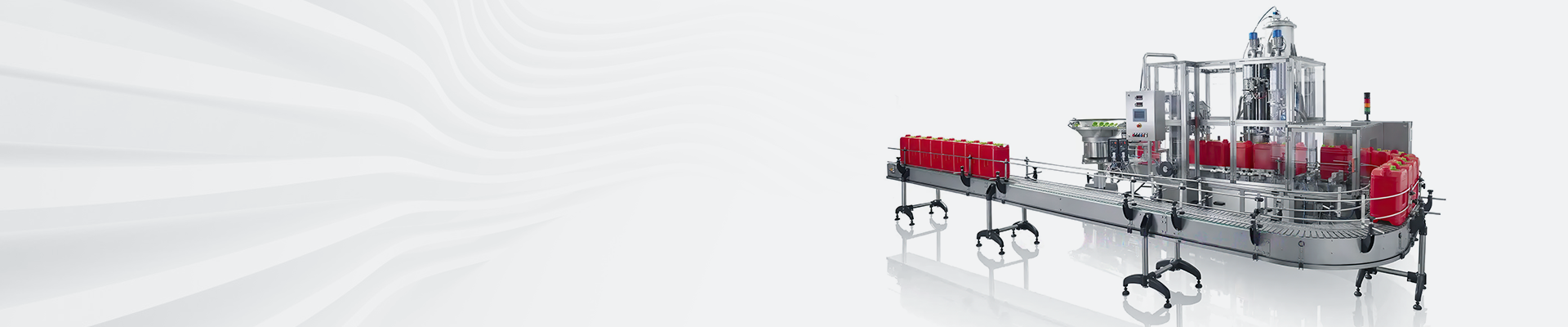
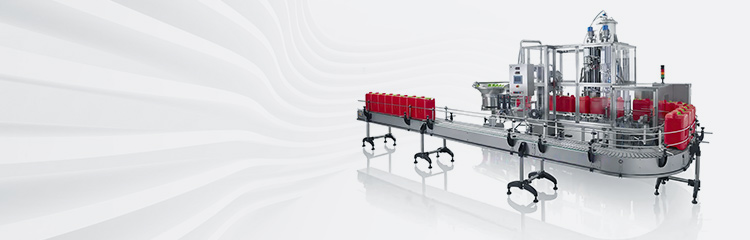

Summary:The microcomputer batching system sequentially controls all kinds of ingredients such as solvents, additives and liquids to enter the weighing reaction kettle, in which dry materials are metered by a vibrating plate, powder materials are metered by a screw feeder, liquid materials are metered by a hydraulic valve, and paste materials are metered by a pump. For each ingredient, coarse material and fine material are used successively to ensure the weighing accuracy of 98% ~ 99%. The weight of the material is converted into an electrical signal by the three weighing instruments installed on the supporting frame and suspended in the weighing reactor, which is read into the computer for weight calculation after A/D conversion, and the result is compared with the set value after tare removal, which serves as the basis for controlling the material switching or the conversion of coarse and fine feed.
1 Introduction
A lubricant factory in 1985 from Germany SIMON Electronics Company introduced a microcomputer with the metering feeder 116EM type production line for lubricant production. Due to the introduction of a longer period of time, incomplete drawings, foreign maintenance inconvenience, etc., from time to time due to the computer control part of the failure to affect the production of the situation occurred. From improving the proportion of localization, saving foreign exchange, convenient maintenance, to ensure production, this paper should be requested by the factory, in the performance of imported devices and electrical signal timing on the basis of a thorough analysis of the development of embedded microcomputer based on the 80318031 automatic automatic dosage system, the system from the performance requirements, signal timing to the appearance of the size of the imported devices are fully compatible with the successful realization of the imported control systems Localization.
2 metering feeder weighing and metering feeding principle
After starting the pre-set metering feeding program, the metering and dosing system first weighs and stores the tare weight of the weighing reactor, and then controls various ingredients such as solvents, additives, liquids, etc. to enter the weighing reactor in turn, of which the dry materials are metered with vibrating disk feeding, powder materials are metered by the screw feeder, liquid materials are metered by the hydraulic valve feeding, and pasty materials are fed by the pump. Each kind of dosage is successively fed with both coarse and fine materials to ensure that the weighing accuracy reaches 98% to 99%. The weight of materials installed in the support frame suspended weighing reactor of the three weighing instruments into electrical signals, read by the A/D conversion into the computer for weight calculation, remove the tare weight and set the value of comparison, the results as a control of the material switching or coarse and fine feed conversion basis. Completion of the weighing of the mixture through the valve discharge to the heated reaction tank, stirring, and then pumped into the dissolver, into the dissolution of sugar production process.
