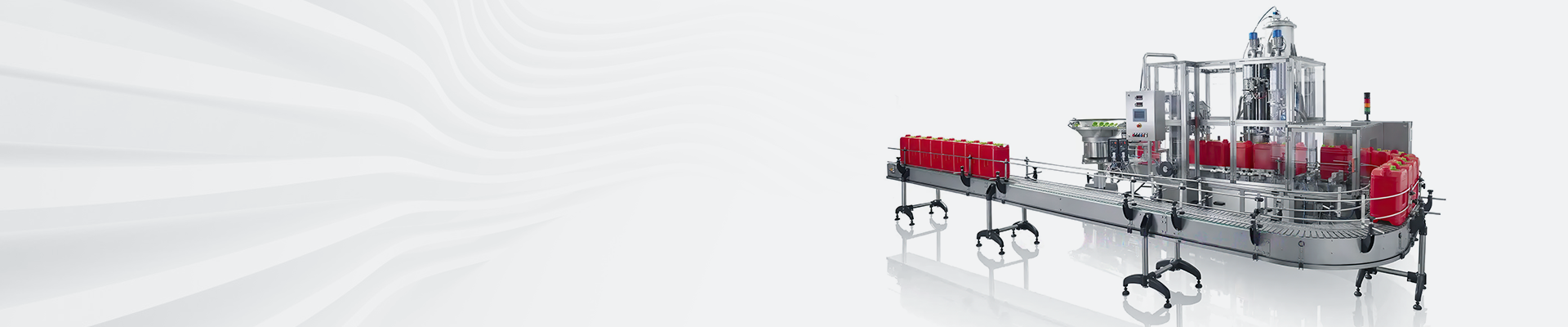
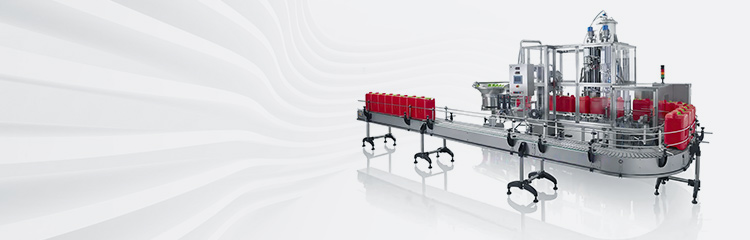

Summary:The alcohol batching system realizes the regulation and control of the production process by automatically adjusting starch → crushing → (adding water) cooking → (saccharifying agent) converting sugar → converting alcohol and carbon dioxide → distillation → extraction distillation → anhydrous ethanol.All monitoring parameters, such as flow, temperature, pressure and equipment status, can be displayed in the form of flow charts or tables.
The process flow of alcohol dosing is as follows: starch → crushing → (add water) cooking → (saccharification agent) conversion of sugar → conversion of alcohol and carbon dioxide → distillation → extractive distillation → anhydrous ethanol. It regulates the distillation vapor pressure of the distillation ladle, the temperature of the second condenser of the distillation tower, the temperature of the third condenser of the distillation tower, the reflux level of the distillation tower, the level of the kettle of the distillation tower, and the temperature in the distillation tower, and displays all the monitoring parameters, such as the flow rate, the temperature, the pressure, and the status of the equipment in the form of a flowchart or a table. Moreover, all the alarm points will flash once the alarm limit is exceeded to remind the operator. The automatic feeding system production process regulation and control is realized through the regulator panel. The regulator has the function of hand-automatic switching, and can carry out self-tuning adjustment under automatic condition. It can be interfaced with various brands and specifications of frequency converter and load cell, which makes the system have great flexibility in the selection of equipment. The monitoring software on the computer utilizes the American DAQFactory configuration software. The software under Windows thread management is very reliable, the software has animation function and PID control function. The flexibility of the configuration software makes the personalization of the system easier and more convenient, and it can be easily customized according to the different needs of the user's interface and operating procedures.
On the basis of real-time trend, the automatic dosage system realizes the historical record of all measuring points. Once you need to trace the past data information, open the historical trend page, click the right mouse button on the blank space below, and in the pop-up dialog box, you can select any curve you need. And also through the historical trend page on the "set parameters" button, according to the user-specified time period for the curve display. Meanwhile, the events occurred during the operation can be displayed in real time and queried in the history alarm page, the query content includes: time, date and time of alarm occurrence, alarm limit value, alarm recovery time, operation user, alarm variable name and so on.
The report page allows historical and real-time query of all parameters, as well as print preview and print function of the report.
Security management of engineering software in the form of sub-users, automatic dosage system can establish multiple users, each user has different powers to carry out a different range of operations, for example: operators can not zero the flow, can not change the PID parameters, can not exit the automatic dosage system during operation and other restrictions, engineers are not subject to restrictions but can not be exited from the automatic dosage system while running, while the automatic dosage Engineers are not restricted but cannot exit the automatic dosage system while running, while automatic dosage system administrator's authority is not restricted, etc.
Typical interface of alcohol dosage system software:
The main interface of the automatic dosage system visually reflects the on-site running condition of the dosage system with realistic animation, and the user can directly apply the control on the interface. The main interface shows the set ratio of each material, the real-time transfer rate of each material, the real-time flow rate of each material, the accumulated output of each material, the actual total flow rate of the material, the actual total output of the material, the indicator light of the operation of the batching machine, the alarm message (which will be displayed only when an alarm occurs), and so on.
The entire weighing and batching system has a master control switch, while each weighing and batching machine has its own control switch, which makes the system operation flexible. At the bottom of the screen are the other controls.
By clicking on a material (white text) in the setup ratio screen, the ratio of that material can be corrected. The ratios of the other materials will be automatically adjusted according to the originally set ratios, so that the ratios of the other materials remain unchanged, and the total ratios remain unchanged at 100%.
In the dosage system parameter setting interface, you can set the alarm threshold for lack of material. When the measured value of the load weighing module is less than the shortage alarm threshold, you can choose the system to abort the task and sound and light alarm.
The hardware parameter setting interface is used to calibrate the load cell and weighing mixer.
The data query interface is used to query the historical data such as alarms and event records. When querying, first set the start and finish time, data category, and then click the query button to query the data.
The weighing control system also has other auxiliary interfaces that allow each user to request personalized interfaces and functions.