and its model specification is: AT products.
2.4 Motor power supply
The motor power supply adopts double power supply: that is, inverter power supply and bypass power supply, when the inverter fails or when it is cut off artificially, the motor automatically switches to the bypass mode, and according to the actual need, the reference current size is adjusted to the disc feeder to run at a constant speed, to ensure that the system operates uninterruptedly, and to ensure that the control accuracy is within a certain range. Frequency converter in large-scale calcium carbide furnace in the use of precautions 3 due to 30000kVA calcium carbide furnace technology is now mature technology in the country, batching control system site working environment has improved greatly. However, due to the large output, transport material system maintenance and maintenance frequently, once the selection is incorrect or unreasonable settings, will easily cause inverter misoperation and failure, can not achieve the expected operating results.
3.1 Electromagnetic interference outside the frequency converter
Large-scale closed calcium carbide furnace heating mainly by three low-voltage, high-current electrodes to complete the electrode burning and normal production often produces arc discharge phenomenon, the formation of a strong source of interference, through the radiation or power line invasion of the inverter internal circuit often occurs inaccurate operation. So in the frequency converter external electromagnetic, noise suppression measures, the main measures are: ① in the frequency converter input installation of noise filters, to avoid interference caused by the power line; ② will be the frequency converter grounding terminal previously through the power grounding into a separate ground; ③ in the control cabinet contactor control coil plus RC anti-impact absorption device, the control cabinet.
3.2 Installation environment requirements of inverter
Because of the calcium carbide furnace system with the type of materials are mainly hot coke, lime 2 kinds. From the coke drying kiln out of the hot coke and gas-fired lime kiln out of the hot lime in the feeding process will produce a lot of powder, dust removal is not good so that the frequency converter accumulates more dust, the temperature rise in the inverter cabinet faster, the semiconductor devices within the frequency converter is easy to be damaged, the implementation of this, we use two sets of frequency converter cabinets, the cabinet is divided into the upper and lower levels of frequency converter layout, and between the upper and lower frequency converter to add a partition board, while in the upper rear door of the control cabinet Installation of axial fan external ventilation cylinder, the lower part of the front door to install the exit filter to avoid dust pollution.
3.3 Frequency converter interference with the outside world
At present, the frequency converter almost all use PWM control mode, such a form of pulse modulation makes the frequency converter operation in the power supply side of the high harmonic currents, and lead to voltage waveform distortion, the power system has a serious impact, especially the symmetrical heavy signal guide and speed signal interference is particularly serious, affecting the measurement accuracy, for this reason, we isolate the signal processing, and control instrumentation power supply to deal with, so as to Ensure that the system operates with high precision.
4 Conclusion
In conclusion, through the use of large-scale closed calcium carbide furnace for several years to see:
① good reliability of the system, to solve the previous user site due to the shed material caused by poor logistics and jamming material so that the feeder can not work properly, resulting in a pile of material phenomenon, etc.;
② high precision of the system, stand-alone operation, the accuracy is better than 0.5%, control accuracy is better than 1%;
③ The energy-saving effect is remarkable, which greatly improves the furnace condition and reduces the power consumption by 150kwH/t (calcium carbide);
④ Low level of environmental pollution. Since the system has been put into production, it not only ensures the quality and output of products, but also overcomes the problem of environmental pollution, creating good economic benefits for the enterprise.