3 dosage function requirements
In order to ensure the performance of the original imported device, the requirements of the metering feed automatic control dosage system has the following functions:
(1) Realize up to 5 kinds of raw materials in the sequence of automatic weighing, stirring and discharging at regular intervals;
(2) Arbitrarily set the weighing value within the range of total weight not exceeding 135kg;
(3) Accumulate the shift dosage of 5 kinds of raw materials;
(4) Self-inspection of ingredients at the end of each weighing cycle and the ability to execute the inspection command at any time;
(5) Can pause the automatic weighing at any time;
(6) If the formula of a certain raw material fails, it can skip the dosage of that raw material;
(7) Fault alarm function:
No compressed air alarm, dosage system stops running;
Motor coupling fault alarm, the dosage system stops running;
The dosage system stops running if the dirty material in the reaction kettle is weighed more than 10kg;
If the liquid level of reaction tank exceeds the set value, the dosage system stops running;
(8) Display: net weight, gross weight, self-check/check value, etc;
(9) Indication: upper and lower weight limits, dosage system failure, etc.;
(10) Automatic / manual switching;
(11) Printing: fixed format automatic printing and single reactor, a single raw material data printing.
4 dosage hardware structure
According to the above functional requirements of the dosage, through the original device sensors, electrical signal analysis of the implementation of components, and taking into account the installation conditions, hardware design based on low-cost, localization, the use of MCS-51 series of electronic scales 8031 for the CPU, connected to the A/D, keyboard / display, dial dial, printer and other interface circuits composed of the dosage system design program.
The whole system consists of the CPU board, A/D conversion board, switching I / O board, display / keyboard, printer interface board, dial pad input board and power supply board. 6 boards in the form of plug-in installed in two drawer-type chassis, embedded in the original device of the weighing instrumentation parts, to achieve the electrical connection with the original device.
The 8031 minimum system consists of a 2764EPROM and a 6264RAM extended by 8031 through a bus driver, and the A/D converter adopts a double-integrated 12-bit A/D converter chip ICL7109 and the corresponding auxiliary chip, which has the advantages of high accuracy, low drift, and strong anti-jamming ability, etc. The 8279 is used as the keyboard/display board, and the 8279 is used as the input board and power supply board. The 8279 is used as the keyboard/display interface, and the CPU handles the key application in an interrupt mode. Five four-digit BCD dial through two levels of decoding, its control terminal and 8421 digital terminal through the 8255 connected to the CPU. Switching I / O and printer interface are also realized by the 8255. System in the premise of ensuring functionality reflects the principle of economic efficiency, based on domestic.
5 dosage software design
Dosing application software in the DVCC-52 and PC machine under the joint development of dosage system, using assembly language and BASIC language mixed programming, modularization, structured design method. The whole program consists of dosage system diagnostic module, automatic dosage module, A/D and data processing module, over-limit alarm module, keypad, display, print module and so on. Each module is relatively independent and complementary to each other, so that the sampling, computing, control, display, parameter setting and other organized, slow and orderly operation. In the weighing accuracy, key response speed, fault alarm ability, etc. have reached the automatic measurement of feeding requirements. Block diagram of the main program. Among them, the diagnostic subroutine includes CPU instruction system diagnosis, RAM diagnosis, EPROM diagnosis, A/D, I/O template diagnosis, and detection of sensor signals in order to achieve the fault alarm function of the dosing system.
The main block diagram of the automatic dosage subroutine. Considering the vibration and inertia of the feeding device, the program adopts comparing the weight increment Δg within two sampling time intervals Δt with the difference e between the set value and the weighing value, and according to the comparison result, switching between coarse material, fine material and changing material is carried out to improve the weighing accuracy. And one unit is used for dosage sequence counting, so that 5 kinds of dosage can share the same program to optimize the program structure and save the program memory space.
The CPU handles the key request by interrupt. In the keyboard interrupt service subroutine, key recognition is performed and the corresponding bit flag variables are set. And each other function module controls the program direction according to the flag variable status.
