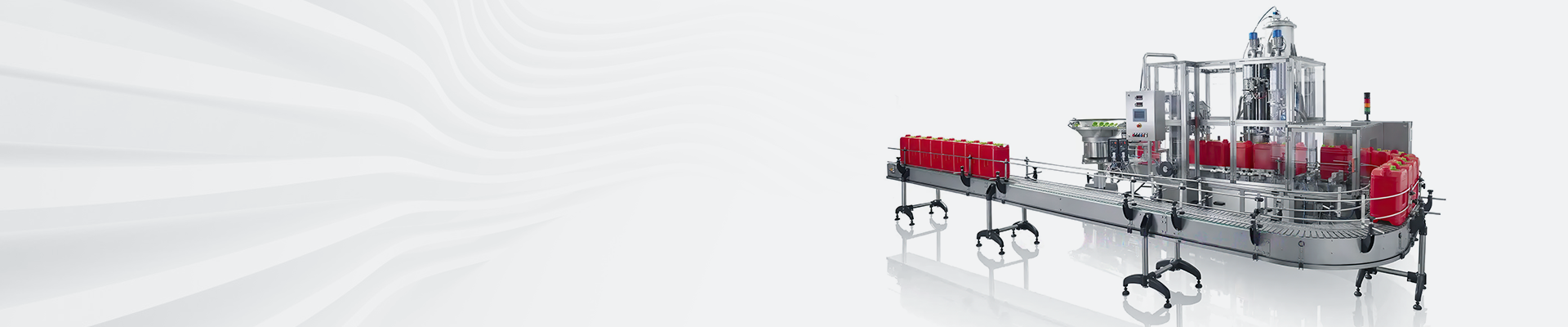
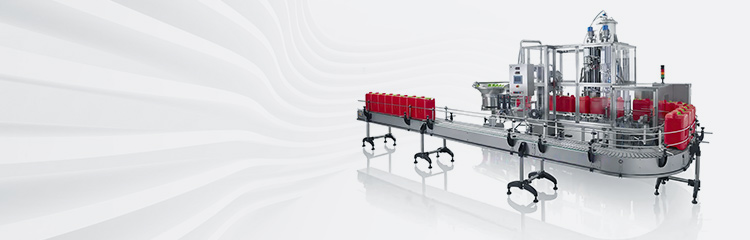

Summary:The batching system solution uses the hopper scale as the control unit. Each hopper scale has a corresponding formula setting boundary for feeding and transporting different formulas, so as to flexibly respond to the needs of different formulas for different production batch tasks.
There are many factors involved in calculating a recipe, not only do the various ingredients have to be matched precisely, but the dosage has to be accurate. Dosing and weighing systems are used to achieve this. Large scales are usually used for large components: small components require greater accuracy and in most cases large scales cannot be used. Because the proportioning weight of each small ingredient is usually less than the minimum permissible weighing value of the large scale, the accumulation of most errors will have a large impact on the proportioning. In addition, the trace components of the ingredients are usually in powder form, thus requiring the batching equipment to be well sealed. In order to produce ideal feed products, it is vital that the dosage of various feed components is accurate and repeatable. Only then is it possible to achieve a batch that is virtually error-free with respect to the designed formulation quantities. To achieve these requirements, only the use of good performance of the feeding system and reliable, correct operating methods, due to the dosage and weighing system is closely related to the use of a set of reliable, stable operation of the weighing system is also extremely important.
1 System selection
When selecting a micro-component dosing system, it is important to consider such factors as the variety of feeds to be dosed, their weights, the accuracy required, the dosing control system and the production capacity, as well as the number of batches to be produced per hour. Three options are given:
1.1 Complete manual dosing
All trace components are added manually, which has the advantage of low investment, flexibility and almost no contamination; however, the disadvantage is that it depends on the operator and is not integrated with the control system, which makes it difficult to control.
1.2 Simple micro dosing
Whether manual addition is used in this feeding system depends on the feed formulation; its advantages are economic investment, the most important components are added by a centralized feeding system, which is easy to control; the disadvantage is that it is limited to a few varieties.
1.3 Multiple micro-dosing
This system is suitable for premixed cattle production, the advantage is that all components are added through the central control system to control, before the dosage can be displayed from the database to show the ratio of values, to achieve the automation of the production process, but the disadvantage is that the investment is large, poor flexibility, as well as pollution and so on.
2 dosage system
2.1 Unloading screw
Unloading screw
The unloading screw can be equipped with various speeds. In order to ensure full outlet discharge, the screw discharge usually consists of a variety of different components, including variable screw, variable screw diameter, asymptotic screw and variable shaft diameter. Long outlets cannot be discharged with a screw because of the limited length-to-diameter ratio of the Screw Mikado. Pitch can be varied between 0.5 to 1.5 times the diameter of the screw diameter, fine grain size and has the knotted nature of the raw material, will be discharged by the screw compression, so it must be considered to take precautionary measures. If the nature of the material is not fully understood, other types of unloaders should be selected as far as possible.
Advantages of spiral dosing:
(1) The material can be conveyed horizontally, so a large-capacity batching bin and a larger batching volume can be used;
(2) Allows the use of more dosage screw;
(3) Easy to operate and maintain.
Disadvantages of spiral dosage:
(1) Horizontal transportation of materials may affect the physical properties of materials;
(2) Smaller discharge opening under the dosing silo reduces the possibility of achieving complete flow;
(3) Smaller range of dosage quantity (difference between maximum and minimum);
(4) Higher energy consumption.
2.2 Precise dosage
The Precision Dosing System consists of a stainless steel homogenizer and a dosing screw in the mixing section. It is particularly suitable for the dosage of premixes.
2.3 Grid plate
The grating consists of an upper and a lower grating. The lower grill is fixed and the upper grill is moved horizontally to accomplish the switching action. It can be used for both fine powder and granule dosage.
Advantages of grating batching:
(1) High dosing accuracy;
(2) The material can be made to flow with the help of gravity;
(3) Large outlet can be used, so that the overall flow is guaranteed and easy to configure with the silo;
(4) Grate type batching is faster;
(5) The height required under the batching bin is not large, just enough to install the grating;
(6) Cheaper;
(7) Smaller energy consumption for skateboard operation.
Disadvantages of grid plate dosage: it is not possible to move the material horizontally in the grid plate dosage dispenser, thus as the number of grid plates increases, the weighing hopper becomes bigger and the hopper is too big to be necessary.
Weighing of various trace components is done by hopper scales. The hopper is fitted with load-bearing elements. In order to ensure the rational use of the dosage device, the capacity of the scale should be accurately selected. The weighing capacity is determined by two main factors, i.e. the total quantity to be weighed per batch and the minimum quantity to be weighed. In addition, two indicators are important, i.e., invariance of the weighing value and accuracy of weighing. Weighing accuracy depends on the number of carrying elements, the error of the carrying elements and the tare weight of the hopper scale. The construction of the weighing system, hopper scale should be installed as far as possible under the dosing device, in order to reduce the proportion of airborne material column, used to improve the accuracy of the dosing, the use of weighing devices must also pay attention to prevent the occurrence of pollution, the following measures should be taken:
(1) Tank and hopper weighing should use stainless steel material;
(2) The turns are rounded and smooth;
(3) Smooth surface or brush coating;
(4) The construction of the discharge funnel should ensure that the overall flow of materials.
In short, there are several ways to achieve accurate addition of trace components, regardless of the way, the following factors must be considered: accurate control system associated with the enterprise management information system: the accuracy of the system; the reliability of the operation; as far as possible to minimize cross-contamination.