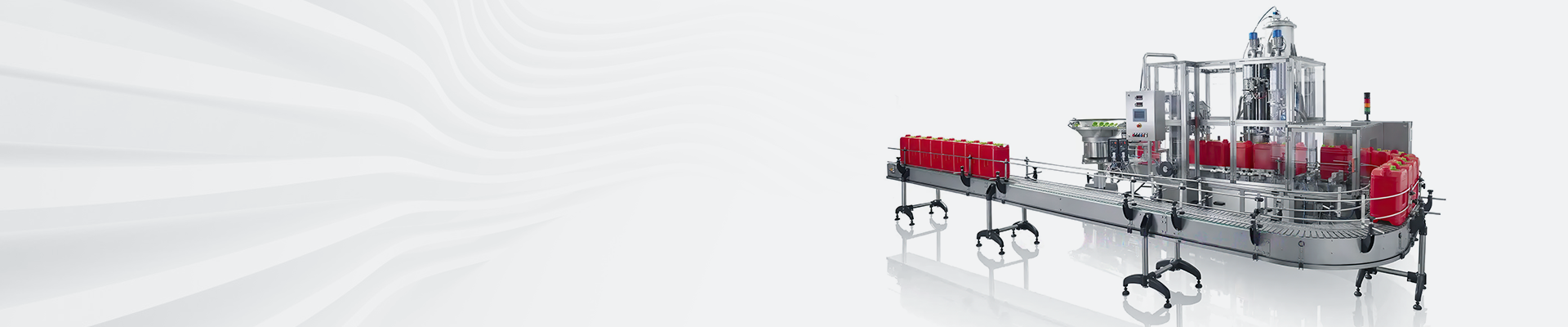
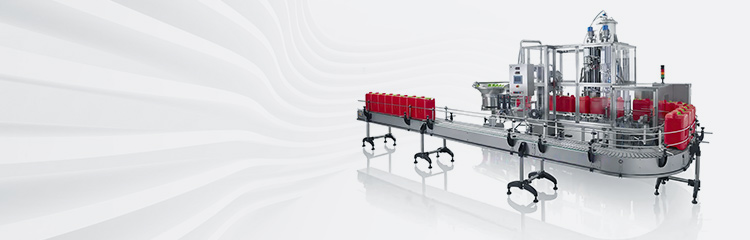
摘要:耐火材料配料系统是一个多变量非线性系统,使用传统的PID控制,很难达到理想的控制效果,本文提出了一种基于控制系统算法的耐火材料配料控制系统,它应用于本溪雅美耐火材料有限公司耐火材料配料生产线的,已成功运行一年多,实践证明,该控制系统完全满足工艺要求,取得了满意的控制效果。
概述
耐火材料投料系统是一个多变量的非线性系统,各变量间存在着耦合并且有些变量难以测量,同时,要在极短的时间内达到较高的控制精度,采用常规的PID控制,难以达到理想的控制效果。控制系统是一种基于规则的控制,它直接采用语言型控制规则,以现场操作人员的控制经验或相关专家的知识作为出发点,在设计中不需要建立被控对象的精确的数学模型,因而使得控制机理和策略易于接受与理解,设计简单,计算量小。控制系统运算速度快,系统的鲁棒性强,干扰和参数变化对控制效果的影响被大大减弱,便于实现快速控制。
控制对象的特性分析
雅美耐火材料配料系统主要工艺设备由44个料仓(44个给料机),9个料斗,11台电子秤,2台运料小车和2台混料机组成。前24个料仓里面装有状料,每6个小料仓的物料依次下到1个料斗中,由变频器控制螺旋给料机精确配料;后20个料仓里面装有粒状料,每4个小料仓的物料依次下到1个料斗中,由电震给料机精确配料。共计9个料斗,每台料斗下安装1台电子秤,每台电子秤负责各自料斗的4或6种物料的称量控制。其余2台电子秤安装在运料小车上。
根据配料系统工艺特点,在一台称重料斗秤上几秒钟内实现多达6种物料的称重、配料,传统的PID控制难以达到理想的控制效果,控制系统是比较理想的控制方法。
3控制系统组成及工作原理
耐火材料PLC控制系统采用S7-300PLC,监控功能用组态软件WinCC实现,本系统可以实现9个料斗称的配料控制,运料车的走行、定位、接料,以及螺旋铰刀机的变频控制和电震给料机的电压控制、配方生成、自动报警、故障诊断、显示、打印等功能。根据工艺要求在上位机上自动生成配方,设置各下料给定值,计算下料控制值,对其进行模糊化,根据模糊算法形成控制输出,从而实现准确配料控制。
控制系统描述
1. 自动配料机的组成
配制工艺流程如下:(1)预混配制一预混混合一烘干一预混入仓;(2)金属筛分一金属入仓;(3)成品配料一成品混合一烘干一交付下一工序。根据配工艺流程,体自动配生产线由药料仓、螺旋给料机、料斗秤、复核料斗和体配料系统组成,料仓下方对应料斗秤,为了防止漏称错称,并确保称量精度,在料斗秤下设置复核料斗,对每次称量的料进行重量复核。每个料斗秤及复核料斗上都配有3个称重模块。称重传感器沿料斗径向安装并经接线盒将重量信号送至称重仪表。复核料斗由自行小车带动,复核料斗同时起到了集料斗的作用。
