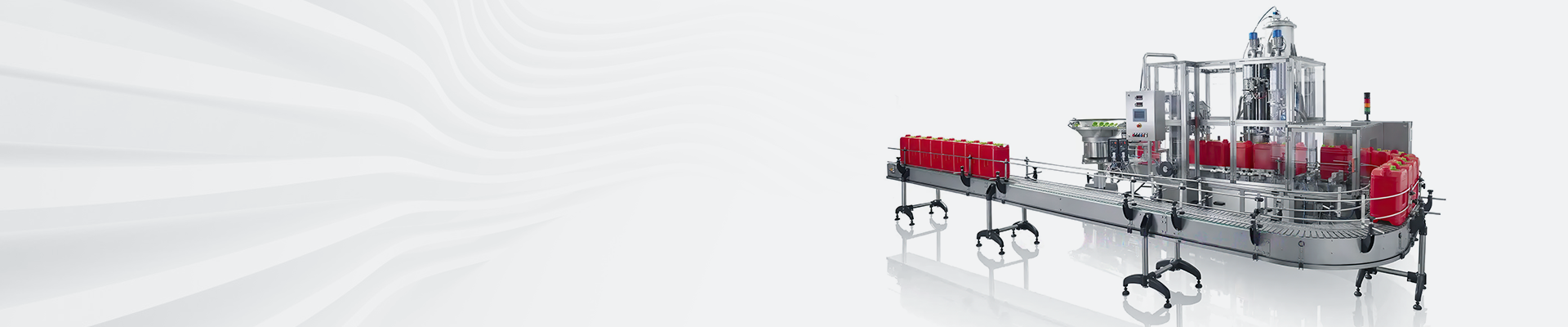
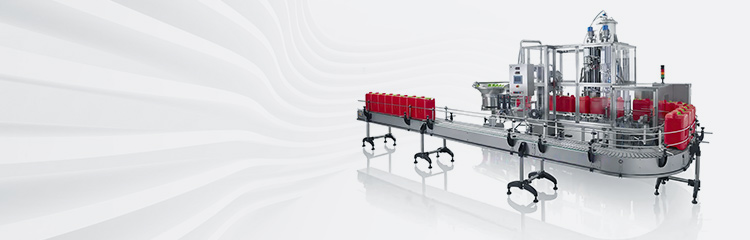
摘要:配料系统采用重量比例前馈控制与模糊自整定PID串级控制的复合控制,通过变频器来控制计量泵的驱动电机转速,从而调节计量泵的投加量,实现自动配料,完成与监控中心的各种通信功能。
0引言
油漆是涂料处理中重要的工艺过程,自动配料系统决定着后续工艺流程的运行效果和最终出厂的涂料质。油漆效果的好坏主要取决于油漆投加量的准确与否。由于油漆过程本身是一个复杂的物理、化学过程,因此,很难准确建立反应过程的数学模型,这就给在线确定油漆投加量带来了困难心。自动配料系统是基本的液体到达油漆制造过程的最基本和最主要的工艺环。根据工艺配方的要求,正确的称重和配料工作是确保生产油漆所需液控制量的基础。如果液控制量不符合标准,或者每个计量放置有不可避免的小偏差,则偏差必须在可接受的范围内控制,否则将影响最终产品的性能。使用现有的工业电子秤或一般的计量,由于人的因素存在,计量的重复准确度不高,开放式人工操作难以确保良好的工艺卫生条件,因此容易偏差计量。因此,自动供液、称重混合配料的运行模式为最佳方式。近年来油漆业的生产技术不断提高和更新。随着《油漆安全法》的推出,油漆安全性的要求也越来越高。自动称重和混合配料的工作模式逐渐应用和普及。
1称重配料工作原理
配料系统主要由数据主要从事电气自动化的釆集设备、称重仪表、变量执行设备等组成。数据采集设备主要包括称重模块、流动电流检测仪和浊度计等仪器仪表,其釆集的模拟量信号经处理后送入相应的称重仪表。各称重仪表执行相应控制算法后得到控制量,此控制量经变量执行设备计量泵控制油漆。供液称重混合配料系统由存储反应罐、供料系统、混合设备、输送设备和控制系统组成。主要功能:接收和储存液体(散装或铁桶),不同液体和沉积液体的分布和混合,分发到间歇性或连续性称重配料罐。适用于需要液体的涂料企业的批量生产。此配料设备生产计量,效率高,解决客户手动携带液体的重型体力劳动,节约劳动力,解决搬运过程中液体的偏差和开封过程中残留液体的浪费,节约反应罐的存储,合理使用空间,灵活设置保存点和使用点。自动配料机由可编程控制器控制,无需手动控制即可持续存储、使用和分配液体。采用重量比例前馈控制与串级控制的复合控制策略。选用频率、冲程双调节的计量泵,其对搅拌量的精确控制原理如下。
①串级控制回路:沉淀池出涂料浊度控制回路为主回路,流动电流闭环控制回路为副回路。流动电流闭环控制回路为主要控制手段。即在线监测原涂料搅拌后的流动电流值(SCD)-与&电位正相关的油漆本质参数,仅此一项参数即可准确判定搅拌量是否合适,从而在数分钟内对搅拌量进行调整。
②重量比例前馈控制回路:为提高计量泵在原涂料重量大幅变化时的响应速度,加入了重量比例前馈控制回路。具体实现方法是在原涂料配料设备设置称重模块,用于获取原涂料重量,并通过改变冲程调节器的比例系数来调节计量泵的冲程长度,使响应时间大大缩短,仅为数几秒。
2配料硬件设计
该配料下位机采用S7-200系列,CPU型号为224XP。充分利用称重仪表的信号采集、A/D转换、模糊控制程序执行、控制信号发送、通信等功能对油漆称重配料进行自动控制。
