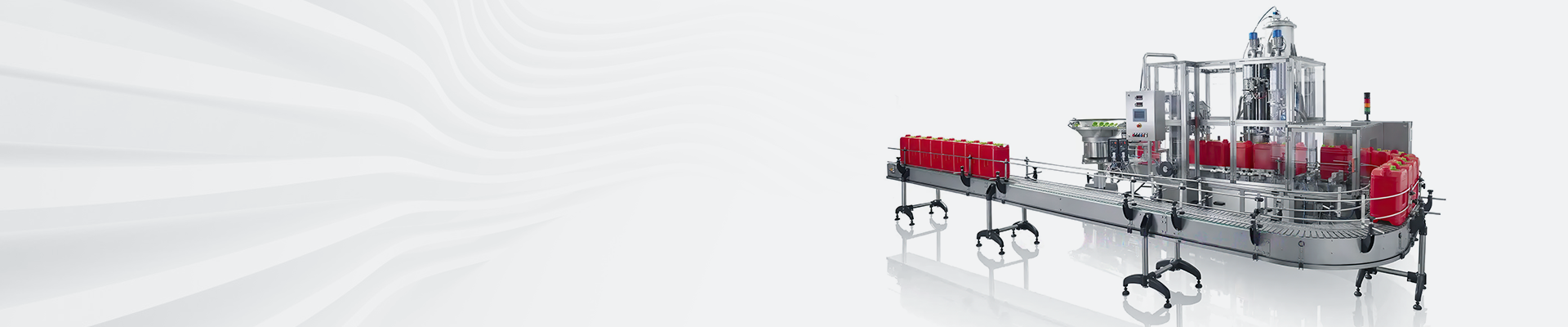
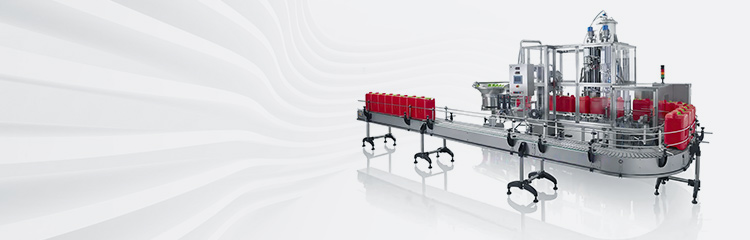

Summary:The automated batching system adopts a three-level control method: upper machine station → PLC → weighing instrument.The silo is divided into three specifications: large, medium and small according to needs to better control the accuracy and feeding frequency, and adopts a horizontal spiral variable speed feeding method.
Friction material plays a vital role in the braking process of automobile, and the proportion and dosage accuracy of automatic dosing system directly affects the driving safety and braking effect. Friction material automatic weighing device for automotive friction plate production line is self-evidently important, in the realization of automation, safe and stable production and energy saving play an important role. At the same time, it is also an effective way to improve product quality and yield, prevent dust pollution and reduce labor intensity. Therefore, the automatic weighing device for automotive friction materials has been carefully designed to improve the weighing efficiency and accuracy, realize the dust-free loading of the system, and the weighing system has a good human-computer interaction capability. This product has good usability and application prospect in the production line of friction material.
Design of automatic feeding machine
According to the requirements of automobile friction plate production line mainly includes hopper, feeding device, feeding device, weighing module, power source and control device. Using PLC system control, it can realize the continuous working cycle of automatic material picking, material conveying, material quantitative weighing and automatic feeding cup. And on the basis of the previous common control mode of dynamic weighing, comparing its advantages and disadvantages, the design of the dual-core weighing mode of operation.
The loading system adopts DCS control system, the whole system of pneumatic, stopping, running in the control room for control and monitoring; the overall equipment with fault detection system, the rear section of the equipment failure, the front section of the equipment comes to a stop, and display the location of the fault point and the reason, with alarm lamps to show the system operation status; control mode adopts three-level control mode: on the machine position → PLC → dosage instrumentation. The control interface is simple and clear, with animation displaying the dosage process and dosage data, which is clear and eye-catching; the personnel in the control room contact with the field personnel through the intercom.
