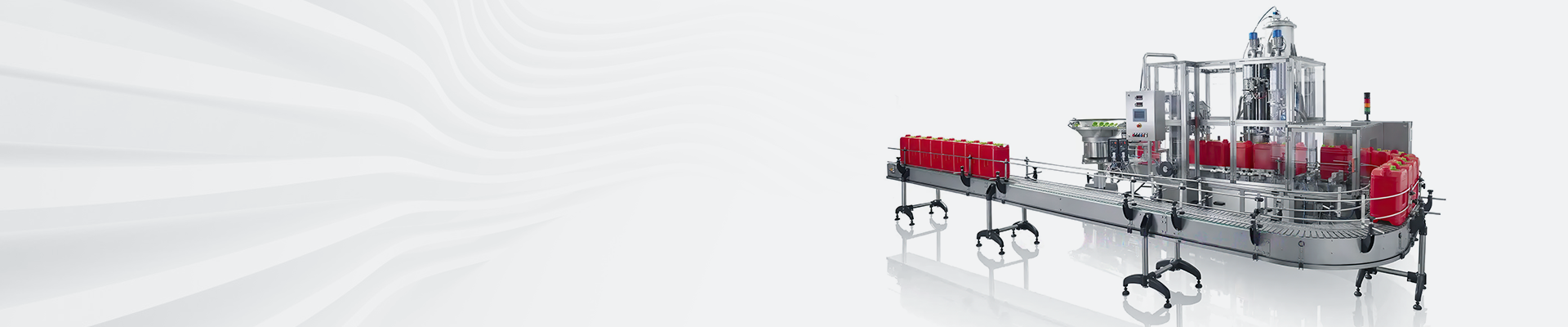
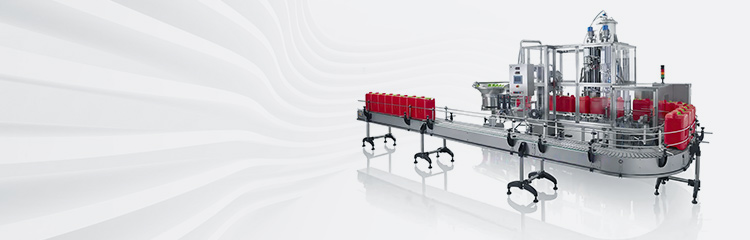

Summary:Two kinds of PVC powder feeding systems, dense phase pneumatic feeding system and thin phase pneumatic feeding system, are introduced. Through the comparison of the two in terms of investment, energy consumption, environmental protection and impact on product quality, it is pointed out that dense phase pneumatic feeding system has more advantages in PVC powder transportation.
0 Introduction
Pneumatic feeding system is widely used in chemical, pharmaceutical and other industries, and is a mature material conveying method. It has the advantages of flexible pipeline configuration, complete closure of the conveying system, high efficiency of bulk material conveying, quality assurance of conveying materials, and quantitative distribution in the conveying process." FCC catalyst is a microsphere particle with reasonable particle size distribution, solid content is not less than 80%, according to its characteristics suitable for pneumatic conveying.
In FCC catalyst plants, semi-finished products such as catalysts and auxiliaries with different properties and effects are often produced, and then these products are blended according to different needs to prepare finished catalysts that meet various petrochemical processes. In addition, in the production process of FCC catalyst, affected by raw material supply, production process, operation timing and other conditions, different batches of product specifications are not the same, in order to ensure uniform particle size and physical stability of the product, it is necessary to further mix.
The existing powder mixing technology can be divided into the following types: gravity mixing, fluid mixing, mechanical mixing and combined weighing mixing. Among them, the structure and operation of gravity mixing and mechanical mixing devices are relatively simple, the production continuity is strong, and the application has been verified in the production of FCC catalyst, but the mechanical mixing processing capacity is small, the energy consumption is large, is not conducive to large-scale continuous production, and the rotating parts are many, easy to cause failure. Therefore, gravity blending is a better model.
1 Technical Content
In order to combine the existing dosing process, overcome the shortage of existing technology, and meet the needs of finished catalysts with different properties, a kind of pneumatic charging system mixing technology of FCC catalyst is introduced in this paper. The orifice jet of the Venturi conveyor is used to spray out high-speed air, thus forming a negative pressure field relative to the positive pressure of the air flow in the pipe, generating suction, and pumping different batches of FCC catalyst and auxiliary powder to make it preliminarily mixed; By using the multi-tube gravity mixing bin, through the air circulation, the final product is mixed several times to achieve different blending purposes and get the finished product to meet different needs.
(1) Product cooling transport process
The high-temperature FCC catalyst enters the cooling silo 2 through the product discharge valve 1, and cools down after reverse indirect contact with the cooling water in the coil tube. At the same time, the positive pressure air generated by the product conveying fan 5 flows through the Venturi conveyor 4, thus forming a negative pressure field in the throat part. The cooled FCC catalyst is sucked into the Venturi conveyor 4 through the product discharge valve 3 which has the locking air function. After being accelerated by the high-speed jet air, it enters the product pulse bag filter 6-1/2 under the positive pressure pneumatic conveying. The separated FCC catalyst enters the product intermediate tank 7-1/2, and the purified jet air is emptied.
Product pulse bag filter 6-1/2, product intermediate tank 7-1/2, product discharge valve 8-1/2 and Venturi conveyor 9-1/2 can be operated in a standby rotation, or parallel operation.
(2) Product transportation and storage process
The FCC catalyst entering the product intermediate tank 7-1/2 enters the Venturi conveyor 9-1/2 through the product discharge valve 8-1/2, while the positive pressure air generated by the product conveying fan 10 flows through the Venturi conveyor 9-1/2, pumps the FCC catalyst and sends it into the product pulse bag filter 11-1/2/3/4. The separated FCC catalyst enters the product storage tank 12-1/2/3/4, and the purified jet air is emptied.