PLC经数字量输入模块EM221(8路数字量输入,输入电压额定值为24VDC)采集手动/自动的按钮开关量信号,决定是否执行自动控制程序。模拟量输入模块EM231(4路模拟量输入,量程为0~20mA,分辨率为12位)采集模块输出的4~20mA的电流信号,输出控制信号送位置式伺服机构,从而调节冲程长度,使其在0~100%的范围内变化;EM231采集浊度计和流动电流检测仪输出的4~20mA标准电流信号,并将其标准电流信号,传送至CPU执行串级控制程序。计算得到的控制信号由模拟量输出模块EM232(2路模拟量输出,量程为。~20mA,满量程时的分辨率为11位)输出4~20mA电流信号,控制变频器,从而驱动计量泵电动机按所需速度运行,实现冲程频率的调节;数字量输出模块EM222(8路数字量输出,输出电压额定值为24VDC)用于显示程序控制设备工作或手动控制设备工作,自动配料系统同时还可以进行故障显示与报警。
上位机主要用于对油漆配料的监控以及为管理者提供相应参数,以便对被控对象的具体状态做出调整。从经济适用方面考虑,上位机釆用普通的PC机,并且在其PCI插槽中插入MPI通信卡。PLC与通信卡之间用MPI电缆连接,并采用MPI协议,实现PLC与上位机的通信,传输速率为187.5kbit/s。
3配料软件设计
3.1控制算法设计
配料控制系统由计算机、机柜和外围设备(前配料秤、后配料秤、料位机)组成。配料监控系统由两台计算机作为整个系统的人机界面。其中一台为主站,完成全部系统参数设定、过程监控、数据记录;另一台作为从站,以主站为依托,主管后配料系统的数据设定、过程监控。主站直接同西门子S7300PLC系统、前配料秤和后配料秤相通信。前配料控制系统现场采用密封型接线盒,防尘、防潮,可确保信号传输可靠。前配料秤采用专用工业过程控制仪,通过RS-485总线与中控室实现通信,既可独立控制,又可实现PLC联机控制。以重量比例调节计量泵的冲程为目的的,由于冲程与原涂料重量成比例关系,采用PID串级控制方案。以改善由于涂料质发生变化时的动态性能和抗干扰能力。
3.1.PID设备
自动配料系统采用西门子S7-400PLC作为下位机,PLC与两个EM200子站、12台西门子MM440变频器通信,采集、处理现场数据和简单的控制。PLC用CP443以太网模块和上位机进行通讯以交换系统运行数据。
组态系统使用组态配料设计的组态界面如下:首页封面、登录界面、设备操作界面、配料设定界面、配方界面、实时数据界面、报表界面、系统诊断界面等。
基于PID参数自整定控制规则,结合工程设计人员的技术知识和实验操作经验,建立符合控制规则表。
进行模糊推理与反模糊化步骤。根据已设计好的模糊控制规则表,应用模糊推理合成规则,计算出模糊控制量。
3.1.2PID算法
PID采用工程上常用的增量式PID算法,PLC是油漆搅拌配料的核心,程序设计采用模块化、功能化结构,便于维护、扩展。软件主要由以下模块组成:
初始化程序,用来设定各寄存器、计数器、PLC工作模式、通信方式等参数初始值;
故障检测子程序,对各种阀门及泵等动力设备故障进行自动检测并报警;据采集子程序,釆集各路模拟量数据,并进行滤波、平均等处理;
