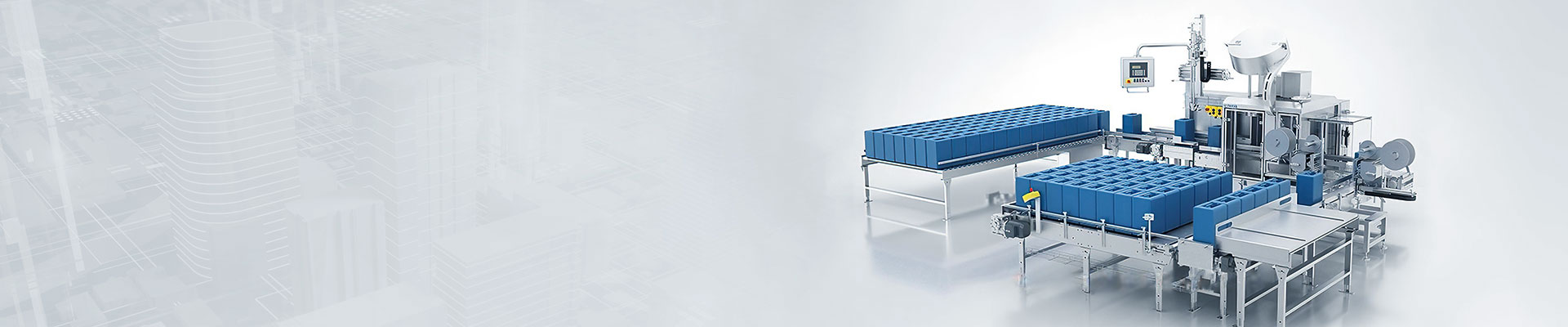
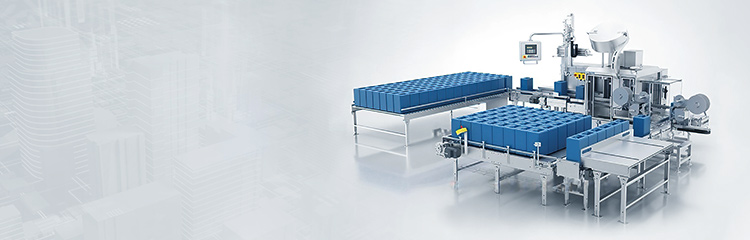
Weigh feeders are used for the automatic dosing and weighing of materials, which are transported from the storage bin to the weighing bin by means of a screw conveyor and are automatically dosed according to the set weight. The screw conveyor is the core component of the screw weighing and feeding machine and consists of a screw shaft and screw blades rotating around it. When the motor drives the screw shaft to rotate, the screw blades will push the material from the storage bin to the discharge port, and then drop down to the weighing bin by gravity.

Weighing and Feeding machine is used for automatic dosing and weighing of materials, which are transported from the storage bin to the weighing bin through the screw conveyor and automatically dosed according to the set weight. The screw conveyor is the core component of the screw weighing and feeding machine, which consists of a screw shaft and screw blades rotating around it. When the motor drives the screw shaft to rotate, the screw blades will push the material from the storage bin to the discharge port, and then drop down to the weighing bin by gravity.
The weighing and feeding machine monitors the weight of materials in real time through high-precision weighing sensors and controllers, and compares the preset feeding quantity with the actual data, and drives the system to adjust the feeding speed to realize precise control. Equipped with advanced control system and software, it can automatically manage and monitor the whole feeding process to improve production efficiency and quality.
The Feeder and hopper door are interlocked in place, and the discharge door is closed before starting the dosage, if the door can not be closed in place within a certain time after the signal is given, the PLC will generate an alarm, prompting the maintenance personnel to maintain and repair the hopper door. The dosage is divided into fast plus, slow plus, until it reaches the specified flow rate, weighing is completed to PLC request for unloading, the material door are closed in place after the PLC allows the dosage of the next kind of material, all the control is implemented by the PLC to control the interlocking, the PLC control of the smooth start, smooth stop.
Weighing and feeding machine is a kind of automation equipment widely used in industrial field, mainly used for precise control of material feeding quantity. The material is accurately weighed by its internal Weighing system, which usually includes high precision load cell and weighing controller, and can monitor the weight change of the material in the feeding process in real time. When the material is added to the feeding machine, the weighing module will sense the weight change and transfer this information to the weighing controller, which will process and analyze the signal quickly after receiving the signal from the weighing module. Based on the comparison between the preset feed quantity and the actual weighing data, the amount of material to be added further is calculated. The calculation process is usually based on advanced control algorithms to ensure the accuracy and stability of the feed quantity.
According to the calculation results of the weighing controller, the feeder will adjust the feeding speed of the material through its drive system. The drive system usually consists of a motor, a reducer, and a transmission mechanism, etc., which can accurately control the rotational speed and feeding volume of the feeder according to the controller's instructions. By adjusting the parameters of the drive system, precise control of the material feeding speed can be realized.
The weighing and feeding machine is also equipped with advanced control system and software, which can realize the automatic management of the whole feeding process. The control system can set the parameters of feeding quantity, feeding speed and feeding time according to the production demand, and carry out real-time monitoring and adjustment through the software interface. At the same time, the control system can also be linked with other equipment on the production line to realize the automation and intelligence of the production process.