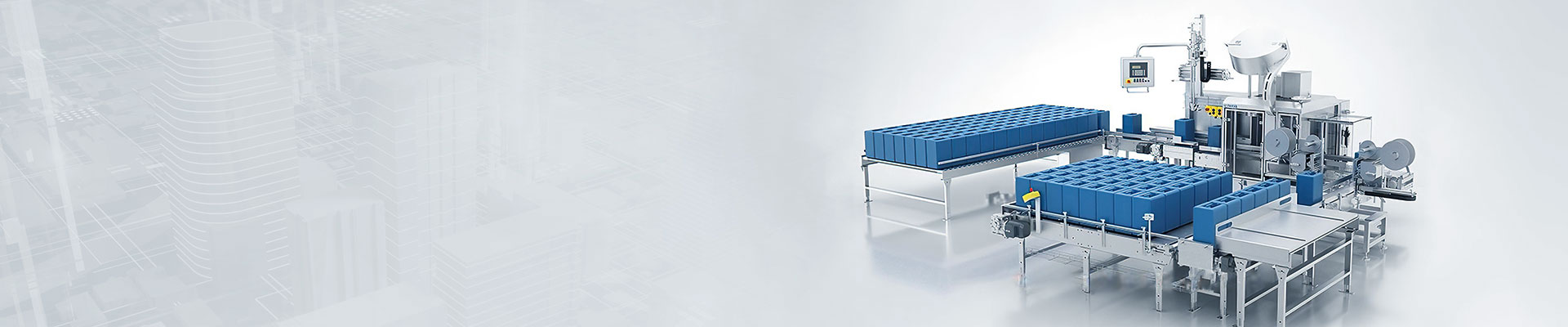
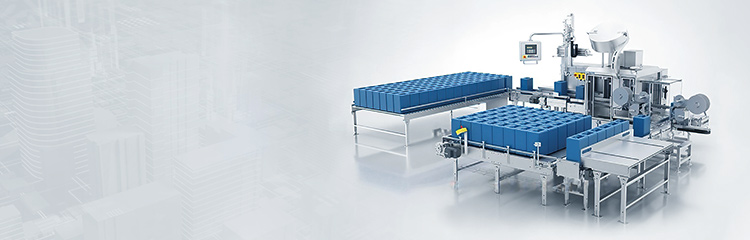
The control system of the feeding system consists mainly of a PLC, a touch screen, actuators and detection elements. The computer downloads the program and monitors the operation of the equipment through the Ethernet PLC on-line. It communicates with PLC through Modbus 485 communication protocol to display the running status of the equipment and set the running parameters for starting and stopping the equipment. The actuator is responsible for executing the instructions from PLC and performing the corresponding actions. The detection element sends the status and parameters of the equipment to the PLC.

The weighing and Batching system mainly consists of industrial control computer (including configuration software), control system (containing plc, etc.), secondary weighing instrument (containing measuring and weighing instrument and expert regulator), frequency converter, on-site operation panel, speed-regulating screw scale and reaction kettle. Production of four kinds of materials for the proportion and become, including the first three kinds of materials have two silos, silos in the material through the respective kettle feeding, and by the dosing spiral scale measurement into the buffer bin, and then by the buffer bin will be mixed into the silo.
The dosage control system is designed by Siemens S7 PLC programming software STEP7V5.2, when receiving the formula data sent by the industrial control machine, it will start the automatic weighing process, and the on-site weighing instrument continuously transmits the data to the PLC through the bus, and decides whether it is high speed or slow speed dosage, and whether it is for overweight processing according to the real-time weighing quantity. Recipe set the order of receiving materials, according to the set order of materials, when a material weighing and the order of the word in line with the time to send a good signal to the PLC weighing, PLC then go to control the receiving bin to receive the corresponding material; weighing the end of the receiving bin continues to rotate with the spiral waiting to receive the next material; when a recipe for all the materials have been received, the spiral automatically turned to the loading and unloading area, replaced by the bin to continue the above process.
Dosing control process is mainly through the spiral scale on the kettle conveying materials for measurement, by the weighing instrument to receive the weighing module signal and speed signals, after processing into the cumulative value and instantaneous flow, and the cumulative value, instantaneous flow signals from the rs-485 port to the industrial control machine (host computer), to 4 ~ 20ma analog current signals transmitted to the pid regulator, the regulator will be compared and operated on the signal and the internal set value, the regulator will be the signal and internal After the regulator compares the signal with the internal set value, the 4-20ma analog signal is sent to the frequency converter, and then the frequency converter adjusts the rotating speed of the reactor Feeder. When the flow rate increases, it reduces the rotating speed of the reactor feeder, and vice versa raises the rotating speed of the reactor feeder, which makes the flow rate of several kinds of materials and the cumulative amount of the phases stay within the set range, and then obtains the reliable quality of the products.