ADC中断程序,对采集后的模拟量进行A/D转换;
模糊自整定PID控制子程序,转换后数据送模糊自整定PID控制子程序,计算出的控制量送PID称重仪表,作为PID称重仪表的设定值;
PID控制子程序,计算出的控制量通过变频器来控制计量泵的驱动电机转速,从而调节计量泵的投加量,实现自动油漆;
信子程序,完成与监控中心的各种通信功能。
3.3上位机组态软件
本称重配料系统釆用组态王6.51(KINGVIEW)软件开发,通过组态王对油漆过程进行组态监控,控制方案和算法在PC机上组态。程序分为主控界面、实时曲线显示、历史曲线査询、报表输出和称重配料系统报警等5个部分,采用3级权限密码设置,即操作员、技术员和系统管理员,以实现不同的级别权限。操作员可以控制设备的启停,可以使用软件但不能修改参数;技术员可以对配料的控制参数进行修改;配料管理员可以进行所有配料功能的修改。PLC程序包含三部分:主程序部分,主要负责手动/自动处理流程的选择、进入液位处理子程序的判断、各种故障状态下报警灯的显示处理与控制循环;子程序有两个,分别是液位处理与自动运行。其中液位处理子程序主要负责通过采集到的液位高低数值信息与设定值进行比较来判断物反应罐内液位的高度,液位的高低信号会决定料泵的开启与闭合状态。当采集的输入数值超过设定液位的最大允许值时,会自动将其限制在合理范围,以免出现异常情况。自动运行子程序的工作过程是主要部分,在未出现其他异常情况与选取手动状态时,会一直按照工艺流程的要求往复循环,其各部分数值会同步显示在组态界面上,以便控制人员参考与监测。
4配料仿真
根据前面建立的算法模型,使用Matlab中的Simu-link和Fuzzy工具箱对配料系统进行了仿真,并且与常规PID串级控制进行了比较。仿真开始时,原涂料重量为1500m'/h,各种控制算法经过一定的调节时间均能使油漆量稳定在350iyh,但配料系统性能优劣不一。由仿真结果可知,常规PID串级控制与模糊PID串级控制相比,后者较前者的超调量小,调节时间短。在油漆量稳定后的某一时刻改变原涂料重量,在此选择开始时刻后的第300s调节原涂料重量为2570m3/h,各种控制算法经过不同的调节时间仍能使油漆量最后稳定在600I/h,配料调节性能同样有优劣之分。由仿真结果可看出,不加重量比例前馈控制与加重量比例前馈控制相比,后者的调节时间明显缩短,油漆量能随原涂料重量变化及时得到调整。为证明上述结论的可靠性,在油漆量稳定后再次改变原涂料重量,这里选第600s调节原涂料重量为1070m'/h,各种控制算法均能使油漆量最终稳定在250I7h,在配料调节性能方面得到相同的结论。
5结束语
该称重配料系统以S7-200PLC作为处理器核心,以普通PC机作为上位机实现对油漆过程的监控与参数管理。这不仅能实现自动控制功能,同时还具备实时监视、数据分析、打印报表等功能。控制算法方面采用重量比例前馈控制和模糊自整定PID串级控制的复合控制策略,发挥PID和模糊控制以及串级控制的优点,扰动控制和偏差控制相结合,具有控制精度高、适应性强、鲁棒性好等特点,能很好地适应现实生产过程中的控制要求。保证将出厂涂料浊度控制在1NTU以下,涂料处理效果好,而且节省搅拌量,取得了较好的经济效益。