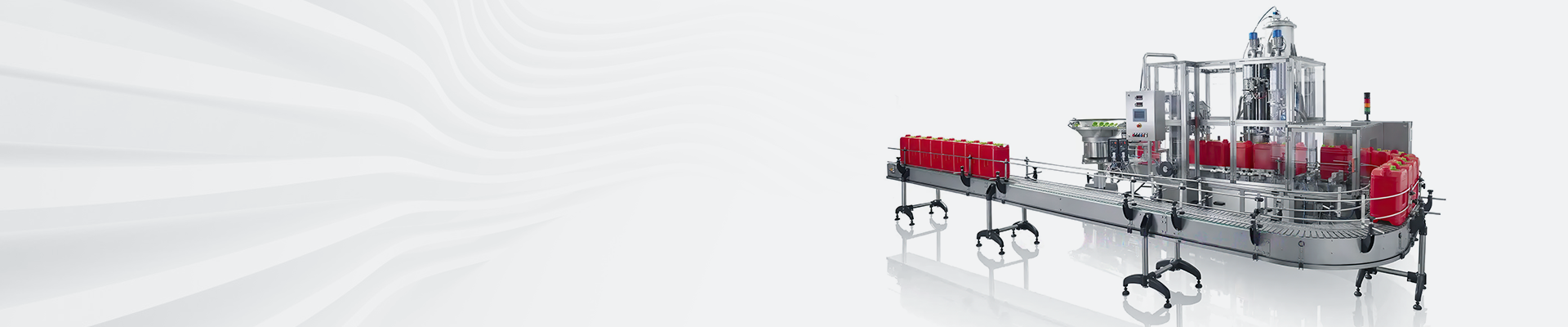
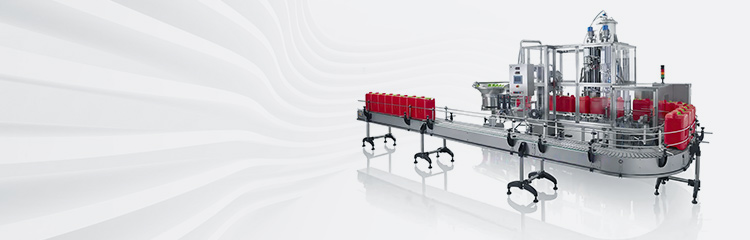
摘要:利用西门子TIA博图V13软件平台,采用PROFINET工业以太网对配料机控制系统进行设计,配料机主要由西门子1516FPLC、G120变频器、TP700人机界面组成。实现自动控制,完成进料、发料、标定等各种操作。对各个阀门采用联锁控制,避免误操作引起物料外泄等事故。
随着现代工业技术的发展和城市化进程的加快,混合搅拌技术也得到了迅速发展。但是如何控制搅拌的过程和质量仍然是一个有待解决的大问题。如何精确控制物料的混合比例、搅拌时间,降低搅拌过程中产生的湍流和搅拌功率,需要通过不断优化技术手段来解决。本研究的目的是利用先进的西门子工业控制技术解决混合过程中的相关问题,并对混合过程进行优化和精确控制。采用西门子高端S7-1500PLC、变频技术和基于PROFIBUS工业以太网技术的总线标准,优化混合搅拌装置的混合搅拌过程和质量,提高混合搅拌质量,实现相对理想的质量和有效的混合混合。
1配料机系统构成
混料机主要由搅拌系统、进料部分、出料部分、控制柜、变频电机、变频器、称重配料系统和控制操作面板组成。西门子1516F-2PNDPPLC用于控制物料配比,G120变频器的输出用于控制电机转速,控制面板用于直观显示电机转速和过程。整个系统可以显示和控制生产过程中各种物料的混合过程。
2配料机控制及通讯设计
2.1配料机的控制设计
在生产过程中,按配方添加的物料由称重控制系统进行计量,产生的信号输入西门子1516F-2PNDPPLC。PLC根据配方控制不同物料的重量和投料顺序。加料完成后,变频电机驱动搅拌系统进行搅拌。采用PLC和变频器控制搅拌速度,实现对产品质量的控制。变频器采用带PROFINET工业以太网口的G120变频器。
2.2配料机系统的通讯及组态设计
(1)配料系统的通讯设计
自动配料系统采用总线网络拓扑结构。PROFINET现场总线用于通信互连。称重模块、行程开关、接触器等信号等现场设备按照就近原则连接至带PROFINET通信接口的1516F-2PNDPPLC的IO模块。变频电机接入G120变频器,PLC、人机界面和变频器均接入同一PROFINET总线网络。
(2)计量配料系统的硬件组态
利用TIA博图V13软件进行硬件组态设计,组建1个S7-1500的控制站,选择CPU模块1516F-2PN\DP(6ES7315-2FJ14-0AB0),对电源模块PS3075A(6ES7307-1EA01-0AA0)、数字模块DI16\DO1624VDC\0.5A(323-1BL00-0AA0)、模拟量计量模块AI4/A028BIT(334-0CEO1-0AA0)进行组态,添加工业以太网总线PROFINET、TP700人机界面及G120变频器(带PN网络接口的控制单元和功率模块)。
