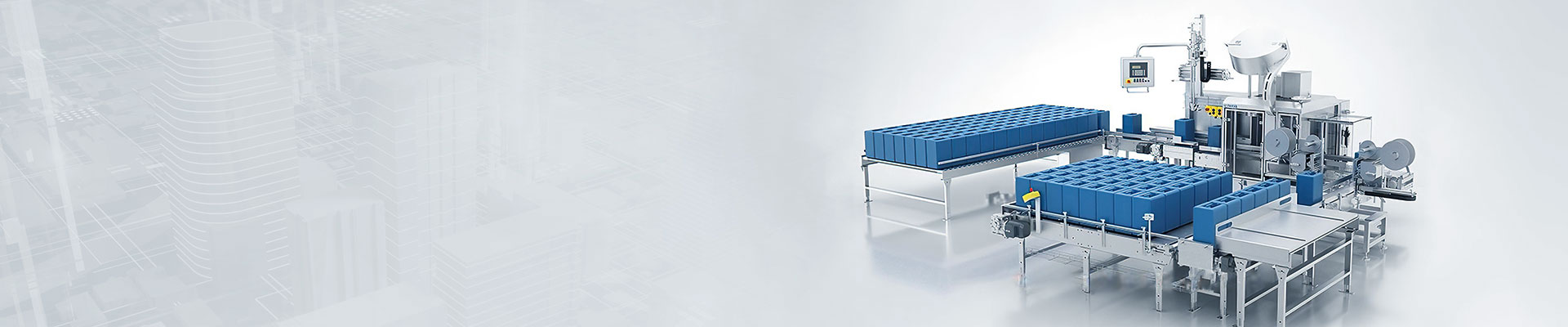
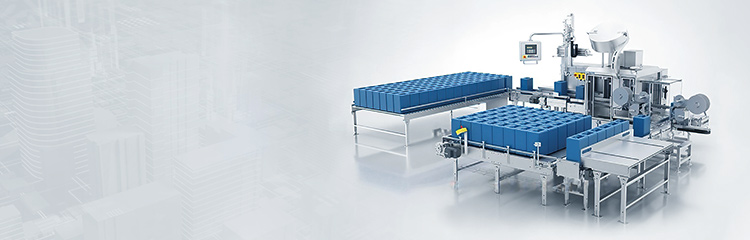
The automatic feeding system mainly completes the data state acquisition and output control of the relevant analog and switching quantities of the on-site equipment. The touch screen is used in conjunction with the metering tank PLC, which makes the application of the tank PLC more flexible. The touch screen can set parameters, display data and depict the production process in the form of animation, which makes the application of PLC visualized. The weighing system uses RS232 interface to connect the touch screen to the PLC via communication cable. The remote touch screen (HMIA) and the local touch screen (HMIB) are connected via Ethernet, both of them can display the instrument data and equipment status, and both of them can control the field equipment.

The Feeder consists of a silo, a loading vibrator, a hopper scale, a discharging vibrator and three tension metering modules. The dosing process is to supply material to the weighing hopper through the loading vibrator, and at the same time to carry out on-line metering of the material until it reaches a given value, stopping the loading process. However, the discharging metering is carried out. That is, the material is continuously discharged to the screw conveyor through the vibrator. In the discharging process, the computer samples and calculates the discharging amount according to a certain sampling period, and when the given discharging amount is reached the discharging process stops, and a dosage process is completed.
Batching machine in advance of the amount of flying material in the air after the closing of the door in the finger, the use of motor-driven eccentric mechanism to produce vibration of the material from the silo added to the hopper, due to inertia when adding material, weighing must be set in the arrival of the target weight before stopping the material motor. The difference between the target weight of the material and the weight of the material at the time of stopping the material is the advance in the feeding control. (Material advance = weight of the material after stopping - weight of the material at the time of stopping)
The amount of advance is not fixed, subject to the influence of many factors, such as the measurement of the Dosage system running fast or slow, the speed of the material falling, the size of the material particles, the viscosity of the material has a close relationship with other factors. Feeding control in advance must follow the real-time situation of the mixer automatically adjusted to ensure the accuracy of the weighing. In advance of the amount of algorithm model first of all on the signal acquisition digital filtering preprocessing, using recursive average filtering. Every time the program system calculates the advance quantity, it refers to the previous discharging historical data, thus obtaining the influence coefficients representing the speed of the material falling, the size of the particles, the degree of viscosity and other factors, automatically adapting to the operating environment, and obtaining the accurate advance quantity. The initial value of the preset advance is not necessarily close to the actual value when the machine is first started, but after a few cycles of operation, it will be automatically adjusted to suit the operating environment, so that the system will soon obtain the accurate advance without manual correction.