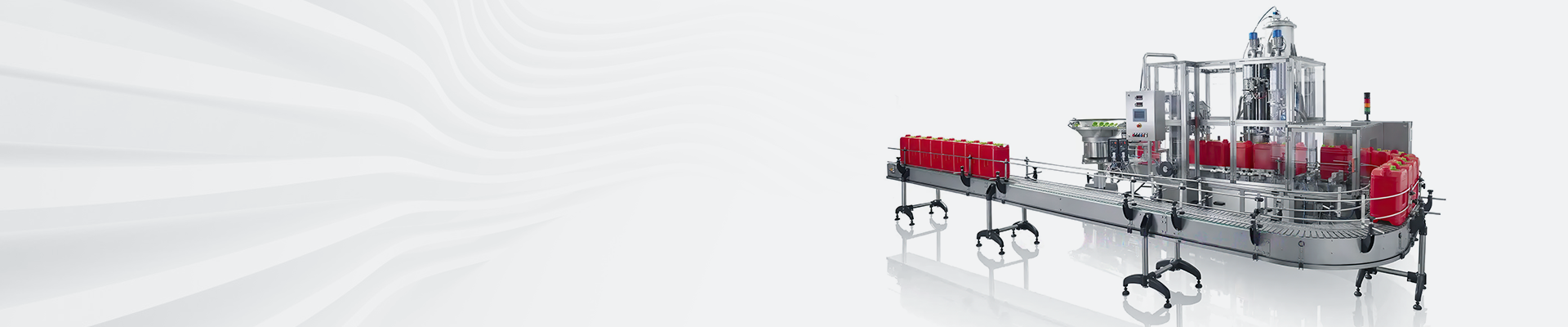
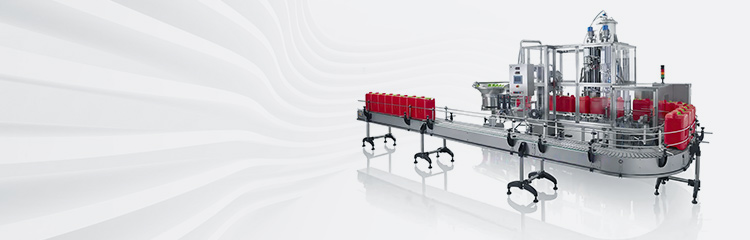

Summary:Two kinds of PVC powder feeding systems, dense phase pneumatic feeding system and thin phase pneumatic feeding system, are introduced. Through the comparison of the two in terms of investment, energy consumption, environmental protection and impact on product quality, it is pointed out that dense phase pneumatic feeding system has more advantages in PVC powder transportation.
The use of pipeline pneumatic conveying technology to transport all kinds of bulk powder and particles has the characteristics of convenience, safety, cleanliness and airtight. With the continuous development of modern industrial production scale, logistics technology specialization and people's awareness of environmental protection, this technology is more and more favored by various industries. In the production of PVC, PVC powder is also commonly used in this transportation technology. Pneumatic conveying technology of pipeline is divided into positive pressure conveying and negative pressure conveying. Because the energy consumption required for positive pressure transportation is much lower than that for negative pressure transportation, under normal circumstances, positive pressure pneumatic transportation technology is usually used in industry, unless there are special process requirements to use negative pressure transportation technology. Positive pressure pneumatic conveying also has dense phase and thin phase, and the corresponding conveying system generally has two forms: ① thin phase pneumatic conveying. The use of low pressure, large flow of gas to form high-speed fluid to achieve short distance conveying materials. Domestic PVC production enterprises generally adopt this technology. ② Dense phase pneumatic conveying. The use of controlled, clean high-pressure gas at low flow rates to achieve block flow or plunger material delivery. Foreign countries in the 1980s began to popularize the technology, Europe, Japan, the United States PVC industry pneumatic conveying generally use dense phase pneumatic conveying, domestic PVC production enterprises in the recent new equipment began to use.
