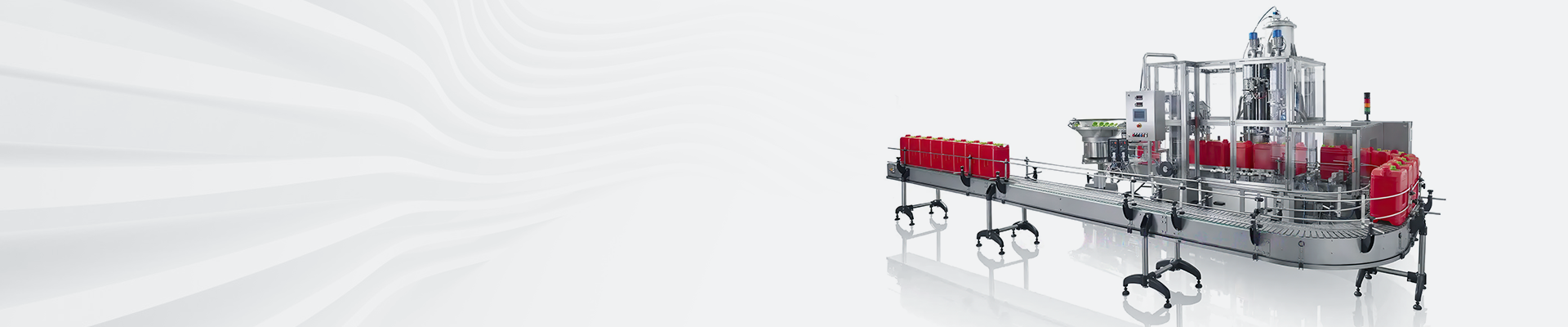
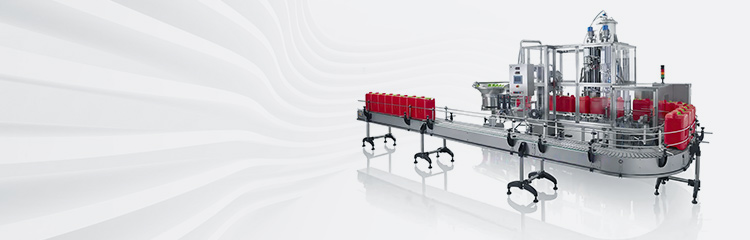
摘要:针对轮胎行业中由成型工序生产的胎坯存在质量均一性不稳定的现象,设计胎坯质量上料系统。通过组合使用动态称量技术和信息控制技术,实现质量的自动采集,同时结合正态分布等统计学算法对称量数据进行分析,对质量出现异常的胎坏及时报警。实际使用结果表明,该系统可靠性较高,有利于提高胎坯合格率。
中国作为轮胎制造大国,橡胶轮胎年产量巨大,但面临着大而不强的问题,与国际轮胎巨头的差距非常明显。由于国产轮胎价格远低于国外品牌,中国轮胎出口经常受到反倾销等贸易保护措施的影响。因此,提高产品质量,扩大高端市场份额,提高利润率是目前企业面临的问题。轮胎是一种安全产品。质量分布不均匀的轮胎在高速旋转时,不平衡的离心力会引起车身的振动,汽车的操纵性能、安全性能和乘坐舒适性会下降,而噪声会增大。
成型是轮胎生产中至关重要的一道工序,半成品零件按照工艺要求组合成轮胎缺陷。轮胎缺陷的质量直接决定了轮胎的质量,是衡量轮胎是否合格的重要指标。因此,需要对轮胎毛坯的质量进行实时监控,根据轮胎缺陷的质量标准进行在线检测和分析,筛选出不合格的轮胎缺陷并进行报警,提示技术人员进行处理,从而优化生产工艺,规范工艺控制流程,减少次品的出现,大大提高产品质量。该方案在深入分析轮胎毛坯生产工艺的基础上,开发了配套的轮胎缺陷供料系统,结合作业流程实现了对轮胎缺陷质量的有效控制。
1硬件系统架构设计
该配料系统采用分层结构设计系统。一是应用三维数字化设计制造技术,以数字化建模、调试和优化为手段,集设计、分析和数据处理于一体。利用得到的分析计算结果,确保弹性元件的结构设计最合理,性能波动最小,确保加料系统中称重模块结构设计和制造的合理性。基于轮胎衡平台制作轮胎胎具,胎具可调,适应不同规格轮胎毛坯称重,称重精度为0.15kg.称重数据通过DEVICENET总线采集。上位机通过TCP/IP网口与PLC(可编程控制器)通信,实时采集轮胎缺陷质量,异常时驱动PLC控制设备动作。设备不断调试,满足现场实际应用需求。
2称量控制流程
PLC控制系统用于轮胎缺陷质量的采集和控制,质量标准规范后,对现行PLC控制系统、驱动装置和称重控制系统进行改造,并与上位机建立通信,实现称重数据的实时采集和质量标准的判断。对不符合质量标准的轮胎毛坯发出警报,并控制设备继续动作。同时提示操作人员联系工艺人员单独处理,处理结束后对当前设备参数进行修正。配料机自动收集数据并进行分析。正态分布函数分析法广泛应用于轮胎质量控制领域,利用正态分布可以很容易地确定其值出现在任何指定范围内的概率。称重中的测量误差一般服从正态分布。使用此功能,可以进行错误分析和质量控制。
3正态分析原理及过程能力指数计算
基于胎坏质量样本的分析,采用正态分布算法可实现对数据的分析、预测,以不断优化轮胎生产过程,提高标准,为工艺改进提供参考数据。正态分布具有如下特性。
(1)正态分布以均值为中心,左右对称取值,理论上没有边界,离越远,函数值越接近于零,但不会等于零。
