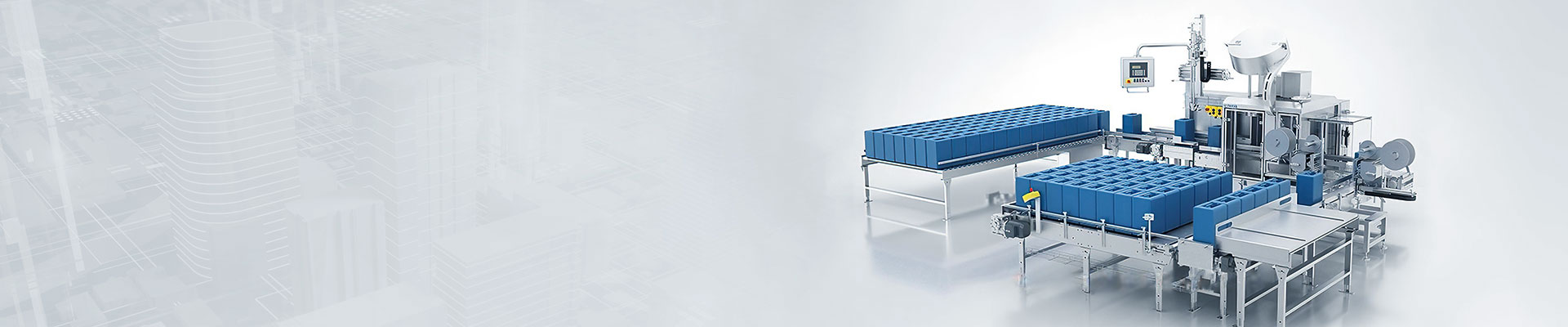
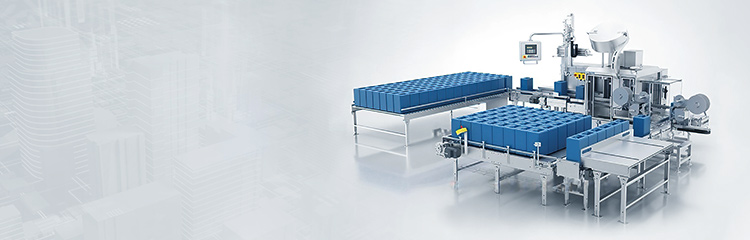
The positive pressure batching system uses the combination of negative pressure pneumatic conveying and weighing technology to complete the material conveying and batching. The system is composed of raw material feeding bin, conveying pipe, feeding valve group and suction feeding multi-component measuring scale. The material is sucked into the storage bin through vacuum negative pressure, and the material is measured while sucking. According to the flow of the material (powder), the arch breaking device can be added to assist the flow, and up to 20 pipes can be connected to the measuring scale at the same time for measurement. Solid material, durable; Meet a variety of material measurement, saving space and cost.

The feeding system will calculate the type and weight of each material that needs to be added, and transmit the corresponding information to the touch and load of the feeding site, add the target value of the powder, touch the start button of the Feeder on the touch screen, and the vibrating feeder will lower the material to the reversible discharge hopper located at the lower part according to the set weight and actual weighing data. When the weighing weight reaches 80% of the set weight, the vibration of the vibration feeder will change from high speed to low speed until it reaches the set weight. After driving the car to the front of the hopper, the hopper will touch the infrared signal of the photoelectric switch installed in the front of the hopper, and after a 5-second delay, it will be installed in the discharge under the control of PLC, so that the lower cylinder will push the side of the discharge hopper from the horizontal position to the highest position and pour the material into the hopper of the forklift truck. The discharge hopper will trigger the high level approach switch at the highest position, and the cylinder will be withdrawn after an automatic delay of 3 seconds, and the lifting side of the discharge hopper will return to the horizontal position to complete the loading action.
The right side of the reversible discharge hopper is fixed by the steel bracket with bearing on the top, and the left side is fixed by the lifting cylinder with bearing on the top support rod. The horizontal and highest positions of the reversible discharge river are respectively equipped with a proximity switch to control the lifting amplitude of the discharge hopper. The upper and lower parts of the lifting cylinder are respectively provided with air intakes to control the lifting of the cylinder. The cylinder can be turned left and right or high and low in the vertical plane, the forklift is not driven to the platform when receiving materials, to avoid platform displacement and damage to the weighing module, the two ends of the photoelectric transceiver device are installed on both sides of the discharge hopper outlet. The signal of the photoelectric device is transmitted to the PLC, and the unloading hopper can be lifted only after the weighing value meets the requirements and the forklift stops the photoelectric signal for 5 seconds, so as to prevent the misoperation of the unloading hopper, and the signals of 3 Weighing modules are received and transmitted to the PLC to provide basis for weighing measurement; Three metering modules are installed in the lower part of the hopper to output millivolt signals to the weight conversion device, and the touch screen is connected to the CPT template of the PLC by DP cable and led to the blanking site. Display the cutting target value on the touch screen and send out the cutting signal; The air source of the air source cylinder is quoted from the compressed air pipe network in the] area, and the pneumatic reversing valve receives the signal from the PLC digital output template for controlling the rise or fall of the lifting cylinder.