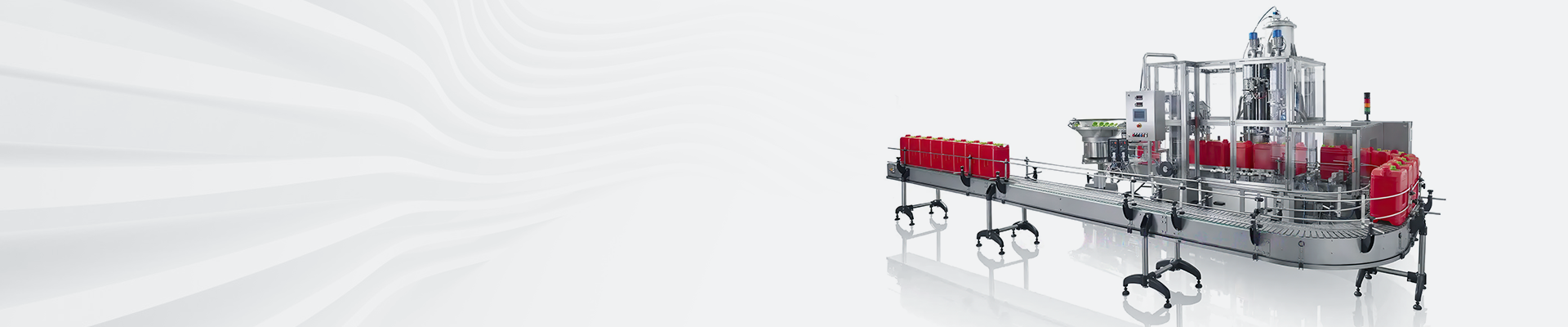
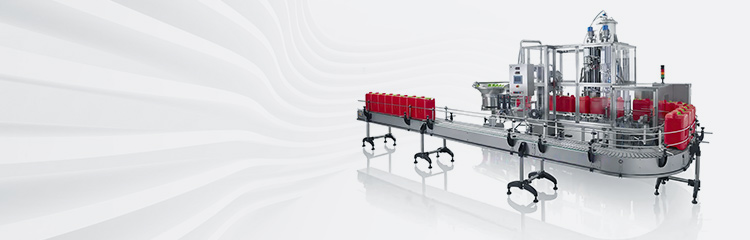

Summary:Refractory batching system is a multi-variable nonlinear system, using the traditional PID control, it is difficult to achieve the ideal control effect, this paper proposes a refractory batching control system based on the control system algorithm, which has been applied to the refractory batching production line of Benxi Yamei Refractory Co., LTD., has been successfully run for more than one year, practice has proved, The control system fully meets the technological requirements and obtains satisfactory control effect.
summarize
Refractory feeding system is a multi-variable nonlinear system, there is coupling between the variables and some variables are difficult to measure, at the same time, to achieve high control accuracy in a very short time, the use of conventional PID control, it is difficult to achieve the ideal control effect. The control system is a rule-based control system, which directly adopts linguistic control rules and takes the control experience of field operators or the knowledge of relevant experts as the starting point. It does not need to establish an accurate mathematical model of the controlled object in the design, so that the control mechanism and strategy are easy to accept and understand, the design is simple, and the calculation amount is small. The operation speed of the control system is fast, the robustness of the system is strong, and the influence of interference and parameter change on the control effect is greatly weakened, which is easy to realize fast control.
Characteristic analysis of control object
The main process equipment of Yamei refractory batching system is composed of 44 silos (44 feeders), 9 hoppers, 11 electronic scales, 2 transport carts and 2 mixing units. The first 24 silos are filled with shaped materials, and the materials of each 6 small silos are successively lowered into 1 hopper, and the screw feeder is controlled by the frequency converter for precise batching; The last 20 silos are filled with granular material, and the material of each 4 small silos is successively lowered into a hopper, which is precisely batched by the electric shock feeder. A total of 9 hoppers, each hopper is installed under an electronic scale, each electronic scale is responsible for the weighing control of 4 or 6 kinds of materials in their own hopper. The remaining two electronic scales are mounted on the trolley.
According to the process characteristics of the batching system, weighing and batching up to 6 kinds of materials can be realized in a weighing hopper scale within a few seconds. The traditional PID control is difficult to achieve the ideal control effect, and the control system is the ideal control method.
