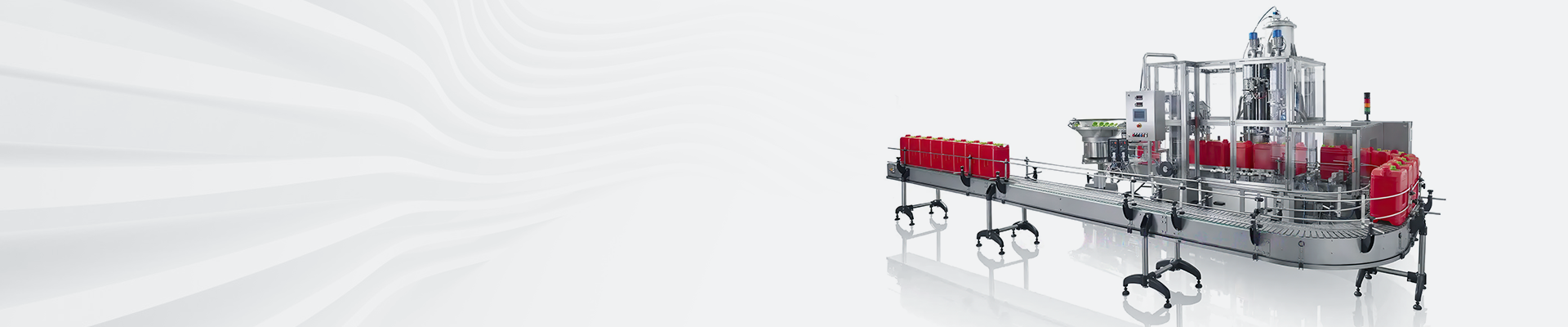
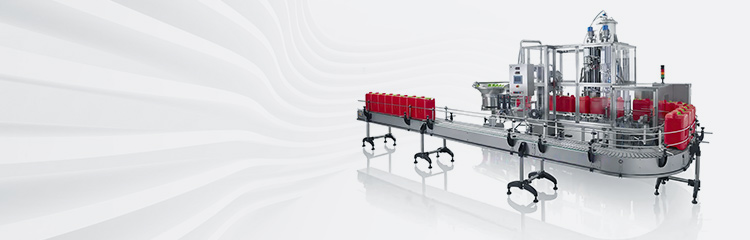

Summary:The automatic filling machine realizes real-time display of filling quality by setting the display output of the label, and monitors the operation of the PLC through touch screen operation. It establishes a connection between the system and external hardware devices, so that MCGS can read data from external devices and control external devices. The working status of the equipment enables real-time monitoring of the filling process.
The automatic filling machine mainly adopts the weighing and dosing method to realize the quantitative filling of liquid by collecting the data from the weighing module. Need to measure the amount of filling and real-time display, the filling system uses a metering module and weighing instrument, set its range of 0 ~ 40kg, the output is a standard voltage signal 0 ~ 10V, through the EM235 analog input channel to achieve the measurement of the quality of the cans, the EM235 port is set to 0.0010. In order to ensure the accuracy of filling, the system in the front of the pump to add a solenoid valve, to ensure that the start / stop the pump can immediately connect and cut off the liquid inflow, the pump selected parameters of 12V. To ensure that the start / stop can be immediately connected and cut off the inflow of liquid, the pump selection parameters for the 12VDC flow rate of 3.1L/min maximum pressure of 0.48MPa, the use of intermediate relays as a conversion to achieve the control of the solenoid valve, pump. In the manual / automatic switching is realized through the two-position selection button, followed by the start, manual filling is realized through the button.
