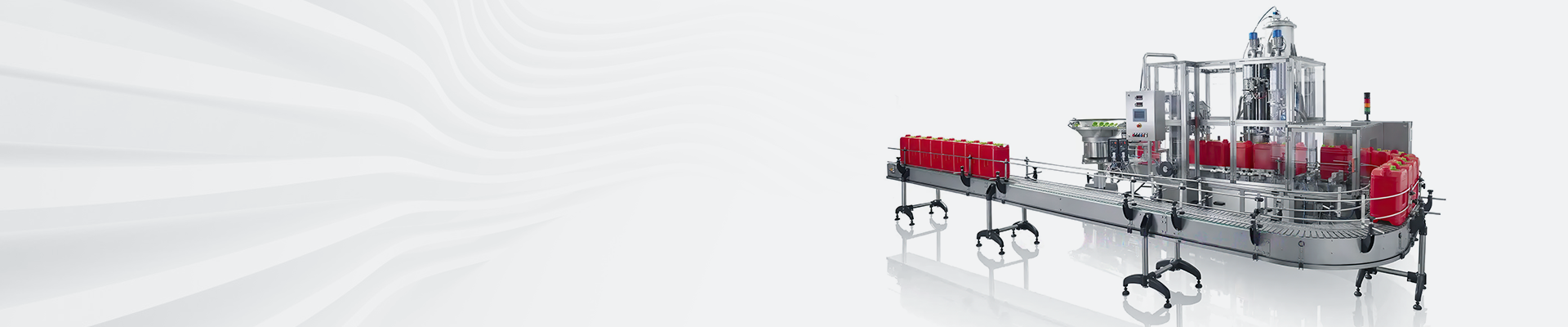
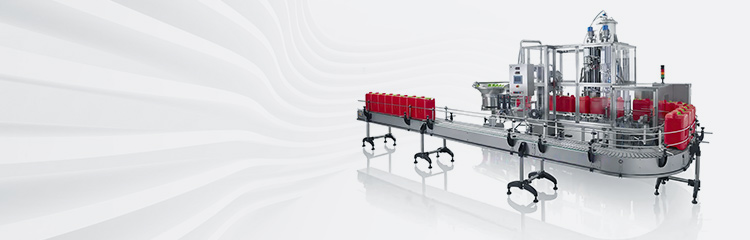
摘要:自动灌装机通过设置标签的显示输出实现灌装质量的实时显示,通过在触摸屏操作实现监控PLC运行的目的,建立系统与外部硬件设备的连接,使得MCGS能从外部设备读取数据并控制外部设备的工作状态,实现灌装过程的实时监控。
自动灌装机主要是采用称重定量方法,通过采集称量模块的数据来实现对液体的定量灌装。需要对灌装量进行测量并实时显示,灌装系统采用了计量模块及称重仪表,设置其量程为0~40kg,输出为标准的电压信号0~10V,通过EM235的模拟量输人通道实现对罐装质量的测量,EM235的端口设置为0.0010。为了保证灌装精度,系统在泵的前端添加了电磁阀,保证启动/停止时能立即接通及切断液体流入,泵选用参数为12VDC流量为3.1L/min最大压力为0.48MPa,采用中间继电器作为转换实现对电磁阀、泵的控制。在手动/自动的切换是通过两档选择按钮实现,其次,启动、手动灌装是通过按钮来实现。
液体灌装机以重量方式精确地将大量的散装液体物料分装到各种容器、铁桶或塑料桶中,采用大小物料阀分段自动灌装方式,从提桶的取用环节就采用全自动生产,只需要将相同规格和型号的桶整齐摆放在指定位置,专业机械手会每次准确取出一个包装桶,通过动力轨道将包装桶精确输送到灌装嘴下面。灌装好的桶,被准确送到自动理盖机下,分盖机通过机械手,每次吸取好一个桶盖,准确放置到灌装好的桶上面,自动封口机会立即配合动作将桶盖准确挤压,对灌装好的桶进行封口。
自动填充机为了实现上述监控要求,监控界面采用埴充效果、流动快的流动属性设置模拟了动态灌装过程;通过添加标准按钮实现手动/自动选择、启动、停止、急停及手动打开泵、电磁阀:通过设置标签的显示输出属性实现灌装质量的设定实时显示,灌装桶数的设定及当前灌装桶数显示等组态监控画面对灌装系统运行状态的监控,通过在触摸屏操作实现监控PLC运行的目的,建立系统与外部硬件设备的连接,使得MCGS能从外部设备读取数据并控制外部设备的工作状态,实现灌装过程的实时监控。设备窗口内配置设备构件为S7-200为所监控的设备构件,设置“通用串口父设备0”为“通用串口设备”设置“子设备0”为“西门子S7200PPI”;其次,必须将操作画面中的图形对象和PLC中编程软件联系起来,这个可以通过在MCGS中定义实时数据库,再通过设备窗口中的通道连接,向实时数据库提供从外部设备采集到的数据变量通道连接。
称重灌装机的I/0分配需要开关量个输人,模拟量的输人信号实时采集灌装质量,开关量输出控制泵和电磁阀的动作,PLC系统有两种工作方式,采用主程序调用子程序的结构、减少扫描时间,测量值的转换、停止及急停的外理等。上位机采用组态软件进行监控界面设计,该软件能快速构件和生成上位机监控系统,通过对现场的数据采集处理,以动画显示、报警处理、流程控制。实时曲线、历史曲线和报表输出等多种方式。监控系统通过画面实时显示当前灌装质量、灌装桶数等现场工作状态,在上位机上可以进行相应的操作,通过界面进行灌装方式的选择及启动、停止等按钮的操作。能够更改灌装质量、桶数及在使用不同的灌装桶时能手动去除皮重(即灌装瓶的质量)。
在承接的灌装生产线项目中,用户的产品品种有三种(1#、2#、3#),每个品种的计量规格也有三种(A、B、C),因此组合后将有9种生产规格,品种规格多样使灌装配置和功能较为复杂。灌装系统的特点是:腐蚀性极强、产品价值高、密度不稳定、流速压力也不稳定。因此在设计和制造过程中,用户除了对生产线的使用材料的耐腐蚀性有较高的要求外,还要求在灌装过程中防止滴漏,并提出了较为苛刻的精度和速度要求。
