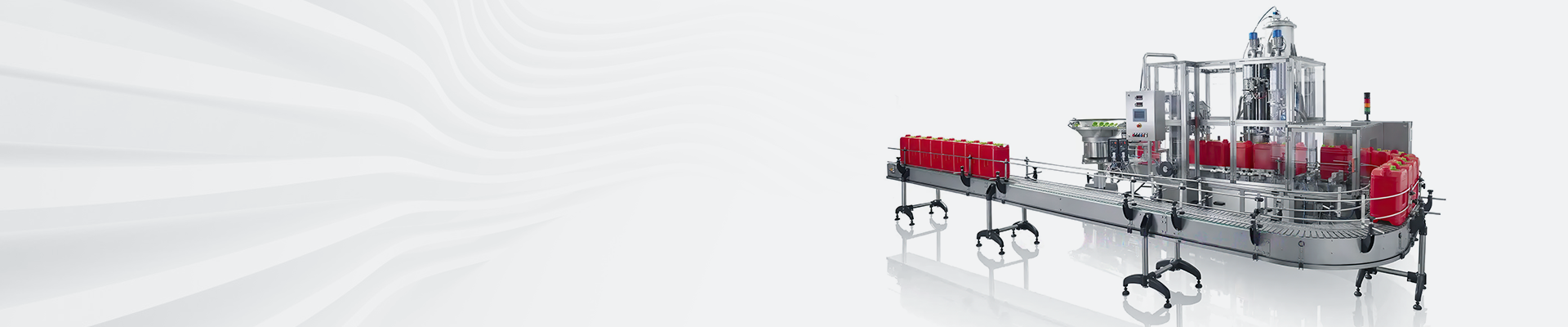
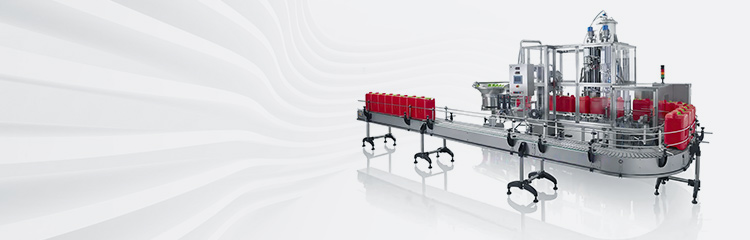

Summary:This article introduces the weighing link and weighing technology of polyethylene weighing and batching control system, as well as the application of PLC in polyethylene quantitative weighing and automatic batching control system.The weighing control system based on OMRONCPM2APLC focuses on the weighing principle and its process, and gives a detailed explanation of the software program design part.
1 Citation
In recent years, the competition of petrochemical products on the international market is becoming increasingly fierce. For the complexity of the production process of petrochemical products, additives, strict requirements of the ratio, variety, poor interchangeability of the characteristics of the development and development of computer and PLC integrated weighing control system is necessary.
Polyethylene has good processing properties, due to the polyethylene itself is very easy to generate static electricity, plus the required dosage of powdered materials, dosage site dust is large, on the health of workers is extremely harmful, the dosage production using PLC control system can save raw materials, improve the dosage speed, and thus improve production efficiency, while also reducing the labor intensity of workers. Batching operation is complex, frequent, and there are more executive elements, the use of relay control logic will inevitably require a large number of intermediate relays, and these intermediate relays in the case of PLC control, it can be programmed to its internal auxiliary relays later replaced. General PLC has hundreds of points of internal auxiliary relays or even more, and there are a variety of specialized internal appliances, only the PLC programming.
2 Electronic Weighing
Polyethylene batching line control in the application of PLC, mainly to control the weighing, sealing, push down the transmission, inspection, palletizing and other parts of the device. Among them, weighing is an important part, the accuracy of its dosage amount and the speed of dosage, which directly affects the economic benefits of manufacturers and the interests of consumers, the traditional mechanical lever weighing method can cause large mechanical errors.
In the polyethylene quantitative automatic dosage system, weighing technology using load cell instead of the traditional mechanical program control, and at the same time the application of programmable logic controller (PLC) to achieve high precision quantitative weighing of polyethylene, so that the designed system will be a simple structure, easy to modify the program and high reliability.
2.1 Composition of weighing section
The electronic scale is mainly composed of two parts: the scale body and the electronic weighing control system. The scale part of the storage bin by the storage bin, feeding and loading, hopper weighing, bag holders and other components. The weighing and batching system is composed of weighing sensors, weighing control instruments and control actuators, of which the weighing module is a very important component.