6 Ingredient Reliability Design
This system is in the complex industrial site with more disturbances, therefore, in addition to adopting hard measures such as optoelectronic isolation, power supply filtering, shielding and grounding and ground processing, as well as using the average value plus median value composite filtering method to overcome the cyclic disturbances and spiky disturbances in the signal acquisition, hardware self-diagnostic technology and software anti-jamming technology are also adopted in the design to ensure the weighing control accuracy and reliability of the dosage system.
6.1 Hardware fault self-diagnosis technology
This system adopts self-diagnosis method combining power-on self-diagnosis, timed self-diagnosis and key-control self-diagnosis for the key hardware to discover system failure in time and ensure the accuracy so as to avoid the system running with disease. Specific diagnostic items are:
(1) CPU instruction dosage system diagnosis 8031 instruction dosage system can be executed correctly is the dosage system normal work of the premise, for this reason designed a test program involving a variety of instructions, to determine whether the results of its operation is correct, in order to exclude the possibility of CPU malfunction.
(2) RAM diagnostics to take to the key RAM area in order to write and read out the operation, compare the read out and write the same content to determine the internal and external RAM chip is good or bad. Power-on destructive test (without protecting the original content), reset, key diagnostics using non-destructive test (to protect the original content).
(3) EPROM diagnostics curing the target program EPROM in the use of long time, window sealing is not good, etc., there may be individual sporadic unit information changes must be actively checked. This paper adopts the “different or sum” checking method. In the program before curing, the use of development equipment to find out all the instructions of the different or and write the results into the last empty unit, diagnosis, and then seek all the instructions, including the “results” of the different or and, if the number of and zero, you can assume that the contents of the EPROM is correct.
(4) The use of hardware redundancy and joint diagnostic techniques for diagnosis of A/D, I/O templates, important parameters sensor diagnosis.
6.2 Software anti-interference technology
When the CPU itself is disturbed, the program counter PC due to interference and change the content, the CPU will not be able to execute the program according to the normal state, thus causing confusion, resulting in the so-called program “flying” phenomenon. For this reason, instruction redundancy, software traps, and pure software watchdog technology have been adopted in the software to control the program flow.
(1) instruction redundancy When the CPU is disturbed, it will cause confusion by treating operands as instruction codes. Analysis of MCS-51 instruction batching system, most of them are single-byte instructions, the longest of which is no more than 3 bytes. When the program bounces to double-byte and three-byte instructions, there is a greater chance of continuing to make mistakes, while when it bounces to single-byte instructions, the program will automatically be brought into orbit. Therefore, three empty operation instructions (such as transfer, subroutine call and instructions vital to the working state of the batching system) are inserted before the instructions that determine the flow direction of the program, and the jump instructions are redundant once to ensure correct execution. Command redundancy technology can reduce the number of bullets flying and bring the program into orbit quickly.
(2) Software Trap When the program flies to the non-program area (EPROM unused area, data area ...), redundant instructions will be powerless. For this reason, a software trap is designed, that is, three instructions NOPNOPLJMP3 are inserted at the program breakpoint (after the unconditional jump instruction and the return instruction) and at the end of the data area. Fill the blank area with LJMP instructions and force the captured program to the entrance of the error handler. The main function of the error handler is to restore the batching system. Because the operation code of LJMP instruction is 02H, if the entry of the error handling program is arranged at 0202H, a large blank area of the program can be solidified into 020202 conveniently by using the Debug function in the development batching system, so that a large number of traps are handled.
(3) Pure software Watchdog If the instruction bounces in the program area, but an infinite loop is formed before encountering redundant instructions, both instruction redundancy and software trap will be invalid. Therefore, this batching system uses the idle timer T2 to design a program running monitoring batching system (watchdog). Set T2 as a high priority, determine the timing constant of T2 and the count value of the counter according to the cycle period of the main control program, add 1 to the counter every interruption, and judge that if the count value is greater than the set value, it will be transferred to the entry of the error handling program. At the same time, the counter is cleared in the main program. In this way, the program is guaranteed to be liberated from the infinite loop in time.
7 concluding remarks
Combined with the actual situation of the factory, an automatic batching system is designed with economical 8031 and peripheral chips to replace the original imported control device. After several years of operation, it has been proved that the batching has complete functions, stable and reliable operation, simple operation and high performance-price ratio. This technology prolongs the service life and creates good economic benefits.