3配料机控制系统软件程序设计
3.1配料机G120变频器参数设置
利用博图V13开发平台对G120变频器的参数进行设定。设置P10=1(进人快速调试模式)P15=6(现场总线PROFINET进行通信)、P922=352(PZD6/6控制字)P10=0(结束快速调试),根据电机铭牌设置基准参数。设置P2051通讯内容。P2051.0r2089(状态字1)、P2051.1r633(频率反馈)P2051.2r68(实际电流)、P2051.3r80(实际转矩)、P2051.4r2132(报警号)、P2051.5r2131(故障号)。
表1配料机变频器参数设置
参数地址/说明/参数
P2000/基准频率/1400.00
P2001/基准电压/380
P2002/基准电流/0.3
P2003/基准转矩/0.41(9.55*功率/转速)
P2004/基准功率/0.06
(1)通讯数据端口设计
通讯数据选用PZD6/6,地址对应为:PIW256-PIW266PQW256-PQW266、PIW256为状态字、PIW258频率反馈、PIW260实际电流、PIW262实际转矩、PIW264报警号、PIW266故障号、PQW256为控制字、PQW258为频率设定值、PQW260-PQW266备用(其中所有的设定和反馈数值都是16#0-4000的数,在写入和读取过程中必须进行转换)。
(2)变频器通讯控制字命令及设置
停止:W#16#047E、启动:W#16#047F、反转:W#16#0C7F复位:W#16#04FE
变频器参数的设置:修改P10=1,修改P15=6(现场总线PROFINET,带两项安全功能宏),修改P922=352修改P10=0。
3.2配料机PLC程序设计
进料系统需要完成两种物料的进料、混合和出料功能。物料的进入由电磁阀的通断控制,称重模块通过监测物料的重量来控制物料的输入。按下启动按钮后,电磁阀A通电,第一种材料开始进入容器。当物料达到预设重量时,电磁阀A断电并关闭。电磁阀B通电并接通,第二种物料进入容器。当物料重量达到预设值时,电磁阀B关闭,电机启动搅拌。电机的旋转时间由预设的搅拌时间控制。
3.3混合机控制系统人机界面程序设计
通过设计HMI系统,可以直观、实时、清晰地显示加药机的运行状态,快速设置和控制设备的相关参数。根据装置和控制的需要,设计了搅拌装置的自动操作界面、参数设置界面、启停记录和历史报警记录。
4结束语
对配料机控制系统采用西门子PROFINET工业以太网通讯技术,实现了现场设备的互联,提高了设备运行效率,减少系统故障,降低了设备维护成本,采用HMI人机界面监控,提高了系统人机交互能力,方便技术人员设备的监控,设计出实用性、安全性和高效性的配料机。