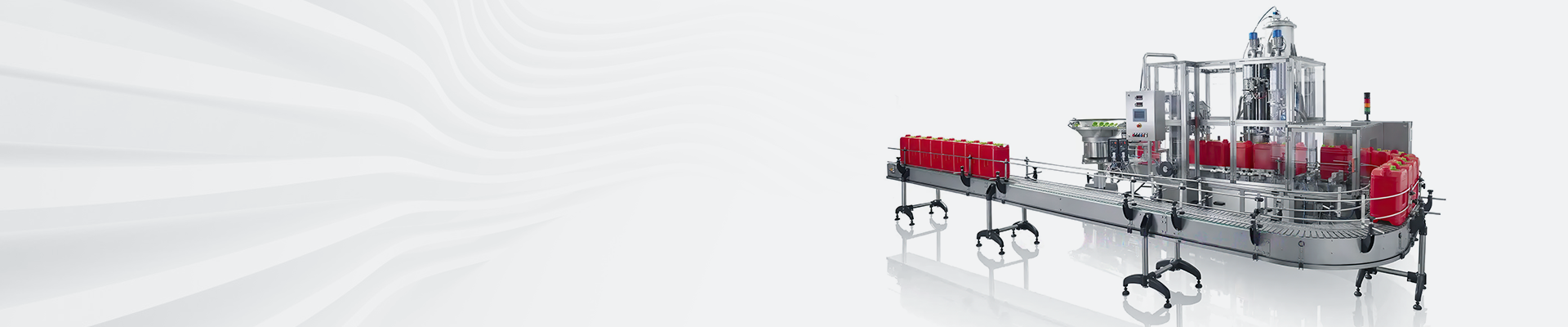
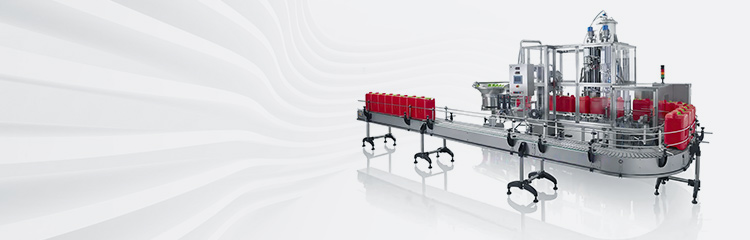

Summary:The batching system weighs and summarizes the raw materials according to the process formula. The entire batch of raw materials with good quantitative proportions is emptied and mixed through the mixer to obtain high-quality raw materials. Radio frequency identification technology can be used to clearly know the inventory status.
First, the asphalt mixing process
Understand the process in order to have a comprehensive understanding of the asphalt mixing system, through the sieving machine will be sieved into a number of hot aggregate specifications, respectively, flow into the corresponding hot material storage silo to store up. According to the set ratio of different specifications of aggregates according to the first small and then large order in batches into the stone measuring bin cumulative measurement: at the same time the asphalt supply system to send the hot asphalt and powder supply system to send the powder, respectively, according to the set ratio into their respective measuring device measurement. After weighing, the materials will be put into the mixing pot for forced mixing according to the order set in advance. The mixed finished material is unloaded into the finished material lifting trolley, which is lifted by the winch and unloaded into the finished material warehouse for storage, or it can be unloaded directly into the tipping truck for transportation of materials.
The batching machine relies on the signals detected by each weighing module to carry out real-time monitoring of important parameters such as material ratio, asphalt content, mixing temperature, etc., so as to ensure that the quality of the produced mix can meet the user's requirements. In the whole process, the electronic control system is also equipped with chain protection devices, so that the equipment from accidental mechanical accidents.
