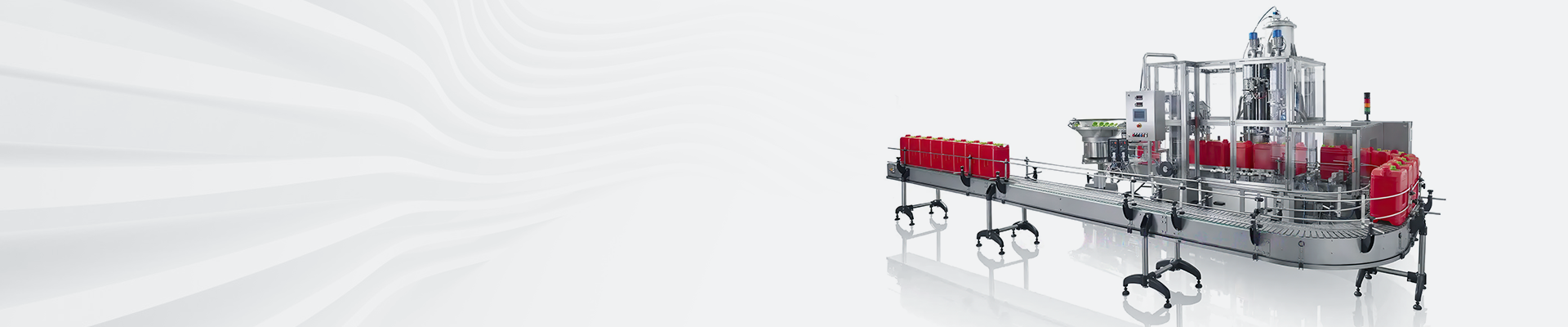
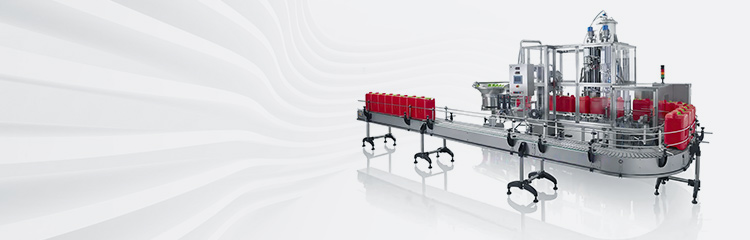

Summary:The batching system is an intelligent, multi-functional batching control system specially designed for the automation industry, which can automatically control the entire production process to achieve production data management.
In metallurgical enterprises, the quality control of batching is directly related to whether the ferroalloy electric furnace can smelt qualified products. The dosage accurately loads the materials required by the electric furnace into the raw material warehouse according to a certain proportion, and the dosed materials are added into the furnace through the material transportation trolley in order to meet the demand of normal production of ferroalloy electric furnace, so the dosage system is especially important in the whole electric furnace metallurgical system. Realizing the automatic control of feeding system and determining the accurate dosing ratio is one of the key links in the process control and quality control of ferroalloy electric furnace. After adopting automatic dosing control system in smelting production of ferroalloy electric furnace, it can not only improve the quality of dosing and stabilize the furnace condition, but also greatly reduce the labor intensity of the operating workers, increase the production and reduce the consumption, and improve the economic benefits, which has become an essential process link in the production. Realize the control system in accordance with the set ratio of various ores, accurate preparation, to achieve the control of the quality of various smelting products and production to achieve the automation of the production process and intelligent, multi-functional control system, can automatically control the entire production process to achieve the production data management.
In the ferroalloy electric furnace production project, the main raw materials used are wood chips (No. 1 material silo), silica (No. 2 material silo), coal (No. 3 material silo) and petroleum coke (No. 4 material silo), etc., and the dosing process as a whole can be divided into four kinds of materials quantitatively given, weighing, dropping, mixing material conveying and unloading and other four major production links, involving production equipment: material silo, hopper scales, vibrating feeder, The production equipment involved are: material silo, hopper scale, vibrating feeder, winch conveying trolley, falling material and unloading device, and so on.
Batching process: from the raw material field will be processed by the different materials transported to the feeding system in the four material silos, four vibrating feeder will be the material according to a certain ratio of quantitative fall into the weighing hopper.
Mixed material conveying process: the feeding system adopts inclined bridge type feeding, which mainly has three parts: inclined bridge, material truck and winch. When the batching is finished and the transportation conditions are met, open the drop gate at the lower end of the weighing hopper, and the mixture will fall into the transportation trolley from the weighing hopper, and then the trolley will be sent to the distributing bin at the top of the furnace through the winch, and then open the unloading gate at the bottom end of the distributing bin, and then the mixture will be finally sent to the mineral heat furnace.
The automatic feeding system consists of load cell, load transmitter, Siemens S7-200 PLC, vibration feeding frequency converter, transporting material winch trolley frequency converter, falling material unloading motor, limit switches, proximity switches, and the upper industrial control computer (IPC) and other components of the upper industrial control machine (IPC) through the PC / PPI communication cable to connect with the PLC, the real-time exchange of data, to complete the display of the field parameters, recording, monitoring and alarm functions. The weighing module supported on the weighing hopper converts the electrical signal representing the weight into a standard signal of 4~20mA after passing through the weighing transmitter, which is then collected by the A/D module of PLC. This signal will be used as the basis for dosing and counting the actual accumulated weight of the vibrating feeder.
Batching control function
The weighing and batching system adopts frequency converter to control the vibrating feeder with two speeds, so as to realize the control function of fast batching, slow batching and point batching for 4 kinds of materials, which ensures the precision and speed of frequency conversion vibrating feeding.
