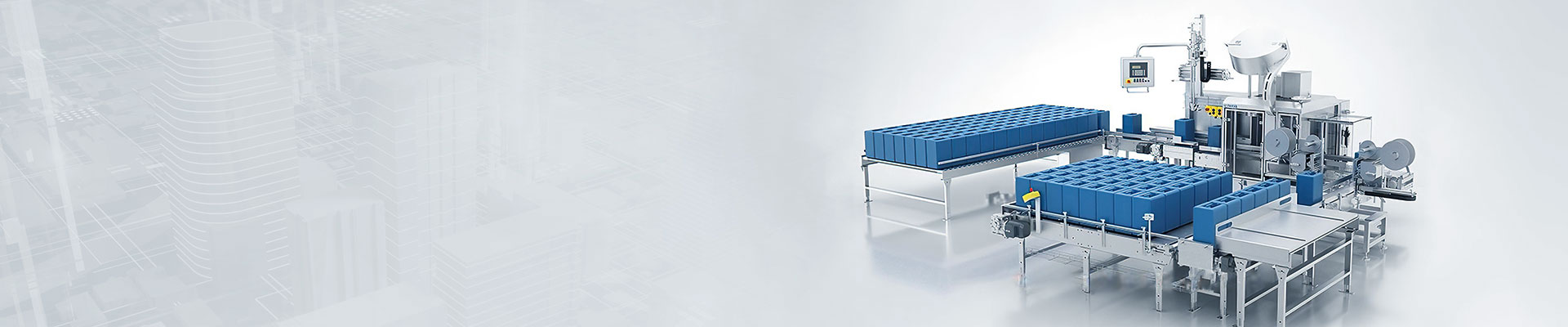
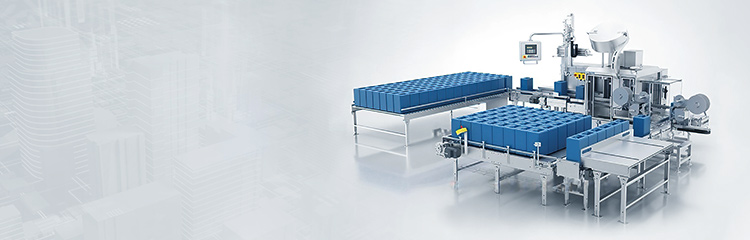
The hybrid weighing system consists of a weighing instrument connected to the CAN bus by a control module. The data acquisition module continuously collects the analog voltage signals from the sensor, converts them into digital signals through the internal amplification A/D conversion, and transmits the digital signals through the communication sub-module to the CAN bus for reception and processing by the corresponding display and control module on the CAN bus to complete the dosage and satisfy the needs of weighing. The data acquisition module consists of signal acquisition and processing sub-module, communication sub-module and power supply circuit. It receives the information sent by the sensor data acquisition module through CAN bus, converts it into weight value, and then displays the weight and sends the corresponding control information through the processing of the main program.

The spiral is one of the most commonly used methods of dynamic weighing and filling in hopper scales. In the quantitative weighing device, the motor-driven screw feeding mechatronic equipment (commonly known as the winch motor) is placed between the silo and the hopper, and the electronic measurement and control device realizes the dynamic quantitative weighing of the powder material, and when the winch motor is activated, the powder material in the corresponding silo enters the hopper along with the rotating of the screw feeding mechanical mechanism. The hopper and the weighing frame are equipped with three strain-type Weighing modules, the weight of the hopper is directly converted into electrical signals by the weighing module group and sent to the electronic measurement and control device, and when it reaches the set weight value, it will shut down the screw motor to stop feeding and control the hopper door to open for discharging, which is to complete a dynamic charging and quantitative weighing.
The feeding system has accumulated excellent technology and experience in opening bag, unloading, conveying, measuring, proportioning and filling of powder in various environments, and has carried out technical modification in the original feeding system, which puts forward various requirements for data acquisition, automatic control, operation monitoring and operation management. The weighing control system utilizes explosion-proof Electronic scales to realize the precise control of the mixing process, and drives the material to the destination reached by drawing the material into the feeding pipe using negative pressure. Its main workflow is as follows:
1. By activating compressed air or inert gas, a high velocity airflow is formed and a negative pressure area is created.
2. During the conveying process, the material is sucked into the airflow and suspended in the airflow, and then pushed into the conveying pipe.
3. The material moves at a high speed in the pipe and is quickly transported to the target point by gravity and air force.
4. A separator needs to be installed at the conveying target point in order to separate the airflow and material and send the material into the target container.
Suction pneumatic conveying machine can effectively improve the material conveying efficiency, and is suitable for a variety of different viscosity and density of material conveying, easy to clean and maintain, is a widely used in many industries a material conveying method.