Liquid filling machine accurately dispenses a large amount of bulk liquid materials into various containers, iron drums or plastic drums by weight, adopts the automatic filling method with large and small material valves in segments, and adopts the fully automatic production from the picking up link of lifting the drums, only need to place the drums of the same specification and model neatly in the designated position, and the professional manipulator will accurately take out one drum at a time, and accurately transport the drums to the filling by the power track The professional robot will accurately take out one pail at a time and convey the pail to the filling nozzle through the power rail. The filled pail is accurately sent to the automatic capping machine, the capping machine, through the manipulator, sucks up one pail cap at a time and accurately places it on the top of the filled pail, and the automatic sealing machine will immediately cooperate with the action of accurately squeezing the pail cap and sealing the filled pail.
In order to realize the above monitoring requirements, the monitoring interface simulates the dynamic filling process by adopting Haniwa effect and fast flow attribute settings; by adding standard buttons to realize manual/automatic selection, starting, stopping, emergency stopping and manually opening pumps and solenoid valves: by setting the display output attributes of labels to realize the setting of real-time display of the quality of filling, the setting of the number of barrels and the display of the number of barrels currently being filled, and other configuration. The monitoring screen monitors the operation status of the filling system, realizes the purpose of monitoring PLC operation by operating on the touch screen, establishes the connection between the system and the external hardware equipment, enables MCGS to read data from the external equipment and control the working status of the external equipment, and realizes the real-time monitoring of the filling process. Configure the device components in the device window as S7-200 as the monitored device components, set "Universal Serial Parent Device 0" as "Universal Serial Device", set "Sub Device 0" as "Siemens S7-200", set "S7-200" as "Siemens S7-200", and set "Sub Device 0" as "Siemens S7-200". "Secondly, the graphic objects in the operation screen must be linked to the programming software in the PLC. This can be done by defining the real-time database in the MCGS, and then through the channel connection in the device window, providing the real-time database with the channel connection of the data variables collected from the external devices.
Weighing and filling machine I / 0 allocation needs switching individual input, analog input signal real-time collection of filling quality, switching output control pumps and solenoid valve action, the PLC system has two ways of working, using the main program to call the structure of the subroutine, reduce the scanning time, the conversion of the measured value, the external reason for stopping and emergency stops and so on. Upper machine using configuration software for monitoring interface design, the software can quickly component and generate the upper machine monitoring system, through the data acquisition and processing of the scene, to animation display, alarm processing, process control. Real-time curve, historical curve and report output and so on in many ways. Monitoring system through the screen real-time display of the current filling quality, filling the number of barrels and other on-site work status, in the host computer can carry out the corresponding operation, through the interface for the filling mode selection and start, stop and other buttons operation. It can change the filling quality, the number of barrels and manually remove the tare weight (i.e. the quality of filled bottles) when using different filling barrels.
In the undertaking of the filling production line project, the user's product variety has three kinds (1 #, 2 #, 3 #), each variety of measurement specifications also has three kinds (A, B, C), so the combination will have nine kinds of production specifications, variety of specifications so that the filling configuration and functionality of the more complex. Filling system is characterized by: extremely corrosive, high product value, unstable density, flow pressure is also unstable. Therefore, in the design and manufacturing process, the user in addition to the corrosion resistance of the materials used in the production line has high requirements, but also required in the filling process to prevent dripping, and put forward a more demanding precision and speed requirements.
1)Temperature of filling material: 5~35℃.
(2) Material density: about 1.2g/cm3, salt about 1.3g/cm3
(3) Material viscosity: about 50CP, salt about 150CP
(4) Inlet pressure of feeding pipeline: ≥0.2Mpa, fluctuation range ±10
(5) Filling equipment layout area: 1200m2
6)The process is as follows (take line Ⅰ as an example)
Empty barrels finishing - empty barrels into the filling station - detection and positioning - filling head down - filling valve open - start filling - quality measurement - to reach 90% x (set value - compensation value) - regulating valve throttling becomes smaller - to reach 100% × (set value - compensation value) - filling valve closed - vacuum adsorption - full barrel out of the filling station - steering -Hanging cap - Capping - Labeling - Palletizing - Winding - Finished product output.