3 Composition and working principle of the control system
Refractory PLC control system adopts S7-300PLC, the monitoring function is realized by configuration software WinCC, the system can realize the proportioning control of 9 hopper, the running, positioning and feeding of the hopper, and the frequency conversion control of the screw reamer and the voltage control of the electric shock feeder, formula generation, automatic alarm, fault diagnosis, display, printing and other functions. According to the process requirements, the formula is automatically generated on the upper computer, the set value of each feeding is set, the control value of feeding is calculated, and the control output is formed according to the fuzzy algorithm, so as to achieve accurate batching control.
Control system description
1. Composition of automatic dosing machine
The preparation process is as follows: (1) Premix preparation, premix mixing, drying and premix warehousing; (2) Metal screening a metal into the warehouse; (3) Finished product batching, finished product mixing, drying and delivery to the next process. According to the dispensing process, the body automatic dispensing production line is composed of a drug bin, a screw feeder, a hopper scale, a review hopper and a body proportioning system. The hopper scale corresponds to the bottom of the hopper. In order to prevent misweighing and ensure weighing accuracy, a review hopper is set under the hopper scale to review the weight of each weighing material. Each hopper scale and check hopper is equipped with 3 weighing modules. The load cell is mounted radially along the hopper and sends a weight signal to the load cell through a junction box. The review hopper is driven by the self-propelled car, and the review hopper also plays the role of the aggregate hopper.
In order to reduce investment and reduce costs, make full use of the existing workshop and equipment, the premix preparation and finished product preparation are arranged on the same production line, the front 12 silos are used for premix preparation, the back 12 silos are used for finished product preparation. Premix and finished products can be prepared separately.
2. Hardware design of the feeder
The feeding system consists of host computer, programmable controller (PLC), weighing instrument, stroke switch, frequency converter, temperature sensor and so on. At the beginning of the distribution, the car reaches the designated hopper scale, the inverter controls the double speed feed of the screw feeder, the weighing instrument outputs the quality signal collected by the sensor to the PLC, and after reaching the set mass value, the discharge gate of the hopper scale opens and the ingredients are unloaded to the review hopper. If the quality value of the unloaded drug is within the specified range, the next material is prepared, otherwise the shutdown alarm. When all the materials in the selected formula have been prepared, the check hopper gate is opened, and the prepared materials are discharged and sent to the mixing machine to start the next cycle of the mixing process. During the weighing process, the position of the trolley is controlled by the travel switch. Because some materials need to be heated and dehumidified, there is a heating and insulation circuit on these silos, and the temperature sensor collects temperature signals at a certain interval and sends them to the PLC, which controls the silo temperature to maintain a predetermined range.
In the production process, it is often necessary to adjust the material formula according to the specific requirements of the user, and a large number of sample tests need to be carried out before the final determination of these formulas, that is to say, in the automatic distribution line also needs to have a perfect manual distribution function, in order to facilitate the preparation of various materials for the test, for this reason, the manual control panel is designed.
Under normal circumstances, the upper computer acts as the host, sending various commands and storing various data. Through PLC control process, the manual control panel completes the control process when the sample test is needed. When the upper computer fails, the manual buttons on the control panel can also be used for emergency control, and the buttons on the control panel and the upper function can achieve the same control function.
3. How ingredients work
When the host computer is used as the host control, the first choice is premixed preparation or finished product preparation, and then the formula selection is carried out. After pressing the start button, the assembly line automatically completes the collocation work, and the collocation data is stored in the real-time database of the host computer for data statistics and report printing. In the manual control panel control, in addition to choosing premix or finished product preparation, the working mode should be selected: manual, single-step operation, single-cycle operation, automatic and back to the origin. If the system is already in the initial position, you can press the start button to start the configuration; If the system is not in the initial position at the beginning, it should first select the working mode back to the origin, press the start button back to the origin, and the car will return to the origin position. Because the system can prepare both premix and finished products, there are two origin points of the system, the origin point is 0 when premix preparation, and the origin point is 6 when finished product preparation.
In the process of premixing preparation, the car starts from position 0, ingredients are added at positions 1,2,3,4,5,6 (different formulations do not need ingredients in some positions), and then goes to position 14 to discharge materials. After the ingredients are removed, it can choose to return to position 0 or position 6 according to the command, so as to start the next round of premixing preparation or finished product preparation.
In the process of finished product preparation, the car starts from position 6, ingredients are added at positions 6, 7, 8, 9, 10, 11, 12, 13, etc. (different recipes do not need ingredients in some positions), and then enters position 14 to discharge materials. After the ingredients are removed, it can choose to return to position 0 or position 6 according to the command, so as to start the next round of premix preparation or finished product preparation.
Conclusion
The system has been successfully run for more than one year, the control algorithm technology is mature, the work is stable, the anti-interference ability is strong, the control effect is satisfactory.