Control function of material transportation system
In order to ensure the correct loading and unloading of the material transportation trolley, the material transportation trolley adopts the operation mode of low→high→low speed, which largely avoids the trolley from overtopping, dropping off the bottom and so on, which directly affects the normal operation of the system. Therefore, the material car winch adopts three speeds for speed regulation. The main control requirements of the material transportation system are as follows:
1) The lower part of the inclined bridge is the loading position of the trolley, and the upper part of the inclined bridge is the unloading position of the trolley, which have strict requirements, that is, there is a requirement for the stopping of the frequency converter.
2) Install 4 travel switches on the inclined bridge, because the material transportation trolley needs 6 points in the process of ascending and descending, up acceleration, up deceleration, up in place, down acceleration, down deceleration, down in place, i.e., 2 variable speed points and 2 limit points. After the special trolley moves to the limit position, the frequency converter should brake to make the trolley stop quickly. The system is equipped with supporting brake unit and independent braking resistor cabinet, which adopts energy consumption braking to realize the braking of the winch system.
3) Since the trolley is towed by the steel cable, the start-up acceleration should be relatively small when the trolley is first started in order to prevent the steel cable from slipping;
4) A proximity switch is assembled in the winch drum part and connected to the high-speed input terminal of PLC, which uses a high-speed counter to detect the accumulated pulses of the proximity switch and convert them into the position points of the material transportation trolley from the start to the end position, so that the position of the trolley can be displayed in real time on the dynamic screen of the upper computer.
5) The multi-segment speed of the inverter is controlled by the function terminals, and when its function terminals are turned on in combination according to the binary law, the inverter outputs each segment speed 3]. The setting and execution steps of the frequency converter are as follows: set the operation control mode → set the specific control terminals → set the frequency of each segment speed → use the control terminals to determine the running time of each segment speed.
Design of batching control system
The automatic dosage system is set up in two control modes, i.e. manual control and automatic control, and the automatic control mode includes single-step and continuous mode. Manual operation is mainly used in system debugging, maintenance or when PLC fails. The automatic control mode is the normal working mode of the batching system. When automatic operation is carried out, according to the production requirements, the ratio of 4 kinds of materials is inputted into the upper computer through the keyboard, and the target value of fast batching and the standard setting value of all kinds of materials are calculated by the upper computer, and the PLC sends out a high-speed instruction to make the 1# vibrating feeder work in the high-frequency state, and the 1# materials fall into the weighing hopper quickly to improve the feeder and to increase the efficiency. fall into the weighing hopper, in order to improve the feeding efficiency, at the same time, the net weight of No.1 material is displayed on the upper computer in real time, when the material reaches the set target value of fast dosage, the frequency converter switches to the smaller vibration frequency, and vibrates the material at a slow speed; when the weighing value is smaller than the standard setting value of No.1 material (such as the difference is outside the tolerance range), PLC will automatically start the point correction, and No.1 material continues to be dosed to ensure the dosage precision; if the difference is If the difference value is within the tolerance range, PLC will output stop signal, the vibrating feeder stops running and 1# vibrating feeding ends. At the same time into the 2 # vibrating feeder. 2 to 4 material dosage process and 1 material dosage process is the same, until the 4 kinds of materials with the end, complete a batch of dosage cycle.
Since the dosage process is a dynamic process, some operations in the control process will directly affect the accuracy of the system, so the following measures are taken in the software:
1) At the beginning of each batch dosage cycle, the difference between the previously set dosage amount and the actual dosage amount is sought as the compensation value of the set dosage amount for the current cycle, in order to eliminate the accumulated error of the dosage amount of each scale.
2) The purpose of not adopting the automatic zero setting method is to facilitate the observation of the working condition of the weighing module, and to display the current weight value after powering on the machine when there is no additional weight in the weighing hopper.
Design of material transportation control system
The main control object of the material transportation system is the sequence control of the trolley, and its control flow is as follows:
After the material transportation trolley is loaded, the weighing hopper drop door is closed in place and the furnace top is ready for work, the upper computer sends out a start signal, the frequency converter is started according to the set acceleration curve, and it reaches the furnace top for unloading after acceleration→uniform speed (high speed)→deceleration→smooth stopping. After unloading is completed, the trolley descends to the starting position (i.e. charging position). Especially when the frequency converter decelerates to 0Hz, the zero-speed output point of the frequency converter should be disconnected, and the motor holding signal is issued through PLC.
Data and report management
The monitoring screen of the upper computer realizes real-time display, alarm and history record of relevant parameters and equipment operation status and forms reports, as shown in Figure 6. Especially for the more complicated data recording and statistics (such as data query, data backup, report printing, etc.) of the production ingredients of each shift, VB script language can be written in WinCC to realize data exchange with Excel files, and make full use of Excel's data analysis function to create daily and monthly reports, which can provide the relevant production management departments with reliable production analysis and decision-making basis. Provide reliable production analysis and decision-making basis for the relevant production management department. Setting up different operating privileges for different operators, only the operator who is authorized can allow related operations, the software has more than 3 levels of privilege protection.
This automated dosage system gives full play to the advantages of Siemens S7-200 PLC's flexible configuration, reliable control, convenient programming and inverter for easy speed regulation, so that the stability of the whole system is reliably guaranteed. Through the humanized intelligent settings, the operation mode is convenient and flexible, and it can accurately monitor and control the production process and optimize the production equipment and enterprise resource management; it can react quickly to the production events, reduce the consumption of raw materials, improve the productivity, and realize the automated dosage of the electric furnace.