Functional requirements
1) This production line includes: Ⅰ filling line (for 30KG filling), Ⅱ filling line (for 250KG or 1200KG filling);
2) No.Ⅰ and No.Ⅱ can be operated independently or at the same time. However, No. II filling line can only produce one specification (250KG or 1200KG) at a time. There are three kinds of running combination of the whole production line: Ⅰ, Ⅰ + Ⅱ, Ⅱ, etc. Ⅰ line has 3 filling stations (1A, 1B, 1C), and each filling station must fill 3 barrels at the same time (corresponding to 3 flow meters respectively); Ⅱ line has 6 filling stations (2A, 2B, 2C, 3A, 3B, 3C), and each time, we can only choose one of the filling stations to do the work (among which, the 2A and 3A stations share 1 flow meter, 2A and 3A stations share 1 flow meter, and the 2A and 3A stations share 1 flow meter, and the 2A and 3A stations share 1 flow meter, and the 2A and 3A lines can only work on one of them. Shared 1 flowmeter, 2B and 3B workstation shared 1 flowmeter ......), and 2A, 2B and 2C (250KG specifications) are 4 barrels as a group of 1 on the pallet, the 4 barrels using a flowmeter, the filling process is: after the end of the first barrel filling, then fill the second barrel, the third barrel, the fourth barrel, in turn; and 3A, 3B and 3C (1200KG specification) each station only fills 1 pail at a time;
3) When the operation mode of the whole filling production line is Ⅰ + Ⅱ, in order to save the investment of equipment and the use of workshop area, it takes the common station in the winding and finished product output part, so when entering the common station, it is necessary to prepare the program to avoid it;
4) Convenient data setting and display: primary filling quantity (65%~99%), final setting value (100%), compensation quantity (to prevent overshooting quantity, can be adjusted arbitrarily), qualified judgment interval setting, qualified product counting, unqualified product counting, total output (number of barrels), total filling quantity (weight), instantaneous flow rate upper (lower) limit alarm setting and display;
5) For the convenience of debugging and maintenance, each conveyor is equipped with on-site manual start/stop switch;
6) Emergency stop switches are provided on the PLC cabinet door, on the site, and on each human-machine interface, etc., to facilitate the operator to stop at the fastest speed in each area of the site;
7) Program operation, you must first select the "filling station", and then select "automatic" is valid, and start running, and vice versa is invalid;
8) in the workshop in a prominent position, the establishment of alarm lights and "start ready" sound and light prompts, "start ready" sound and light prompts from the selection of the "filling station" to select the "The sound and light prompts are intermittent and the alarm sound and light are continuous;
9) including frequency counting output (FC) and analog output (FA), frequency output as a cumulative flow of filling measurement, analog as instantaneous flow of upper and lower limit alarm;
10) "filling button", status and equipment failure instructions on the human-machine interface, filling process text prompts, measurement of the end of the filling machine, reset the "start filling" button, filling process, such as the need to abort, you can press the "manual stop filling". If you need to stop the filling process, you can press the "manual stop filling" button;
11) anti-drip design: after filling, residual viscous material on the surface of the filling head after a certain period of time to flow out, if it drips to the outside of the container, it will cause contamination, the filling using vacuum generator suction filling can ensure that there is no drip.
The program design has received strong support and cooperation from the relevant technical personnel of Schneider, integrating computer technology, programmable control technology, data setting and display technology, bus technology, high-speed counting technology and software programming technology, etc., so that the program design is advanced, the software and hardware are reasonably configured, and the project progresses extremely smoothly, with each parameter meeting or exceeding the user's acceptance standard, especially the metering accuracy is controlled within ±0.1% (acceptance standard is ±0.125%). 0.1% or less (acceptance standard is ± 0.125%), the filling speed reached 3 barrels / minute within 30KG. After two months of trial operation, it passed the user acceptance at the site in one go. Now, the production line has been running stably for nearly one year, and has been fully affirmed by the users.