1PVC thin phase pneumatic feeding system
The first task of pneumatic conveying is to maximize the solid gas ratio of pneumatic conveying (that is, to maximize the ratio of conveying material quality to air quality), because to follow the law of conservation of energy, so the solid gas ratio is proportional to the pressure loss of conveying. The solid gas ratio of thin phase pneumatic conveying is generally lower (3:1 ~ 8:1), so the pressure loss of thin phase pneumatic conveying is small, and most of them are powered by Roots fans or centrifugal fans. The pressure rating of Roots fans is 50 to 100 kpa, while the centrifugal fan is even lower, 5 to 10kPa. Typical PVC thin phase pneumatic feeding systems generally use Roots fans and rotary valves for conveying. The process is described as follows: The PVC powder stored in the PVC silo is evenly pumped through the rotary valve to the injector, where it is mixed with air pressurized by the Roots fan. The mixed air and PVC powder are driven by the pressure difference and transported to the PVC receiving bin through the conveying pipe. The air with powder material passes through the bag dust collector at the top of the bin to recover the powder material and become clean air and empty.
Compared with the traditional thin phase pneumatic conveying technology, the newly built PVC production enterprises tend to use dense phase pneumatic conveying technology in recent years, the reasons are as follows: (1) dense phase pneumatic conveying technology has achieved a comprehensive technical breakthrough in theory and practice; ② Today's electromechanical equipment and automatic control equipment are becoming more and more perfect; ③ Dense phase pneumatic conveying is more energy saving and environmental protection than thin phase pneumatic conveying.
Dense phase pneumatic conveying uses a high solid-gas ratio, generally 30:1 ~ 50:1, and ultra-dense phase pneumatic conveying can even reach 80:1 ~ 100:1. Therefore, dense phase pneumatic conveying requires higher conveying pressure, and compressed air is generally used for conveying, and the pressure of compressed air is 500~1000kPa. The vast majority of dense phase pneumatic conveying adopts bin pump for intermittent conveying, and individual enterprises also use rotary valve continuous conveying (similar to thin phase pneumatic conveying), but this conveying method has very high requirements for the air tightness of the rotary valve, and can only use imported equipment, which is expensive.
The typical flow of dense phase pneumatic feeding system is introduced by using the down type double bin pump of Hyman Pneumatic Conveying Company as an example. The process adopts the down type bin pump and combines with the US patent technology - Venturi annular gap air conditioning technology to carry out material transportation. The PVC powder stored in the PVC silo enters one of the silo pumps (such as the A silo pump) through the three-way valve. When the level meter detects that the material level has reached the specified position, the feed valve and the drain valve are closed. The program automatically opens the lower intake valve to purge the pipeline, and then opens the discharge valve of the bin pump and the upper intake valve. The PVC powder is pressurized by compressed air and enters the Venturi injector for mixing with the lower intake air. The mixed PVC powder and air are transported to the PVC receiving bin through the conveying pipe. The air containing PVC powder is filtered by the cloth bag filter on the top of the bin and emptied. After the A bin pump is delivered, the discharge valve and the upper and lower intake valves are closed, the empting valve is opened, and the feed is re-fed, and then the B bin pump is delivered. The two bin pumps alternately "feed" and "transport" the PVC powder continuously delivered to the target bin.
3 Comparison of two feeding systems
3.1 Device Configuration Comparison
Thin phase pneumatic conveying technology is mostly powered by Roots fans, and the pressure level of Roots fans is 50~100kPa. In order to achieve a certain distance and a certain amount of material transportation, it is necessary to increase the air volume, reduce the material concentration, and improve the material transportation speed. Therefore, the configuration of conveying pipe diameter, valve and dust collector is much larger than that of dense phase pneumatic conveying.