(2)正态分布中,曲线下面积集中在以称取值为中心的部分,越远离中心,曲线越接近轴,曲线下面积越小,超过一定范围以外的面积(概率)可以忽略。
(3)正态分布以均值为中心,左右对称,正态曲线在横轴上方均数处最高。
(4)为了方便应用,常对正态分布变量作如下变量变换,为标准正态变量或标准正态离差,位置(即均值)参数,为变异(标准差)参数。变换使原来的正态分布转化为标准正态分布。
(5)正态分布决定分布曲线在横轴的偏移位置。在一定时,增大,曲线沿横轴向右移动;反之减小,曲线沿横轴向左移动。
(6)正态曲线下的面积分布有一定的规律,即所有的正态分布曲线在左右相同倍数的标准差范围内面积相同。
(7)基于正态分布通过样本计算对应检验过程指标。通过对过程能力指数的分析和历史数据对比能够发现当前产品控制过程应该改进之处。
4软件架构功能
喂料系统可实现质量信息的采集、统计和分析。通过数据的分析,预测出偏差的原因,根据不同的原因制定对应的局部措施或者系统措施以进行规避。
4.1质量标准管理
维护胎坯质量标准,对每种胎坯的标准质量标准上限和标准下限进行统一标准化管理。
4.2设备参数管理
维护设备的各项具体参数,对秤通讯的波特率、串口、数据位、校验位、P地址和PLC的通讯参数进行具体配置。
4.3接班管理
对人员接班信息进行管理,记录人员、班次、班组和岗位,对应到机台和日期。胎坏称量时关联对应接班信息,建立追溯关系,可以根据胎坯条码追溯到接班信息和称量信息。能够从人员、班次、班组、岗位、日期和机台不同维度分析称量的合格率。
4.4质量采集
PLC与称量仪表进行通讯,将数据采集到PLC中。PLC与上位机进行通讯,将质量实时采集到数据库中保存。
4.5质量偏差报警
上位机采集到胎坯质量后,自动下载质量标准并且与其进行对应,对不符合标准者进行报警,控制设备继续动作,提醒操作人员进行处理,处理完毕后进行异常启动,继续生产。
4.6胎坯质量合格率
分析针对日期、机台、班次和班组对胎坏合格率进行分析,为合理安排生产计划和改进工艺技术提供数据支持。
4.7胎坯质量正态分布
针对日期、机台、班次、班组选取样本类型,进行质量正态分布分析,找出偏差原因,并采取措施改进,以提高过程控制质量。
4.8胎坯质量分析
针对日期、机台、物料、班次和班组进行质量分析,根据分析结果,确定影响过程性能的变差因素,并进行优化改进,以提升各项性能指标。
4.9胎坯质量报表分析
基于日期、机台、物料、班次和班组分析称量数据,能够实时展示称量明细报表、称量异常报表、异常处理报表、均值分析报表、极值分析报表、合格率分析报表和不合格率分析报表,为优化排产、改进工艺提供最优的数据。
结语
集自动称重、自动控制、信息化于一体的轮胎缺陷自动配料系统,可自动采集轮胎毛坯质量数据,根据轮胎尺寸参数自动下载质量标准,并对缺陷产品进行报警和控制,提高产品合格率。该系统与工厂信息系统无缝集成,可实现信息共享。通过该系统可以提高轮胎产品的质量,从而提高企业的经济效益和轮胎行业的社会效益。该系统已在多家企业应用,能够准确发现和避免质量不合格、缺件、错料的产品,在优化生产调度、改进工艺、保证轮胎质量等方面发挥了显著作用。