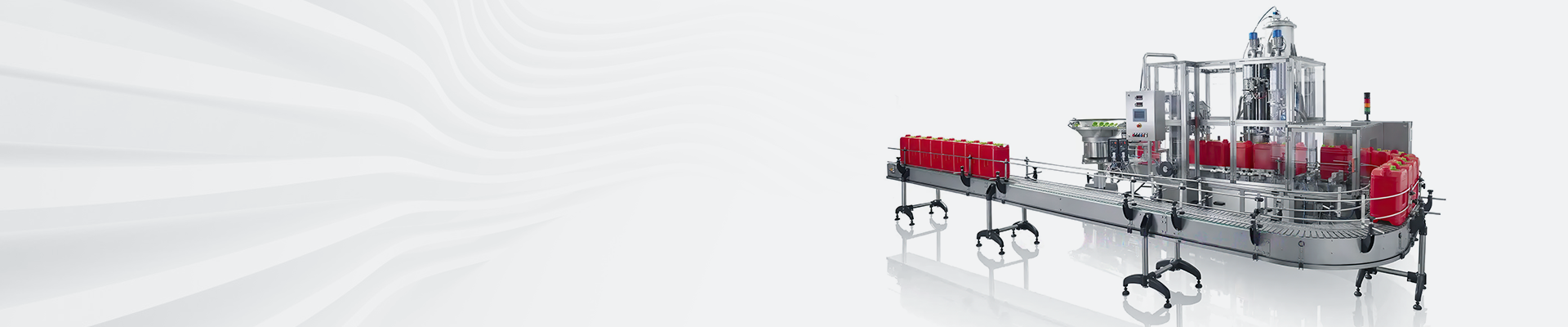
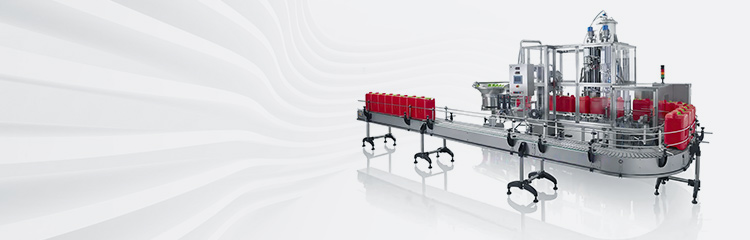
摘要:配料控制系统可以用于各种减量式给料设备的称量控制应用,通过在固定时间间隔取得物料质量的变化,可以计算得出物料瞬时流量。PID控制器利用这个流量值来控制减量式给料设备的给料量。
前言
IPA(间苯二甲酸)是生产PET瓶片的重要成分。为了连续生产高质量的PET瓶切片,需要高精度地连续测量和控制IPA,IPA的量直接影响最终产品的质量。为了确保整个过程的高效稳定运行并确保测量的准确,必须优化生产过程并实现高度自动化,申克公司的INTECONTPLUS减量给料系统能满足精确计量和自动控制。
1控制回路
连续过程的控制一般称为过程控制或过程控制,是一种具有连续调节性质的控制。调节控制通过反馈对不断变化的对象进行连续控制。流量控制回路通过在IPA范围内调节变频器输出来控制电机转速,以达到将控制流量保持在预定流量范围内的目的,采用PID控制回路,根据所需的设定值自动调节变频器的输出值。
2测量原理
INTECONTPLUS减量进料设备每隔固定时间间隔读取一次质量值,并根据前后两次质量差计算单位时间内的减量(瞬时流量),Intecontplus称重控制器将实际测量值与预设流量值进行比较,并控制螺旋给料机的转速以调整给料量。当减量秤料斗中的物料质量达到最低设定值时,加料阀将自动打开进行定期加料操作。为了确保称重结果的准确性,避免机械振动的影响,可以选择合适的滤波器在测量过程中对称重信号进行滤波,可以分别设置料位和称重值的过滤参数。
计量过程可通过3种模式实现:质量法模式、体积法模式、体积法同步模式。
(1)质量法模式:给料速率实际值由特殊的设定值来控制。最大可能的设定点与额定的给料速率相一致。如果输入了高于额定的数值,信息S8通过INTECONTPLUS输出面板显示。
(2)体积法模式:物料传送机构根据设定点的比例被控制。料斗质量的改变没有影响。在额定的条件下,给料速率与输人的设定点相一致。设定点限于额定给料速率的3倍。
(3)体积法同步模式:从质量法到体积法模式的转换平稳地进行。设定点与给料速率实际数值之间的关系比在非同步体积法模式下要更精确,如果设定点改变了也是同样。
3系统配置
上料系统主要分为三个部分:下料系统、称重控制系统和卸料单元。料斗入口与管道之间安装了软连接以减少下料振动对称重的影响,管道中安装了蝶阀以控制原料的添加。称重系统的主要部件包括:料斗、称重模块和搅拌电机,它们由支撑架固定。出料由进料电机组件、螺杆和出料管组成。当物料通过进料管进入料斗时,延伸料斗可用作物料缓冲器和搅拌器的接收器。当物料达到设定的出料量时,由进料电机组件驱动的出料螺杆按照设定的转速动作,通过出料管可以连续控制和计量IPA物料。
4计量控制过程
4.1卸料称量
卸料称重原理设计通过设计为对各种散装固体进行给料,在受控卸料下运行,如系统不计量卸料给料总量;而对测量称重料斗中的减量。灌装和称重时,系统会测量增加的质量,整个工艺路线设计为防尘密闭。装满的料斗由称重模块计量,并获得单位时间内的质量变化。这相当于卸料装置的进料速度。该进料速率可以通过特定的设定点来测量或控制。如果低于最低料斗料位,则通过进料阀开关重新填充料斗。整个卸载和称重过程分为五个步骤。
(1)MIN填充信号输出且料斗被填充。在此阶段,给料速率不能被测量且控制继续在控制的模式下。控制系统显示设定值:测量系统,给料速率保持最后被测量的平均值。
(2)ECH0加料门的讯息被监控,需要的话,事件信息被输出。
(3)MAX达到最大填充质量,填充停止。
(4)在加料门的回讯信号和设定时间TB过去以后,给料速率测量且减量式控制启动。
(5)BLOW-0UT填充喷嘴吹气移走残余物料。