1)灌装物料温度:5~35℃
2)物料密度:约1.2g/cm3、盐约1.3g/cm3
3)物料粘度:约50CP、盐约150CP
4)进料管道进口压力:≥0.2Mpa,波动范围±10%
5)灌装设备布置面积:1200m2
6)工艺过程为(以Ⅰ号线为例):
空桶整理—空桶进灌装工位—检测定位—灌装头下降—灌装阀打开—开始灌装—质量计量—到达90%×(设定值-补偿值)—调节阀节流变小—到达100%×(设定值-补偿值)—灌装阀关闭—真空吸附—满桶出灌装工位—转向—挂盖—旋盖—贴标—码垛—缠绕—成品输出。
功能要求
1)本生产线包括:Ⅰ号灌装线(适用30KG灌装)、Ⅱ号灌装线(适用250KG或1200KG灌装);
2)Ⅰ号和Ⅱ号既可独立运行也可同时运行。但Ⅱ号灌装线每次只能进行一种规格(250KG或1200KG)的生产。整条生产线的运行组合方式有Ⅰ、Ⅰ+Ⅱ、Ⅱ等共三种;Ⅰ线有3个灌装工位(1A、1B、1C),每个灌装工位须同时灌装3个桶(分别对应3个流量计);Ⅱ线有6个灌装工位(2A、2B、2C、3A、3B、3C),每次也只能选择其中1个灌装工位进行工作(其中2A和3A工位共用1个流量计,2B和3B工位共用1个流量计……),而2A、2B和2C(250KG规格)均以4个桶为1组放在托盘上,该4个桶使用1台流量计,灌装过程为:第1桶灌装结束后依次再灌装第2桶、第3桶、第4桶;而3A、3B和3C(1200KG规格)各工位每次只灌装1个桶;
3)当整条灌装生产线的运行方式为Ⅰ+Ⅱ时,为节约设备投资和车间使用面积,在缠绕和成品输出部分采取公用工位,因此在进入公用工位时,须编制程序进行避让;
4)方便的数据设定和显示:一次灌装量(65%~99%)、最终设定值(100%)、补偿量(防止过冲量、可任意调整)、合格判定区间设定、合格品计数、不合格品计数、总产量(桶数)、总灌装量(重量)、瞬时流量上(下)限报警设定及显示;
5)为方便调试和维护,在每台输送机旁均配现场手动启动/停止开关;
6)在PLC柜门上、现场、各人机界面上等均设有急停开关,方便操作人员在现场的各个区域以最快的速度停车;
7)程序运行,必须先选择“灌装工位”,后选择“自动”时有效,并开始运行,反之无效;
8)在车间显著位置,设立报警灯及“启动预备”声光提示,“启动预备”声光提示是从选择了“灌装工位”开始至选择“自动”结束,声光提示为断续音,报警声光为连续音;
9)包括频率计数输出(FC)和模拟量输出(FA),频率输出作为累计流量灌装计量用,模拟量作为瞬时流量上下限报警用;
10)“灌装按键”、状态及设备故障指示设在人机界面上,灌装过程中有文字提示,计量灌装机结束后,复位“开始灌装”按键,灌装过程中,如需中止,可按下“手动停止灌装”按键;
11)防滴漏设计:灌装完毕后,残留在灌装头表面的粘性物料要经过一定的时间才能流尽,如果滴到容器外,就会造成污染,本灌装采用真空发生器回吸灌装可确保无滴漏。
方案设计得到了施耐德公司相关技术人员的大力支持和配合,融合了计算机技术、可编程控制技术、数据设定和显示技术、总线技术、高速计数技术和软件编程技术等,使方案设计先进、软硬件配置合理,项目进展极为顺利,各项参数均达到或超过了用户验收标准,尤其是计量精度控制在±0.1%以内(验收标准为±0.125%),灌装速度达到了3桶/分钟•30KG以内。经过两个月的试运行后,在现场一次性通过了用户验收,现在,该生产线已稳定运行了近一年,得到了用户的充分肯定。