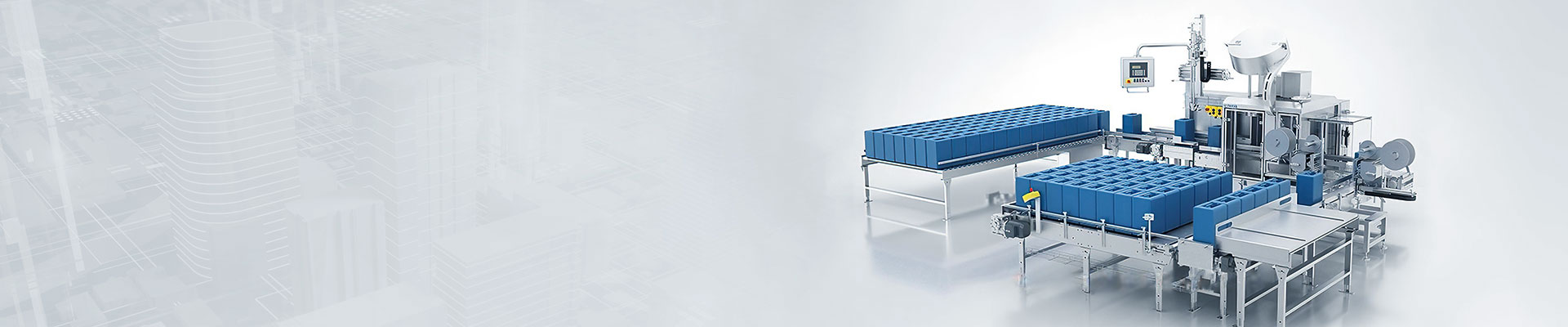
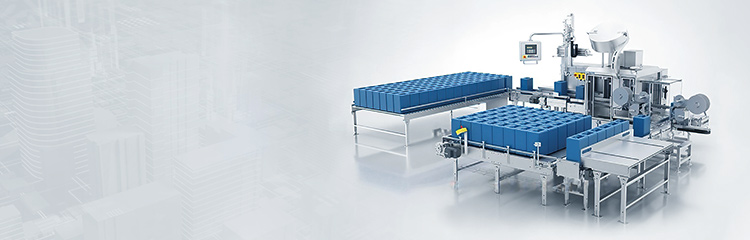
The spiral weighing system uses the human-machine interface to input the corresponding ratio parameters, transmits the signal of each weighing scale to the weighing instrument through the weighing sensor, and then connects to the central controller through the weighing instrument conversion signal. The central controller controls the feeding time and feeding amount of each material according to the real-time data of each weighing machine in combination with the formula set. All are entered into the horizontal mixer, after full mixing, through the vacuum suction machine or gravity into the main screw.

Spiral weigher mainly consists of pre-feeding feed screw (can also be used impeller feeder and other pre-feeding equipment), weighing screw (or metering screw), weighing module, weighing instruments, frequency regulator and electrical control cabinets and other components.
The feeding screw is adjusted by the frequency converter speed controller to regulate and control the feeding volume, so that the metering screw reaches the instantaneous flow rate set by the system. When the metering screw is running at constant speed, the instantaneous material load in the spiral tube is measured by the load cell, and the material gravity is converted into a proportional electrical signal input to the controller, which automatically adjusts and controls the material flow through signal processing, arithmetic, flow rate display and according to the set parameters.
Screw weighing system is mainly applicable to powder color matching function and functional granule batching, injection molding, extrusion, plastic molding and other industries, usually used for more than two kinds of ester granule raw materials in proportion to do batch mixing, and program control to make batch mixing to do continuous action, so as to achieve the mixing ratio to get uniform performance. Weighing system adopts human-machine interface to input the corresponding proportioning parameters, through the load cell to each weighing scale signal transmission to the weighing instrument, and then through the weighing instrument to convert the signal and the central controller connection, the central controller combined with the setting of the formula according to the real-time data of each weighing, to control the charging time of each type of material and the amount of materials added when all the raw materials are weighed and finished, are entered into the horizontal mixing machine, after sufficient mixing, through the vacuum suction machine to make continuous action to achieve a uniform mixing ratio performance. When all the raw materials are weighed and finished, they will enter into the horizontal mixer, and after sufficient mixing, they will enter into the main screw by vacuum suction machine or gravity. The Dosage system can weigh up to 8 kinds of granular raw materials, and the error of mixing ratio of each batch (according to the size of the set ratio) is controlled within ±0.1-0.5%F.S.
Functional features:
Suitable for multi-species and multi-color, often changing auxiliary materials, and need to pre-mix the occasion.
Intelligent operation interface in Chinese, more convenient to modify parameters.
Modular design is easy to disassemble, simple and quick to assemble, easy to disassemble and clean the main parts including mixing device.
Separate weighing of main and auxiliary materials, improving weighing accuracy and speed.
Fast material change/cleaning without residual material
Adopting advanced anti-vibration technology, solving many problems caused by vibration on site and improving weighing accuracy.
Combined with the multi-station feeding system, it can quickly form an automatic production line.
Abundant communication interfaces: RS232/485, MODBUS fieldbus, DP bus, meanwhile it can be connected to the main screw system or enter into the DCS system to realize the remote management of the equipment on the computer.