填充过程也可以被暂时地控制(脉冲填充),但当达到MAX数值时立即停止。
4.2填充称量
填充称量原理与卸料称量相反。测量和控制在料斗填充时进行。有速度控制的给料单元(例如给料螺杆)和振幅控制的给料单元。2种类型对于电枢电压或振幅来说都需要一个外部的功率控制器存在,以及特殊控制线路。实际给料速率与设定值相比较,其差值被传输到RP中,控制器会持续改变卸料单元的给料速率直到实际数值与设定值相等。为加快设定值的校准,控制器通过附加的预先控制调解。
灌装称重与卸料称重的原理相反,当料斗装满时,进行测量和控制,速度控制进料螺杆和振幅控制的给料单元。这两种类型都需要外部功率控制器和用于电枢电压或振幅的特殊控制电路,将实际进料速度与设定值进行比较,并将差值传送给RP,控制器将继续改变出料单元的进料速度,直到实际值等于设定值。为了加速设定值的校准,控制器通过额外的预控制进行调节。
4.3于扰自动消除器(DAE)
在整个称量计量过程中,由于各种原因会产生2种干扰,即卸料干扰和测量干扰。
(1)卸料干扰。产生于物料的不均匀性,物料的变化以及卸料单元的非线性等。
(2)测量干扰。产生于建筑的振动,鼓风,称量触点等。
第1种干扰在测量信号和流动过程中都存在,第2种只在测量信号中存在。这种类型的干扰一定不能被输人到测量值评估和控制中。鉴于有这些类型的干扰,一个特殊的消除器已经被改进在模糊逻辑原理下操作。系统对干扰进行分类并决定需要的测量和控制介人。微分的滤波器下和控制参数作为预测干扰的一个功能进行校准,以保证只有不确定的一部分输入到测量和控制中。干扰自动消除器允许物料在不改变操作模式的情况被重新填充。如果消除器正常校准,重新填充应平稳进行。特殊的设置也能实现较为复杂的填充顺序。如果体积法给料速率是料斗料位的一个功能,控制器在质量法状态下必须连续重新校准卸料单元。为了模拟在填充时的状态,卸料单元控制幅值在此阶段被调整为料斗料位。这增加了填充阶段的给料精度并确保平稳转换到质量法状态。
4.4线性化控制
振动给料机超过它们整个功率范围就不是线性的而是呈现出给料速率向幅值累进的特征。线性化能在整个设置范围内保证控制精度并阻止在设定点步骤的下冲和过辐射。
5系统操作
自动配料系统通过INTECONTPLUS控制器实现,操作面板可以显示和设定各类参数。
程序控制整个称重过程,配置开关输入信号包括启动键、关机键、斗门状态和其他检测信号。开关输出是控制信号(如厚度进给电磁阀、排气电磁阀、夹袋等)、称重显示器、报警输出信号。数字通道接收称重模块重量输入信号。其中料斗秤关闭和夹子后夹紧测试是近距离开关,缓冲区门、料斗称和夹子后盖由电磁阀驱动和控制。在理想状态下,大供应是小供应,共同完成额定重量值的95%,在非常短的时间内完成。接着大供应停止,小供应品再生产额定重量值的5%10%,占用更长的时间。在实际生产中,这两个段的重量和时间参数必须根据情况不断调整,才能达到最佳状态。
6系统优势
整个配料控制系统投入运行以来,计量精确,控制良好,可以通过INTECONTPLUS控制直接进行参数管理并设置称量系统的预设值,可以方便地在远程设置定量给料的参数,自动获取特性曲线的使用,可实现对计量参数的简单远程调节。主要优点是:
(1)提高批量加料计量精度,不受外部因素(例如机械振动等)的干扰。
(2)分别获取和显示料位和物料质量值,可适用于不同种类、不同密度的固体粉料介质计量控制。
(3)易于集成在INTECONTPLUS系统中,使得称量和控制完美结合。
(4)易于安装并且可通过各种通讯方式读取称量数据和设置称量系统,例如可通过一个调制解调器或以太网通讯模块简单集成到称量系统。
(5)称量的数据通过背板直接送入DCS系统,节省了称量设备与DCS系统之间的通讯环节,降低了成本;同时实现了高速的远程控制功能。