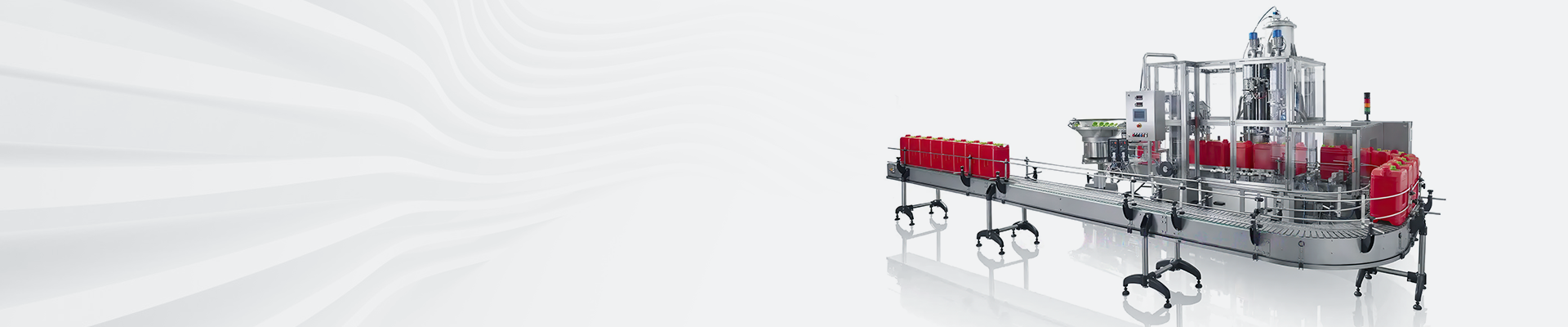
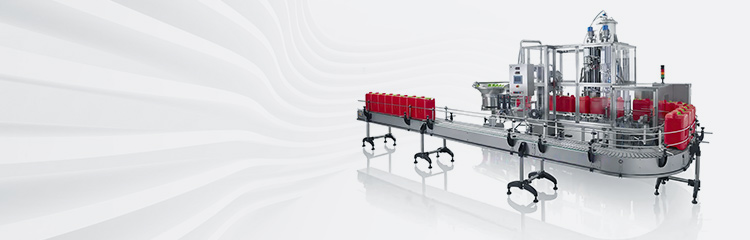

Summary:The automatic filling machine processing is transformed through process control and visualization technology. When adding additives, you only need to enter a formula, and the controller controls each step according to the definition of the formula.
The weighing and filling machine adopts the configuration software for monitoring interface, which can quickly build up the components and generate the upper computer monitoring system, through the data collection and processing of the scene, with animation display, alarm processing, process control. Real-time curve, historical curve and report output. In order to achieve the above monitoring requirements, in the monitoring interface design using Haniwa effect, flow fast flow attribute settings simulate the dynamic filling process, through the addition of standard buttons to achieve manual/automatic selection, start, stop, emergency stop and manually open the pump solenoid valve, through the setting of the label display output attributes to achieve the quality of the filling of the real-time display of the set filling quality, the filling of the number of bottles set up and the number of barrels to be filled by displaying the current configuration monitoring screen, to complete the monitoring of the operation of the filling system, real-time curves, historical curves and report output. It can realize the real-time display of filling quality setting, the setting of the number of bottles to be filled and the display of the current number of barrels to be filled.
Liquid filling machine through the weight sensing and input pulse frequency fast and slow realization, when the frequency of the pulse occurs to reduce, the speed of the stepping motor decreases; when the frequency grows, the speed is accelerated. In order to achieve the purpose of metering size adjustable and improve the accuracy of metering, requires adjustable screw speed and positional positioning accuracy, the use of stepper motor control screw speed and number of revolutions, not only simplifies the mechanical structure, but also makes the control very convenient. Without overloading, the rotational speed and stopping position of the stepping motor only depend on the frequency of the pulse signal and the number of pulses, and are not affected by the change of load.
The weighing and filling machine displays the current filling quality, the number of filled barrels and other on-site working status through the screen in real time, and the corresponding operation can be carried out on the upper computer, through the interface for the selection of the filling mode and the operation of the buttons of start, stop and so on. It is possible to change the filling quality, the number of barrels and manually remove the tare weight (i.e. the quality of the filled bottle) when using different filling barrels. In order to realize the above monitoring requirements, the monitoring interface simulates the dynamic filling process by adopting Haniwa effect and fast flow attribute settings; it realizes manual/automatic selection, starting, stopping, emergency stopping and manually opening the pump solenoid valve by adding standard buttons; and it realizes the real-time display of the filling quality settings, the setting of the number of barrels and the display of the number of barrels, etc. by setting up the display output attribute of the labels, and it also realizes the monitoring of the running status of the filling system by setting up the monitoring screen. Filling system operation status monitoring.