The main parameters are as follows: the PVC powder conveying capacity is 15t/h, the horizontal conveying distance is 30m, the vertical conveying distance is 20m, and the 90° elbow is about 4. Under the conditions of these parameters, the equivalent conveying distance of dense phase pneumatic conveying technology is about 110m, and the solid-gas ratio is 40:1. The equivalent conveying distance of thin phase pneumatic conveying technology is about 170m, and the solid-gas ratio is 8:1. What should be explained here is that the translation of the equivalent distance is also different for different conveying speeds. For example, the equivalent distance of the elbow is considered from 10 to 50m in thin phase pneumatic conveying, and from 5 to 10m in dense phase pneumatic conveying.
3.2 Comparison of energy consumption
Dense phase pneumatic conveying uses a high solid-gas ratio, even when PVC conveying solid-gas ratio reaches 40:1, it can be stable conveying, so the conveying efficiency is high and the energy consumption is low.
3.3 Comparison of conveying quality
(1) Thin phase pneumatic conveyor generally uses Roots fans and rotary valves for material transportation, and the conveying air with high humidity is often accompanied by impurities such as oil and rust after pressurization, and it is usually necessary to install coolers and dryers at the outlet of Roots fans, but it is often abandoned because the pressure loss of the fans is too large, thus affecting the quality of the delivered materials; Dense phase pneumatic conveying uses compressed air as the power, the air into the compressor through the precision air filter to remove solid impurities, compressed air through the cold dryer to remove oil and water, but also through the molecular sieve dryer to further remove water, the air obtained clean and dry. (2) The rotary valve used for thin phase pneumatic conveying, because of the problem of processing accuracy, PVC powder will enter the end cap and bearing of the rotor, and form a plasticized block after a long time of grinding, which not only pollutes the product, but also causes frequent maintenance of the equipment. The dense phase pneumatic conveying adopts static equipment, which completely solves the problem of plasticizing block. Automatic valves are used in dense phase pneumatic conveying. Because PVC powder has no grinding property, the valves used can run stably for a long period.
(3) Thin phase pneumatic conveying due to the low solid gas ratio, the amount of air used for conveying is large, the conveying speed is fast, and the end speed can reach 30m/s. If the conveying speed is too high, the high-speed friction between PVC powder and the conveying pipe wall generates a lot of heat, which will lead to the decomposition of PVC yellow, and even melt to produce "wire drawing" phenomenon. Dense phase pneumatic conveying because of the high solid-gas ratio, the conveying speed is slow, the end speed is less than 18m/s, the heat generated by the friction between PVC and the pipe wall is naturally little, even in summer, the temperature of the pipe wall is not too high.
3.4 Comparison of conveying distance
Since the resistance is proportional to the square of the speed, the increase of the conveying speed is bound to cause the increase of the resistance, because the pressure of the Roots fan is limited, the conveying distance of the dilute phase pneumatic conveying technology is generally not more than 200m, and the conveying distance of the dense phase pneumatic conveying technology can reach several thousand meters.
3.5 Compare the impact on the environment
The noise pollution of Roots fan, which is used in thin phase pneumatic conveying, is always a difficult problem to solve. Usually the noise of Roots fans exceeds 90dB, if you want to reduce the noise by a few decibels, you can sacrifice valuable pressure at the cost of adding inlet and outlet mufflers. Even if the muffler and sound enclosure are added, the noise of Roots fan is difficult to meet the environmental requirements. Dense phase pneumatic conveying adopts air compressor, compressed air can be transported for a long distance, the compressor can be centrally arranged, through the compression room noise reduction and sound insulation treatment, can meet the "industrial enterprise noise health standards".
4 Concluding Remarks
In PVC powder transportation, compared with thin phase positive pressure charging system, dense phase pneumatic charging system has the advantages of low investment, low energy consumption, clean transportation, long transportation distance and low noise, so most enterprises are more inclined to use dense phase pneumatic batching system. Dense phase pneumatic feeding system is the inevitable trend of pneumatic conveying development in the future.