Product pulse bag filter 11-1/2/3/4, product storage tank 12-1/2/3/4 and product discharge valve 13-1/2/3/4 are mutually standby. Different batches of FCC catalysts can be stored in different product storage tanks.
(3) auxiliary mixing transport process
Under the action of multi-tube gravity mixing pipe, the additives entering the additive mixing bin 20 reach the performance homogenization, enter the Venturi conveyor 22 through the additive unloading valve 21, and at the same time, the positive pressure air generated by the additive conveying fan 23 flows through the Venturi conveyor 22, pumps the additive and sends it into the additive pulse bag filter 15. The separated auxiliary enters the auxiliary storage tank 16, and the purified jet air is emptied.
(4) The blending and conveying process of finished products
FCC catalysts entering product storage tank 12-1/2/3/4 enter Venturi conveyor 14-1/2/3/4 through product discharge valve 13-1/2/3/4 respectively. The additives entering the auxiliary storage tank 16 enter the Venturi conveyor 18 through the auxiliary discharge valve 17; At the same time, the ambient air is pressurized by the product conveying fan 19 and enters the Venturi conveyor 14-1/2/3/4 and Venturi conveyor 18 respectively. The FCC catalyst and auxiliary are pumped and fed into the finished product pulse bag filter 25-1/2, the initial mixed "FCC catalyst + auxiliary" finished powder enters the finished product mixing bin 26-1/2, and the purified jet air is emptied.
Different batches of FCC catalysts stored in product tanks 12-1/2/3/4 can be transported individually, in pairs, or simultaneously to the finished product blending tank 26-1/2 for blending, depending on the desired finished product specifications.
The "FCC catalyst + additive" powder entering the finished product mixing bin 26-1/2 can be mixed in a single warehouse, multiple mixing in a single warehouse, and multiple mixing in a double warehouse. Among them, the finished product conveying fan 30 is not opened in a single warehouse for single mixing. Under the action of multi-tube gravity mixing tube, the powder of "FCC catalyst + auxiliary agent" is only mixed once in the finished product mixing bin 26-1/2, that is, discharged through the finished product discharge valve 27-1/2 and the reversing valve 28-1/2. For multiple mixing in a single bin, the finished product conveying fan 30 needs to be opened. Under the action of the multi-tube gravity mixing tube, the powder of "FCC catalyst + additive" is mixed in the finished product mixing bin 26-1/2 respectively, and enters the corresponding Venturi conveyor 29-1/2 through the corresponding finished product discharge valve 27-1/2 respectively. At the same time, the ambient air is pressurized by the finished product conveying fan 30 and enters the Venturi conveyor 29-1/2 respectively. The pumped "FCC catalyst + additive" powder is respectively fed into the finished product pulse bag filter 25-1/2, and the separated powder is mixed again in the finished product mixing bin 26-1/2, which can be cycled several times until the performance uniformity is achieved. The finished product mixing bin 26-1/2 can be operated in a rotation, or parallel operation at the same time; For multiple mixing in double silo, the finished product conveying fan 30 needs to be opened. Under the action of multi-tube gravity mixing pipe, the powder of "FCC catalyst + auxiliary agent" is mixed in the finished product mixing silo 26-1, and enters the Venturi conveyor 29-1 through the finished product discharge valve 27-1. Meanwhile, the ambient air is pressurized by the finished product conveying fan 30 and enters the Venturi conveyor 29-1. The "FCC catalyst + additive" powder is pumped into the finished pulse bag filter 25-2, and the separated powder is mixed again in the finished product mixing bin 26-2. When the finished product mixing bin 26-1 and 26-2 are connected in series, the powder can be circulated several times between the two silos.
Note: The auxiliary mixing bin and the finished product mixing bin may be Phillips type or wall-mounted multi-tube gravity mixing bin, or multi-channel gravity mixing bin.
2 Technical Features
(1) Small power consumption: in the conveying stage, the Venturi conveyor is used to spray high-speed gas to form a negative pressure field, thereby improving the vacuum degree in the conveyor, so that the powder can be sufficient and uniform into the conveyor; In the mixing stage, the purpose of mixing is achieved by the gravity flow of powder itself. No moving parts and mechanical transmission, low energy consumption. (2) Simple equipment: In addition to the fan and rotary discharge valve, the system is a static equipment, simple operation, easy maintenance, low investment cost.
(3) Strong functionality: the system includes a variety of technologies such as catalyst cooling, silo transportation, mixing, etc., the system is compact and functional.
(4) High selectivity: the system can blend FCC catalyst powder according to different needs, which is manifested as (1) different batches of the same type, (2) different particle sizes of the same type, and (3) different types with different properties. The obtained catalyst can be further mixed with the additive powder with different efficacy, so as to obtain the finished product with different properties.
(5) The homogenization effect is good: in the pneumatic conveying stage, the FCC catalyst and auxiliary powder are initially mixed; In the gravity mixing stage, a variety of mixing methods can be selected, such as single warehouse single time, single warehouse multiple times, multi-warehouse multiple times, etc., and the homogenization effect is good.
(6) The technical conveying capacity is large, the conveying distance is long, the degree of automation is high, the system is closed, and there is no pollution.
3 Closing remarks
Using pneumatic conveying + gravity mixing technology, the flexibility and continuity of FCC catalyst transportation and different blending needs of products are realized, the fluctuations of product particle size distribution caused by unstable factors in the production process are eliminated, and the uniform and stable product quality is ensured, which provides a basis for the design optimization and selection of FCC catalyst production equipment.