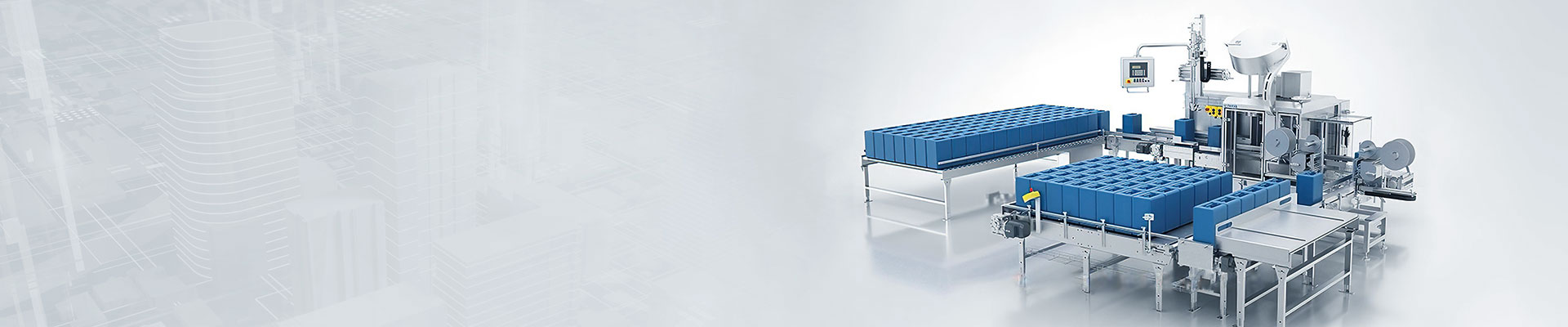
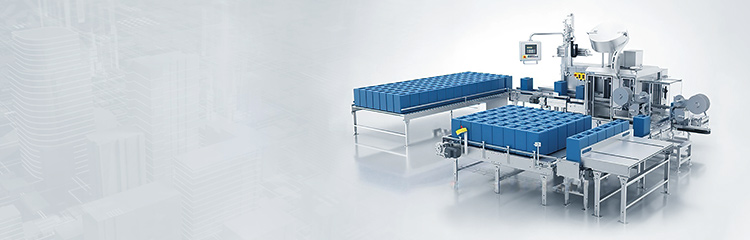
The weighing system adopts automatic/manual proportioning control, and multiple materials are mixed at the same time, with fast batching speed. The feeding sequence can be adjusted at will, formula calculation and manual correction. The graphical interface shows the working conditions of batching, and the operation is intuitive. Realize the recording, printing and report generation of proportioning data. Automatic and manual control of arch breaking. Intelligent diagnosis of sensor wiring fault, accurate positioning of faulty sensor and faulty wiring, and automatic tare tracking. Remote data browsing and printing.

The Weighing system (weighing dosing machine) can realize the proportional transportation of various materials, and has the characteristics of accurate measurement, high speed, no abrasion to materials and high measurement accuracy. It has the characteristics of high degree of automation, simple operation, environmental protection, accurate feeding and high proportioning accuracy. Through the computer control center, the whole production process can be surveyed, and the operation process can be effectively controlled, thus eliminating the possible errors caused by human operation. Widely used in pharmaceutical, food and chemical industries.
The weighing and Batching system is mainly used for industrial automation weighing and batching. The continuous conveying, accurate metering, automatic batching and automatic weighing system can realize the accurate proportioning and mixing of various materials, saving a lot of labor for production. The system is widely used in dairy products, pharmaceuticals, food, fine chemicals, coatings, PVC plastics, batteries, bioengineering and other production processes that require a variety of materials to be mixed in proportion.
Main features of weighing control system
1. Flexible arrangement and simple installation;
2, materials are transported in a closed pipeline, no dust is leaked, and the environmental protection quality is high;
3. The batching system can realize various technological processes at the same time in the conveying process, such as mixing, batching, grading, packaging, dust removal, etc.
4. Avoid being affected with damp, damaged and mixed with other sundries, avoid manual intervention and ensure product quality;
5. For inflammable and explosive materials, inert gas can be used for closed-loop transportation to improve system safety;
6. Reduce packaging and loading and unloading costs;
7. The weighing and batching system can realize intermittent or continuous conveying, multi-point feeding and multi-point discharging, with flexible scheme and wide selection;
8. Less moving parts, convenient maintenance and high reliability;
9, high degree of automation, suitable for continuous production process.