The working principle of dual-core weighing
The working process of dual-core weighing is divided into three stages: (1) material preparation stage (2) coarse weighing stage (3) fine weighing stage. The last two stages are executed cyclically after the machine is started until the end signal is given and the whole process is finished. Firstly, the operator will put the weighing cup to the position 1 of the conveyor belt, and the conveyor belt will bring the weighing cup to the outlet of the coarse weighing unit, i.e., position 2, and touch the travel switch; at the same time, the coarse weighing unit will start, and when the travel switch and the preset value of the coarse weighing meet the requirements, the coarse weighing unit will open the outlet, and the materials will fall into the weighing cups; and then it will be delayed for a certain period of time, and let the materials of the coarse weighing unit fall down as much as possible, and then the coarse weighing unit will start. Then by the pushing mechanism will weigh the material cup pushed to the fine weighing unit of the material outlet, that is, the position and touch the travel switch, at this time the fine weighing unit to repeat the action of the coarse weighing unit, to complete a coarse weighing and fine weighing process. In the push device will be the first weighing cup pushed to the fine weighing unit of the outlet, coarse weighing unit and do not need to wait, directly start the next coarse weighing, in the fine weighing unit to accept the drop of the weighing cup by the push mechanism will be sent to the location of the discharge table. Dual-core weighing can make the coarse weighing and fine weighing at the same time, with convenient operation, accurate and reliable measurement, high production efficiency and so on.
Design of feeding device
Weighing and mixing machine adopts double screw structure conveyor, the double screw structure is installed in a "8" type body, with the spiral rotation, the material in the body is subject to a forward thrust forward movement, at the same time in the process, the material is squeezed, so that the body produces a certain sealing effect, and then produces a certain amount of Sealing pressure, so this conveying structure for conveying powder, paste, cake and other wet materials have a very good effect.
Control system design
The control system mainly includes signal input and conditioning module, data acquisition module, dosage control and calculation processing module, input and display module, motor drive module and discharge valve drive module. The load cell converts the weighing signal into a voltage signal, which is amplified and adjusted by the transmitter, and then converted into A/D by the data acquisition card, and the digital quantities generated are processed in the dosage controller, which can be shown in the display, and at the same time can provide feedback to regulate the coordinated actions of the motor, the pusher, and the unloading valve. The preset quantities are entered into the controller from the keyboard.
System Circuit Design
The system is powered by circuit breaker QF2 to control the main circuit of the system. The machine is turned on, and after the weighing system is started, PLC controls KM1 and KM2 to close, and the motor M1 driving the stirrer and the motor M2 driving the conveyor belt are started; these two motor splits are connected to a fuse FRI and FR2, respectively.The motors of the coarse and fine spiral feeding device are controlled by a VFD004121A inverter, and the control switch of VFD004L21A is controlled by a PIC.
Powder type of vacuum feeding device, in the design of the material feeding device selected spiral feeding system, the whole device of the feeding, feeding system sealed connection, good control of dust flying. Reference to the previous coarse and fine weighing method, and improve it, try to produce accurate weighing of the dual-core working mode: that is, after the end of the coarse weighing process, by pushing the device will weighing cups pushed to the fine weighing unit, the coarse weighing process does not need to wait, directly into the next weighing cycle. Coarse weighing and fine weighing two processes at the same time, to avoid the past due to the fine weighing process affects the weighing efficiency of the entire device shortcomings. Greatly improve the weighing efficiency and practicality of the equipment.
Through the signal input and conditioning module, data acquisition module, dosage control and calculation processing module, input and display module, motor drive module and unloading valve drive module of the control system, it realizes good man-machine interaction function. Can simultaneously control multiple scales, a variety of different materials or control output operation is intuitive, clear, automatic recovery function; powerful reporting function, can be a large number of records to store all kinds of data and tabulation printing; good reliability; powerful alarm prompt function, can minimize the rate of scrap; equipped with automatic monitoring software on the line, through real-time on-line monitor, at any time to monitor the production of important information.
Foolproof, feeding layer of the silo size and material required in accordance with the material design, silo according to demand is divided into large, medium and small three specifications in order to better control the accuracy and frequency of feeding, according to the cost and service life of the choice of stainless steel or carbon steel materials; silo materials and the outside world outside the air isolation, each silo has a barn door, are maintained in a closed state, to reduce the material and the outside world, to avoid the material hand humid air Barcode identification feeding error prevention, the original information used in dosage can be traced to avoid material mixing; the top of the silo is set up with a single dust removal system, customers can choose according to demand for the top of the silo with a single dust removal or pipeline unified dust removal to reduce material loss. Automatic dosage system all materials using horizontal screw variable speed feeding mode, the use of large auger to speed up the way to ensure that the feeding speed, the use of small auger to ensure that the slow addition of feeding precision, bin installed 40 * 40 diameter 5 mm stainless steel welded screen, filtering raw material impurities or lumps of material; equipped with material level alarm device, can be a small material dosage, as a stand-alone system operation.