At present, in the field of weighing technology is widely used in resistance strain load cell, divided into metal resistance strain type and semiconductor strain type two kinds. The former has the advantages of high precision, small temperature effect, good linearity and repeatability, but the price is high, and the output sensitivity is low; the latter performance is the opposite of the former, in terms of precision and temperature characteristics of the former is one order of magnitude worse, and the output sensitivity is one order of magnitude higher than the former, and the price is half of the former. According to the actual control requirements and working environment, the choice of semiconductor strain gauge sensor, the load cell for the S-type structure, pulling the two pressure. In this system selected two weighing sensors, the use of series connection method for the realization of accurate measurement, in addition to switching control, but also need some sensors and some solenoid valve cylinders and so on.
The main functions of the system are:
(1) To realize automatic control of bagging weight, its set value and actual value can be set by the programmer;
(2) Detecting and correcting the tare weight of the weighing hopper after each discharge;
(3) Automatic compensation for weighing error;
(4) Fault detection and alarm.
2.2 Weighing process
The feeding device of the filling machine supplies materials to the hopper scale with two kinds of flow rates. The weighing module converts the weight signal into electrical signal and transmits it to the weighing control instrument. The weighing control instrument measures the weight value and programmatically controls the entire weighing process, constituting an automatic weighing control system.
The switching input signals in the system include start button, stop button, bucket door status, bag clamping and other detection signals; the switching output signals include coarse and fine feeding solenoid valves, discharging solenoid valves, bag clamps and other control signals and some display and alarm output signals. The digital channel receives the sensor weight input signal, in which the weighing hopper door closes and the bag clamping detection with a proximity switch, the buffer door, weighing hopper door and bag clamping by the solenoid valve to drive the cylinder to control.
Ideally, the big feed and the small feed work together to feed 95% of the rated weight value in a short period of time. Then the big feed stops, the small feed and then complete the rated weight value of 5% to 10% of the feed volume, and occupy a longer time. The actual production of these two sections of the weight and time parameters should be adjusted according to the specific circumstances in order to achieve the best state.
3 error and adjustment methods
In the measurement department to check the electronic scale to its static accuracy and dynamic accuracy are assessed. In actual production, the measurement accuracy of the product mainly depends on the dynamic accuracy. From the theoretical and practical debugging and production analysis, dynamic accuracy errors mainly from the internal system and external environment. Internal system errors mainly include:
① load cell error;
② weighing instrument error:
③ control element and execution element hysteresis error.
The external environment error mainly includes:
①) The uniformity of materials, whether it is lumped or not; whether the discharging material is uniform or not:
②) Whether the equipment is affected by external electrical or vibration interference.
4 Software program design
When the two weighing controllers of each batching line are set up, and after any one electronic scale (such as A scale) is started to run. At this time X0, X1 automatically send a signal, A scale of the large and small valves open. The big valve in the last pre-feeding into the hopper, A scale fast and slow feeding spiral start feeding, when the fast feeding (slow feeding at the same time) weight reaches the set value, fast feeding signal X0 stops, A scale big valve closed. Fast dosing spiral delay work 2S after stopping, this time the fast dosing material falls on the big valve to do the next pre-feeding amount to improve the dosing speed. The small dosing screw continues to add material to the actual value. At the same time, the small valve feeding screw stops at the same time. a scale from the judgment of the weight qualified to send X2 discharge signal to the PLC, and then by the photoelectric switch to determine whether the dosage bag box bag, if not, then send an alarm message to take the bag cylinder drive suction cup up and down swing, automatically grab the bag, the bag will be placed in the toothed belt drive on the trailer, transferred to the positioning platform. When the dosage bag mouth to the upper and lower two suction cups between the cylinder drive suction cups sucking the bag mouth and open, the cylinder drive to set the bag into the storage hopper. PLC after judging the bag clip has been closed. The PLC determines that the bag clamp is closed, and then puts the bag on the hopper. Scale does not discharge. After a delay of 3S send a signal to open the scale door discharge. A delay of 1S closes the weighing door for the next loading. Electronic scale through the weight sensor to determine the weighing hopper has been emptied and within the allowable error, again issued X0, X1 signal to restart the charging process. Otherwise, the error display stops the filling process. The bag clamp is opened after a delay time determined by the special data memory of the PLC (the size of which can be adjusted at will by the potentiometer on the PLC). After the sewing machine sews the bag, puts the bag to the belt conveyor, B scale also works the same as A scale. This two scales and a PLC to form a set of weighing and dosage system can be in the case of manual bag continuous work, you can improve productivity. In order to prevent the two scales discharge at the same time in the program should be added interlock function.
Conclusion
Weighing and dosage is an important process of automated production system, this weighing and dosage device realized by PLC controller system has the value of promotion in automated production line, which can be widely promoted to the weighing and dosage of many kinds of bulk particles, such as candy, etc. At the same time, the device also helps to realize the automation of the production, intellectualization and equipment miniaturization.