Second, mixing control process
Dosing system is a kind of production equipment used for different powder or liquid main materials and auxiliary materials in industry according to the automatic precise formula, which is usually composed of weighing system, control instrument, PLC system and upper computer. Three weighing modules installed at the bottom of the mixing tank transmit the weight signals of the mixer kettle to the junction box, which connects the weight signals from the weighing modules in parallel to the weighing terminal or weighing controller, which processes the weight signals into corresponding weight data. The weighing terminal generally provides certain input/output control functions to the field actuator, while the weighing controller generally provides the weight data and other information to the upper dosage system, e.g. PLC, DCS, etc. in a specific form. The system has the function of fully automatic weighing and distribution of powder, granule, oil and other materials according to the required production formula, which can be adapted to different specifications of 75~150L refiner, mixer, extruder, etc. It is mainly applicable to the production of large and small material formulas, and it can intelligently store production formulas, call production formulas at any time, and store production data, which is helpful for product quality tracing.
Mixing system through the PLC programming output a certain number of square wave pulse, control the stepping machine angle and thus control the servo mechanism of the dosage feed, ring pulse distributor will be programmable controller output control pulses according to the stepper motor energized order of distribution to the corresponding winding, the use of PLC to control the stepper motor and its pulse distribution can be realized by the software of the dosage, sealing, sealing, palletizing, weighing equipment, and the corresponding conveyor. The batching, capping, sealing, palletizing, weighing equipment and the corresponding conveying. In the dosage weighing process, the PLC receives the weight of the weighing module, analyzes the signal, controls the frequency and stroke of the metering pump and adjusts the dosage quantity. According to the comparison with the target standard value set by the upper computer, through the PID algorithm to calculate the opening degree required for filling, control the pneumatic valve action, so as to obtain the qualified and stable dosage weight to realize the closed-loop control.
Churning control process pavement stone requirement standard is according to the road supervisory department under the process notification, through the replacement of the sieve plate divided into their diameters, the sieve process is of course the first sieve fines, and then the small and medium and large, the order of joining the large, medium, small and fine, the four kinds of stone were added to the aggregate weighing within the scale for weighing. Weighing is composed of weighing module and weighing instrument, the instrument through the calculation of the output signal to the computer. Such as: pavement standard is given in large 300, 250 small 150, fine 100 asphalt for 50, mineral powder 150, from the program design aspect is divided into stone, asphalt and mineral powder, weighing at the same time weighing is completed at the same time into the stirring bin mixing, mixing a few minutes after the release of the trolley, the trolley upward, the trolley discharge, the trolley downward. Program design considerations:
1, stirring time;
2, the mixing bin discharge time;
3, the trolley poured into the storage tank time;
4, stirring state, set a Boolean variable, if not set a stirring variable, the computer weighing will be completed in the stirring time to add people again stone asphalt and mineral powder, set a stirring state, in the stirring (Boolean value of 1) will not be added to the raw materials, but also will not be in the stirring, the stirring of the material in the silo into the trolley;
5, stone weighing mineral powder and asphalt when they weigh 0 (of course, will not really be 0, zero range or so), and the lower bin door is closed state, and then weigh again.
Third, the monitoring system structure design
Mixing system adopts DCS centralized control mode, choose Siemens S7-300PLC constitute data acquisition control system, modular design, economical and practical. The human-machine interface monitoring software adopts the leading configuration software "Configuration King" in the field of industrial control, which has the advantages of good openness, easy maintenance and secondary development. All process control data and equipment operation status can be centralized management, real-time record, print and check at any time. The structure and function of dosing is composed of computer, cabinet and peripheral equipment (weighing mixer, pneumatic control valve, transfer pump, etc.). The structure of the monitoring system consists of a computer as the human-machine interface of the whole system. It is set as the master station to complete all the system parameters setting, process monitoring, data recording; another weighing instrument as a slave station, relying on the master station, after the main batching data setting, process monitoring. The master station communicates directly with Siemens S7300 PLC system and automatic control instrument. The weighing and batching machine adopts sealed junction box, which is dust-proof and moisture-proof, and can ensure reliable signal transmission. The instrumentation adopts special industrial process controller, which communicates with the central control room through RS-485 bus, and can be independently controlled and PLC on-line control. The signal detection of each valve position and unloader position adopts load cell, which has the characteristics of no contact, anti-interference, anti-dust and humidity resistance. The silo level adopts heavy hammer type material level meter, which can realize the continuous silo level detection.