为了减少投资,降低成本,充分利用现有车间和设备,将预混配制和成品配制安排在同一生产线上,前面12个料仓供预混配制使用,后面12个料仓供成品配制使用。可以分别配制预混和成品。
2. 喂料机的硬件设计
喂料系统由上位机、可编程控制器(PLC)、称重仪表、行程开关、变频器、温度传感器等组成。配开始时,小车到达指定料斗秤下方,变频器控制螺旋给料机双速给料,称量仪表将传感器采集的质量信号输出至PLC,到达设定质量值后,料斗秤的卸料闸门打开,将所配料卸到复核料斗。若卸下的药质量值在规定范围内,则进行下一料的配制,否则停机报警。当所选配方中全部料均已配制完毕,复核料斗闸门打开,将配好的料卸出,送至混机,开始下一周期的配流程。称量过程中,小车的位置由行程开关控制。由于部分料需加热除湿,因此这些料仓上有加热保温电路,温度传感器按一定时间间隔采集温度信号并送至PLC,由PLC控制使料仓温度保持在预定范围。
在生产过程中,需经常根据用户的特定要求调整料配方,并且在这些配方最终确定前需要进行大量的配样品试验,也就是说,在自动配生产线上还需要有完善的手动配功能,才能方便的对各种料进行配制试验,为此,设计了手动控制面板。
在正常情况下,上位机作为主机,发送各种命令,存储各种数据。通过PLC控制配流程,在需要进行配样品试验时由手动控制面板完成配流程的控制。上位机出现故障时也可以由控制面板上的各手动按钮作应急控制,控制面板上的按钮与上位机能实现相同的控制功能。
3.配料工作原理
上位机作为主机控制时,首先选择是预混配制还是成品配制,然后进行配方选择,按下启动按钮后配生产线自动完成配工作,并将配数据存储在上位机实时数据库中,以便进行数据统计和报表打印。在手动控制面板控制时,除选择预混配制还是成品配制外还应选择工作方式:手动、单步运行、单周期运行、自动及回原点。如果系统已经在初始位置,则可以按启动按钮开始配;若系统开始不在初始位置,则应首先选择回原点工作方式,按回原点启动按钮,小车将返回原点位置。因为系统既可以配制预混,又可以配制成品,因而系统的原点也有两个,预混配制时原点是位置0,成品配制时原点是位置6。
在预混制备过程中,小车从位置0开始前进,分别在位置1,2,3,4,5,6(不同配方在某些位置不需配料)处配料,然后进至位置14卸料,所配料卸清后,根据命令选择返回0位置或6位置,以便开始下一轮的预混配制或成品配制。
在成品配制过程中,小车从位置6开始前进,分别在位置6,7,8,9,10,11,12,13等处配料(不同配方在某些位置不需配料),然后进至位置14卸料,所配料卸清后,根据命令选择返回0位置或6位置,以便开始下一轮的预混配制或成品配制。
结语
本系统应用于雅美耐火材料厂的耐火材料配料控制生产线,已经成功运行一年多,该控制算法技术成熟,工作稳定,抗干扰能力强,控制效果令人满意。