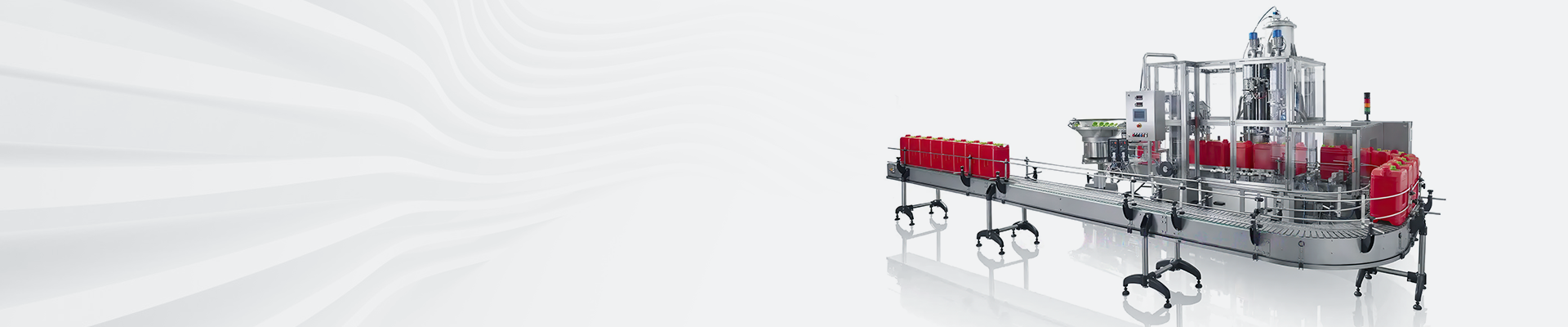
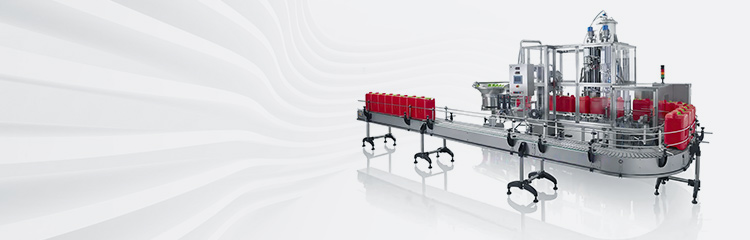

Summary:The weighing system outputs three 4~20mA current control signals, and the hopper scale sends them to the PC through RS-232 (or RS-485), which samples the three weight signals (A/D conversion), calculates the weight, and displays the weight in Chinese. status, and controls the start and stop of vibration of the hopper scale according to the weight.
Fierce competition in the domestic iron and steel industry market, increasingly busy business traditional information processing and measurement methods with large errors have been difficult to meet the needs of the actual business. In order to further improve the management level and competitiveness, make full use of the development results of computer technology and information science and technology, the company through the improvement of the blast furnace hopper scale weighing system, to complete the computer system as the basis for the formation of modernized metering and dosage system. Through the implementation of the project, a steel company's coke consumption management to provide automated means of timely, accurate, systematic and complete data and information to reflect to the customer, thereby reducing operating costs and maximize corporate profits.
1 blast furnace hopper scale weighing system design background and significance
A steel company ironworks currently has three blast furnaces, a total of eight hopper scales: 1 # blast furnace two hopper scales, 2 # blast furnace two hopper scales, 3 # blast furnace four hopper scales. Blast furnace feeding using computer-controlled hopper scales for feeding, measurement, but after analysis found that the dosing control system exists in the measurement and the actual consumption deviation is too large phenomenon, therefore, in order to effectively monitor the material casting, to improve the accuracy of the measurement, now improve the system design to achieve the hopper scales weighing control system, to achieve the consumption of the three blast furnaces coke real-time monitoring and measurement, to ensure that the data information is accurate and reliable. The system is now improved to realize the hopper scale weighing control system to realize real-time monitoring and measurement of coke consumption in three blast furnaces, and ensure the data information is accurate and reliable.
2 Deficiencies of the current system
At present, the hopper weigher will be 4 ~ 20mA signal and hopper switching bin door digital signal are connected to the L1 PLC control system, the system process is the trolley arrives at the hopper scale, open the door of the hopper to start loading, the end of the loading off the door. When the control system receives the trolley arrival signal, the hopper scale data is collected as tare weight, and when the hopper door closure signal is received, the hopper scale data is collected as gross weight, and then the system calculates the net weight to save the display and upload. However, there is a certain mechanical time difference between the hopper closing signal and the complete closing of the door, and the time is not fixed, during this period of time there is still coke loaded into the trolley, but it is not recorded in the gross weight, so each time the collected and calculated weight and the actual consumption of the weight have a large error, resulting in a large difference between the monthly cumulative amount and the actual consumption of the cumulative amount.
3 Improve the design and realization of weighing system
3.1 Improvement of system structure
Improve the system by connecting the 4~20mA signal of the hopper scale to the dual signal transmitter, split into 2 ways, one way to connect to the L1 control system, and one way to connect to the new weighing collection system. The original PLC control system's acquisition and transmission methods remain unchanged, while the new weighing acquisition system communicates directly with the weighing equipment by installing RTU devices at the site of each district and city, reads the data by using the Modbus/Tcp protocol, and then obtains the amount of coke loaded each time by using the judgment and stabilization algorithm.
The RTU devices added in each district city are connected to the backbone Ethernet through the network interface, and the system communicates with the regional RTUs through the Ethernet, using the Modbus protocol format to interact with the data at each site.The Modbus protocol defines the information structure that the controllers can recognize and use, and when communicating on a Modbus network, the protocol enables each controller to know its own device address, to And identify the data addressed to it, take out the data information contained in the packet, the controller can also organize the answer information, and use the Modbus protocol to transmit this information.
3.2 System Design and Algorithm Implementation
Add 1 STC-511RTU to each area, the dosage device uses the open Modbus/Tcp communication protocol. In order to improve data communication and processing efficiency, the software adopts object-oriented multi-threading technology to develop Modbus/Tcp based C/S architecture software, using the relevant digital and analog data acquired to carry out the corresponding logical judgment, data analysis, and save the resultant data to the SOLServer database. In order to facilitate users to query and analyze the measurement data, the system is also designed with B/S architecture, and various accumulated data, analyzed data, and report data are published on the Web through the browser to easily realize the corresponding functional operations.
When the system receives the signal of the arrival of the trolley to start the algorithm, the collected data is stored into the defined array, when the next cycle arrives, the collected data is compared with the first value in the array, and if it is within the defined value, it will run the interpolated sorting algorithm to save the value into the array. Sequential operation each time the collected value is compared with the first value in the array, according to the results to determine whether to save. If the value of 10 consecutive times (array dimensions) to meet the conditions, that the weight of the object on the hopper scale is in a stable state, you can get the tare weight and gross weight. Its intermediate value, cycle period and array dimension can be adjusted according to the actual application.
3.3 System application results
Weighing and feeding system on-line operation after 3 months of statistical data sinking as follows (unit: t), the theoretical weight is the theoretical value of the total amount of coke output from the coke oven, the weight collected by the PLC system and the measurement system compared with the following table, from the table can be seen that the measurement system statistics and the theoretical weight of the data and the difference between the smaller, improve the accuracy of the measurement.
4 Conclusion
Through the implementation of this project, real-time monitoring and statistics of coke feeding data of 1# blast furnace, 2# blast furnace and 3# blast furnace are realized, and the metering accuracy of coke consumption is improved, which meets the design requirements of the project.